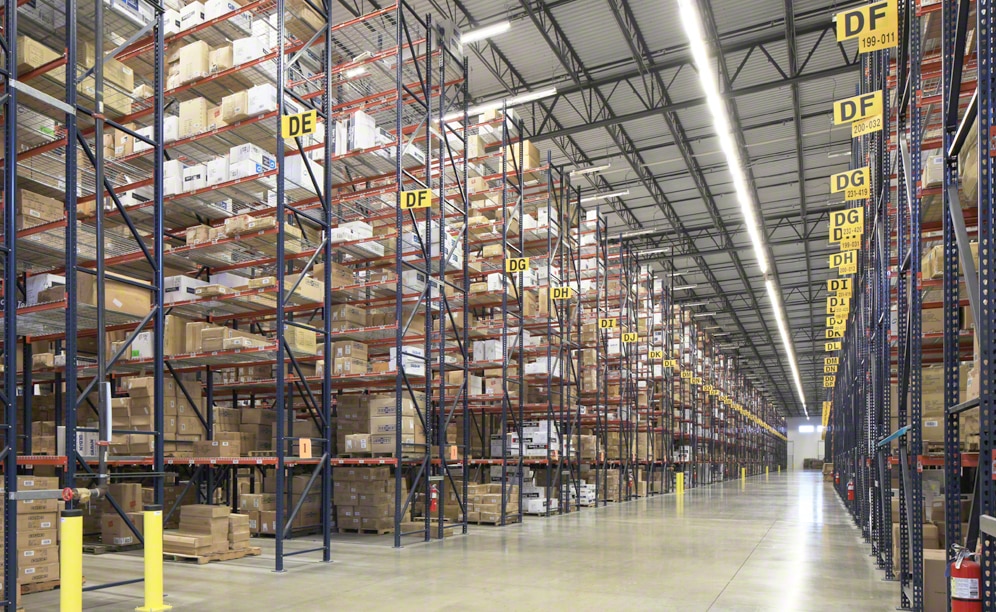
The Clothes Make the Plan: Interlake Mecalux High-Rise Pallet Racking
How SanMar’s new garment distribution center relied on old friends for Pallet Racking results
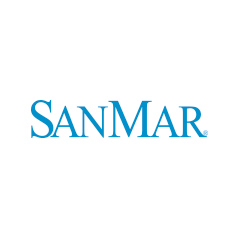
It is noon in Texas, and many warehouse employees throughout the state are preparing for lunch. For SanMar, however, the day is just beginning. The wholesale garment distributor, based out of Seattle, recently expanded eastward into a newly constructed Dallas distribution center. However, at SanMar, the company’s regional distribution centers do not dictate operating hours: the home office does. So while most of Texas awaits 11:30 shifting into noon, it is functionally only half-past nine in SanMar’s 700,000 ft² facility.
The company values efficiency and punctuality over all other qualities of a successful business, which is exactly why the company’s busiest time is later in the afternoon when the day’s orders are in and the personnel stays as late as necessary to see that each shipment makes it out the door. RH Brown, the rack distributor and installer who collaborated with SanMar on the Dallas project, views SanMar’s national synchronization as a boon to customer service. “It’s incredible,” said RH Brown management. “Whenever a company does something a little off the norm and they make it work successfully, it’s worth noting.” Also worth noting is the wholesale distributor’s pattern of growth, which not only expanded outside the Washington area into Texas, but has veined into Florida as well. Nourishing that growth is the increasing footprint of clubs and corporations demanding high-volume garments such as embroidered t- shirts and polo shirts designed for large groups.
Customer’s Needs
With business expanding nationally, SanMar recognized the necessity to expand its warehouse space. Under the current product flow, SanMar receives product by the truckload that is then divided by storage location. Red shirts, for example, go with red shirts; black sweatshirts go with black sweatshirts and so on. As the product comes off the containers into storage locations, the company then re-palletizes the product according to SKU.
Whether the item in question is a size XXXL neon-green polo shirt or a medium-sized plain white tee, the company’s desired turnaround speed dictates that each distribution center inventory enough stored product to facilitate getting anything out the door with minimal lag time, most of the time with less than a day’s turn around. To do that, a lot of product must be on-premises; and to do that, SanMar needed to build upwards and outwards.
The garment wholesaler wanted this installation project organized around its materials. They wanted their distribution center managers to be able to continue working unabated throughout the installation. It was important to SanMar that they had a partner able to insulate the existing operations from having to get involved, while also involving hundreds of other in the contract.
Interlake Mecalux’s Proposed Solution
Few organizations understand SanMar’s growth as much as RH Brown, which has worked with the wholesale garment company since its first 2005 retrofit collaboration in Seattle. RH Brown, the systems integrator specializing in turnkey conveyor and storage packages, also calls Seattle home.
They have synchronized with SanMar’s growth patterns enough so that after the garment company identified the need to expand into larger facilities in Dallas and Jacksonville, Florida, RH Brown had the goods to expand right along with them. “They were looking to build bigger facilities and they needed a partner they could turn to, to handle both facilities,” RH Brown management said, referring to both the Texas and Florida warehouses, “and had the capacity to manage and install both facilities as well as turnkey projects in their entirety.”
