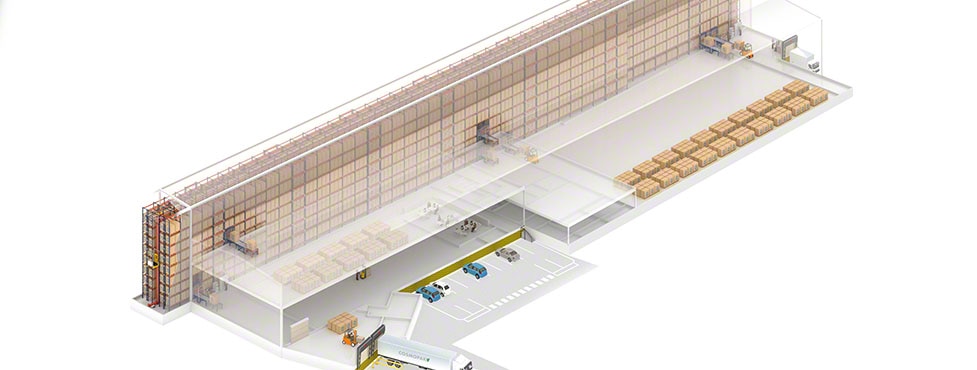
Cosmopak: one aisle, two temperatures and thousands of SKUs
In the aisle, pallets are organized based on whether they are raw materials or semi-finished or finished products
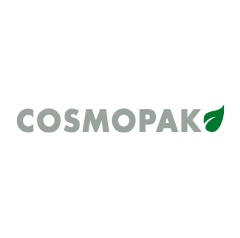
Is it possible to store finished products, semi-finished goods and raw material in pallets, big bags and IBCs (intermediate bulk containers) in a single aisle with both cold and ambient temperatures? Cosmopak, a company dedicated to producing and packaging cosmetic products, has opened a versatile, personalized, 486-foot-long automated warehouse at its logistics center in Ovar, Portugal. Connected to production at three different levels, the installation manages over 2,500 SKUs. Easy WMS provides the traceability and adaptability needed to ensure that customers and the production lines are provided with goods whenever required.
The road to innovation
Cosmopak is devoted to the manufacture and packaging of cosmetic products such as body gels and lotions, shampoos, conditioners, and colognes. Since it was founded in 1999, this firm has stood out for its constant innovation, striving to minimize its environmental impact and adapting to a demanding, ever-changing market.
Its day-to-day activities consist of developing new packaging lines, using high-quality yet affordable materials to manufacture its cosmetics, and working closely with customers to offer them personalized solutions that exceed their expectations. The business aims to prepare and send samples to companies that request its services in less than 48 hours.
Cosmopak has a production plant in Ovar, northern Portugal. There, it manufactures all the goods that are distributed to its customers throughout Europe. Just beside that site is its 11,464 ft2 installation, where over 2,500 SKUs — comprising raw materials as well as semi-finished goods, finished products, and packaging — are managed.
The raw materials include gels, shampoos, and fragrances used to manufacture the cosmetics and stored in IBCs (for liquids) and big bags. Meanwhile, materials used to package the products include bottles, tops, and cardboard boxes.
In terms of the functions of the warehouse, Cosmopak owner Javier Fernández explains, “On the one hand, it supplies production with the raw materials needed at just the right time. On the other, it stores and dispatches the finished products when necessary.” All aspects must be controlled, from the temperature at which the raw materials are kept to the goods flows.
Recently, Cosmopak has expanded its installations to meet the increased demand seen over the past few years and, thus, add new production lines. As the production plant was restructured and the workload grew, the firm was forced to update its supply chain. Javier Fernández says, “We were looking for a solution that would allow us to store a large number of goods in a limited area. We had a restricted space, so we had to take advantage of every last inch.”
Moreover, since Cosmopak manages such diverse products, its owner emphasizes, “We wanted to optimize flows in the plant and installation and, at the same time, accurately track each item.”
Cosmopak is an extremely modern company that has always incorporated the latest technological advances in its processes to be more competitive and guarantee the utmost quality in its products and services. Automation was an essential requirement in this modernization project, as it would maximize the height and available surface area to accommodate all the products.
To drive this project forward, Cosmopak got in touch with Mecalux because, according to Javier Fernández, “It is a firm with vast experience in implementing all kinds of logistics solutions. The assurances they gave us convinced us to make this investment.”
After analyzing Cosmopak’s needs, Mecalux proposed setting up an automated installation run by the Easy WMS warehouse management system. Of all its advantages, the software stands out for boosting productivity in goods handling and providing complete control of the stock used in the various production processes.
