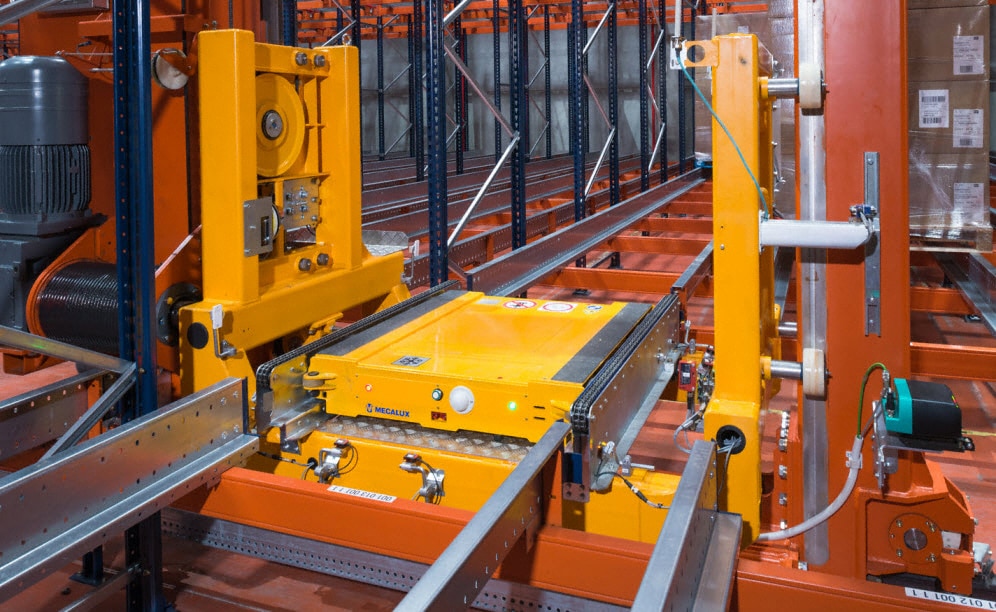
Maximum swiftness and the full use of space in the new automated warehouse with Pallet Shuttles at UNITED CAPS in Luxembourg
UNITED CAPS grows with the automatic high-density Pallet Shuttle system with stacker cranes
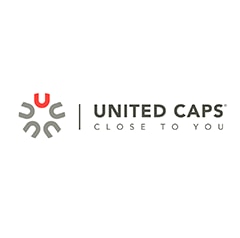
The company, specialized in the development and manufacture of caps and closures, has built a four-level high automated warehouse at its production plant in Wiltz (Luxembourg). The facility, with a capacity to store over 5,500 pallets, is served by two stacker cranes that each operate a Pallet Shuttle. Also integrated within the new set up is the Easy WMS warehouse management system by Mecalux, in charge of controlling all the center’s operations.
About UNITED CAPS
UNITED CAPS is a leader in the design and production of plastic caps and closures. Based in Luxembourg, this family business offers innovative solutions worldwide and has production facilities in France, Belgium, Germany, Hungary, Ireland, Luxembourg, and Spain.
The company, which achieved a turnover of 132 million US dollars in 2015 and employs more than 530 workers, has a product portfolio with more than 600 different caps and closures.
The solution: the automatic Pallet Shuttle
Given its relentless growth, UNITED CAPS needed a warehouse that would grant them the highest possible storage capacity without losing accessibility to the different SKUs and, at the same time, would allow a maximum, speedy flow of goods.
To do so, Mecalux designed and installed a high-density warehouse with the automatic Pallet Shuttle system with stacker cranes, as well as the implementation of management software.
Two stacker cranes are responsible for moving the load between the entrances/exits of the warehouse and the channels of the racks, offering agility and strict control of the goods, within this fully automated installation.
A transfer car is set up at the front of the warehouse, which is used to connect the conveyor circuit with the stacker cranes. When the operator deposits a pallet in one of the input stations of the conveyor circuit, the Easy Mecalux WMS reads the SKU it contains and takes on its internal control and management.
Parts of the UNITED CAPS warehouse:
- A high-density system with an automatic Pallet Shuttle
- Stacker cranes
- Transfer car
- Input conveyors
- Output conveyors
- Area with full pallet stacker and empty pallet stacker
The automatic Pallet Shuttle: how it operates
The Pallet Shuttle is housed in the cradle of the stacker crane in a position slightly below the pallet support level; this level consists of two motorized chains that pick up or leave pallets in the input or output stations.
Once the stacker crane has placed itself in front of the assigned location, the shuttle is raised with the pallet on it and inserted into the channel to transport the pallet to the free position furthest from the aisle and place it on the rails.
Each shuttle has eight wheels that provide the correct weight distribution of the pallet on the profiles and, at the same time, help the stacker crane to transfer items gently into the channels. The rails have centering elements on the side facing the aisle to facilitate the transfer of the shuttle.
Charging of the Pallet Shuttle’s battery is done in the very cradle of the stacker crane, directly and automatically. Supercapacitors are used for energy storage, and capable of charging in a matter of seconds.