Saddled was with a 300,000 ft² building in Dallas that was straining at the seams to handle its product flow. So, SanMar relocated to a new construction more than twice the size of the old building that allowed a more even flow and efficient operation. The trick, in this instance, was going to be creating a design and completing the installation before the building was fully erected. It was no easy task.
Interlake Mecalux partner RH Brown identified SanMar’s business objectives and enacted a design plan that would encompass those goals. The plan aggregated a number of factors including product capacity, shipping ranges, number and volume of SKUs and cubic space. Also of notable importance was the manner in which SanMar wanted to organize the project.
With the design in place, RH Brown worked closely with the contractors in charge of the building’s construction in order to ensure the product would come in on time and had a place to go once it arrived. A big part of the process was the coordination of the on-site schedule for shipping and receiving product.
Once the product made it inside the facility, the installation went smoothly and SanMar was pleased with RH Brown’s decision to use Interlake Mecalux racking. “One of the reasons we turned to Interlake Mecalux for the racking solution was that we needed a solution for the high-bay shelving,” said a spokesperson. “A lot of this racking is 38” tall with beams every two feet.” The solution, in this case, came in the form of z-beams at the ends of the bays. SanMar had been using pallet rack beams to store its products in the previous facility, which was not as reliable.
Products are now stored on Interlake Mecalux high-rise, narrow-aisle, Pallet Racking according to whether or not they are high rotation or low rotation items. The Dallas facility has a primary picking area, which necessitated bulk storage or full case picking. Part of the 38’ high-rise racking is full pallet, part of it is partial pallet and some of it is single-case.
Beyond the rack bracing, Interlake Mecalux proved to be the best choice for the installation because the company had a wealth of regional distribution centers. They could ensure that the product was manufactured and had the logistics to deliver the volume of product.
Almost immediately, SanMar saw its efficiency rise and its daily turnover capacity skyrocket. Today, the garment wholesaler turns over more than four times the orders it did in the original Dallas facility, a feat only partially explained by the increase in storage space. It isn’t just the space, but due to the optimal layout and the durability of the racks that their system is now optimized.
As the clock creeps ever closer to noon in the garment distributor’s new facility, there’s a chance that despite working as if they are running on Pacific Standard Time, these SanMar employees will clock out at Central Standard Time, as they’ve become just too efficient to necessitate staying any later.
Advantages for the Customer
- Raised Efficiency: organized new high-rise racks make input and output to a large network of distribution centers through the U.S. a snap.
- Safety & Storage: qualified engineers dedicated to structural design specified a safe high-rise storage solution able to withstand full pallet loads.
- Product Control: controlled racks means organized products and regulation of stock.
High-Rise Pallet Racking for SanMar Warehouse | |
---|---|
Location: | Dallas, Texas |
Previous Capacity: | 300,000 ft² |
New Facility Capacity: | 700,000 ft² |
Rack Type: | High-capacity, high-rise Pallet Racking |
Storage Type(s): | Full or partial pallets/ 24” span/ Single-case |
Bay Bracing: | Z-beam |
Pallet Depth: | 1 or 2 deep |
Rack Height: | 38” |
Gallery
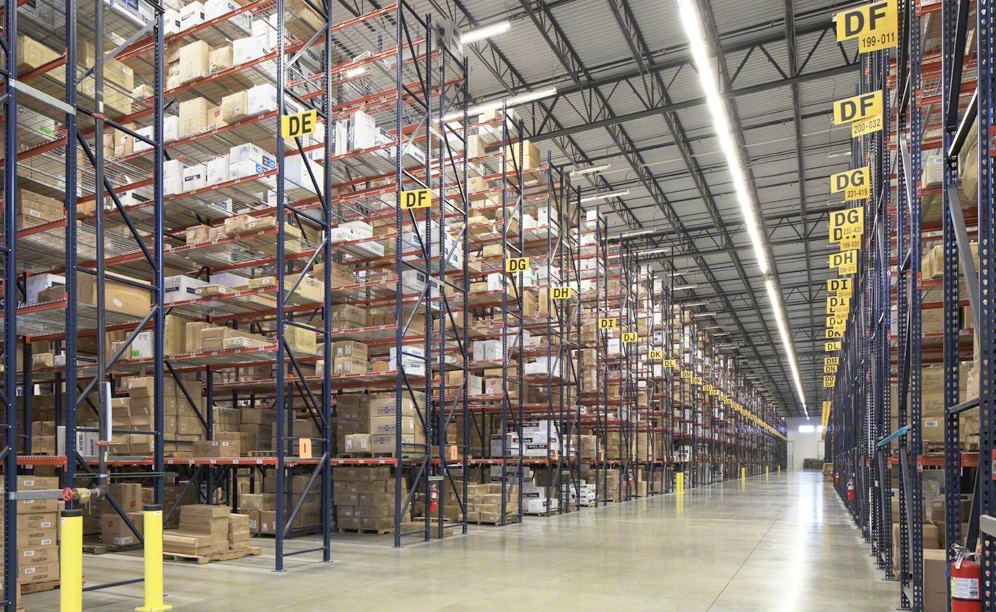
Pallet Racking offers the best solutions for warehouses with palletized products and a wide variety of goods
Ask an expert