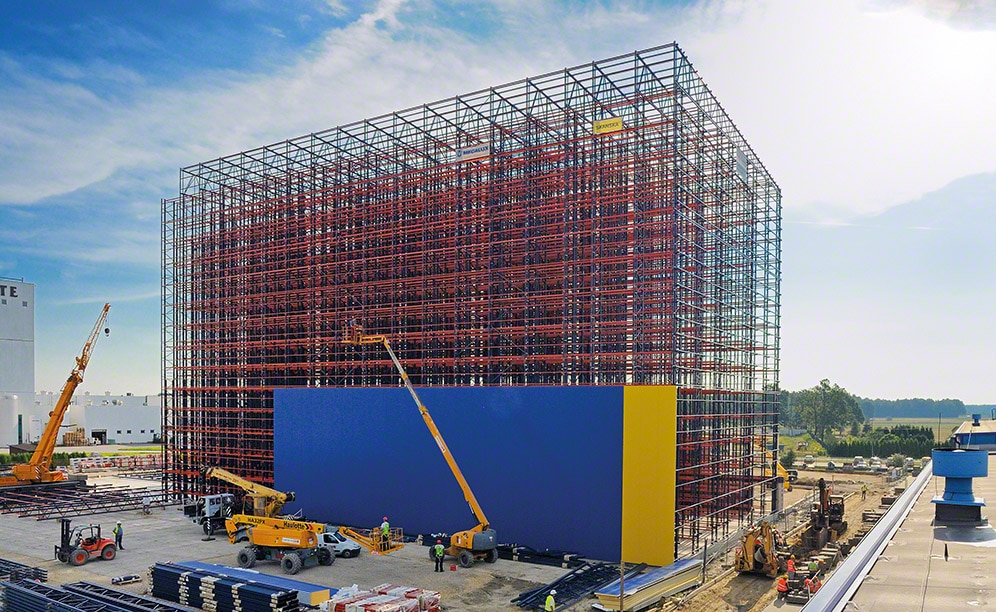
A rack supported warehouse for the Lakma chemicals company
Picking is one of the primary operations of the Lakma clad-rack warehouse
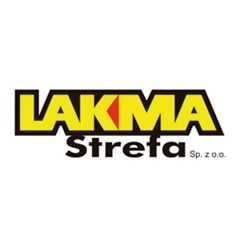
Picture a fully-automated, 105' high rack-supported warehouse built key-in-hand, with all goods managed smoothly and efficiently by the Easy WMS of Interlake Mecalux; then, add storage capacity for 15,428 pallets. That is ‘Multisoft’ in a nutshell, the 47,361 ft² sophisticated logistics complex of Lakma Strefa –one of the most cutting-edge chemical companies in Poland–, located in the town of Warszowice, in the southern region of the country.
Leader in chemical product manufacturing
Lakma Strefa is a Polish chemical products company, whose goods are used in different industrial sectors, such as in construction, household care, professional chemicals and thermal insulation.
In 1988, the company installed its first plant in the city of Cieszyn (close to Czechia), allocated to chemical products for the building sector, in addition to varnishes and paints. Only five years later, it expanded its business by offering household chemical products.
The 1998 construction of a new manufacturing center in the town of Warszowice, Southern Poland, was explicitly built to deal with business growth.
“Our company is flourishing, and our customers demand faster and faster product distribution, not only nationally but also to foreign markets,” explained Maciej J. Paluch, President of Lakma Strefa. The business boasts a massive distribution network that stretches through the vast majority of countries within the European Union. As a result of this expansion, Lakma Strefa has updated its laboratories, manufacturing center and warehouses, and has set up technology in as many processes as possible.
The firm reached out to Interlake Mecalux to build it a new 1.05 acre fully-automated distribution center. This project was dubbed ‘Multisoft’. Automating, in the words of Maciej J. Paluch, has allowed, “maximum optimization of the supply chain, from the storage zone up to picking orders for our customers.”
Maciej J. Paluch - President of Lakma Strefa
“Its experience in carrying out similar international projects was key when we chose Interlake Mecalux to be solely in charge for our project. Our new warehouse means we have boosted storage capacity, improved productivity and goods management, and reduced personnel and maintenance overhead.”
Building Multisoft
Interlake Mecalux erected the Multisoft rack supported structure over a period of eleven months. Situated on a tract of poor-quality land that could not support such a huge, heavy building like the one that was designed, it had to be built on top of 254 serially bored foundation piles.
A 13" thick concrete slab rests on 220 out of 254 foundation piles. Then, the racks that comprise the rack supported installation were placed on top of this slab. A layer of fiber cement paves the remaining 31 piles, upon which a building was erected for pick tasks, entries and exits, business offices and the changing rooms.
Multisoft is a cutting-edge, high-tech project, which is why fire safety was a priority. For this reason, Maciej J. Paluch points out, “The design and construction of this warehouse required our involvement, as well as the collaboration of Państwowa Straż Pożarna (a fire suppression service provider in Poland) so that the building would comply with all safety standards.”
Multisoft: a modern logistics center
Multisoft is an automated rack supported warehouse featuring four aisles of double-deep racks on each side. These racks are 105' high and 265' long, with fourteen storage levels, and provide a 15,428-pallet storage capacity.
The company opted for the double-deep rack because Lakma Strefa’s stock often includes many pallets of each SKU. This solution doubles the storing capacity in comparison with the single-depth system, without lowering the output of the warehouse.
