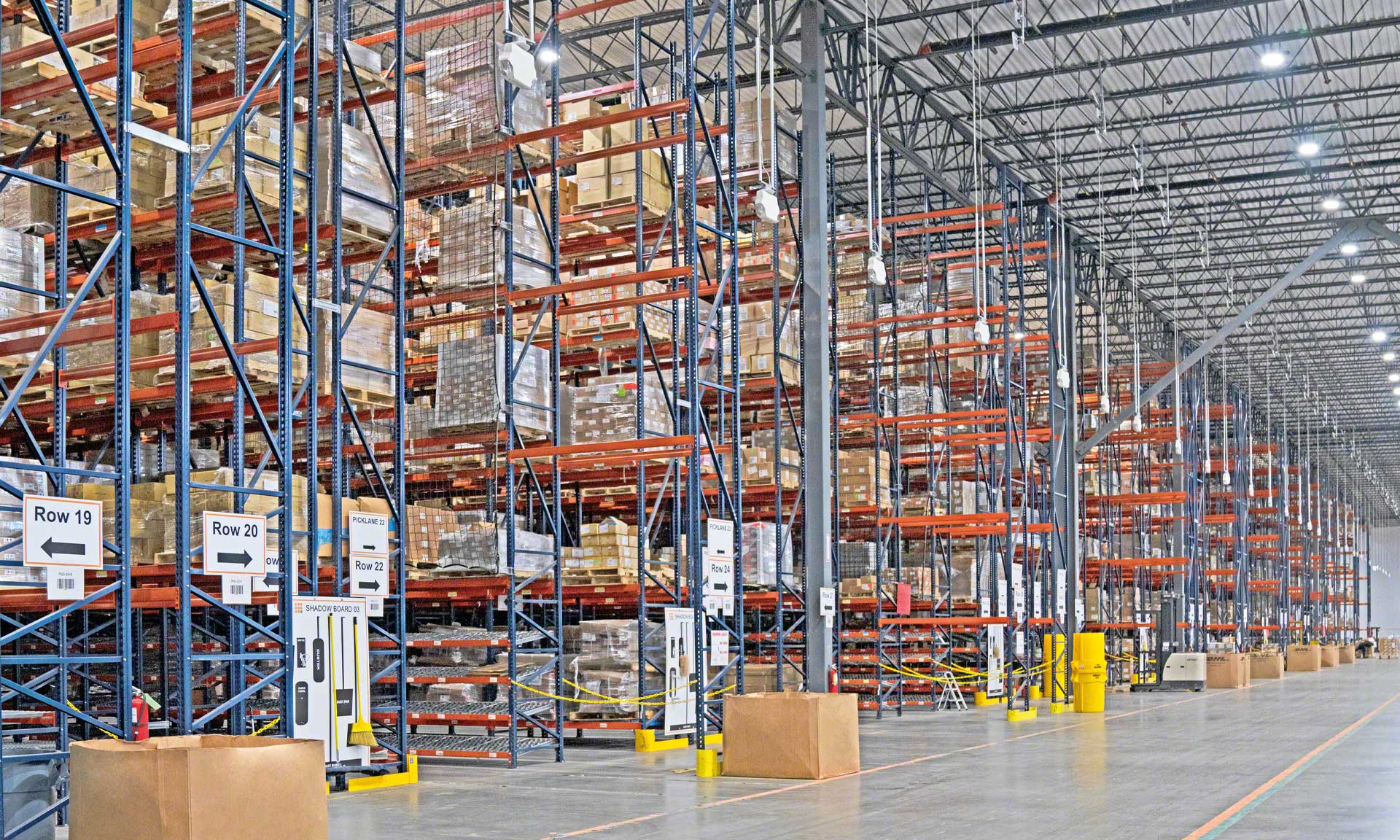
Multiple solutions to expand Capacity's storage capacity
The facility of warehousing services provider Capacity incorporates several productivity-enhancing systems.
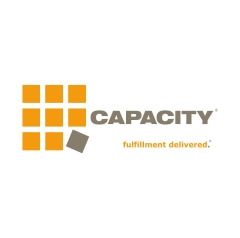
Capacity, a comprehensive order fulfillment and warehousing provider, has installed several storage systems in its New Jersey logistics center. The new facility features multiple solutions to boost the capacity and productivity of logistics operations.
