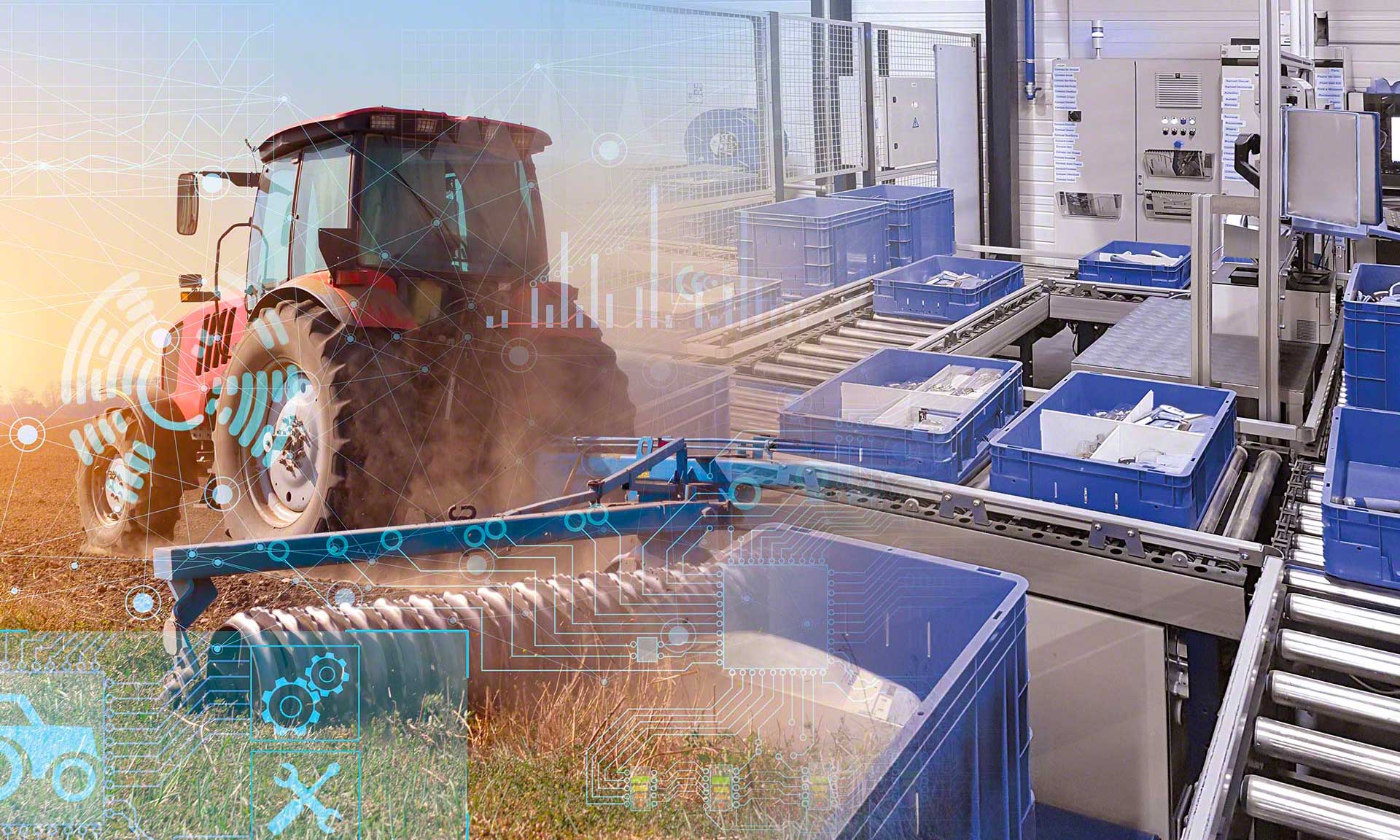
Groupe LORCA: same SKUs in 80% less surface area
With the new facility, each of Groupe LORCA's operators can manage 57% more order lines/hour
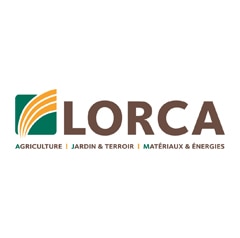
French agriculture cooperative Groupe LORCA has modernized its distribution center in Lemud (France) with the installation of an automated warehouse for boxes. This solution represents a major logistics achievement for the company with respect to its old mezzanine floor. This new, fully automated system is able to store the same SKUs occupying 80% less surface area. On top of that, it has optimized its picking operations: each employee can manage 57% more order lines per hour.
