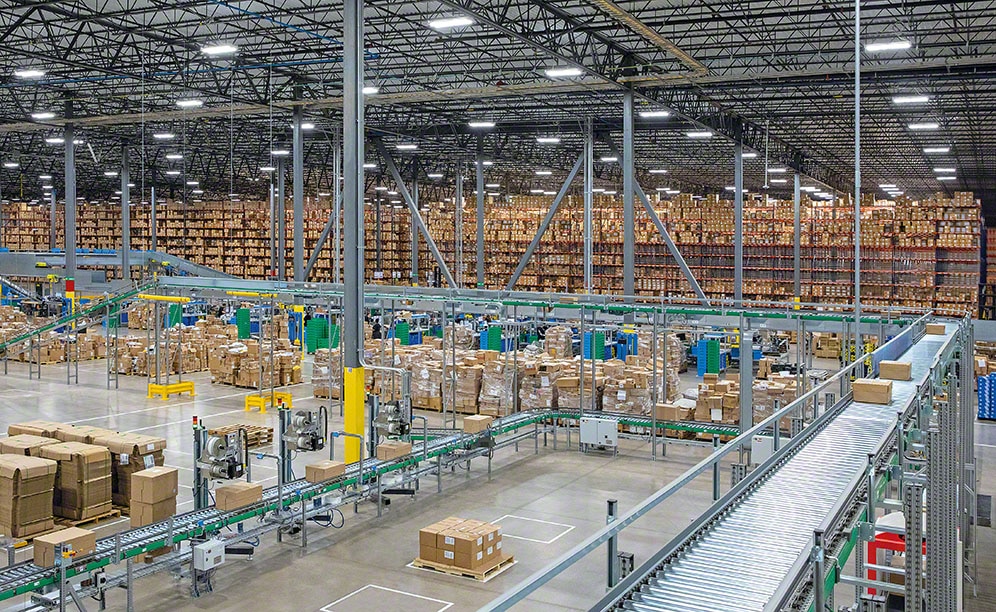
The need for e-speed: New Adidas distribution, fulfillment center designed to move product
Adidas sportswear and footwear are stored on Interlake Mecalux shelves
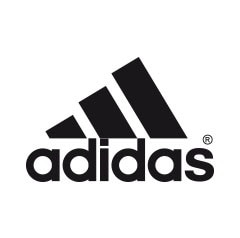
The footwear and sports apparel company Adidas has equipped its Pennsylvania fulfillment and distribution center with Interlake Mecalux storage racking, as well as some selective pallet racking. These racks now house up to 16 million cases of these bulk goods or a massive 71,000 different SKUs, translating into a 35% bigger distribution network. This solution allows for easy access to the company’s products, which enables Adidas to accomplish its goal of preparing orders in two hours.
Adidas: impossible is nothing
Adidas is a German multinational founded in 1949 which manufactures footwear, sportswear and other sports equipment. With a team of more than 57,000 employees and over 900 million products produced each year, Adidas leads today’s global economy as one of the largest suppliers of sporting goods.
Speed to e-consumers
The new fulfilment and distribution centre for world-renowned company Adidas prides itself on its speed. “This building as a whole was built for speed,” Adidas Director of Operations Felix Felder says of the facility in Wilkes-Barre, Pennsylvania..
“The goal of this building was to get our products out in two hours, from the time a customer orders them online to the time they are placed on the truck to ship out.” he said. The company was able to accomplish that goal with help from Interlake Mecalux, which outfitted the facility with the storage racking needed to swiftly move product throughout the building.
The new warehouse services the fastest growing division of Adidas, which is e-commerce, as well as its fastest growing market – North America. Adidas has been growing by double digits – between 20 and 30% – every year for the last five years, especially in North America, according to Felder. This growth necessitated a move into the new warehouse because the company’s network capacity had not changed since 2012.
From the outset, when designing the warehouse’s layout, the objective was very clear. “Throughout the whole building, we needed things that were fast, that allowed us to be efficient and to be flexible. Things change very quickly here. Because we have such a short window to get product out, we needed something that we could flex and change with a couple of minutes notice,” Felder said. The 843,000 ft² state-of-the-art facility provides a full solution for e-commerce and retail fulfillment and distribution, according to Felder. In order to provide the speed the company was looking for, the building needed about 450,000 to 500,000 ft² of racking and a solution that would mean Adidas could pack as much product into that location as possible. The company required reserve racking for the bulk goods that it stores in cases, as well as an area for selective pallet racks.
Felix Felder - Adidas Director of Operations
"The solution installed by Mecalux has enabled us to achieve this warehouse's main objective: to get orders ready and shipped out in the shortest time frame possible. Plus, it has also really helped us improve our warehousing space so that we can achieve a higher storage capacity.".
Flexible and accessible racking
In total, the new Adidas facility features about 492,000 ft² of Interlake Mecalux racking. The main storage area has 68 aisles and the racks are between 23 and 26 bays long, 35’ to 28’ high and have 10 levels. This allows the company to store 16 million cases in 409,000 locations.
When it came to the design of the racking, Adidas wanted a solution that was flexible enough to store oversized items such as golf bags. The racking also needed to be accessible to not slow down the facility’s operational processes, which is why there are two sides of racking with a main lane down the middle. “We don’t want anything to be more than 100 feet from one of our main thoroughfares,” Felder said.
There are also three areas of pallet racking. One area of racks is 40’ high with two individual aisles. Some of the pallet locations are in a high-value cage where the company stores high-end products, such as designer shoes. The last area has about 5,000 ft² of racks for bulky items. Overall, there are a total of 498 pallet locations.