Inside the warehouse: features
The 42’ high and 160’ wide warehouse consists of only two 159’ long storage aisles and 15 racking units to store two types of pallet: 39” x 47” x 98” and 31.5” x 47” x 100” with a maximum weight of 771 lb each.
A twin-mast stacker crane circulates in each aisle that carries a Pallet Shuttle in its cradle and is capable of moving at a travel speed of 394 ft/min and a lift speed of 125 ft/min.
Front of the warehouse: conveyor circuit and transfer car
In this area, the inputs and outputs of palletized goods are produced automatically via a conveyor circuit that directs the pallets from its origin to its destination. Thereby, the load units move swiftly, without any human intervention and reducing any logistics errors.
The operator only must place the palletized goods in the entry of the circuit or remove them at the exit with the help of a counterbalanced forklift.
The goods input area has a checkpoint whose role is to check that the dimensions, weight and status of the pallets meet the specifications of the installation.
The goods that do not pass inspection go to the rejects conveyor, which is placed exactly in parallel, for refurbishment. The conveyor circuit also incorporates a full pallet stacker, which can lift the pallets to place them on slave pallets, and a station where empty pallets are stacked and unstacked.
The conveyors for direct outputs, located in the area closest to the loading docks, include a closed sequencing circuit that places outgoing goods according to the required sequence.
Software: Easy WMS and Galileo
The UNITED CAPS warehouse is controlled by the Mecalux Easy WMS warehouse management system, responsible for organizing and coordinating the various operations that take place within the facility, from entries into the warehouse until the final dispatches.
Easy WMS controls the input and output processes, locations based on algorithms or parameterizable rules, the stock, the storage processes, the management of batches and all operations in the management of the warehouse.
In addition, the Mecalux Easy WMS warehouse management system is connected directly and at all times with Axapta (Microsoft Dynamics AX), the ERP application that the customer uses, exchanging information permanently and bidirectionally. Galileo is the control software of Mecalux. It is responsible for the logical execution of the movements of each machine, to carry goods from one point to another in the warehouse.
Advantages for UNITED CAPS
- Expanded storage capacity: the UNITED CAPS warehouse can accommodate 5,507 pallets in a surface area of approximately 25,618 ft2.
- Maximum throughput: the installation is fully automated with a conveyor circuit, a transfer car and the Pallet Shuttle system with stacker cranes.
- Profitable management: thanks to the Mecalux Easy WMS warehouse management system, UNITED CAPS can efficiently manage all movements, processes and operations taking place in its warehouse.
Automated warehouse with Pallet Shuttle, Luxembourg | |
---|---|
Storage capacity: | 5,507 pallet |
Max. pallet weight: | 772 lb |
Warehouse height: | 42’ |
Racking length: | 159’ |
No. of stacker cranes: | 2 |
Type of stacker crane: | twin-mast |
No. of Pallet Shuttles: | 2 |
Gallery
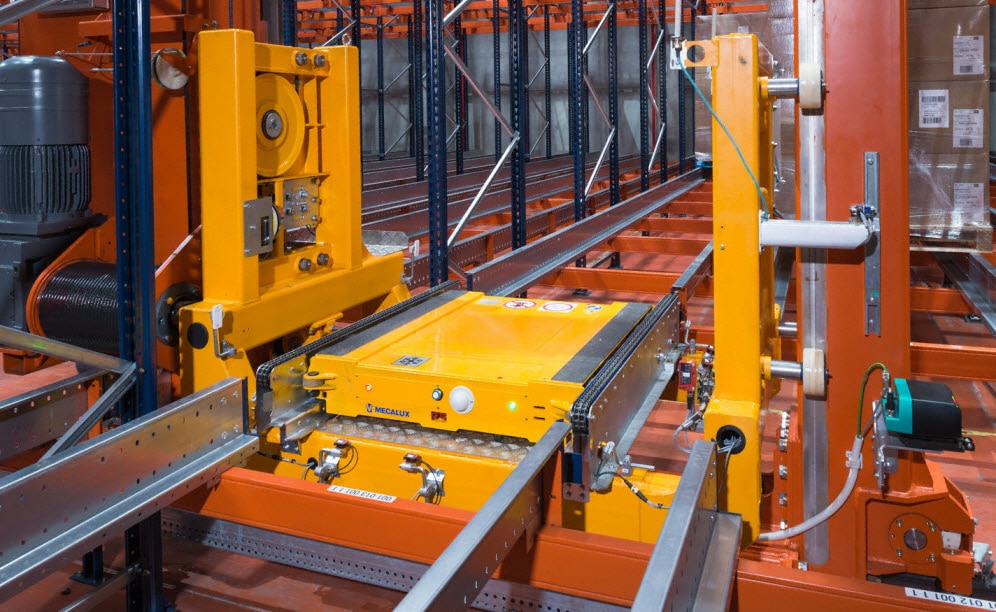
Mecalux designed and installed a high-density warehouse with the automatic Pallet Shuttle system with stacker cranes
Ask an expert