Over 661,380 tons of cereals a year
The business activities of agricultural cooperative Groupe LORCA, founded in 1970, are divided into three branches: Agriculture, linked to cereal crops and farming and livestock supplies; Gardening & Soil, with its network of gardening centers Magasin Vert and Point Vert; and Materials & Energies, specializing in construction materials and the sale of fuel to private individuals. The group is made up of more than 600 employees and 1,700 farmer members.
This co-op’s main activity comprises the harvesting, storage and sale of cereals: every year, members collect around 738,548 tons that are distributed primarily in northern Europe. Over the years, the firm has developed new activities that complement farming to enhance its business and expand its market, with the distribution of gardening and DIY tools as well as construction materials.
Growing distribution centre
The company’s distribution center, located in Lemud, France, supplies 51 gardening centers, its 77 franchises and the LORCA co-op’s farmer members.
In 2020, Groupe LORCA added on to this distribution center to increase its storage capacity: before, it occupied a surface area of 64,583 ft2; today, that figure stands at 96,875 ft2. Thanks to this new space, the company can confidently face its future prospects: to open more shops, boost its online sales channel and increase the turnover of the gardening and DIY division by 15% to 20% within the next five years.
To do this, Jean-Noël Rivat, Operations Manager at Groupe LORCA, explains that the firm needed a solution that would leverage the storage area better than its previous system: “Although we have more space now, we wanted to make the most of it. Hence, we looked for a storage solution for small products, which we had been storing on a 16,000 ft2 mezzanine floor.”
Another of Groupe LORCA’s priorities was “to increase productivity in storage tasks and, especially, picking,” says Jean-Noël Rivat. Before, operators had to go to the mezzanine floor to locate the items requested by each shop one-by-one. This process was very slow and, as it was entirely manual, it entailed a high risk of error.
In light of this, the co-op decided to contact Mecalux because, Jean-Noël Rivat contends, “We were convinced that it would help us find the perfect solution for meeting our objectives and needs.” After analyzing its requirements, Mecalux proposed building an automated warehouse with capacity for 6,000 boxes with about 6,500 SKUs. In just 3,230 ft2 of surface area, the automated facility is capable of managing the same SKUs that used to be stored on a 16,000 ft2 mezzanine floor.
Lastly, in order to control everything that occurs in the automated facility for boxes, the company has implemented Mecalux’s Easy WMS warehouse management system. This WMS monitors goods movements in real time and speeds up order preparation.
Characteristics of the automated facility for boxes
The warehouse consists of a single 112-foot aisle with double-deep 33-foot-high racking divided into 22 storage levels. A miniload stacker crane inserts and removes boxes from their locations with complete autonomy, following instructions from Easy WMS.
The boxes measure 16” x 24” and have two different heights: 7” and 16.5”. To maximize space in the facility, the upper levels of the racks are allocated for taller boxes, while the lower levels hold smaller ones.
Easy WMS organizes and distributes all the goods in the warehouse. When a box arrives, the first thing the WMS does is assign it a location based on algorithms taking into account its size and demand level. For example, boxes with a higher turnover are deposited on the ends of the aisle to expedite their entry and exit.
“One of the greatest advantages of this WMS is that we’ve been able to integrate it with our ERP, Microsoft Dynamics Business 360,” notes Jean-Noël Rivat. Communication between both software programs is fundamental for increasing productivity in the facility. Thus, the moment a shop places an order, the ERP system informs Easy WMS to organize its immediate preparation.
More efficient picking
This is the main operation of this warehouse: every day, workers prepare between 20 and 25 orders, each of which is sent to a specific shop. The complexity lies not in the number of orders picked, but in the fact that each one could contain up to 900 lines.
The automated warehouse for boxes has optimized the operation and even ramped up its productivity. According to Groupe LORCA’s Operations Manager, “Before, employees managed a maximum of 70 lines per hour. Now, they can handle close to 110 lines an hour, a figure we’ll surpass in a few weeks.”
The company has achieved this thanks to the automation provided by the automated warehouse for boxes. Operators no longer have to travel to the mezzanine floor to locate the products. Now, they follow the product-to-person method, whereby they remain at their pick stations while the stacker crane and conveyors bring them the goods they need.
Once they receive the boxes from the facility, the operators remove the products indicated by Easy WMS and sort them into orders. They deposit the goods behind them on racking for carton flow picking with capacity for 54 boxes (each corresponding to an order).
This racking is 6.5’ high, comprising slightly inclined platforms with rollers, causing the boxes to slide via gravity to the end of the lane. The benefit of this solution is that, once operators have completed a box, they push it to the other side of the racking, where it slides automatically to the dispatch area.