Process flow
The layout of the new Adidas facility facilitates the speed required in order processing. The company receives products as full cases which go onto an inbound sorter that separates them into footwear, apparel and equipment. Operators then place the items onto pallets that travel down a pallet conveyor to the main lane of the storage racking.
The products eventually go into the racks as individual cases in the case reserve area. Once a customer places an order, operators take the products for the order from the racking and bring them to the warehouse’s decant area. In this area, operators remove the items from the cardboard boxes and place them in plastic totes, which then go to an automated system. The system brings the totes directly to a picking station where operators take the items they need for each order and the excess products go back into the automated system.
Once the order is ready, it goes to either a manual packing area or to a highly automated speed packing area to prepare the order for shipment. Then, the orders move to an outbound shipping lane with multiple sorters that assign the orders to a particular freight carrier. The facility’s design accommodates 71,000 SKUs and the warehouse can handle 200,000 units each day, or about 150,000 orders, according to Felder. E-commerce orders average about 1.8 lines per order and orders for retail replenishment average almost 15 lines per order. The warehouse also receives about 17,000 cases per day, mainly from suppliers all over the world and from other Adidas facilities.
Safety first
Interlake Mecalux also worked closely with Adidas on the layout of the warehouse’s racking to ensure the company had the safest possible setup. For instance, the racking needed 6” of flue space in every bay to ensure that water could flow freely in the event of a fire. “That was something that came up after the fact, after the design was already complete,” Felder said. “So being able to build that flue space in was something that was really important.”
Adidas also wanted the racks to be a certain height, but that arrangement conflicted with the warehouse’s sprinkler system. The company needed to make some adjustments to the plan at the last minute to ensure that the warehouse met insurance and safety requirements. “Those were two things that made us change the design slightly at the 13th hour,” Felder said.
“But Interlake Mecalux was able to adapt, give us additional options, give us suggestions on how we could make these things work and the most important thing was to minimize the amount of lost space that we had from a capacity standpoint.” As a result of these efforts, the Adidas warehouse earned the highest possible safety rating that is available from its insurance provider.
Productivity/capacity boost
Overall, the design of the warehouse and its racking has improved productivity 10-fold compared to the company’s other facilities that do not handle e-commerce or retail order fulfillment, according to Felder. “We were able to increase our productivity and that’s due in large part to building this from the ground up and making sure we could design every piece to optimize that quick flow out of the building,” he said.
Capacity also sharply increased as a result of the project. Felder estimated that Adidas increased its network distribution capacity by about 35% with the addition of the facility. These benefits have empowered Adidas to innovate the services that it offers, such as same-day delivery to certain locations or one-day ground delivery without having to charge customers extra for overnight shipping. “We’re able to offer those innovative services to allow us to continue to grow our customer base and meet their needs,” Felder said.
Advantages for Adidas
- Speed: the layout of the Interlake Mecalux racking lets Adidas accomplish its goal of preparing orders for shipment in two hours.
- Greater capacity: the storage racks can house up to 16 million cases – a nearly 35% increase for Adidas in network distribution capacity.
- Highly accessible: warehouse workers are able to easily access the goods in the racks, thereby speeding up storage and order fulfillment.
- Safety: the height of the racks and their flue space are of an appropriate size to accommodate the warehouse’s sprinklers and to ensure water flow in the event of a fire.
Distribution centre of Adidas | |
---|---|
No. of pallets: | 498 |
No. of boxes: | 16 million |
No. of SKUs: | 71,000 |
No. orders/day: | 150,000 |
Gallery
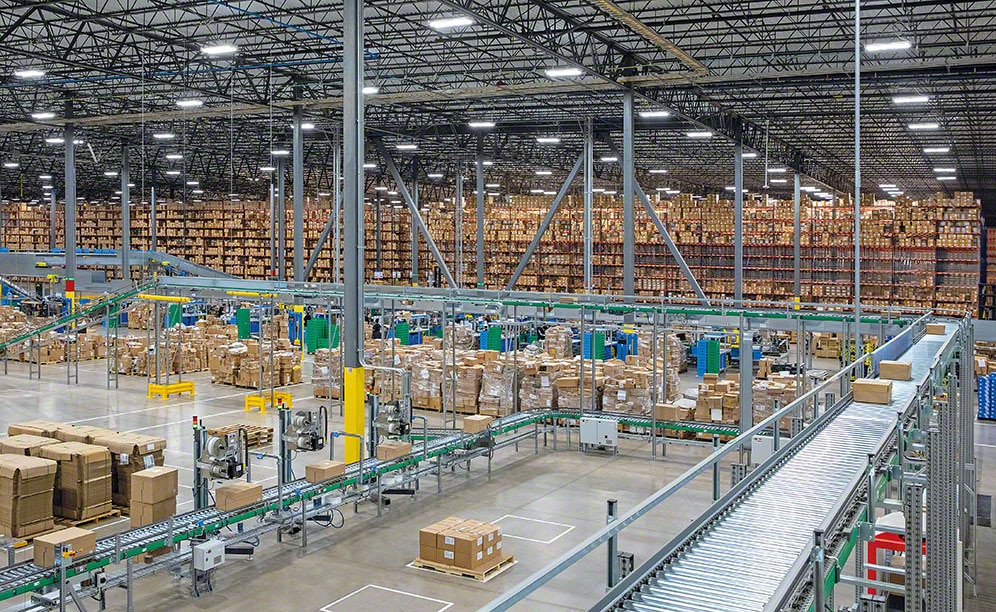
The Adidas warehouse for sports shoes in the United States
Ask an expert