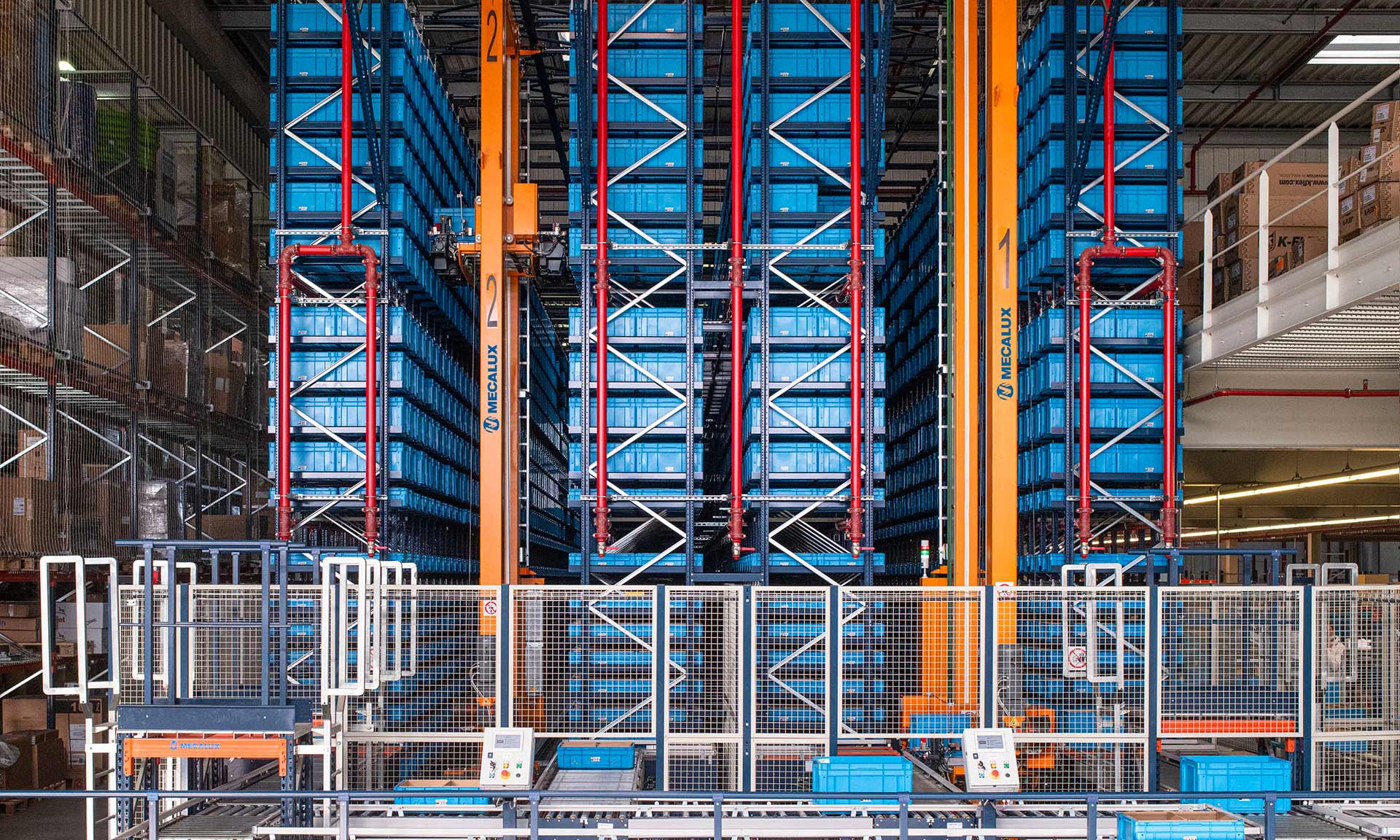
COVAP: automation to prepare 3,000 order lines a day
The automated warehouses for boxes can store 10,000 SKUs in merely 4,000 ft2
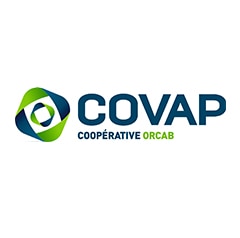
Cooperative COVAP has reorganized the layout of its logistics center in La Chaize-Le-Vicomte, France, with the start-up of an automated installation for boxes supervised by Interlake Mecalux’s Easy WMS warehouse management system. This automated structure, which can store 10,000 SKUs in merely 4,000 ft², has enabled COVAP to absorb its 40% increase in business by optimizing its available resources. Picking is this logistics center's main operation: with the combination of pallet racks, cantilever racking and the automated installation for boxes, the firm can prepare 70% more orders with the same number of employees.