Capacity: a comprehensive order fulfillment and warehousing services provider
Capacity and its team of highly responsive engineers, client service professionals, and warehouse associates offer engineered solutions for comprehensive order fulfillment and warehousing. Founded in 1999 by Jeff Kaiden and Thom Campbell, the company’s vision entails innovation in fulfillment technology and customer satisfaction.
- Founded in: 1999
- International presence: warehouses in Indiana, Los Angeles, New Jersey, the UK, and an office in India
CHALLENGES
|
SOLUTIONS
|
BENEFITS
|
---|
A comprehensive order fulfillment and warehousing provider such as Capacity requires nimble fulfillment operations, including product storage and order processing, packaging, and distribution.
With five buildings already bursting at the seams due to the company’s incessant growth, Capacity decided to expand its operations by constructing another 300,000 ft² facility in North Brunswick, New Jersey, with the goal of increasing operational efficiency and productivity.
To do this, Capacity needed to outfit its new building with storage systems that would adapt well to the various types of loads it stores to cater to its wide variety of clients. And it needed the building to be operational in a short period of time to handle its ever-expanding client base. Capacity also needed to optimize its surface area to increase storage capacity while maintaining operational agility.
The company selected Interlake Mecalux and its partner ABCO Systems to help design and install racking systems that would meet the business’s needs and be installed within Capacity’s tight timeline.
“Interlake Mecalux and ABCO are great companies to work with. Everything comes on time, and it’s all made well,” says Paul Jakobovic, Industrial Engineer at Capacity. “Their diverse rack offerings have helped us store more in our facility than we thought possible.”
More than 120,000 ft² of pallet racking
Pallet racks are the most universal system for direct access to each pallet, and the direct access offered by Capacity’s pallet racks is essential for the company to handle the frenetic pace of operations. The warehouse features approximately 120,000 ft² of racking. The pallet racking’s strength, versatility, and adaptability to any type of load are some of its key features. Capacity’s racks stand 38' tall with 20 different elevations/configurations.
Overall, the facility can accommodate approximately 17,500, 40” x 48” GMA pallets at two or three pallets per level. This allows the racking to store a wide variety of products of different sizes and weights. To make the most of Capacity's storage space, Interlake Mecalux minimized the size of the racking aisles.
Complementary storage systems
The warehouse also contains a mix of push-back racking, pallet flow racks, and carton flow shelving. The push-back racks are 22' tall and made up of a number of channels arranged with a slight incline. The front portion of the racking is lower so that when an operator removes a pallet, the pallets behind the initial one move forward by gravity to the front position. Operators have access to the different SKUs in the same aisle, so travel in the warehouse is minimal. The racking operates based on the LIFO (last in, first out) method, in which the first pallet introduced into the system is the last to leave.
Based on the same gravity flow principle, but operating under the FIFO (first in, first out) system, the pallet flow racks are 36' high and contain a set of slightly sloped channels that make it easy for the pallets to properly move from the highest part (entry point) to the lowest part (exit point).
Lastly, Interlake Mecalux installed carton flow storage on some of the lower levels of the pallet racks. This allows for efficient order picking, as the boxes containing the merchandise that operators need to retrieve are always available. Like the pallet flow racks, carton flow racking enables perfect product turnover using the FIFO system: operators deposit the goods at one end, and they slide safely and gradually via gravity to the picking aisle. Carton flow racks also separate picking and stocking tasks into different aisles, thereby avoiding interference between the two operations.
Future-ready warehouse
By installing several storage systems, Interlake Mecalux has provided Capacity with higher storage density. Consequently, the company can now prepare more orders — as well as larger orders for its premier customers.
Capacity was able to raise its productivity while maintaining the same footprint. This reduces the need to take on an additional facility, all with the peace of mind that the Interlake Mecalux racks were well-built to stand the test of time.
Interlake Mecalux and its partner ABCO worked closely together to deliver the racking on tight timelines and provide fast, efficient installation that now enables Capacity to cope with its pace of growth.
Thanks to the different storage systems installed, we've increased our storage capacity in a reduced space. We can now store more products than we thought possible.
Ask an expert