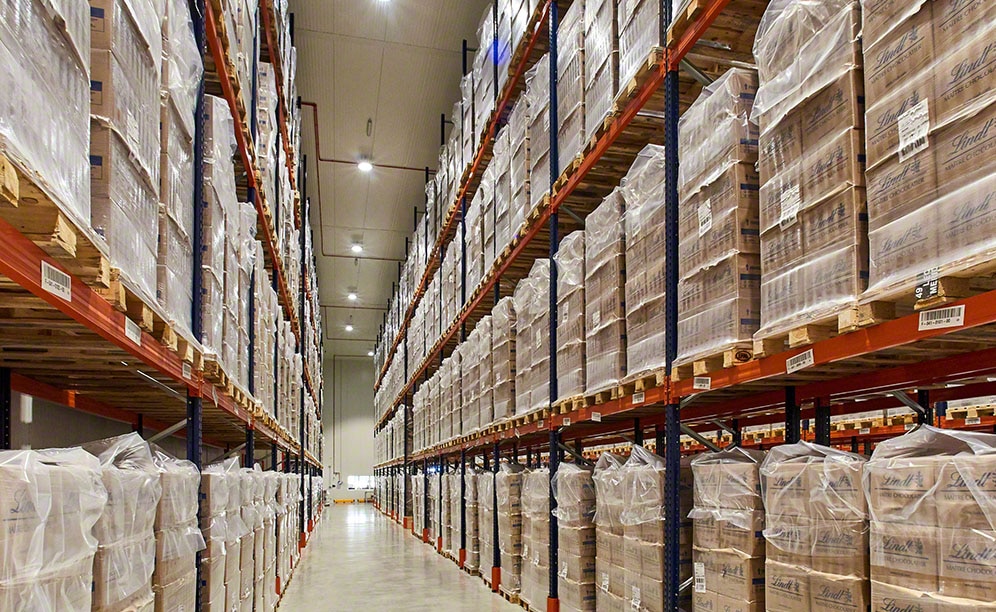
Pallet and push-back racks at the Brivio & Viganò warehouse in Italy
Interlake Mecalux racking in Italy for the food of logistics operator Brivio & Viganò
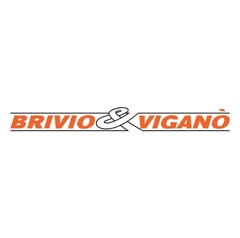
A logistics operator specializing in food products such as Brivio & Viganò must have a dependable warehouse, with an efficient organization of the goods and quick operations to store and distribute orders in the best conditions possible. The company has opened a 7.4 acre logistics center in Pozzuolo Martesana (Italy) with seven cold-storage chambers that Mecalux has equipped with two storage systems: pallet and push-back racking. The racks, specially designed and reinforced to absorb forces generated by seismic tremors, provide a storage capacity of 29,336 pallets.
Organization and transportation
Brivio & Viganò is a well-known Italian partner in the distribution and integrated logistics sector for food products. The company began in the mid-70s, when Luigi Brivio and Giovanni Viganò decided to develop a network of local supermarkets to sell a wide range of high-quality products.
Over time, the company has combined its experience and expertise in transportation to revamp and consolidate itself as a leading logistics operator in the Italian market. After nearly 40 years in business, it has grown from just two trucks to more than six hundred.
“Our goal is to continue growing and improving progressively, as we have always done since we first opened our doors. In the last ten years, we have expanded thanks to investments and cutting-edge technology and innovation,” said Stefano Brivio, Managing Partner of Brivio & Viganò.
Logistics you can trust
“Today, Brivio & Viganò has succeeded in positioning itself as one of Italy’s leading players in the comprehensive temperature-controlled food logistics sector, with solutions tailored to its customers,” Stefano Brivio said. The company is fully aware that to keep leading the market in the coming years, customer trust and support are essential. For this reason, logistics takes on special importance.
In Italy, Brivio & Viganò has a total of 36 acres dedicated to product storage and order preparation. To supply its national clientele, it has set up a 7.4 acre warehouse in the community of Pozzuolo Martesana, consisting of seven cold stores: two for refrigeration (31.3 ºF) and five for freezing (-11.2 ºF).
According to the Managing Partner, the company was looking for “a solution that would help us maximize storage capacity in both floor space and height. Also, it was imperative that the storage system be certified to be seismic resistant.”
The company’s stock is very diverse and includes more than 8,000 different items with different sizes, weights, heights, characteristics and demand levels. It was clear to the company that one of its priorities was to manage a wide variety of goods correctly.
Another of its needs was to streamline operations. This warehouse stands out for being high-paced (i.e. goods in motion). So, the racks must make an operator’s work easier. Many pallets are received daily from suppliers. Meanwhile, around 150 orders are prepared and distributed to Europe, the United States and Asia.
With all these requirements firmly in mind, “we compared the storage solutions proposed to us by all the different vendors who participated in the bidding process. We chose Mecalux because its offer met all the basic technical needs,” Stefano Brivio explained.
The Interlake Mecalux solution is based on installing pallet racks and push-back racks with a total storage capacity of 29,336 pallets. Interlake Mecalux has taken the specifications laid out in the Italian NTC 2008 and European UNE-EN 16681 standards into account to design and construct the racks. This means they have been specially reinforced to withstand any potential earthquakes that may occur in the region, guaranteeing the safety of both operators and the goods.
