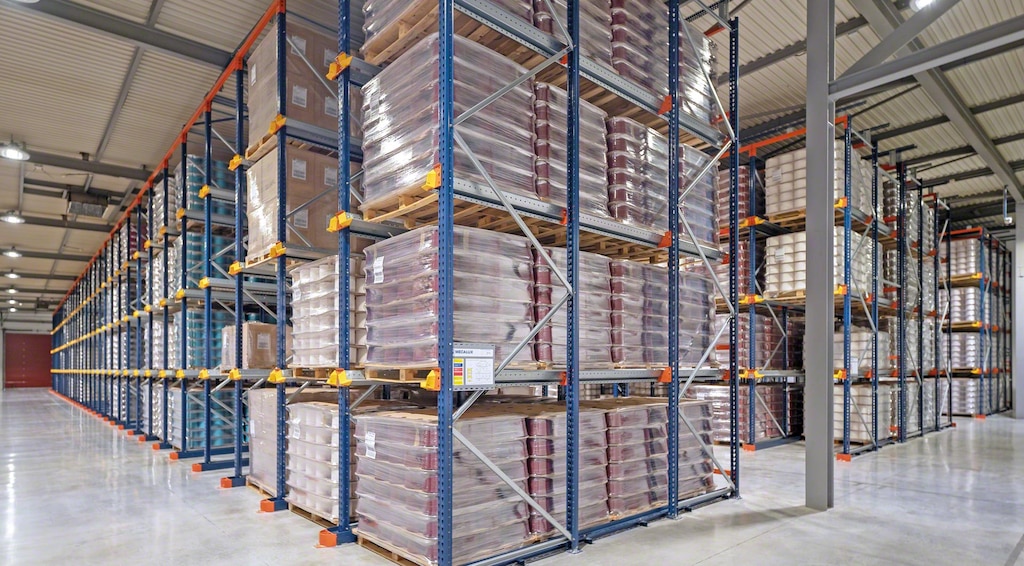
Drive-In/Drive-Through Pallet Racking
The product
Drive-in/drive-through racking system: ideal for warehouses that store large inventories of limited product types
Drive-in and drive-through pallet racks are systems designed for high-density storage. These racks allow products to be stored multiple pallets deep, with handling equipment entering the structure to load or retrieve units.
This system can adopt two configurations: drive-in and drive-through. Drive-in racks operate with a single entry and exit point, following a last in, first out (LIFO) method, while drive-through racks offer first in, first out (FIFO) access by allowing loading on one side and unloading on the other.
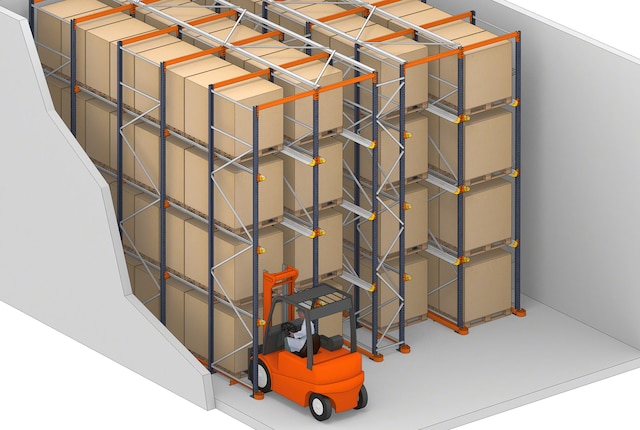
Advantages of drive-in/drive-through racking
- Maximizes space: It makes the most of both floor space and height, increasing storage capacity compared to standard pallet racks.
- Simple and cost-effective: It is the simplest high-density storage system and requires the least investment.
- Customizable: The depth and height can be adjusted to fit each customer’s needs and the type of goods being stored.
- One or two aisles: It can be set up with one aisle (LIFO: last in, first out) or two aisles (FIFO: first in, first out).
- Forklift-friendly: Interlake Mecalux drive-in racks include accessories that guide forklift movements and help position pallets correctly.
- Energy-efficient: A smaller footprint reduces the area that needs cooling in cold storage and freezer warehouses.
- Simplified inventory management: Each lane holds one type of product (SKU), making it easy to track stock.
- Fits various pallets: This system works with pallets of different sizes and weights.
