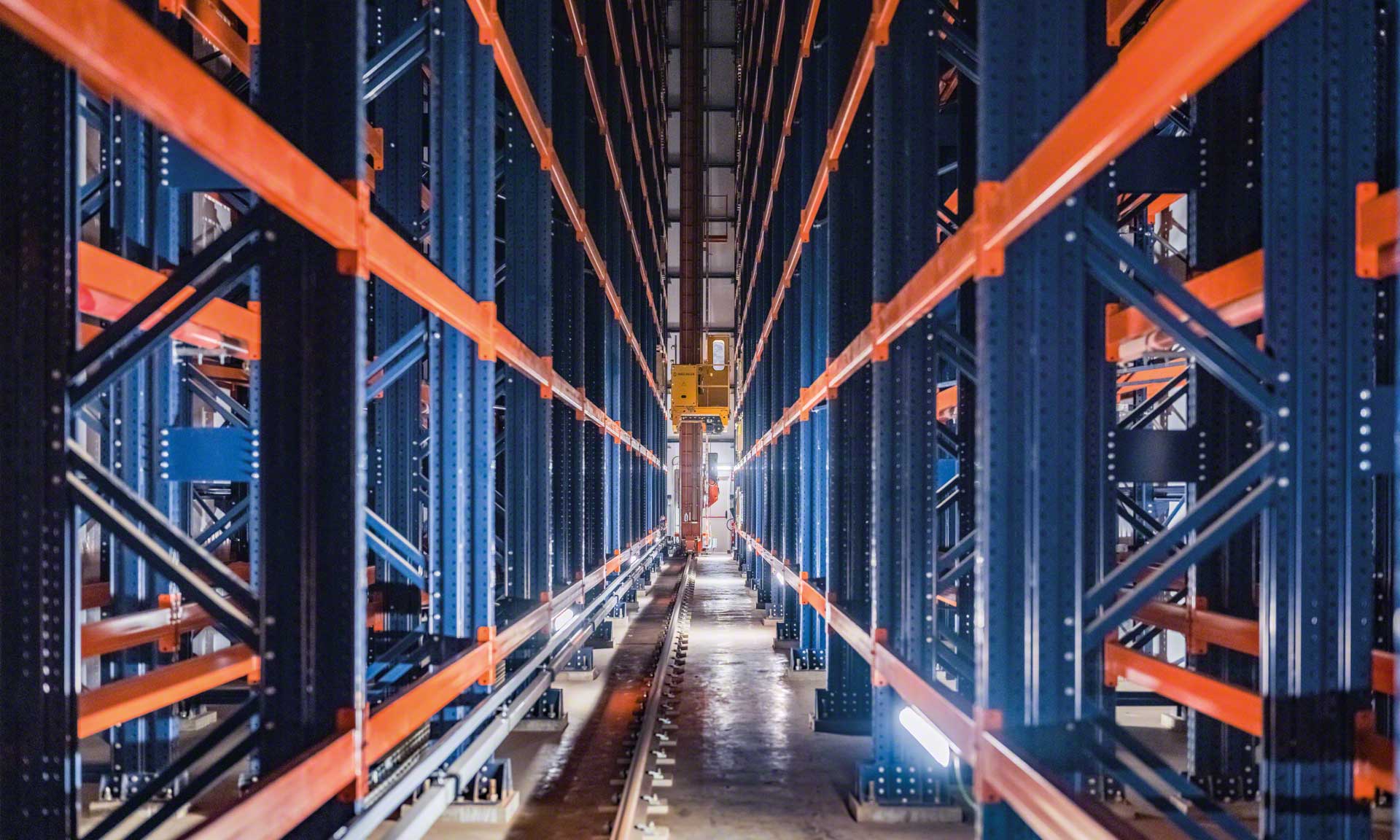
IMEFY gains agility in transformer manufacturing with an automated rack-supported building
The electrical transformer manufacturer has centralized the storage of its parts and raw materials.
IMEFY is an electrical transformer manufacturer of highly efficient solutions approved by electric companies worldwide. The business has centralized the management of its parts and raw materials in a rack-supported building from Mecalux.
Electrical transformers supported by R&D and innovation
IMEFY is a manufacturer of electrical transformers for various industrial applications. Its highly efficient solutions are approved by numerous electric companies worldwide. At its headquarters in Los Yébenes (Spain) spanning 17 acres, it manufactures dielectric-liquid-immersed, epoxy-resin-encapsulated, and power transformers that meet environmental sustainability norms and the rigorous tests required by international standards. Founded in 1973, IMEFY manufactures electrical transformers for businesses worldwide.
CHALLENGES
|
SOLUTIONS
|
BENEFITS
|
---|
Due to their large size, the items made by electrical transformer manufacturer IMEFY cannot be housed in conventional storage systems. Nevertheless, the company succeeded in increasing its production capacity with an automated warehouse from Mecalux. The 78-foot-tall, 262-foot-long facility accommodates the raw materials that the family-run business has used to manufacture transformers for the energy industry since it was founded in 1973.
“We decided to unify our operations in a single automated warehouse. Our goal was to have greater control over inventory and speed up the management of raw materials. We also needed to prevent them from deteriorating when moving them from one space to another,” says Armando Fontecha, Chief Operating Officer (COO) of the company based in Los Yébenes (Spain) and with locations in Italy and Poland.
