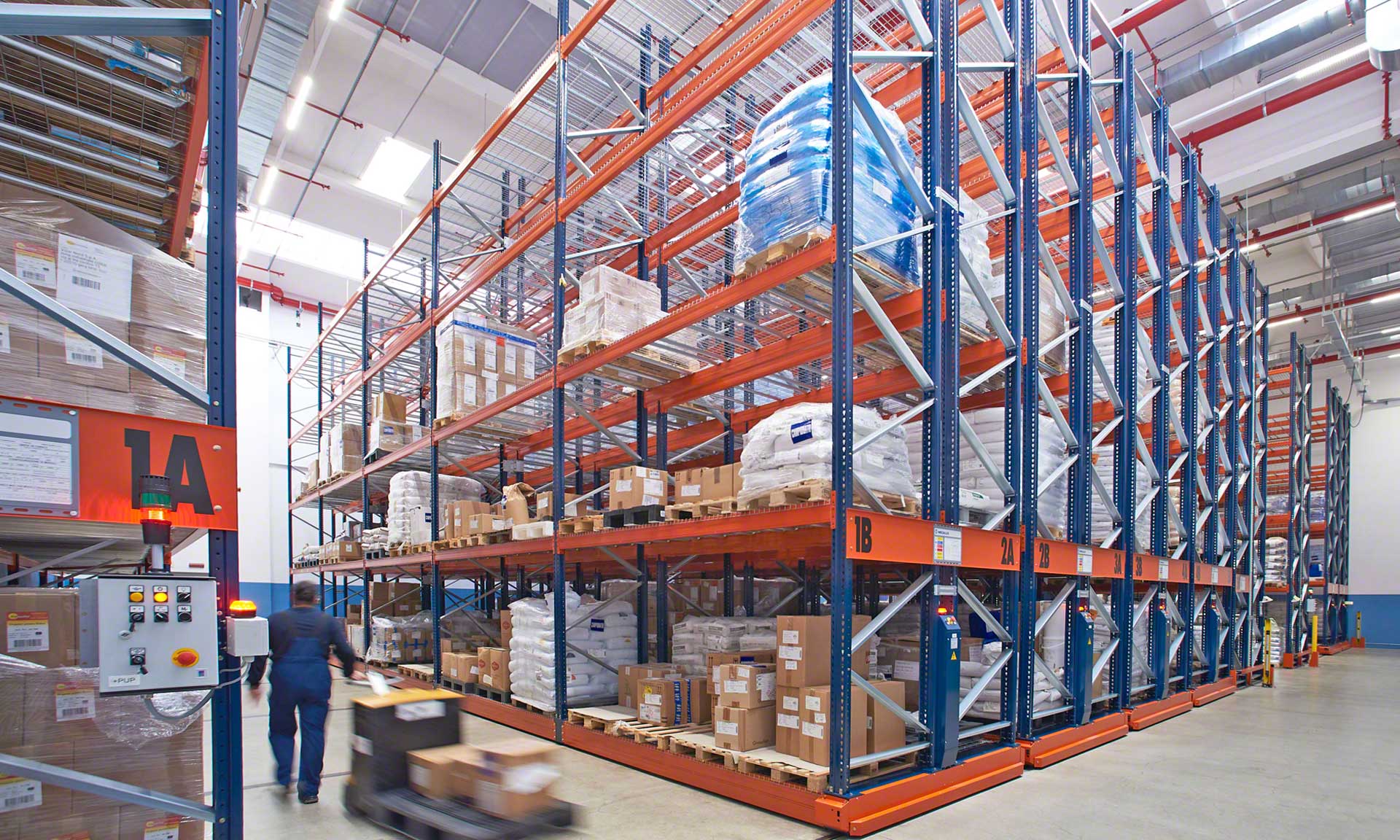
Vibar Nord: automation connects production to the warehouse
Automation has reduced the time taken to move the goods from production to dispatch
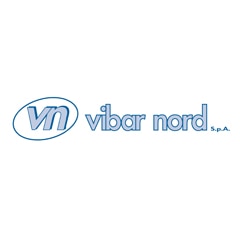
Vibar Nord, a producer of over 5,500 tons of food and dietary products a year, has opted for robotics in its new warehouse in Gera Lario, northern Italy. Mecalux has automated the connection between the production plant and dispatch area via a dual conveyor line and a pallet lift that automatically join the two zones. Mecalux has also implemented two earthquake-proof storage systems: Movirack mobile pallet racking and pallet racks, which have increased warehousing capacity by 70%.
