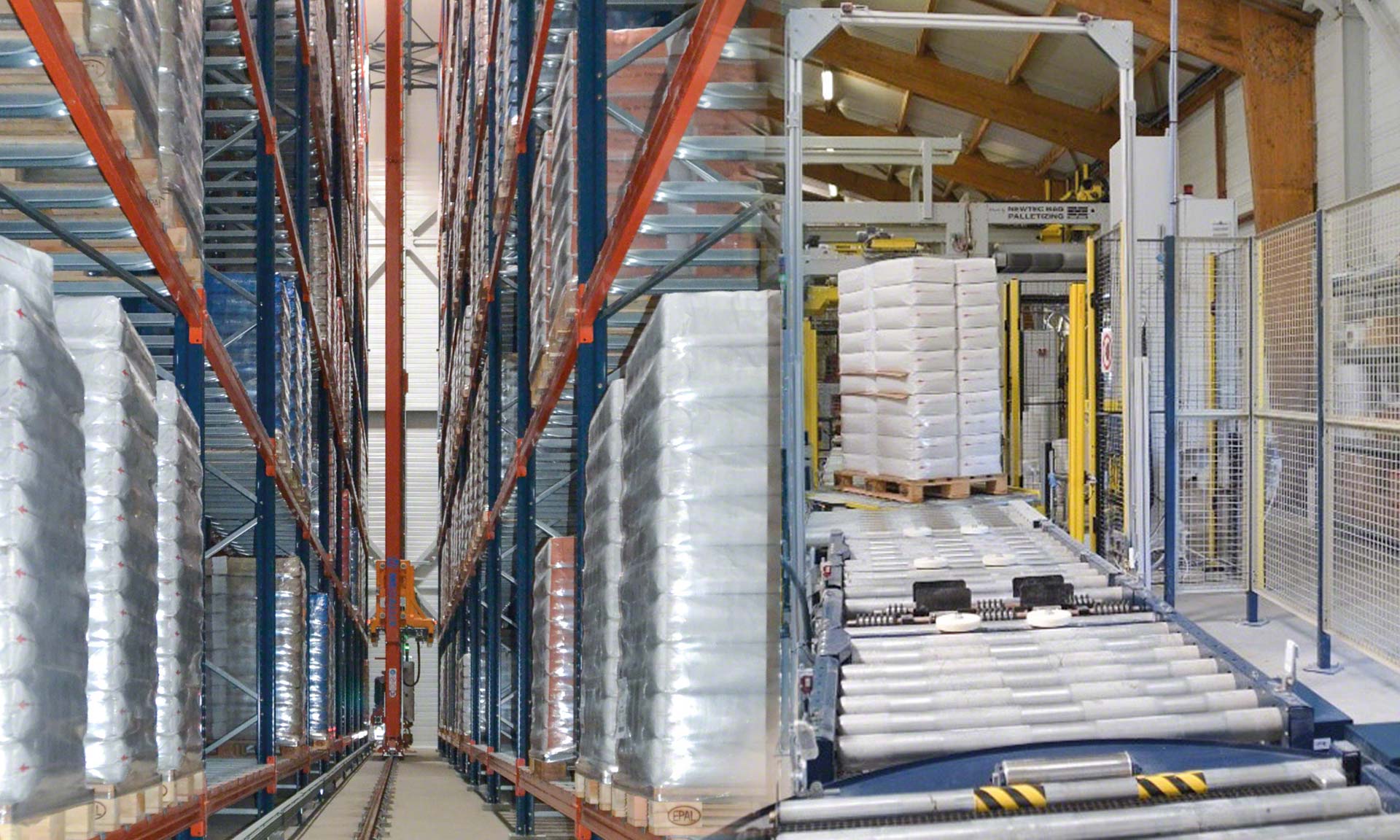
Flour producer Paulic Meunerie automates its facility
Paulic Meunerie triples its production pace and automates its logistics operations to tackle business expansion.
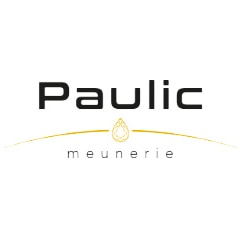
Paulic Meunerie automates its supply chain to cope with the increased rate of wheat flour production in recent years. The company has implemented Easy WMS to control the traceability of its goods in real time and know the exact location of each of its items.
Paulic Meunerie: four generations in the family business
Paulic Meunerie is a renowned producer of wheat flour and buckwheat flour in Brittany, France’s most northwestern region. Founded in 1957 as Minoterie Paulic, the company has been serving the needs of professionals in the bakery, crepe and food industry in France and abroad for four generations.
- Founded in: 1957
- No. of mills: 3
- Total production: 340 tons/day of wheat and buckwheat
CHALLENGES
|
SOLUTIONS
|
BENEFITS
|
---|
“Innovation, research, and technology are in our DNA, and that makes the difference,” says Jean Paulic, President and CEO of Paulic Meunerie. The company produces more than 220 tons of wheat and buckwheat flour a day to supply over 700 customers. Over the past five years, the business has made investments upwards of $13 million. This led it to become, in early 2020, the first agricultural technology company to be listed on Euronext, the pan-European stock exchange. During the first half of 2022, Paulic Meunerie had a turnover of $7.5 million, up 53% compared to the previous year.