Consolidating the multiple warehouses spread out across different areas of IMEFY’s 17-acre center into one building has significantly cut down on travel between the various production zones. Moreover, it has enabled the business to manage its perishable and non-perishable products using the FIFO (first in, first out) method.
This new space constructed by Mecalux is a rack-supported building. It consists of the load-bearing racks, the roof, and the sides of the warehouse. They form a high-density structure that stores up to 4,854 pallets. The rack-supported system features a double-deep stacker crane and three input and three output points.
The manufacturer made the decision to implement this solution in consultation with Mecalux’s technical team. The intralogistics specialists analyzed the quantity and type of pallets IMEFY wanted to store, the number of anticipated goods-in/goods-out movements, and the space available for the installation. They determined that logistics automation was the best option for this benchmark company, which has been transforming energy for over 50 years.
Inventory management with Easy WMS
IMEFY employs the latest engineering technologies to enhance the quality of its products. Similarly, it uses Mecalux’s Easy WMS warehouse management system to oversee 100% of its raw materials, slotted in the new rack-supported building. “The program is extremely intuitive and efficient. It also generates reports and real-time warehouse status graphs, along with historical data and analytics that are invaluable for optimal inventory management,” says the company, which dedicates significant R&D and innovation efforts to transformer manufacturing. Now, production has access to items such as cellulose insulators, aluminum conductors in strip or wire format, and all kinds of accessories via its automated warehouse.
Rack-supported buildings make the most of available surface area. This solution has enabled IMEFY — currently expanding its production facilities — to free up space previously occupied by its old warehouses. “We implemented these upgrades to increase our capacity to manufacture distribution transformers for our clients, the leading European electric companies,” says Fontecha. The company started out making distribution transformers cooled in dielectric liquids. Today, it also produces epoxy-resin-encapsulated and power transformers and has sold over 200,000 units to 2,000 clients in 80 countries.
IMEFY had relied on Mecalux’s manual racking solutions for many years. It chose the intralogistics specialist again to implement this warehouse due to its ability to support clients throughout the project life cycle. “Their customer care has always been top-notch. For the rack-supported building, Mecalux offered us a comprehensive, all-in-one installation service, saving us from coordinating multiple suppliers,” says Fontecha.
Mecalux offered us an all-in-one installation service, saving us from coordinating multiple suppliers. Plus, their customer care has always been top-notch.
Gallery
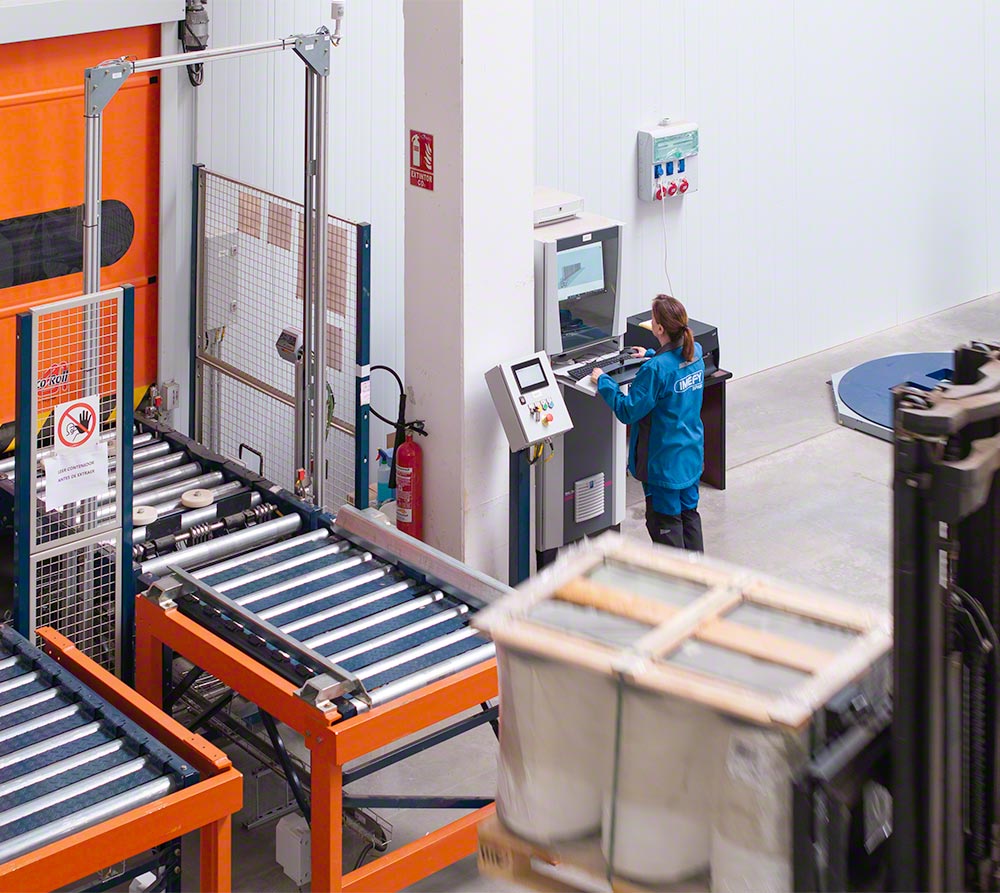
The rack-supported building forms a high-density structure to house 4,854 pallets
Ask an expert