“Sorting the orders directly on the racks has saved us a tremendous amount of time in this operation,” highlights Jean-Noël Rivat. To facilitate the work of the operators preparing orders, the picking racks are outfitted with put-to-light devices. These are located on the front of the racks and serve to show the number of SKUs to be put in each box. Once the operator has placed the item(s) in the box, he/she pushes the confirmation button to notify the WMS that the action has been completed and to receive more orders.
Better leveraged distribution center
The new automated warehouse for boxes has constituted a huge step forward for Groupe LORCA: it not only accommodates the products in a small space measuring 3,230 ft2, but has also raised productivity in order picking.
Furthermore, Groupe LORCA’s facility is prepared to support the business’s growth in the coming years, as space has been set aside to install an additional pick station when required.
For its part, the Easy WMS warehouse management system provides extremely strict control of the goods and sends instructions to the operators on how to prepare the orders more quickly. “We’ve improved picking dramatically, achieving greater efficiency and agility,” enthuses Jean-Noël Rivat.
BEFORE |
AFTER |
PERCENTAGE |
|
---|---|---|---|
Solution | Mezzanine floor | Automated warehouse for boxes | |
Surface area | 16,000 ft2 | 3,230 ft2 | -80% |
Lines/hour | 70 | 110 | +57% |
In addition to the maximized productivity and use of space, the automated warehouse for boxes with Easy WMS has significantly enhanced picking. This solution ensures total availability of the goods, which streamlines picking.
Advantages for Groupe LORCA
- 80% less surface area occupied: Groupe LORCA has gone from storing its 6,500 SKUs in a 16,000 ft2 mezzanine floor to housing them in an automated warehouse for boxes measuring a mere 3,230 ft2.
- 57% rise in productivity: product-to-person picking has streamlined picking tasks. Operators used to manage 70 lines/hour and can now handle up to 110 lines/hour.
- Maximum efficiency: Easy WMS ensures more rigorous control of the goods and increased speed in storage and picking tasks while reducing errors and optimizing operating costs.
Automated warehouse for boxes | |
---|---|
Storage capacity: | 6,000 boxes |
Box sizes: | 16” x 24” x 7” / 16.5” |
Max. box weight: | 110 lb |
No. of SKUs: | 6,500 |
Racking height: | 33’ |
Racking length: | 112’ |
Total surface area: | 3,230 ft2 |
Gallery
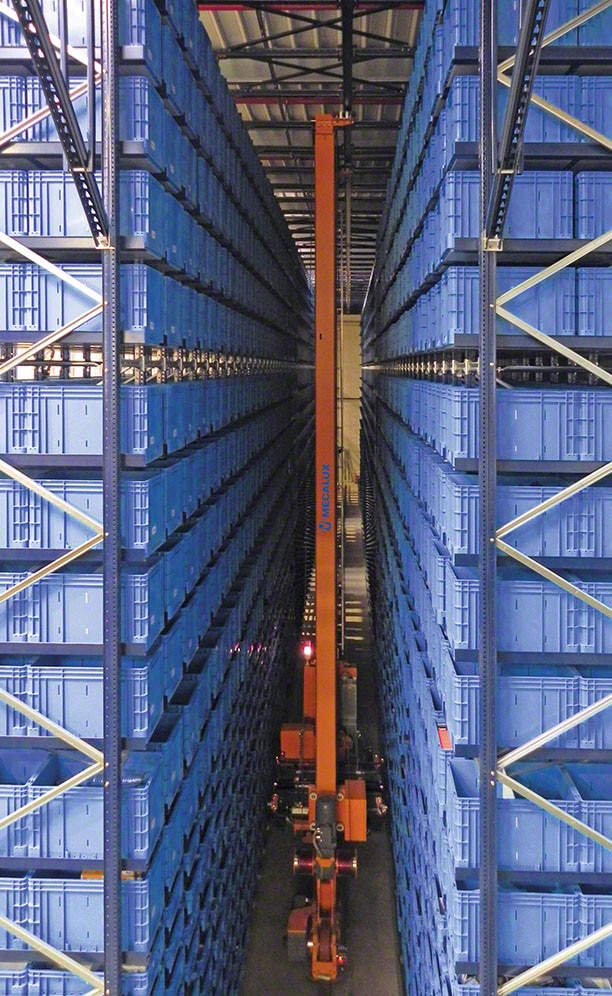
Groupe LORCA's automated warehouse for boxes in Lemud, France
Ask an expert