Layout of a very long aisle
The Cosmopak warehouse is formed by a single 486-foot-long aisle aisle with double-deep racking on each side that provides a storage capacity of 3,800 pallets. A stacker crane runs down the aisle, carrying out goods movements from the warehouse entry points to the location assigned by Easy WMS to each item.
The storage aisle has been adjusted to the dimensions of the installation to leverage all available surface area, spanning the length of the premises. Concentrating all activity and goods in the same aisle, however, requires criteria that prevent errors when it comes to distributing the merchandise. Easy WMS plays a vital role in organizing the goods, as it decides where to place each pallet based on its demand level, its specific features, and whether it contains raw material, semi-finished goods, or finished products.
Raw materials can be stored at an ambient or cooled temperature (liquids stored in IBCs), while semi-finished goods and finished products are housed at ambient temperature. Therefore, at one end of the aisle, the temperature is constantly maintained at 68 ºF.
Finished products, meanwhile, are deposited closer to the dispatch docks to streamline their distribution. Products in big bags are very heavy, weighing up to 1.32 t. Consequently, they are placed solely on the lower level of the racks.
Connection and integration
One of the particular features of the Cosmopak warehouse is the connection and integration between the installation and the various production processes. The automatic handling equipment provides continuous and safe goods flows, supplying the different production areas with the raw materials needed to manufacture the perfumes and cosmetics.
With such a large amount of goods movements between so many different work areas, Javier Fernández affirms, “We needed greater stock control and traceability.” Easy WMS is charged with monitoring the products throughout the various processes they go through and, at the same time, organizing shipments of the goods to their required destination.
Easy WMS is integrated with the SAP ERP at Cosmopak in order to get the most out of the warehouse operations. The two systems transfer data continuously on the different processes being carried out. Easy WMS manages the following processes:
Goods entries
Every day, the installation receives multiple pallets from two possible sources: production or suppliers. In the case of the latter, Easy WMS directs operators using radiofrequency terminals to place the pallets on the corresponding inbound conveyor.
All pallets must go through a checkpoint, where their dimensions are verified. If the measurements fall within the corresponding ranges, the WMS decides where to place the goods.
To be stored in the automated warehouse, the products have to be palletized. If they are not, the operators need to group together the loose products and place them on a pallet, following instructions from Easy WMS at all times to avoid any potential errors.
Storage and control
Traceability is key at Cosmopak’s warehouse. All items are identified by a barcode, enabling Easy WMS to carry our rigorous tracing of the more than 2,500 SKUs available.
Knowing the status of goods in real time helps the company reduce errors and take correct action in different situations. For example, when the installation is about to run out of a product, the ERP can request more from the suppliers.
To comply with good practices in manufacturing cosmetic products, Cosmopak must closely monitor its IBCs, as they have a very long useful life and are reused several times a year. For this reason, it is necessary to register all related movements (receipt, location, emptying of product, washing, filling, etc.), which the system stores for a maximum of four years.
Goods dispatch
Every day, 150 pallets leave the warehouse with two possible destinations: production or the loading docks.
The dispatch process begins when the ERP notifies Easy WMS of the products that need to be shipped. Regardless of destination, the WMS organizes them according to the FIFO (first in, first out) system.
In production, the operators pick the pallets and move them as required. At the docks, the products can be sent to customers or to Cosmopak’s central warehouse in Madrid.
Automation and digitalization
Thanks to automation, Cosmopak has an efficient, fully optimized supply chain. Undoubtedly, having such a complete and personalized installation has provided the company with a competitive edge and significant savings in logistics costs.
The new automated warehouse enables the firm to manage extremely diverse goods in various unit loads and at two different temperatures, all in a single aisle. In addition, the control, management and traceability offered by Easy WMS are indispensable for ensuring the safety and quality of Cosmopak’s more than 2,500 SKUs.
Javier Fernández - Owner of Cosmopak
“We set out to automate all processes to guarantee that we would be able to keep up with our growth rate. We are extremely satisfied with the new warehouse because it has provided us with better stock control and traceability.”
Advantages for Cosmopak
- Connected warehouse: Cosmopak’s installation is automatically linked to the production lines. Easy WMS arranges the shipment of the necessary raw materials, while handling equipment carries out those movements automatically.
- Organization equals efficiency: in a single aisle, the 3,800 pallets are arranged according to their unit load, the temperature at which they should be kept (cold or ambient), and whether they are raw materials, semi-finished goods, or finished products.
- Full traceability: Easy WMS knows the exact location of the 2,500 available SKUs and tracks all IBC movements.
Cosmopak warehouse | |
---|---|
Storage capacity: | 3,800 pallets |
Pallet sizes: | 32"/39" x 47" |
Max. pallet weight: | 1.32 t |
Warehouse height: | 50' |
Warehouse length: | 486' |
Gallery

Cosmopak's automated installation in Portugal for cosmetic products
Ask an expert