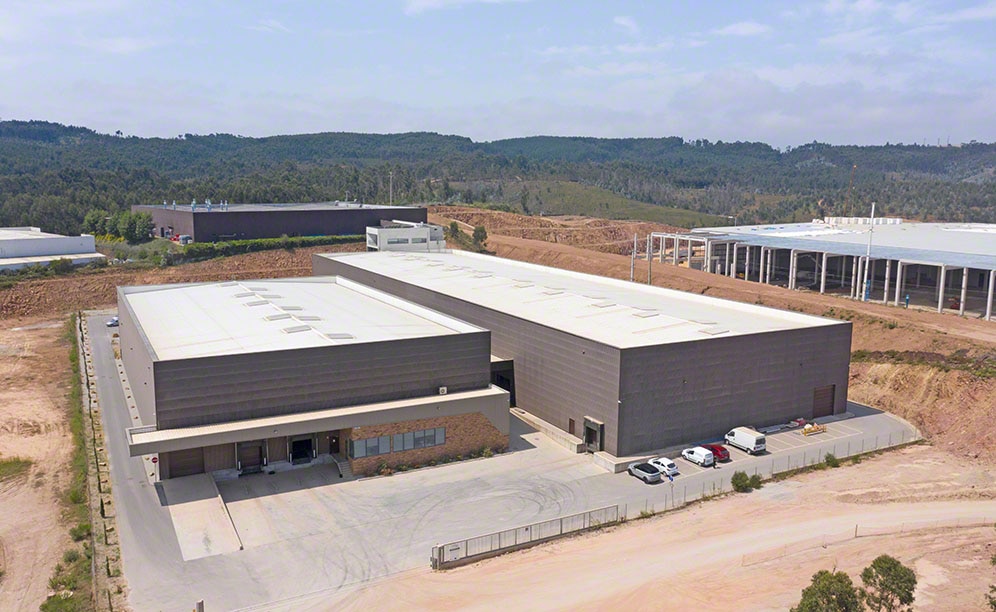
Automated management of 1.5 million paper bags a day
The automatic Pallet Shuttle with stacker crane in Finieco's warehouse for paper bags in Portugal
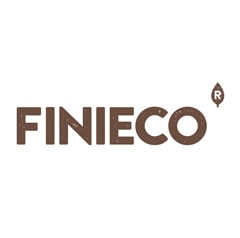
Finieco has revamped its logistics systems with the start-up of a new warehouse in Santo Tirso, Portugal. It is connected directly with the production area, where 1.5 million paper bags are made every day. Mecalux has equipped the facility with the automatic Pallet Shuttle system served by a stacker crane. This solution maximizes space, speeds up goods movements, and provides storage capacity for almost 5,000 pallets. Mecalux’s Easy WMS warehouse management system supervises all operations, providing greater stock control and ensuring fast, error-free order preparation.
Finieco’s new project
Headquartered in the Portuguese city of Santo Tirso, Finieco is one of Europe’s largest paper bag manufacturers. It has been in business since 1998 and is present in Germany, Spain, France, the UK, and Switzerland, among other countries.
The bags serve not only to move, store, and handle products, but also to set apart the brands that use them. Over the past few years, the pace of work at Finieco has steadily increased. Currently, it manufactures more than 1.5 million paper bags a day.
To meet this rise in demand and, thus, production, the company needed to boost its storage capacity and improve inventory control. Since its installation for finished products could not store all the goods, Finieco decided to expand its storage capacity, automate operations and update all its processes to make them more efficient.
Warehouse features
Finieco is a company that relies on automation and technological advances. Its objective was to maintain its competitiveness and guarantee the utmost quality and sustainability of its products and services. As Finieco boasts 16 fully automated production lines for paper bags, it was clear to the firm that its new installation needed to have automated operations and management.
On this basis, Mecalux proposed equipping the warehouse with the automatic Pallet Shuttle system served by a stacker crane. This solution leverages all the available space to provide greater storage capacity in addition to speeding up workflows.
The result is an installation comprised of two high-density racking units measuring 33' high and separated by a single, 148-foot-long aisle in which a stacker crane operates. One of the units is five pallets deep and the other, 33. In total, they provide storage for 4,990 pallets with a maximum unit weight of 1,323 lb.
The stacker crane picks up the pallets and brings them to the corresponding storage channel. An electric shuttle then moves them to the deepest available location in the channel.
One of the advantages of automating the installation is the high accessibility this offers. The company is now well prepared to deal with high peaks in demand. The conveyors and stacker crane can establish continuous goods flows and operate 365 days a year if necessary. Normally, however, Finieco’s warehouse runs 16 hours a day, divided into two work shifts.
For this installation to function properly, the following elements are essential: conveyors, a stacker crane, an electric shuttle, and a warehouse management system (WMS). This last component is charged with assigning the goods a location according to their characteristics and demand level.
Furthermore, in the warehouse design phase, future expansion was taken into account. The facility’s capacity can be increased if the company’s growth prospects require this. When the time comes, a second stacker crane will be added, duplicating the number of movements. This expansion will be carried out without interrupting the installation’s daily activity.
