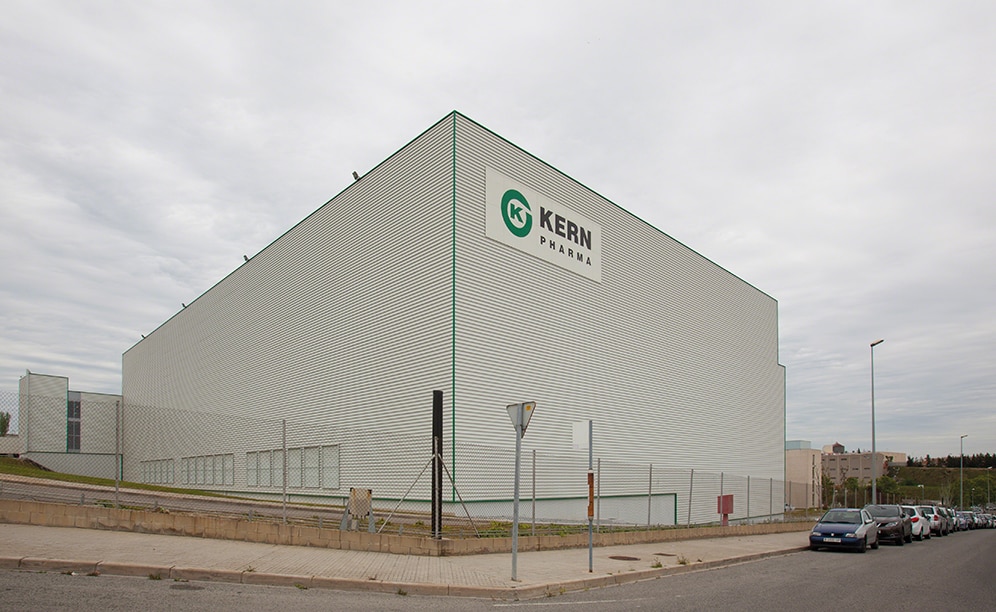
The pharmaceutical laboratory Kern Pharma builds a clad-rack warehouse that combines stacker cranes for boxes and for pallets
Kern Pharma expands its logistics centre with an automated clad-rack warehouse for boxes and pallets
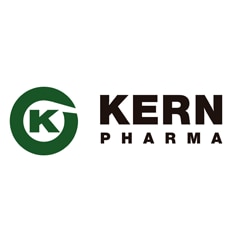
The new automated rack-supported warehouse of Kern Pharma in Terrassa (Barcelona) has a capacity of more than 10,000 pallets and 9,700 boxes. Warehouse operations are fully automated and ensure maximum agility of incoming and outgoing goods, as well as a higher productivity. With this investment, the company consolidates its expansion in Europe and is set up to strengthen its growth rate.
Health and wellness
Kern Pharma is a pharmaceutical laboratory that is part of Grupo Indukern.
Founded in 1999 in Barcelona, it has become a mainstay in the manufacture of generic, inpatient, and over-the-counter medications, as well as those for women's health.
The company wants to expand internationally, so it has established partnerships with distributors in virtually all countries within the European Union. Its business strategy emphasizes ongoing research and development of new solutions for patients, doctors and pharmacists in an ever shifting, innovation-driven market.
The needs of Kern Pharma
Kern Pharma has positioned itself as one of the leading hospital and pharmacy suppliers in Spain, with a production that exceeds 100 million units of medications yearly.
The company needed to expand its manufacturing center located in Barcelona to efficiently provision all its customers and, in turn, to be prepared to cope with forecasted growth rates.
In the same installation, different load units are deposited (pallets and boxes), with distinct turnovers and characteristics that require specific curation. For this reason, the pharmaceutical firm requested the collaboration of Interlake Mecalux to find the solution that would best solve its needs.
Interlake Mecalux's solution
Interlake Mecalux built a new, 21,528 ft² rack-supported warehouse measuring 85' high and 276' long. It consists of five aisles with single-depth racks on both sides with a deposit capacity of more than 10,000 pallets. Another aisle, attached to the existing warehouse, houses more than 9,700 boxes.
In each aisle, the stacker cranes are designed to locate and extract pallets and boxes from the racks. The movement of this equipment is managed by the Interlake Mecalux Galileo control program connected to the ERP and warehouse management system of Kern Pharma.
The rack-supported warehouse is an integral construction formed by the racks themselves on which the outer cladding is fixed. When calculating the structure, experts take into account its own weight, that of the stored goods and external forces such as the wind, snow, and thrust of the stacker cranes; even the degree of seismicity corresponding to each territory, as well as local regulations. The advantage of this type of facility is the height optimization to achieve massive storage capacity.
Miniload aisle installation
In the warehouse, an aisle was enabled and set aside to deposit the boxes of Kern Pharma products. Single-deep racks consist of 36 levels, reaching 66' in height.