The combination of these various solutions means the goods can be sorted as per their characteristics and level of demand. A well-organized warehouse has an impact on all operations: when operators carry out storage or order picking tasks, they know which areas they should go to, gaining speed and efficiency.
In short, as Stefano Brivio commented, “The proposed solutions have been adapted to our specifications. They have the right seismic resistance and have helped us to optimize warehouse space in a major way”.
Features of the pallet racks
Divided between three and five levels, they stand 34.5’ tall and hold around 28,388 pallets.
These racks are equipped with elements and components to adapt the levels and shelf surfaces to the characteristics of the goods. They are ready to store any type of load, with variable weight and volumes. The versatility of pallet racks makes them ideal for handling such heterogeneous goods.
These racks offer direct access to products, a feature that streamlines their inflows and outflows; in fact, this has a direct impact on order preparation. Pallets are picked directly off the lower levels of the racks, while reserve products are picked off the higher levels. With this system, goods are on hand and ready at all times to avoid disruptions to operations.
Push-back racks
The racks consist of a series of channels arranged with a slight incline. The front part is lower so that when a pallet is removed, the rear pallets move forward by gravity to the front position.
These racks make good use of the available space by holding three pallets deep in each channel. At the same time, they make merchandise handling much more agile, since operator maneuvers are kept to a minimum. Operators have all the different SKUs at their fingertips in the same aisle, so walking distances are very short.
Voice picking devices
Operators are aided by a voice picking system to prepare orders. These voice picking devices are connected to the warehouse management system and convert orders into voice commands that the operator hears on their headset.
Once executed, the operator speaks into the device to confirm their movements. Then, the information is logged in the system automatically. The big plus of voice picking is that it gives the worker greater freedom of movement and a wider field of vision, reducing errors and making operations more dynamic.
Putting the “S” in satisfaction
Brivio & Viganò performs an essential function within the logistics chain: supplying its customers with the requested products. So, it is always a race against the clock. To get to the finish line, impeccable organization is a must for all its processes, as well as modern, flexible logistics processes. This adds value for the various companies in the food sector with which it works.
“We are very satisfied with the storage solutions installed,” said Stefano Brivio, Managing Partner of Brivio & Viganò. Its new cold store is equipped with two earthquake-proof storage systems that help organize products based on their characteristics and demand level. This is a basic tenet to ensure operators are more productive when preparing 150 orders per day. Both warehousing solutions also guarantee that food is stored and distributed in the best possible conditions.
Advantages for Brivio & Viganò
- Maximum storage capacity: the two storage systems optimize the cold store’s volume to accommodate 29,336 pallets.
- Merchandise organization: each product is deposited in the appropriate storage system based on its characteristics and level of demand.
- Efficient handling of goods: Mecalux’s storage solutions are designed to facilitate the processing of 150 orders per day.
- Earthquake resistant: the racks are calculated and specifically reinforced to withstand any seismic movement that may occur.
Cold-storage chamber Brivio & Viganò: Pallet racks | |
---|---|
Storage capacity: | 28,388 pallets |
Pallet size: | 32” x 47” |
Max. pallet weight: | 1,984 lb |
Racking height: | 34.5’ |
Gallery
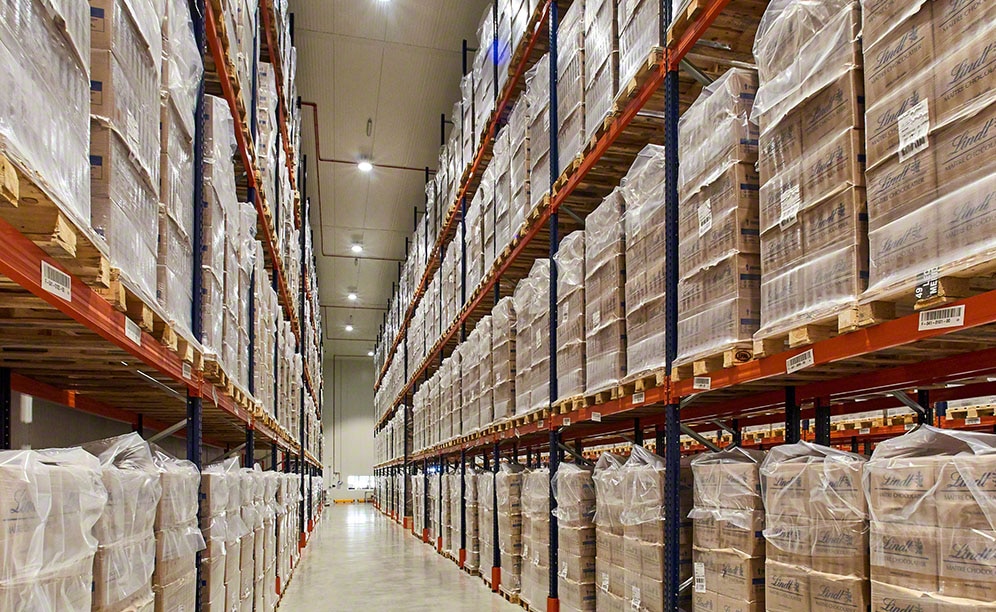
Pallet racks at the Brivio & Viganò warehouse in Italy
Ask an expert