Another aspect that has helped to cut costs is the connection of the storage area with production via a conveyor circuit. Automating this process streamlines the movement of 240 pallets a day arriving at the warehouse from the production center.
Goods distribution
The installation has a vast and complete dispatch area where the pallets to be distributed every day are prepared (and subsequently divided between 10-12 trucks). To optimize the trucks’ load volume, a pallet placing device that stacks one pallet on top of the other has been set up.
A transfer car has also been installed. This sorts the pallets into 11 flow preload channels based on whether they correspond to the same order or transportation route.
The flow channels are slightly inclined so that pallets flow via gravity from the highest to the lowest point (which faces the docks). At the exit point, the rollers are split so that operators can remove the pallets by means of pallet trucks.
Easy WMS: a key role
Previously, the company produced on demand, leaving some reserve stock in an auxiliary warehouse. There, an operator would make a note of the products received on a piece of paper and later enter them in the ERP. By renovating its logistics systems, Finieco set out to improve this process and eliminate any risk of error.
It is now equipped with Easy WMS, the nerve center that manages all warehouse processes and contributes towards obtaining better results and stepping up productivity.
To achieve this, the software carries out extremely strict control of the products from the moment they arrive at the installation. Easy WMS assigns the goods a location based on their turnover (A, B or C): products with the highest turnover are deposited at the ends of the aisles to expedite their entry and exit and, at the same time, optimize the stacker crane’s movements.
The WMS knows the inventory status and location of each item at all times. This way, the company can know whether it has enough goods to prepare pending orders.
Easy WMS plays a central role in dispatches, as it orders pallets to be sent to the flow preload channels and subsequently sorted by order or route. To know which products customers have requested, Easy WMS has been integrated with Finieco’s ERP. This system notifies the WMS 12 to 24 hours in advance of the goods that need to be dispatched. Consequently, exit orders can be left prepared to save time.
Finieco’s smart warehouse
The Pallet Shuttle is a high-density system designed to store products with a large number of pallets per SKU. It is particularly suitable for installations with high goods flow movements, as is the case with Finieco. The version deployed in the company’s warehouse is fully automated, as it includes a stacker crane that transports the goods between the warehouse entry and exit points and the storage channels.
The motorized shuttle quickly carries out the goods movements in the storage channels, transferring pallets to the first free location. Likewise, the implementation of Easy WMS is vital for exploiting the facility’s possibilities, controlling stock, and ensuring the timely delivery of orders to customers.
Advantages for Finieco
- Control of operations: Mecalux’s Easy WMS knows the status of all the products, from the time they arrive at the installation through to their delivery to the customers.
- Future prospects: the warehouse will be expanded at Finieco’s request, without interrupting operations.
- Maximum use of surface area: the installation optimizes all the available space, attaining a storage capacity of 4,990 pallets in just 18,300 ft2.
Finieco’s smart warehouse | |
---|---|
Storage capacity: | 4,990 pallets |
Pallet sizes: | 32" / 39" x 47" |
Max. pallet weight: | 1,323 lb |
Racking height: | 33' |
Racking length: | 148' |
Gallery
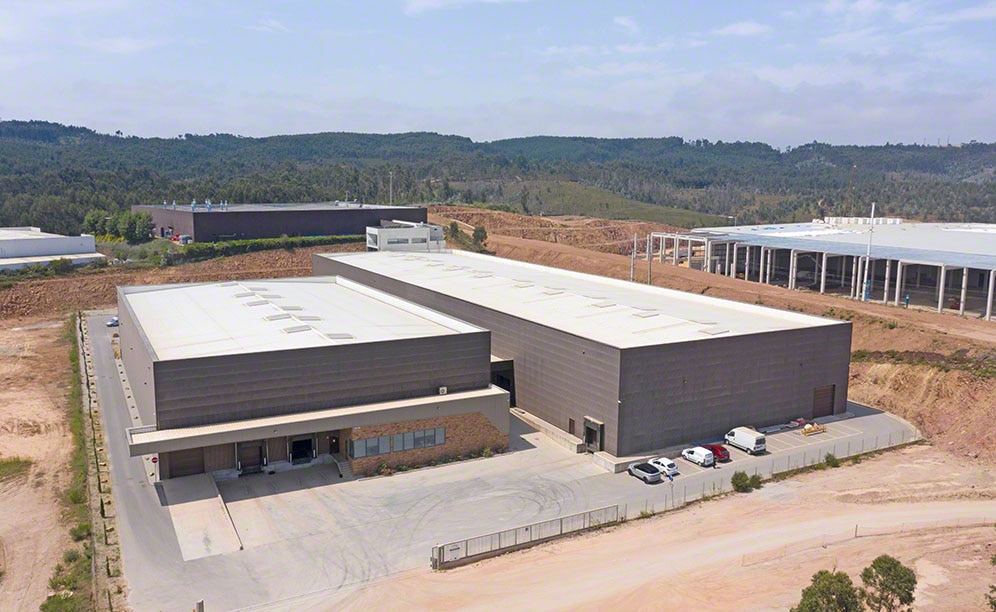
Finieco stores paper bags at its new centre in Santo Tirso, Portugal
Ask an expert