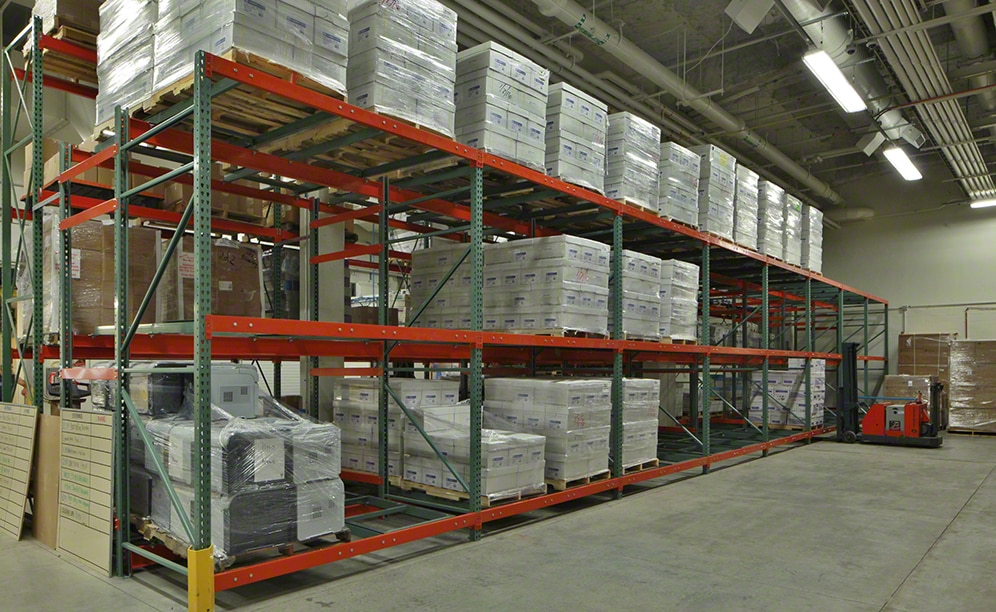
Just the Right Size: Mecalux Push-Back Racking Vertical Solution
Push-Back racking is the solution to the height and depth issues for the College of DuPage warehouse
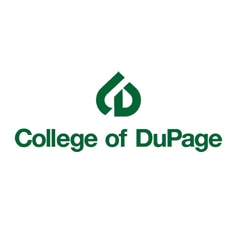
The warehouse at College of DuPage in Glen Ellyn, Ill., is unlike a typical warehouse. Rather than handling finished goods or some type of commodity that is shipping to a retailer, the college’s warehouse stores products used by a very specific type of customer – namely students, faculty and staff. With more than 28,000 students, College of DuPage is the second largest provider of undergraduate education in the State of Illinois. The Glen Ellyn campus covers 273 acres and has 11 major buildings. An institution of this size also uses a lot of paper and supplies, and that is where the college’s warehouse plays an important role.
Needs of the Customer
For a warehouse this busy, the standard pallet racking that it had in place was becoming insufficient. The existing rack was too deep, creating a safety hazard by forcing warehouse staff to reach in and grab product. The warehouse’s racking also was too high and close to the ceiling. “Whenever we put anything up there, we had to be really careful that we wouldn’t hit lighting or sprinkler heads.” said Angelo Conti, supervisor of warehouse services for College of DuPage. The height problem also required workers to break down pallets of paper in order to fit them in the racks, which consumed a lot of time, thereby increasing labor costs.
Interlake Mecalux’s Proposed Solution
After researching different rack manufacturers, College of DuPage brought in Interlake Mecalux to devise a solution. Shortly thereafter, they determined that Push-Back racking would be the ideal solution to the height and depth issues caused by the warehouse’s standard racks. “We kind of knew what the best scenario was going to be,” Conti said. “Interlake Mecalux was able to identify the specific product that would help us and our needs.”
There is no wasted space with Push-Back as the system minimizes the number of aisles needed to access product, creating a high-density, high-efficiency storage solution. The Push-Back system consists of carts and rails set within a supporting structure of frames and beams. The supporting bolted or welded structure uses standard pallet rack components for maximum flexibility and lower cost. Carts can be two-, three- or four-deep, depending on the application and space requirements.
When a forklift removes a pallet, gravity pulls the remaining pallets forward, ensuring that the front pallet position is always full. This makes pallet extraction simple, which is a benefit that was important for the College of DuPage warehouse considering the safety issues with its former racking. “Sometimes we just need one case of paper and with our old system, you’d have to reach in the rack to grab that case of paper. So for us, not having to put a person in the rack underneath thousands and thousands of pounds was a big plus,” Conti said. “It’s just the fact that you’re eliminating the potential for injury. You can’t really put a price tag on that.”