The business has directly benefited from the technology, speeding up processes to do with storage, order picking and dispatching of goods. Thanks to this, Lakma Strefa has pulled off workflows of 162 pallets/hour.
A single-mast stacker crane circulates in each aisle, operating at a speed of 524 ft/min and 125 ft/min when raised. The equipment runs storage tasks that, in a traditional warehouse, would be done by forklift operators. Its job is to move goods between racking slots and the input-output conveyors set up at one end of the aisle. In-warehouse stacker cranes have telescopic forks to access the second pallet of each location.
The logistics center is managed in its entirety by the Easy WMS warehouse management system of Interlake Mecalux. According to Grzegorz Stokłosa, Interlake Mecalux Sales Manager in Poland, “through radiofrequency devices, it lets us control all in-warehouse processes, from receipt orders to those for dispatches, as well as the stock of stored goods.”
Soaring productivity just next door
A shorter, 26' tall building was constructed along one of the sides of the warehouse and occupies a 23,034 ft2 surface area. It is allocated to incoming and outgoing goods and order prep.
This is a bustling zone and, as such, has been specially designed so that all operations are done in the most efficient manner.
Warehouse inputs
Every day, the installation receives 70 pallets from other manufacturing centers or suppliers. Workers insert pallets onto the input conveyors and, soon after, the goods pass through a checkpoint where their size, weight and status are verified to see if they match the quality requirements laid down for the AS/RS. Once the pallet is accepted, a double-capacity transfer car collects the load and takes it right up to the storage aisle assigned by Interlake Mecalux’s Easy WMS warehouse management software.
An entry point was also opened up for goods flowing directly from the plant (around 130 pallets/day), located in premises next to the warehouse. The two buildings are interconnected via a raised, roofed-in overpass.
Order picking
Picking of goods is central to Multisoft’s operations. Dozens of orders are prepared each day in a specific warehouse area enabled with gently-inclined flow channels, meaning pallets move via gravity from the highest to the lowest point.
Operators access pallets directly at the front of the channels, picking boxes listed in each order with the assistance of ground-level order picker equipment. Everything is done according to the instructions the Interlake Mecalux Easy WMS warehouse management system shows on the radiofrequency devices.
Warehouse outputs
On a daily basis, an average of 180 pallets flow from the warehouse, although dispatches can swell to more than 600. Despite the fact that most orders require some prior preparation, entire unsplit pallets are also distributed.
For these cases, three fast-response exit points were installed in the flow channels for picking. Operators collect pallets using forklifts and insert these pallets directly into the transport vehicle to be shipped out.
ADVANTAGES FOR LAKMA STREFA
- Maximum warehouse capacity: Multisoft obtains a 15,428 pallet storage capacity by making good use of its 1.05 acre floor surface.
- Efficient warehouse management: faster, error-free customer care can be guaranteed by automating all operations.
- Swift pickings: setting aside an entire zone specifically for picking means dozens of orders can be prepared per day.
Automated rack supported warehouse of Lakma Strefa | |
---|---|
Storage capacity: | 15,428 pallets |
Pallet size: | 32" x 48" x 63" |
Warehouse length: | 265' |
Max. pallet weight: | 1.1 t |
Warehouse height: | 105' |
No. of transfer cars: | 10 |
Gallery
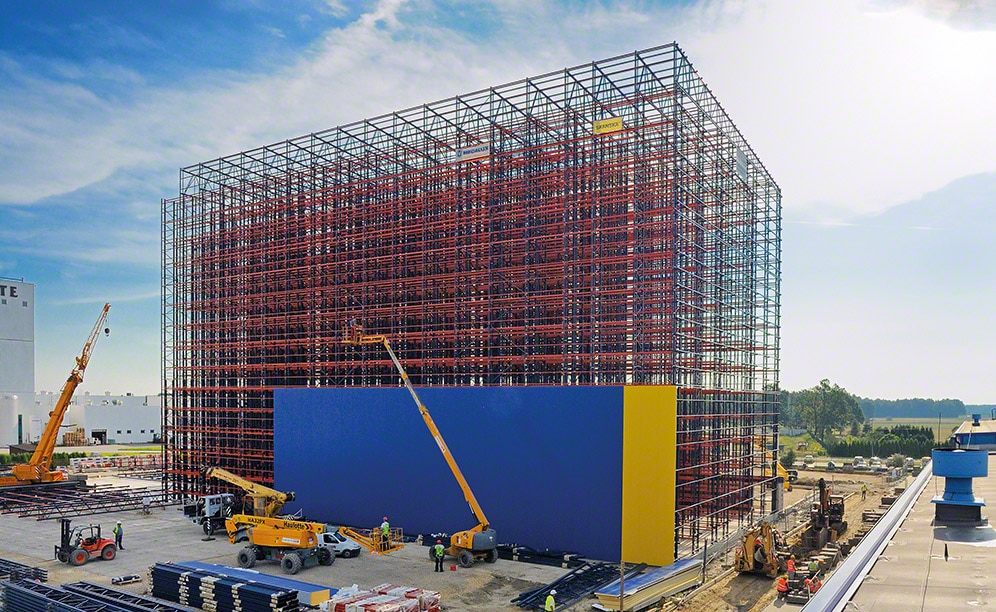
The clad-rack warehouse of the Lakma chemicals company in Poland
Ask an expert