Tradition and modernity
Founded in 1982, COVAP is a French cooperative comprising more than 450 tradespersons (electricians, plumbers and appliance repair persons, among others). In order for these professionals to provide efficient service to their customers, the company supplies them with the materials they require.
COVAP has a catalog made up of 300,000 SKUs of materials used in all kinds of construction and repair work. Therefore, it needed a logistics solution with certain characteristics: on the one hand, a high storage capacity to manage a wide variety of products, and, on the other, a system that would facilitate order prep and dispatch tasks in the shortest time possible.
A few years ago, COVAP equipped its warehouse in La Chaize-Le-Vicomte (France) with cantilever and pallet racking, two ideal systems for storing products of different sizes and shapes. Thus, these racks held mainly bulky goods. “Meanwhile, we put smaller products on the picking shelves with raised walkways, where there were around 10,000 slots in approximately 24,000 ft². We followed the person-to-product principle to prepare orders,” explains Wilfried Ferré, Logistics Manager at COVAP.
The cooperatives membership and the types of services these workers had to provide to customers all over France rose. Consequently, so did its warehouse activity, especially in relation to the supply of materials.
Against this backdrop, Wilfried Ferré acknowledges, “We needed more labor to take on the increased volume of work in the installation. So we were forced to optimize all our available resources and to improve operations.” It was then that COVAP felt compelled to automate its systems to boost its efficiency: it replaced its picking shelves with a modern automated warehouse for boxes.
This new installation ensures continuous, safe goods movements with minimal intervention from workers. In addition, it solves the lack of staff for performing storage and order prep tasks and eliminates possible errors stemming from manual management.
The COVAP Logistics Manager contends, “We sought the collaboration of Mecalux because of its long history and extensive experience in developing automatic storage solutions. Visiting other warehouses with operations like ours, such as the installations of Grégoire-Besson and SCD Luisina, convinced us to choose Mecalux.” After all, the automated warehouse for boxes had to be started up without stopping the activity of
COVAP’s logistics center at any time.
“One of our priorities with this project was to drastically reduce the percentage of errors,” notes Wilfried Ferré. The automated installation for boxes was the perfect solution for obtaining more productivity and accurate goods control. All movements are orchestrated by the Easy WMS warehouse management system.
“We thought Mecalux’s proposal was highly competitive because it was specifically designed to speed up picking,” says COVAP’s Logistics Manager. The automated warehouse for boxes makes it possible to prepare 60 orders simultaneously according to the product-to-person method.
The pallet racks, located in two areas of the center, were maintained; their versatility and adaptability make them the ideal complement to the automated installation for boxes, much like the cantilever racking.
Standing 28' high, the pallet racks can house over 10,000 SKUs in 8,500 pallets. They offer direct access to the products, streamlining goods management and facilitating stock control (each location is assigned to a single SKU).
By combining three storage systems in a single space, COVAP organizes its goods based on their characteristics and turnover. Every day, the center receives 300 boxes containing COVAP’s smallest products, which are deposited in the automated warehouse for boxes. Meanwhile, approximately 200 pallets with larger items (boilers, for example) are stored directly on the pallet racking. COVAP’s bulkier products, especially in terms of length, are deposited on the cantilever racks.
Technical features of the automated warehouse for boxes
One of the particular characteristics of this storage system is saved space, as it leverages the height and 4,000 ft² of available surface area to place a large number of boxes in a limited space. With a capacity of 10,000 SKUs in 13,224 boxes, the automated installation comprises two 141-foot-long, 26-foot-high aisles with double-deep racking on both sides.
The racks’ 19 storage levels have been personalized to accommodate boxes of two different heights: 7" and 12". The first nine levels store the less bulky boxes, while the other 10 hold the taller ones. The boxes are perforated on both sides in compliance with fire safety regulations.
