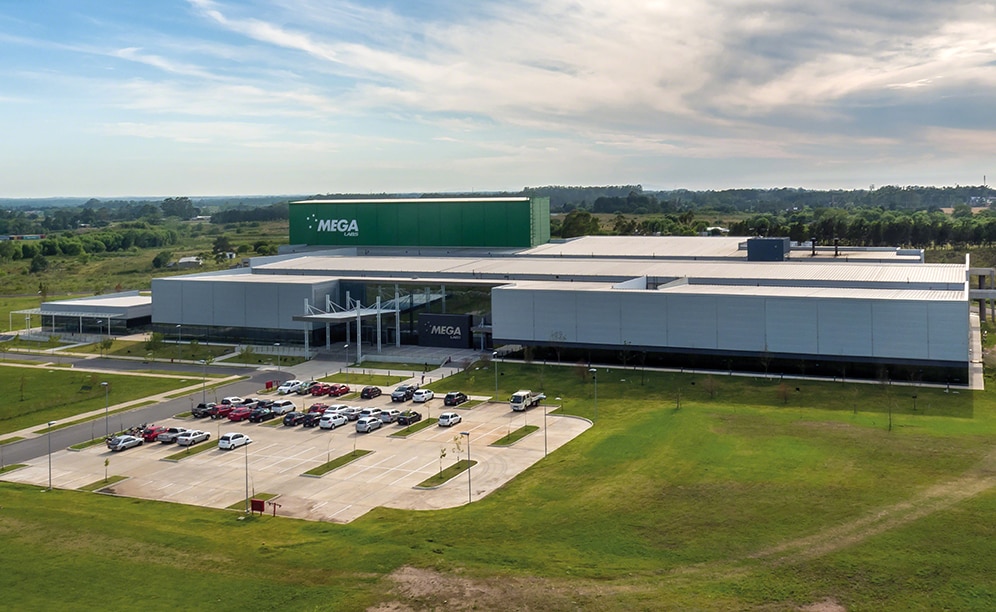
The pharmaceutical company Mega Pharma is on the technological forefront with a fully-automated clad-rack warehouse
Mega Pharma builds an automated clad-rack warehouse in Uruguay managed by the Easy WMS
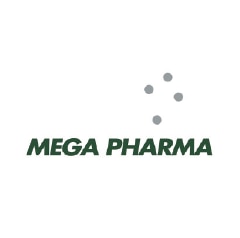
Mecalux has built Mega Pharma a new automated clad-rack warehouse in Uruguay with a capacity of over 6,900 pallets. It consists of two double-depth storage aisles and a conveyor circuit for inflowing and outflowing goods. The entire operation is controlled and managed by the Mecalux Easy WMS warehouse management software.
Research and innovation
Mega Pharma is one of the leading pharmaceutical companies in Uruguay, with their medications being sold in more than 20 countries in Latin America. It is an enterprise committed to healthy living, whose research and innovation-based strategy focuses on developing new medicines, incorporating the latest technology in its production processes and using high-quality raw materials.
The company recently opened Mega Labs, its largest manufacturing plant, located in the Parque de las Ciencias Free Zone (Uruguay). With a total expansion of 5.44 acres, the center is considered one of the most state-of-the-art in Latin America. Also, it is set up to grow, taking into account current and future needs of the business.
Needs and the solution
The aim of this production center is to strengthen the Mega Pharma's lead in Latin America, while enhancing the forecasted growth rate in the coming years.
The company needed a warehouse to house raw materials and to package medications. This installation had to have enough storage capacity to cope with increased production, whose operations have been fully-automated to ensure the maximum safety of goods and achieve high throughput. Mega Pharma requested the collaboration of Mecalux to make this project a reality. The result is a 9,300 ft² automated clad-rack warehouse, which more than meets the company's expectations.
Features of the clad-rack warehouse
Clad-rack warehouses are buildings formed by racks that must support their own weight, the stored commodity, the lateral and roof cladding attached to the structure, as well as the forces transmitted by the stacker cranes.
In addition, when designing this type of storage, one should take into account certain factors that have an impact on the structure, such as the force of the wind, the seismicity corresponding to the area in question and the local standards in force. The clad-rack warehouse's design optimizes the surface and height available, so that only the space strictly necessary is taken up.
Warehouse inputs
The receipt of the goods is automatically carried out in the P&D area of the warehouse. A entire roller conveyor circuit is enabled, continuously directing the pallets. It incorporates the following elements:
- Input conveyors
- Checkpoints
- Rejects conveyor
- Sampling stations and product quality control
- Empty pallet stacker
- Warehouse access door
The goods that arrive from production are inserted onto an incoming conveyor. The checkpoint verifies that the pallets are in perfect order and meet the requirements in terms of weight, condition and size, before being introduced into the warehouse.
If the pallet is in good condition, it continues its journey to the entry point of the automated warehouse. Meanwhile, the pallets that do not pass inspection move on to the rejects conveyor, placed in parallel, to be reconditioned.
