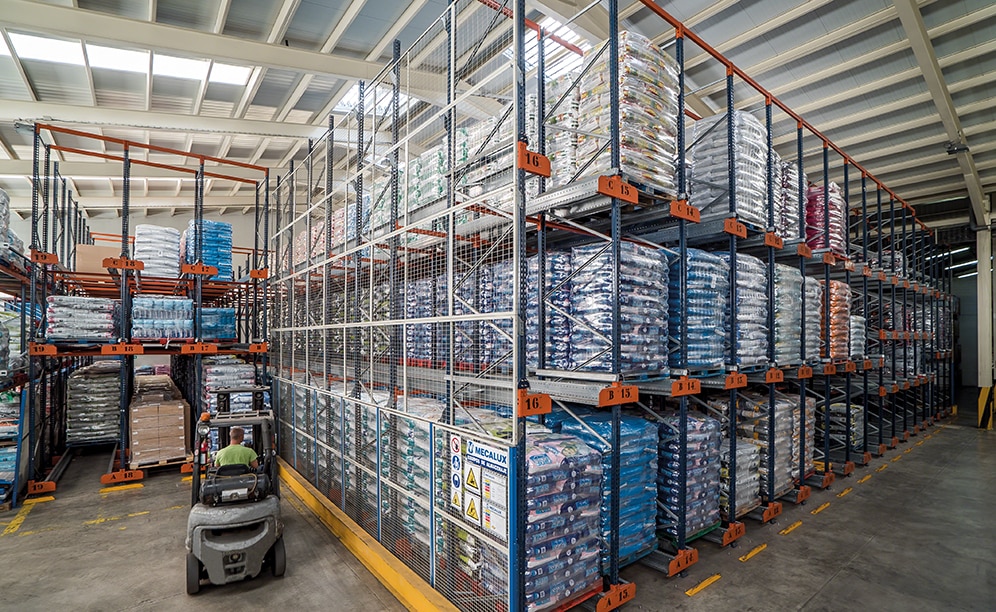
The high-density Pallet Shuttle system optimises product turnover for a dry pet food producer
Six Pallet Shuttles transport Alinatur's products using the FIFO method
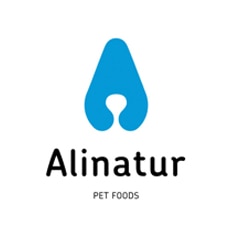
Alinatur, a company specialized in the manufacture of dry dog and cat food, has hired Mecalux to supply a warehouse with Pallet Shuttles at its central warehouse in Lorca (Murcia) with a capacity for 1,500 pallets.
Pallet Shuttle warehouse: features
After analyzing the needs of Alinatur, Mecalux chose to install the Pallet Shuttle storage system in order to maximize the available space.
The warehouse has six Pallet Shuttles that increase workflows by reducing time spent on storage, extraction of pallets and the loading of transport trucks.
The Pallet Shuttle is a system that, as well as making full use of space, offers high capacity storage by using autonomous shuttles that work within the channels.
The pallets are introduced into the production side, while dispatches take place on the opposite side, which coincides with the area allocated to the loading docks.
Thus, the channels operate using the FIFO (first pallet in is the first out) criterion, enabling complete product turnover.
Semi-automatic Pallet Shuttle operations
The operator uses the various integrated commands on a remote control that works via radio frequency to give orders to the Pallet Shuttle.
That is when the shuttle starts to work autonomously.
This shuttle model, besides the drive and lift components, has the following devices as part of its setup:
- Operating pilot lights
- Anti-entrapment and anti-crushing safety bumpers
- An on/off switch
- A battery status indicator
- End-of-track sensors
- Fast-charging batteries
- A minimum reserve battery
- Movement direction and breakdown sensors
- An emergency stop button
- A RF aerial
- Position sensors
The order output process
The channels, due to space, have variable depths to store the pallets according to the SKUs and consumption. By having a small number of SKUs, the operator does not have to continuously change the channel the shuttle occupies, thereby increasing warehouse throughput.
During the output process, also managed with two shuttles, movements are optimized by several pallets of the same SKU being extracted at the same time, but for different orders. In addition, pallet racking was placed on one side to store prepared orders and lower consumption SKUs.
As a further safety measure, mesh was installed on the sides of the racks to prevent the accidental entry of operators and possible falling of goods into common areas.
Advantages for Alinatur
- Space optimization: the new Alinatur warehouse stores 1,500 pallets, in an area of only 6,189 ft2, spread over 62 channels that are 43’, 69’ and 75’ long.
- Increased productivity: thanks to the work of the four Pallet Shuttles maneuvering, times are reduced in the warehouse, extracting and depositing loads faster.
- FIFO system: there is total product turnover because the pallets enter the channels on the production side and subsequently exit on the opposite, next to the loading docks.
Pallet Shuttle system in the Alinatur warehouse, Spain | |
---|---|
Installation capacity: | 1,500 pallets |
Pallet size: | 47” x 31.5” |
Pallet type: | Euro pallets |
Pallet weight: | 1.1 t |
Number of shuttles: | 6 |
Shuttle model: | 121RSM-0812/131RSM-0812 |
Max. unloaded speed: | 197 ft/min |
Max. loaded speed: | 138 ft/min |
Gallery
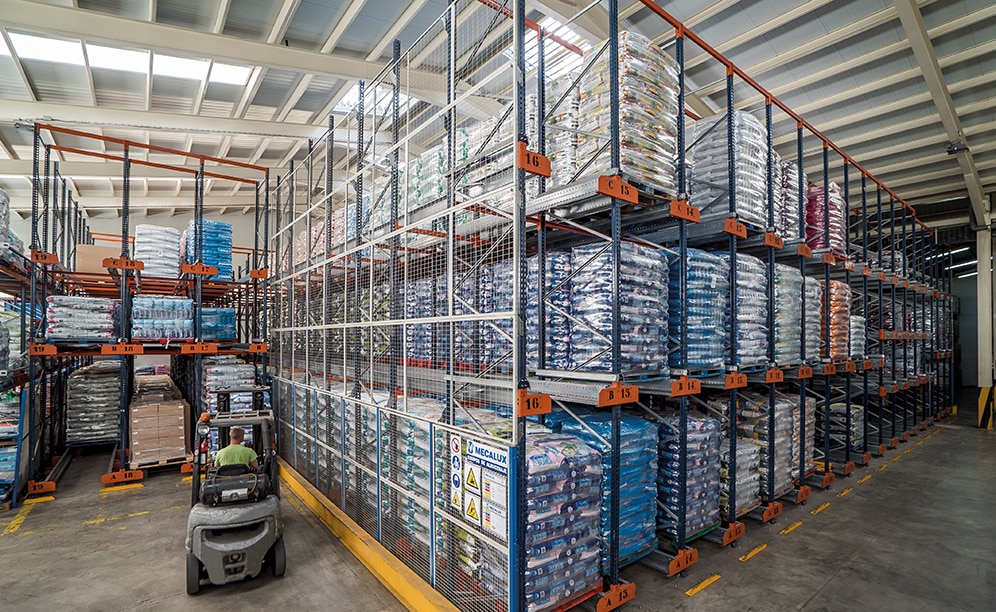
The warehouse has a 1,500 pallet capacity dispersed over 62 channels that are 13, 21 and 23 m deep
Ask an expert