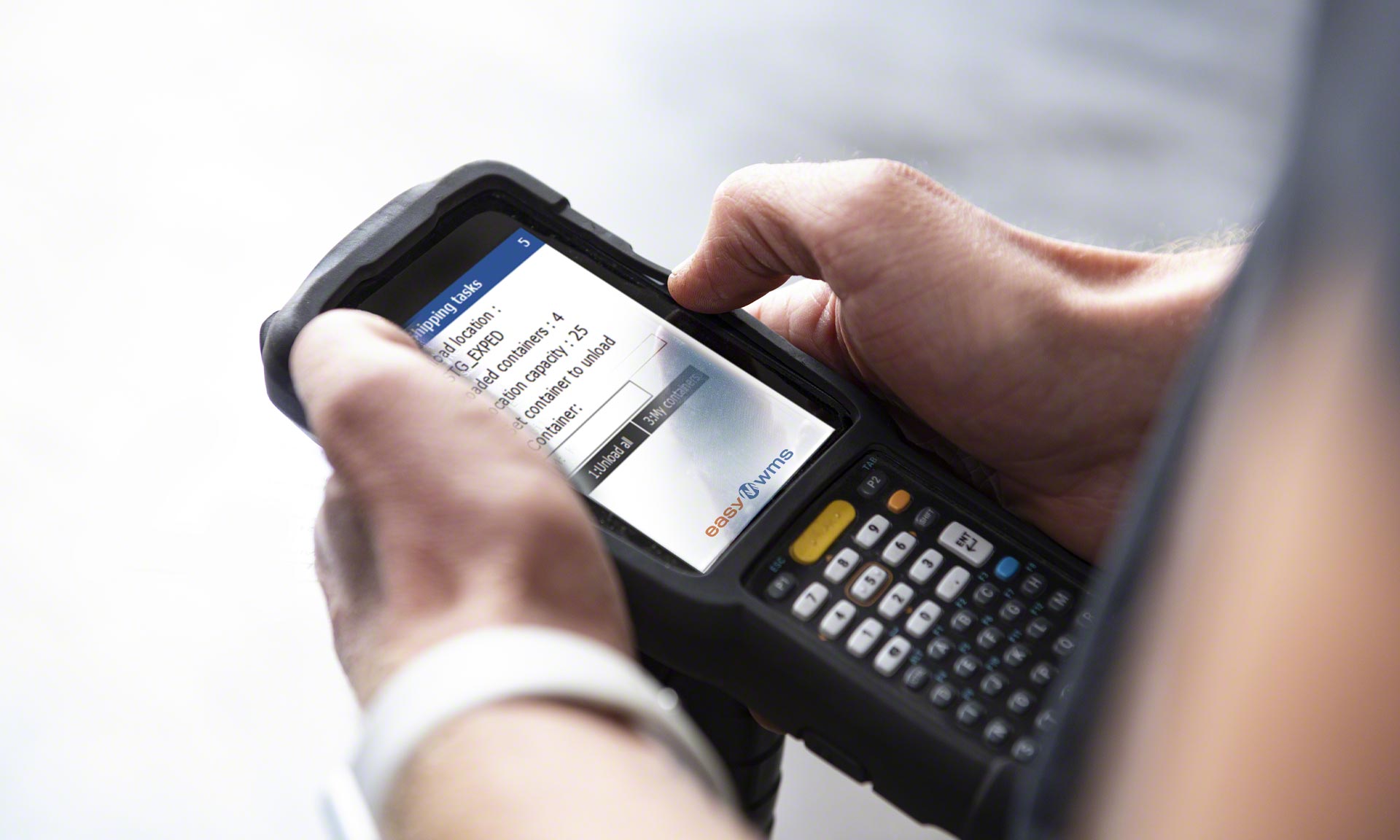
Logistics digitally integrated with production
Dexel cuts manufacturing times with efficient logistics operations managed by Mecalux software
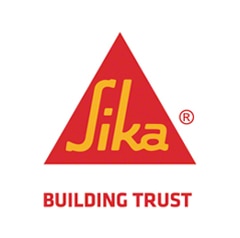
Dexel has implemented Easy WMS management software from Mecalux in its two warehouses in France, in addition to the WMS for Manufacturing module. Through technology, the company can ensure that its production lines are efficiently supplied with the necessary raw materials.