Pallets with raw materials, from outside the manufacturing plant, must pass quality control. Four input conveyors have been installed which direct the goods to three detached cabins where operators evaluate the characteristics of the products. Subsequently, the pallets also go through a checkpoint to validate their insertion into the warehouse.
Automated warehouse
The Mega Pharma automated warehouse is 236’ long, 39’ wide and 79’ high, and kept at a controlled temperature.
It is composed of two aisles with double-deep racking on both sides. In each aisle a stacker crane circulates, operating at a speed of 525 ft/min and 125 ft/min when raised. These machines are responsible for moving the goods between the corresponding locations on the racks and the input and output conveyors located at one end of the aisle.
Warehouse outputs
Pallets leaving the warehouse can proceed to two destinations: either the direct exit point (when the merchandise is required in the production center) or dispatch, through a live accumulation channel. In the latter, the pallets are on-hold awaiting transfer to the loading docks, located on the opposite side of receptions.
Empty pallets are gathered at the warehouse exit point, which are then stacked in the entrance area, where a pallet stacker is installed. The aim is to have pallets for incoming load units that do not meet manufacturing specifications and have inadequate storage bases. In this situation, they are placed on top of a pallet to ensure the load's durability and stability in the circuit and inside the warehouse.
Easy WMS by Mecalux
The Mega Pharma warehouse is equipped with a robust warehouse management system the Easy WMS by Mecalux, whose task is to monitor and streamline all internal processes carried out.
The WMS is the brain of the system since it directs operations, among which include:
- Managing incoming goods, either from manufacturing or outside sources.
- Assigning pallet locations using rules and algorithms, depending on the consumer criteria and product turnover.
- Organisation and management of stock.
- Control of the warehouse exit points, grouping the output commands based on its destination.
Easy WMS by Mecalux is in constant two-way communication with the SAP ERP at Mega Pharma, transferring the data and information needed to optimize all processes.
Advantages for Mega Pharma
- Massive capacity: the new Mega Pharma clad-rack warehouse has the ability to store over 6,900 pallets in a 9,300 ft² area, besides being set up for future expansion.
- Maximum throughput: the installation is fully automated with a complete conveyor circuit, a transfer car and two stacker cranes that circulate in each of the aisles.
- More efficient management: the implementation of the Mecalux Easy WMS and the Galileo module represent logistics cost-savings, improved service quality and maximization of warehouse productivity.
The Mega Pharma automated clad-rack warehouse | |
---|---|
Storage capacity: | 6,960 pallets |
Max. pallet weight: | 1,323 lbs |
No. of stacker cranes: | 2 |
Fork type: | double depth |
Warehouse height: | 79’ |
Warehouse type: | clad-rack system |
Gallery
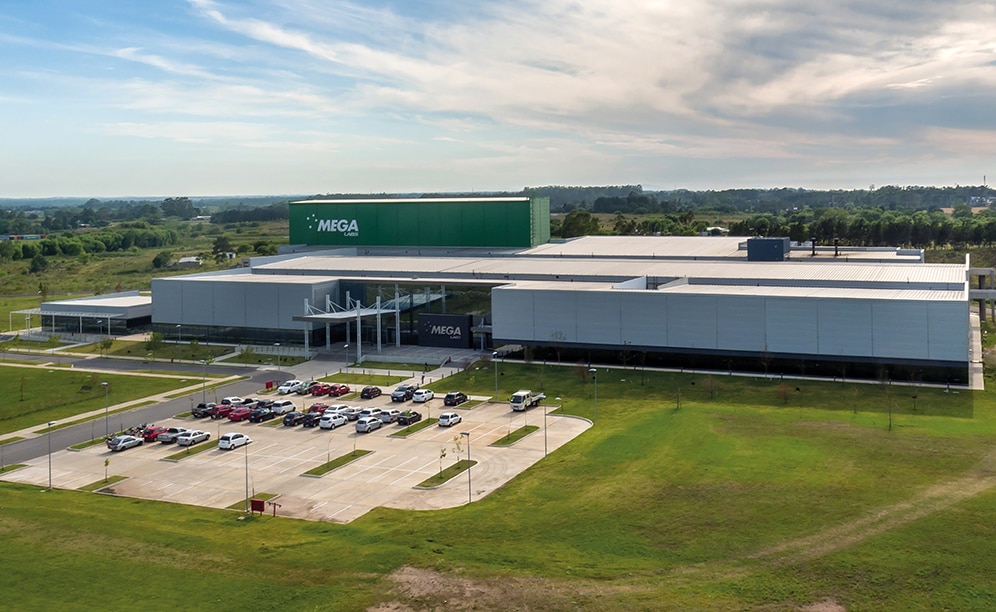
Mecalux has built Mega Pharma a new automated clad-rack warehouse in Uruguay with a capacity of over 6,900 pallets
Ask an expert