Founded in Italy in 1972, Vibar Nord produces food and dietetic products for third parties in the form of soluble powder and granules. It was the first Italian company to apply the fluidized bed granulation process on an industrial scale in the food and dietetic sector.
The firm’s business activity began in its historic plant in Colico in northern Italy. In a surface area of 107,639 ft², the facility is equipped with the latest technology to ensure high quality standards. As a result of the growth seen in recent years, Vibar Nord has opened a new production plant just three miles away, in the Gera Lario area.
Gera Lario plant
With a surface area of 64,583 ft², the Vibar Nord center in Gera Lario features the production lines, a product quality control lab, an R&D area, and a storage zone for raw materials and finished products.
One of the first challenges of the new plant was to design the flow of movements to link the production area on the second floor with the storage and dispatch zone on the first.
Vibar Nord’s main logistics need was to have an intelligent transportation system that would safely move pallets from the second level to the first. In doing this, it would have to overcome an incline of over 23', taking into account the available space, the movement flows required, and the type of unit load handled: a metal container typically used in the food sector.
In addition to this logistics requirement, Vibar Nord was looking for a storage system that was versatile, seismic-resistant, and that would optimize the center’s floor space to store the raw materials used in the production process. “We wanted to achieve the biggest possible storage capacity and speed up order prep. We also had to improve the connection between the storage area on the second floor and the loading docks on the first floor,” says Alessandro Tenzi, Head of Operations at Vibar Nord.
With all these requirements defined, the company began the search for a logistics provider capable of meeting them. “We chose Mecalux’s solutions after comparing them with those of other competitors,” says Tenzi.
Automatically connected to the dispatch area
To streamline the movement of goods between the production and dispatch zones, Mecalux has installed a 93-foot-long dual roller conveyor that connects to a lift charged with lowering the merchandise to the first floor automatically.
Tenzi says, “The conveyors have made goods transfers much faster. Now, we only need one operator to place the goods on the conveyor. Before, we had a slower lift that forced us to use two workers - one on each floor - charged with placing or removing goods from the lift. Thanks to this new system, pallet handling takes a third less time.”
Both the conveyor system and the lift have been personalized to match Vibar Nord’s needs. The company works with two types of pallets (31.5"/39.4" x 47.2") and with a type of metal container with only two skids. This required a detailed analysis to ensure that both automated handling systems would operate efficiently when moving horizontally and vertically.
When the product leaves the production lines, the operator, aided by a forklift, places the unit load on one of the conveyor lines, which moves it to the lift automatically. The lift then brings the goods down to the first floor, where a conveyor circuit moves the unit load to one of the five exit points. At this part of the process, the operators remove the goods from the conveyor line and place them in front of the loading docks in a rack-free area.
There, with the goods stored temporarily on the floor, the operators organise the pallets by order or transport route, and they are eventually loaded onto the lorries. In addition to the lift, the warehouse is outfitted with other freight elevators that serve mainly to raise the raw materials stored on the second floor to the production lines on the upper level.
Earthquake-resistant racks
For the storage area, Mecalux proposed installing two different storage systems to manage the raw materials: pallet racks and a Movirack mobile pallet racking unit.
“We chose Movirack racking because we realized it would make the most of the available space. We were convinced by how easy this storage system was for managing goods and by the excellent manufacture of its structure,” says Tenzi.
Movirack racks are a compact storage system that increases storage capacity while maintaining direct access to the goods. The figures speak for themselves: “The racks we used previously allowed us to store 1,000 pallets. Now, with Movirack, we can accommodate 1,700, that is, 70% more items in the same space,” says Tenzi.
The Movirack unit stands 28' tall, with 4 racks on mobile bases and 2 fixed racks at each end. According to Tenzi, “this solution helps us optimize our warehouse space and gives operators ample room to access the load and maneuver.”
The Movirack racks store all of Vibar Nord’s goods — around 280 SKUs — in a safe, controlled way using just a radio control device.
The racks are installed on mobile bases that move sideways autonomously. To open the required aisle and remove or deposit the goods in their locations, the operator merely has to give the command by means of the radio control device.