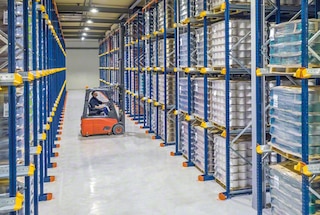
We opted for a drive-in storage system because it’s enabled us to expand our center’s capacity considerably
Drive-in pallet racking applications
Ideal for warehouses with few SKUs and many pallets
Drive-in racking is ideal for companies that manage homogeneous SKUs with a large number of pallets per SKU and want to maximize their available surface area and storage capacity.
How does a drive-in racking system work?
Loading and unloading operations with the drive-in and drive-through varieties
Load management depends on the configuration of the racks. With drive-in pallet racking, storage and retrieval are carried out from a single working aisle. With drive-through pallet racking, two different aisles are used.
Case studies
See more case studiesDrive-in racking components
Interlake Mecalux drive-in racking is engineered in accordance with the 2023 RMI design standards, recognized by ANSI, and referenced in the International Building Code. Its designs also comply with AISI specifications and meet regulations set by IAS.
The structure of drive-in pallet racking is made up of a set of upright frames that provide the system’s vertical support. These frames incorporate interior lanes equipped with support rails, i.e., horizontal profiles on which the pallets are placed.
Interlake Mecalux drive-in pallet racks have a series of components — some optional — that reinforce the safety of the system and help to prevent accidents when forklifts operate inside it.
FAQs
Drive-in pallet racking — also known as drive-through pallet racking (or drive-in/drive-thru racks) — is a high-density pallet racking system made up of multiple racks that form internal lanes with support rails to hold pallets. Forklifts enter the structure, moving inside these lanes to load and unload goods. Thanks to the height and depth of the lanes, this solution makes excellent use of the available space and increases storage capacity compared to conventional pallet racking.
Depending on the type of load management strategy required, this high-density storage system can be configured in two ways: drive-in or drive-through racking. In the first and most common variety, loading and unloading operations are carried out from the same working aisle. Thus, stock is managed following the LIFO (last in, first out) principle. With drive-through racks, on the other hand, pallets are deposited and retrieved in two different aisles: goods go in on one end and are removed from the other. In this case, the loading/unloading sequence is done in line with the FIFO method (first in, first out). This configuration is typically employed when the system is used as a buffer or interim warehouse to effectively regulate flows between two work areas (for example, between production and shipping or between different manufacturing stages).
The drive-in/drive-through racking system is a compact storage solution that meets a wide range of requirements. Its storage capacity is greater than that of conventional racking. Additionally, it is the simplest and most affordable system compared to other high-density storage solutions. However, since the forklifts have to enter the racking, more maneuvering time is required for storage and removal operations. Furthermore, as each storage lane is reserved for a single SKU, drive-in pallet racking is not recommended for warehouses that manage a broad array of products. For these scenarios, Interlake Mecalux has other compact solutions that facilitate the management of more diverse goods. These include Pallet Flow Racks, Push Back Racking Systems and the Pallet Shuttle system.
There are no structural limitations to a drive-in racking system design. However, the maximum height of these racking units will be conditioned by the maximum lifting capacity of the handling equipment employed and by the maneuvering assistance systems they incorporate (camera, height pre-selector, etc.).
The height of each drive-in racking storage level is determined by the height of the pallets and the construction system used (either GP, C, Z, FC, or DR rails). For GP, Z, and FC rail systems, the storage level height equals the pallet height plus 8" to 10", while for C and DR rail systems, it equals the pallet height plus 10" to 12".
The depth of each lane is the sum of the depth of all the pallets (including the load dimensions if the load overhangs) plus a clearance per unit load of at least 1". Meanwhile, the number of pallets stored in each lane is usually a multiple of the production batches or of the pallets that fit in a truck. For instance, the lanes of a drive-in unit used to store finished orders could be designed to hold 11 pallets deep and 3 high. This would add up to the 33-pallet capacity of a trailer.
To achieve maximum efficiency, all pallets deposited in the same storage lane should have the same SKU. This avoids unnecessary handling.
Depending on the type of pallets to be used, both the width and depth can serve as the loading side for the system. GMA pallets are recommended to be loaded by their width, while CHEP pallets can be loaded by the width or depth. The loading equipment should also be considered since this will also affect the required bay width.
Drive-in racking uses both counterbalanced forklifts and reach trucks. Counterbalanced forklifts typically reach up to 25', while reach trucks can go beyond 40'.
Since forklifts operate inside the storage lanes, it is important to ensure there is enough clearance for safe movement. There should be at least 3" of space between each side of the forklift and the vertical racking elements. Additionally, the first level of support rails must be high enough to avoid interfering with forklift parts, like the cab enclosure.
Ask an expert