Dexel: construction and industry
Dexel is a subsidiary of Sika France, a leading chemical company in the development and manufacture of adhesive, sealing, and soundproofing products for the construction and industrial sectors. Since it was acquired by Sika France in 2004, Dexel has become the group’s innovation and experimentation laboratory, manufacturing products for major do-it-yourself (DIY) retailers under the Sika brand.
- Headquarters: Salles-du-Gardon (France)
- Founded in: 1999
- Annual turnover: $6.8 million
- No. of employees: 20
- International presence: 100 countries
CHALLENGES
|
SOLUTIONS
|
BENEFITS
|
---|
Logistics and production are two processes that go hand in hand. For Dexel, the supply chain plays a key role: it reduces the time taken to manufacture the goods (lead time), ensuring that the production lines have all the materials they need to make the products as soon as possible.
How has Dexel managed to ensure such seamless communication between its warehouses and production lines? With the help of the Easy WMS warehouse management system from Mecalux, which has provided it with visibility of stock in real time and full traceability of all its products, from raw materials to finished goods.
The company has two warehouses in Salles-du-Gardon, France. The one used to store raw materials consists of a 32,292 ft² automated storage and retrieval system (AS/RS) located in the same building as the production lines. The other is a 2.47-acre facility allocated to finished products belonging to Dexel and Sika France. According to Nathalie Burgals, Finance Manager at Dexel, “100% of production is delivered to Sika France.”
Before implementing the solution from Mecalux, the company managed the goods in both warehouses with the help of its Sage ERP (enterprise resource planning) system. This program was designed to run the most basic day-to-day operations in the facilities. For example, it could monitor the goods received and dispatched and organize the preparation of a limited number of orders. “As the number of items began to grow, we started to find it difficult to control the stock,” says Burgals.
Dexel set out to modify its logistics processes with a single objective in mind: to strictly monitor production. The business wanted not only to streamline the delivery of raw materials to production, but also to know all the processes through which each item had gone. Traceability was an essential requirement for this sealing products manufacturer. “We decided to implement warehouse management software. Mecalux’s technical team perfectly understood our needs and proposed a software program adapted to our way of working,” says Burgals.
The company deployed Easy WMS, the warehouse management system from Mecalux, in its facilities in France. Mecalux also installed the WMS for Manufacturing module, an extension of Easy WMS specifically designed to ensure that the production lines are efficiently supplied with the raw materials they require.
Faster, smoother logistics
The implementation of Easy WMS has completely transformed Dexel’s supply chain. In addition to digitally connecting the company’s two warehouses with the production lines and ensuring full product traceability, the management software has optimized the other operations.
Meanwhile, warehouse operators noticed significant improvement when carrying out any task, from product storage to production line supply. Burgals says: “We’ve equipped each operator with an RF scanner so that they can follow instructions from Easy WMS. These instructions make the operators’ work easier in addition to speeding up tasks.”
Via the RF scanners, operators receive clear instructions from the management software on how to complete their tasks in short order: the program designates the products that have to be moved to the production lines and shows the operators which aisles they will find these items in. Furthermore, the system generates pick paths that ensure that the operators trave the shortest possible distances.
Computers have also been installed at different points in the two warehouses so that Dexel’s logistics managers can consult the status of the processes. Easy WMS provides information in real time on the number of available items and on products to be sent to the production lines, among other data.
Efficient organization
Every day, a large number of movements take place in both Dexel facilities: they receive raw materials, semi-finished goods, and finished products. Simultaneously, merchandise is sent from them to the production lines and to customers.
Organizing all these flows might seem complicated, but Easy WMS does this automatically to prevent interference and mistakes. “Easy WMS has been adapted to the characteristics of our business. It uses different criteria to distribute the 600 SKUs in the facilities. The software assigns a location to each product taking into account its size, weight, characteristics, and type,” says Burgals.
By identifying all products the minute they arrive at the warehouse, Easy WMS knows the exact location of the goods in real time. Likewise, by sending the operators instructions, the software knows every movement each item makes as well as the processes it has gone through, ensuring total traceability. “We need to provide our customers with accurate information on the merchandise. Easy WMS knows all the quality controls the products have passed, their batch number, expiration date, and whether they have been stored following the FIFO (first in, first out) method,” says Burgals.