As for the pallet racks, the company chose them for their versatility in storing all kinds of products: their 5 levels house 340 pallets of variable heights. In addition to its high resistance and scalability, this system expedites goods loading and unloading.
Movirack racking: safety in motion
Movirack mobile pallet racking ensures completely safe movements, as it is equipped with several safety devices::
- Exterior barriers stop the racks from moving when an operator enters the aisle.
- Interior barriers detect the presence of objects in the aisle that would prevent the system from operating properly.
- Emergency buttons immediately block the movement of the racks in the event of an incident.
- Proximity photocells ensure a smooth, safe stop.
Logistics on the rise
Vibar Nord has a challenge ahead: the company has set out to improve all its processes to continue to grow. “We want to move all the SKUs in our old warehouse to the new plant in Gera Lario,” says Tenzi. “So far, our growth rate has reached 5%, and we expect this to increase even more in the future.”
The conveyor and pallet lift have enabled Vibar Nord to manage various orders simultaneously and very quickly. Likewise, the structure of the Movirack mobile pallet racking guarantees greater storage space to house the raw materials needed for production.
Each storage solution is used for a specific type of product based on its characteristics and demand level. The combination of both storage systems has helped the company to optimize its surface area and efficiently manage its products.
With these storage and transportation solutions from Mecalux, we’ve saved time when it comes to goods handling. We’re really happy with the Movirack mobile racks, as our storage capacity has risen by 70%. With the conveyors, we’ve slashed the time it takes to move the goods from production to the dispatch area by a third.
Advantages for Vibar Nord
- 70% more items: the Movirack racking leverages all the available space to provide storage capacity for 1,700 pallets.
- Direct access to goods: both the pallet and Movirack racks provide direct access to the products, streamlining pallet storage and removal operations.
- Warehouse connected to production: the conveyors have increased speed, shortening the time needed to move the goods from production to the dispatch area by a third.
Pallet racks | |
---|---|
Storage capacity: | 340 pallets |
Pallet sizes: | 31.5"/39.4" x 47.2" |
Max. pallet weight: | 2,205 lb |
Rack height: | 28' |
Gallery
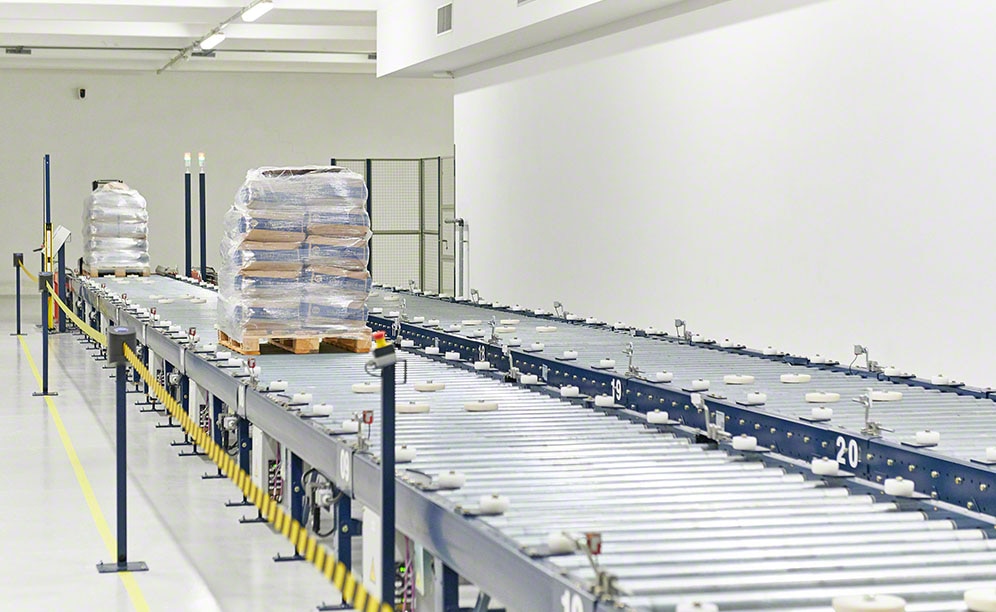
The new Vibar nord warehouse in Gera Lario with dietetic products
Ask an expert