A twin-mast stacker crane travels down each aisle and can handle up to four boxes simultaneously, each weighing 110 lb, quadrupling movement flows. Together, the two stacker cranes guarantee up to 264 combined cycles per hour, a pace high enough to meet COVAP’s logistics needs. In other words, a total of 528 incoming and outgoing container movements are carried out every hour.
All goods arriving at the warehouse must go through a checkpoint to verify that their weight and sizes meet the established criteria for placement in the warehouse.
Wilfried Ferré enthuses, “The automated installation has enabled us, among other advantages, to minimize the number of errors made in both management and picking and to absorb the 40% growth in our business activity.”
Preparation of 3,000 order lines a day
On one side of the automated warehouse for boxes, two pick stations with carton flow racking have been set up. Here, workers prepare orders ergonomically and in line with the product-to-person principle.
This has meant a huge change for COVAP’s logistics systems. Before, operators spent half their working day walking around the installation to locate the SKUs that made up the orders. Now, conversely, the goods are brought to them automatically via conveyors, raising throughput in order prep. At present, close to 70% more orders can be prepared with the same staff.
Each pick station is equipped with a computer connected to Easy WMS and with carton flow storage where the products are placed into cardboard boxes (each one comprises an order). In total, up to 30 orders can be prepared. To help employees minimize errors and enhance efficiency in picking, each location is equipped with a put-to-light device that lights up and displays the number of items required.
Finished orders are placed on a pallet that is subsequently sent to the shipping and consolidation zone. There, using radiofrequency terminals, the operators verify that no mistakes have been made during order prep. Additionally, some of these orders are completed with items from other areas in COVAP’s warehouse. The packages are finally moved to the loading docks, where they wait to be placed on the delivery truck.
Automation and optimal organization of logistics processes have enabled much faster and more effective order prep. The solution was designed as part of the growth strategy COVAP plans on implementing over the next five years.
Easy WMS: at the helm of automation
Tasks in the automated installation for boxes are overseen by Easy WMS, Interlake Mecalux’s warehouse management system. To optimize all activities, this software communicates and exchanges data in real time with COVAP’s WMS.
Easy WMS rigorously monitors the goods from the moment they go through the checkpoint until they are sent to the pick stations. To ramp up efficiency, it assigns a location to each item based on product type and demand level.
Demand for COVAP’s merchandise is seasonal. The data analysis performed by Interlake Mecalux confirmed that the number of orders soars between October and December, with peaks at the beginning of the week, especially between 2:00 p.m. and 9:00 p.m.
To ensure effective operations in these circumstances — regardless of workload — Easy WMS logically organizes the goods to streamline order prep and dispatch. At the same time, by sending operators instructions on their tasks, they can carry them out more quickly. Lastly, the put-to-light devices on the carton flow shelves help to prevent any possible mistakes.
Innovation and automation
Automation has given COVAP a host of advantages, primarily increased productivity and availability, as it can run from 6:00 a.m. to 10:00 p.m. at maximum throughput. Moreover, the implementation of Easy WMS has a dual role: to update the inventory in real time and guide workers in picking.
With the automated warehouse for boxes, this cooperative has made much better use of the space of its logistics center to house a greater number of products. It has also sped up picking while employing the same resources as before.
Having a large, flexible installation was fundamental for COVAP: it not only holds a substantial amount of products of varying sizes and turnovers, but also successfully manages the daily preparation of a considerable number of orders.
With the new automated warehouse for boxes, we’ve cut down on errors, and our goods inflow and outflow processes are faster and safer. I should emphasize that the efficiency in picking has allowed us to meet the 40% surge in our business activity. With such an advanced logistics system, we’re very optimistic about further developing our cooperative and expanding geographically, appealing to new professionals.
Advantages for COVAP
- Surface area optimization: in just 4,000 ft², COVAP has a fully automated solution for 13,224 boxes, each weighing up to 110 lb.
- High, error-free productivity: the combination of three storage systems makes it possible to prepare and dispatch 3,000 order lines a day without error and as quickly as possible.