The miniload installation provides functions that best meet the logistical requirements of the company. It has a twin-mast stacker crane that operates at a speed of 722 ft/min and 197 ft/min when raised, obtaining an optimum flow of incoming and outgoing goods in the warehouse.
The stacker crane incorporates a fork extraction system, the most widely used in the market. These forks are inserted through the bottom of the boxes, removing or placing them in locations on both sides of the aisle. The cradle has the capacity to handle two cases at once.
Pallet storage aisles
Currently, there are four, 236' long aisles in operation. The single-deep racks, on both sides, accommodate more than 8,000 pallets of 32"x 47" x 53”/71" with a maximum weight of 1.1 t.
Moving elements (conveyors and stacker cranes) are protected by metal enclosures and optical barriers that prevent access by unauthorized personnel.
In each aisle, the stacker cranes are responsible for transferring the pallets between input and output conveyors and their corresponding location on the racks in the same motion (called a combined cycle), which increases the productivity of the installation.
Warehouse inputs and outputs
The entry and exit of warehouse goods are carried out on two different levels to avoid interference between the two operations.
Receptions are on the same level as the manufacturing plant. Automatic Guided Vehicles (AGV) collect and deposit pallets on incoming warehouse conveyors.
AGVs are forklifts that emit a signal that bounces off laser deflectors placed at points along a route and thus determine its trajectory.
The management system knows its exact position and orders it to go to the charging stations when the battery level reaches a set limit. Being a fully automatic connection, human intervention is not needed in this process.
The dispatch area is located on the upper level, next to the loading docks, to expedite the distribution of the company's medications.
Operators, with the help of front loading forklifts, remove pallets from the outgoing conveyors. These are protected by specialized structures to prevent any damage or blow that could undermine the smooth running of the system.
Multiple software
The warehouse is equipped with different software that work concurrently to improve the throughput of all processes that take place inside it, including the receipt of goods, storage, dispatch and output of the products. The Galileo software's mission is to control the movement of unit loads within the warehouse.
It is in direct and permanent connection with the other programs running the installation, to optimize all logistics processes.
Advantages for Kern Pharma
- Greater capacity: with the expansion of the logistics center, the company has increased storage capacity to over 10,000, 1.1 t pallets and 9,700 boxes weighing a maximum of 66 lb each.
- Streamlined operations: the construction of an automated rack-supported warehouse meets the logistics requirements of Kern Pharma, applying a very straightforward and quick operational system with minimal personnel.
- Optimal oversight: the organization of goods and automated management ensure efficient service, increased warehouse productivity and savings in logistics costs.
AS/RS for Pallets of Kern Pharma in Spain | |
---|---|
Storage capacity: | 10,080 pallets |
Pallet sizes: | 32" x 48" x 53"/71" |
Max. pallet weight: | 1.1 t |
Racking height: | 85' |
Racking length: | 236' |
Levels high: | 14 |
No. of aisles: | 5 |
Gallery
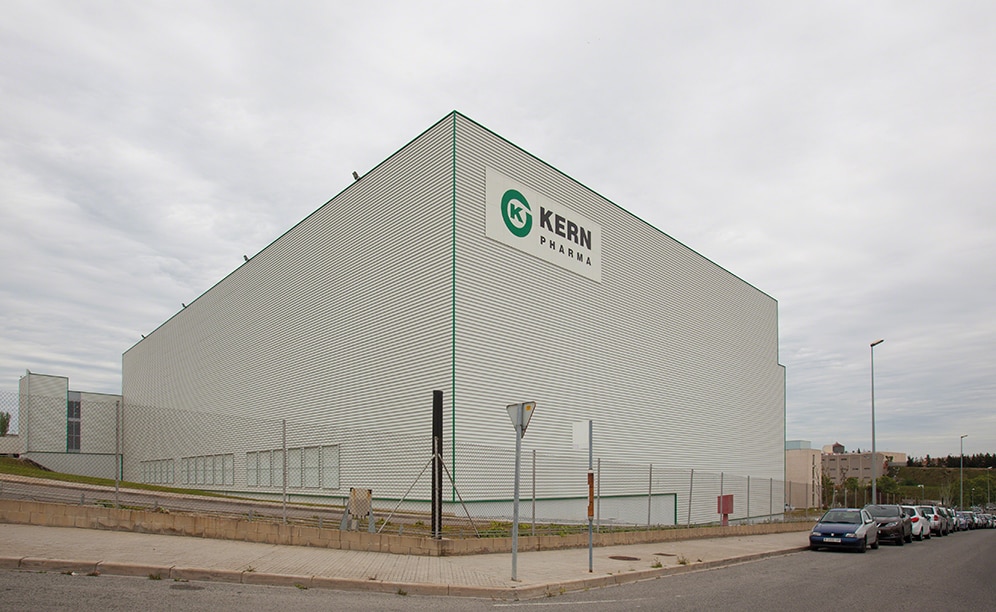
Mecalux built a new, 2,000 m² clad-rack warehouse measuring 26 m high and 84 m long
Ask an expert