Connection with production
To digitally connect the warehouses with the production lines, Easy WMS has been integrated with Dexel’s manufacturing execution system (MES). This system is designed to organize, control, and monitor processes in the production center. Thanks to this connection between the Mecalux management software and the MES, the warehouse knows exactly when the production lines need raw materials to manufacture the goods.
The WMS for Manufacturing module has also been installed. This solution from Easy WMS controls the just-in-time supply of raw materials and records finished products as they leave the production lines. “Our priority is to have a complete record of our products, knowing detailed information on production and logistics processes that each of them has undergone,” says Burgals.
The MES sends the WMS for Manufacturing module the bill of materials (BOM), i.e., the complete list of the materials, packaging, and accessories needed to make the products. The BOM includes the components that make up the products as well as the quantities required. WMS for Manufacturing then arranges all these items to be sent from the warehouse to the production lines. As the production process goes on, the operators supply the necessary products to avoid any type of interruption in service.
The module also supervises a key operation for the production process: the weighing of the raw materials. The operators, following instructions on their RF scanners, are charged with validating the weight of the items to be sent to the production lines. “The supply of goods to the production lines must be flawless to ensure the proper production of the merchandise,” says Burgals.
Quality and good service
Dexel has completely overhauled its supply chain, relying on digitization to connect its two logistics facilities in France with its production lines.
The Easy WMS warehouse management system has increased logistics efficiency, thanks to seamless communication between all processes. The supervision of this system enables the company to have just-in-time logistics operations, sending the required goods to the production lines when the time is right. Easy WMS also organizes all the merchandise and operator tasks, increasing speed and eliminating any possibility of error. Digitization has made Dexel’s supply chain securer and more efficient.
With Easy WMS, we have more exact information on the goods and on production and logistics processes. Our inventory is much more accurate, and we’ve minimized the chance of making mistakes.
Dexel responds:Interview with Nathalie Burgals, Finance Manager at Dexel |
---|
Why did you decide to implement the Easy WMS warehouse management system from Mecalux? Our business has evolved considerably over the past few years. We used to manage goods and operations in both facilities with the Sage ERP system, but it wasn’t designed to orchestrate logistics processes. And this prevented us from controlling the traceability of our products. As the number of items began to grow, we started to have trouble controlling the stock. We decided to implement warehouse management software because we wanted to improve the distribution of the goods in the facilities, guarantee total traceability of the products, and automatically connect the warehouses with production. |
How important for your business was it to digitally connect the warehouses with production? It was very important. For our business to run smoothly, we believe it’s fundamental to strictly control all processes, from the production of new items to their subsequent storage. Our priority is for the warehouses to be connected to the production lines for two reasons: so that raw materials are received at the right time and so that products are stored as they leave the production lines. We’ve installed the WMS for Manufacturing module to gain visibility of stock in real time and total traceability of raw materials and finished products. The installation of this module has changed the way our operators work. With this system, they can check the supply of raw materials to the production lines and their consumption in production. The software also tells operators when they can pick up the final product. |
|
Could you describe the Easy WMS installation process in the two warehouses? First, we did a functional analysis in which the operations in both warehouses were studied in detail. Then, we appointed an internal project manager to help coordinate all the processes. We had to prepare a detailed list of all our items, specifying their characteristics. This way, by the time Easy WMS went live, we already had all the items entered into the database and only needed two weeks to fine-tune the operations. Mecalux’s technical team was by our side during the entire deployment period. |
Have the warehouse operators adapted well to Easy WMS? Yes, they work really well with the software. The operators participated very actively in the functional analysis, describing in detail their day-to-day work in the warehouse as well as their needs. Our mission was to find the best solution for optimizing our supply chain and to make the operators aware of the advantages of Easy WMS. The Mecalux technical team helped us a lot when installing the system: it was always available to answer our questions and adapt the system to our requirements. |
|
Is the company satisfied with Easy WMS? Yes, very much so, because we now have total traceability of our goods. In addition, we’ve minimized errors. Logically, operators can still make mistakes, but these can be detected and corrected more easily with Easy WMS. Another major advantage is that, thanks to this software, our inventory is much more accurate and consistent. The WMS is flexible and can be upgraded taking into account the needs of the warehouse. Our operators wonder how we ever worked without this software. They’ve adapted to Easy WMS so easily and in such a short time — there’s no turning back now! |
Ask an expert