Installing the Push-Back racking system also solved the warehouse’s height issue. The standard racking that was in the warehouse previously was taller than the Push-Back system, but its setup was not beneficial. By installing the Push-Back rack, warehouse personnel were able to eliminate a top shelf level that was no longer practical. “We are now able to store full pallets of paper without breaking them down,” Conti said. “We used to have to break them down in order for them to fit in the racking. Now they can just be taken off the truck and put on the racks.” This, Conti adds, saves the college in terms of labor costs. The choice of Push-Back racking saved the college from having to buy specific handling equipment, such as a reach truck, to move a pallet. Instead, warehouse staff can now use a smaller sit-down forklift because all of the pallets in the racking are gravity-fed to the front, eliminating the need to reach or drive into the rack and decreasing the risk of rack damage.
The Push-Back racking installed in the College of DuPage warehouse also needed to be able to handle the heavy weight of the pallets full of paper. Interlake Mecalux’s welded structural steel Push-Back carts are perfect for heavy-duty applications. Each standard Push-Back cart carries a load of up to 3,000 lbs.
Ultimately, however, one of the things that impressed Conti was how responsive Interlake Mecalux was in meeting its customer’s needs. College of DuPage has strict requirements and stipulations when selecting its vendors, and Interlake Mecalux was able to supply the college with the data it needed to make the wisest choice in selecting a racking system.
“Personally what I liked is the customer service that I received and how Interlake Mecalux was able to work with our unique situation,” Conti said. “Interlake Mecalux worked with me and understood our needs and was able to provide the information I needed.”
Advantages for the Customer
- Efficient Use of Space: the College of DuPage’s new Push-Back system provides excellent selectivity without sacrificing product accessibility.
- Enhanced Safety: the Push-Back racking makes pallet extraction simple, eliminating the need for reaching or driving into the rack and reducing the potential for injury to operators.
- Cost savings: the college’s warehouse staff no longer has to spend time breaking down full pallets to fit them into the racking, saving the college on labor costs.
- Sturdy construction: The Push-Back system installed in the college’s warehouse can handle the heavy pallets full of paper because each cart can hold a load of up to 3,000 lbs.
Storage solution: Push-Back system | |
---|---|
Number of bays: | 24 bays |
Beam specs: | 96” Push back Beam - 4 Flange holes |
Number of beam levels: | Three |
Height of rack: | 11’ 6” |
Number of aisles: | one |
Aisle width: | 15’ |
Pallet positions: | 96 |
Pallet type: | 48 x 40 |
Pallets per level: | 32 |
Capacity: | 300,000 lbs. total |
Area racked: | Warehouse |
Gallery
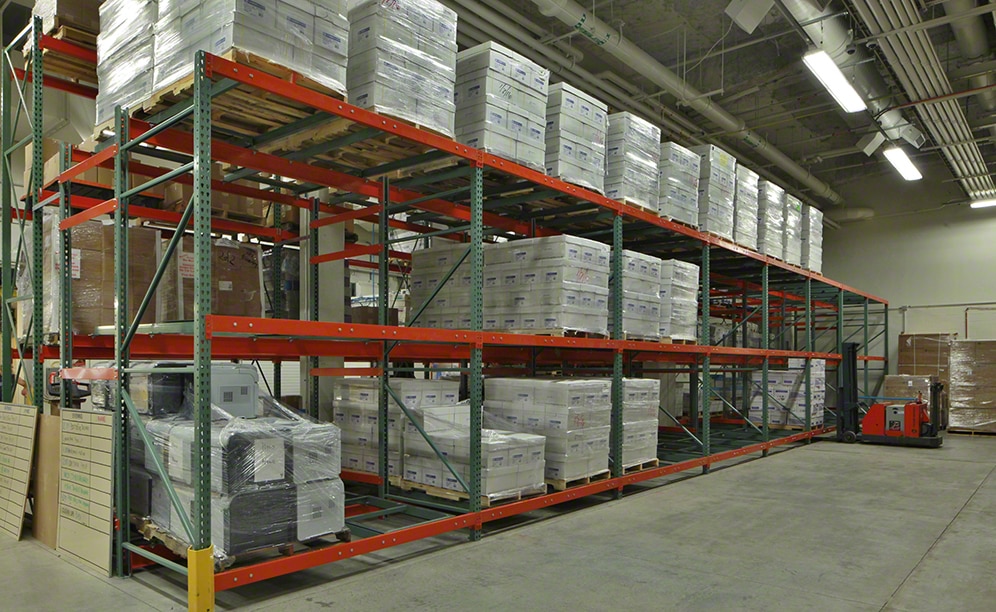
The Interlake Mecalux Push-Back system minimizes the number of aisles needed to access product
Ask an expert