“Our production centers are in the heart of Brittany, so they’re in a strategic position to reach customers more speedily. Our priority is to supply wheat to farmers in the region. Currently, over 70% of our flour comes from Breton wheat. This location enables us to be as close to our customers as possible to supply them quickly. Proximity allows us to produce and market 100% local flour while reducing our business’s environmental impact,” says Paulic.
Since 2020, production in the center has tripled. To cope effectively with this rate of growth, the company needed to modernize its main production center. The Paulic Meunerie facility has been outfitted with five bagging machines to fill 55-lb packages of wheat flour, specialty flours and buckwheat flour, as well as small 2-lb packages of wheat and buckwheat flour.
Additionally, a new storage area has been set up, equipped with an automated system that connects to the packaging lines. A warehouse management software program controls product traceability, accurately tracking all goods movements. This solution, installed by Mecalux, consists of an automated storage and retrieval system (AS/RS) for pallets to house finished products, automatic conveyors to connect the AS/RS with the production lines, and the Easy WMS warehouse management system.
Automated logistics operations
Paulic Meunerie’s new AS/RS is located in a strategic area that facilitates goods-in and goods-out processes: it is close to both the production lines and the loading docks. Moreover, through automation, the company now has continuous product flows.
The racks, which stand 62’ high in a 115-foot-long aisle, house 864 pallets of finished goods. The pallets arrive from production by means of conveyors. Once in the AS/RS, a twin-mast stacker crane with telescopic forks picks the products up and deposits them in the corresponding locations. The racks have been personalized to accommodate pallets of different sizes.
To dispatch the goods, Mecalux has installed a 49-foot-long gravity conveyor channel next to the AS/RS. Pallets that Easy WMS has marked for shipment are placed there, and operators subsequently move them to the loading docks.
Real-time traceability
“Our Moulin du Gouret production plant has a very effective traceability system. Mecalux’s Easy WMS warehouse management software allows us to see our material flows and how much stock we actually have in real time,” says Paulic.
To control inventory in real time, the pallet checkpoint set up at the start of the conveyor line automatically reads the barcode label on each pallet. This checkpoint also verifies that the pallet matches the one previously indicated by Paulic Meunerie’s enterprise resource management (ERP) software. The dimensions and condition of the pallets are also checked to ensure they meet the requirements for storage.
It was essential for Easy WMS to be integrated with Paulic Meunerie’s ERP software. Now, the two systems can exchange information and data on the status of the warehouse and on business needs, e.g., items scheduled to arrive or orders placed by customers that have to be shipped as soon as possible.
To assign each pallet a location on the racks, Easy WMS makes a series of calculations, taking into account the number of empty slots, the SKU and the demand level. This is where automation comes into play: the pallets are moved to their corresponding locations via conveyors and a stacker crane.
Once the pallets are stored, the WMS software knows the status of all the goods in real time and shares this information with Paulic Meunerie’s ERP system. When dispatching the pallets, the ERP system again notifies the Mecalux software of the pallets it needs. In turn, Easy WMS manages the picking list for those pallets in line with the transportation route of the requested order.
Forward-looking logistics
Thanks to automation, Paulic Meunerie now has a flexible supply chain ready to take on any challenges that lie ahead. “Our production plant is outfitted with cutting-edge technology. This enables us to respond to current food industry challenges and offer our customers agile service — both in France and abroad. We’re prepared to absorb the tremendous growth our business is experiencing,” says Paulic.
We’re really happy with the features of our AS/RS from Mecalux. Our investment in technology has given us a flexible, scalable and secure supply chain.
Gallery
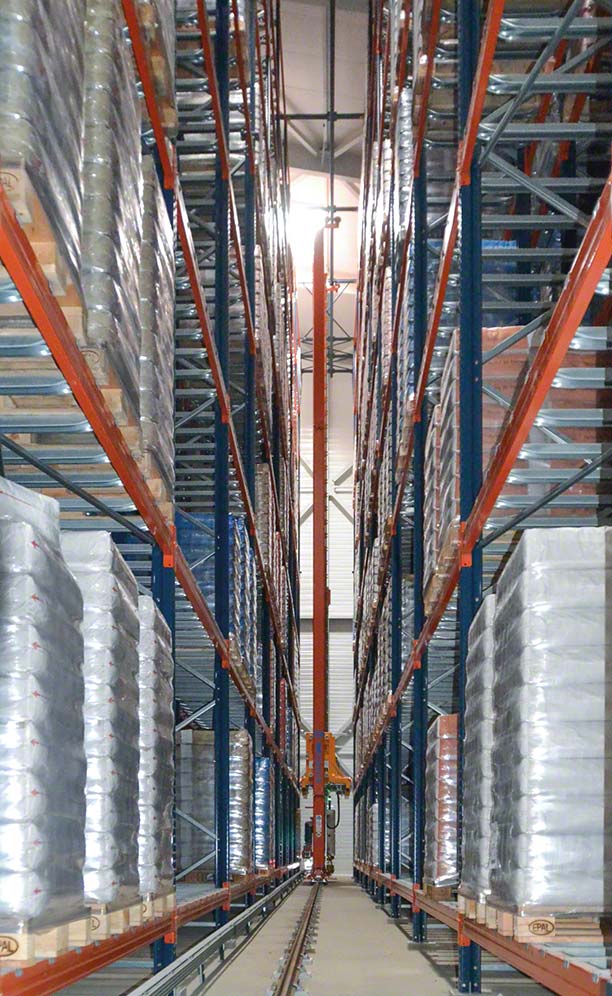
Stacker crane for pallets in Paulic Meunerie's AS/RS
Ask an expert