- More orders with the same resources: the automated warehouse for boxes and other logistics solutions facilitate the preparation of 70% more orders using the same staff.
Automated warehouse for boxes | |
---|---|
Storage capacity: | 13,224 boxes |
Box size: | 16" x 24" |
Max. box weight: | 110 lb |
Racking height: | 26' |
Racking length: | 141' |
Gallery
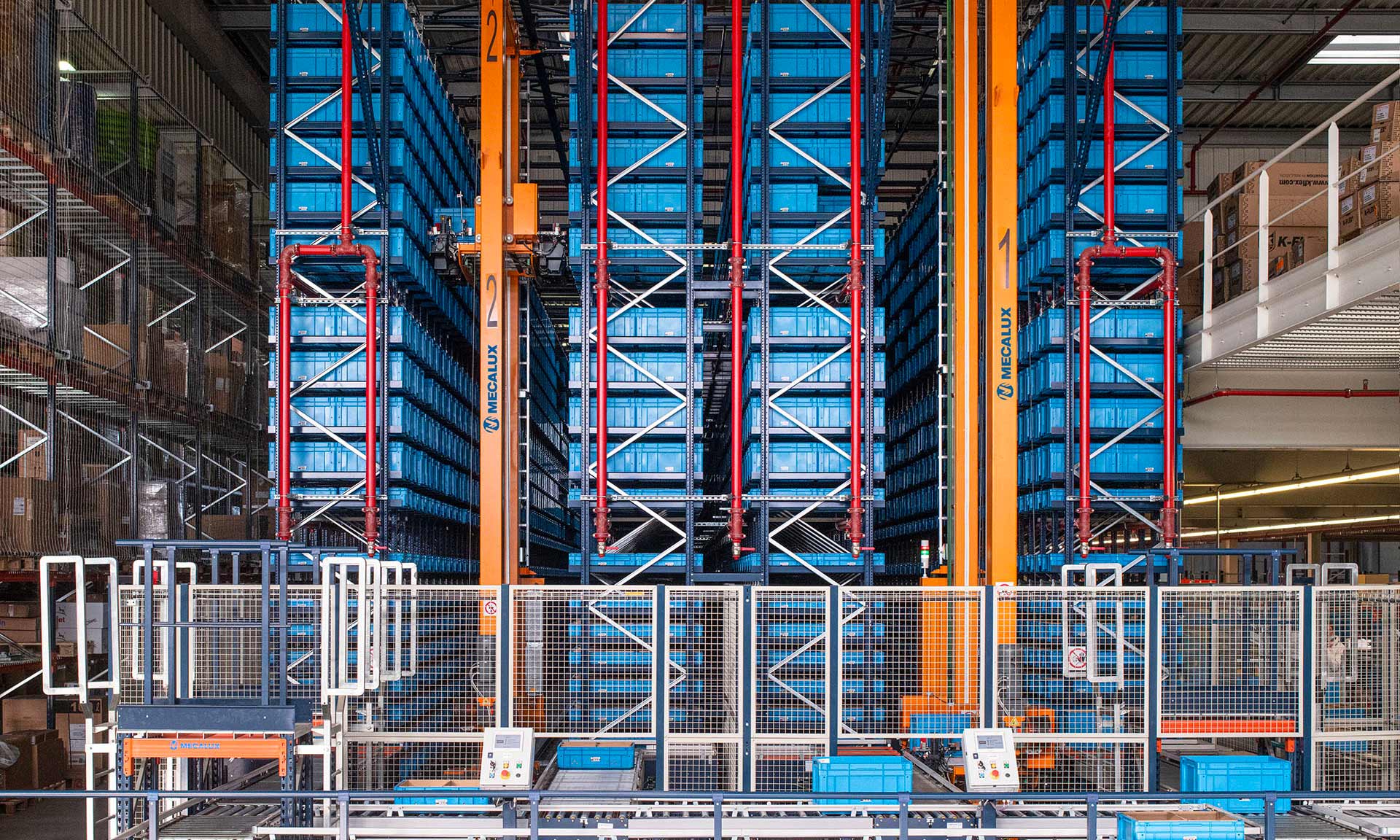
Automated installation for boxes at COVAP's centre in France
Ask an expert