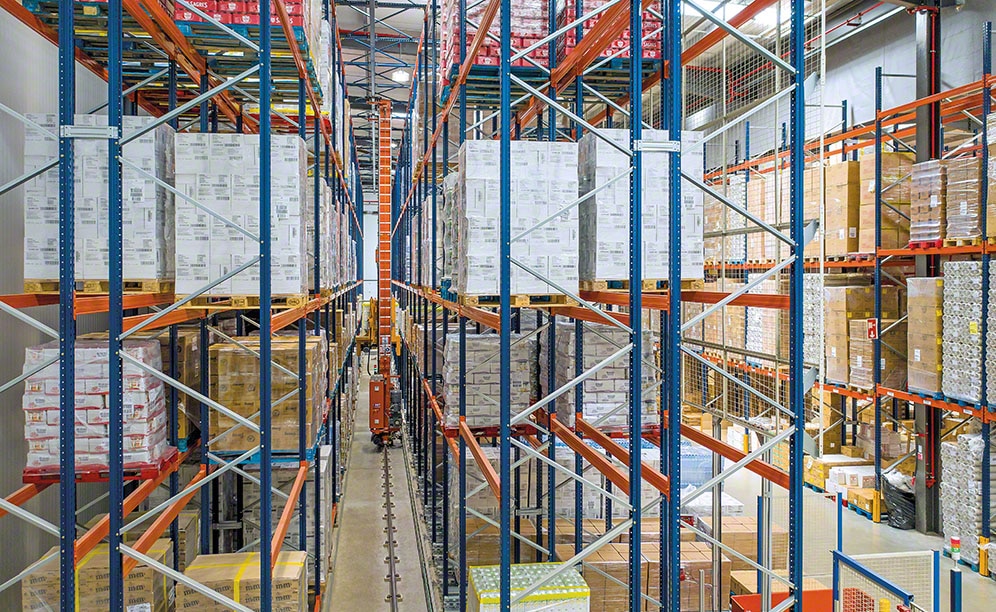
Technology and automation reduce in-freezer working hours
HAVI’s fully automated freezer store, where it houses food.
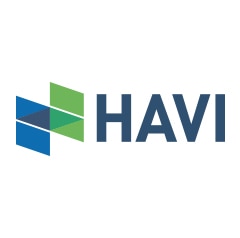
HAVI has opened a modern logistics center in Portugal divided into three areas operating at different temperatures. Mecalux has installed all the storage systems (two automated warehouses, pallet racks, drive-in racks, and racks with the Pallet Shuttle system). In addition, it has implemented Easy WMS.
About HAVI
HAVI is a global, privately owned company that focuses on innovating, optimizing, and managing the supply chains of leading brands. Services range from analytics, logistics, supply chain management, and packaging. Founded in 1974, HAVI partners with customers in more than 100 countries. In Portugal, HAVI’s clients in the food service sector include global players such as McDonald’s and domestic brands such as Portugalia.
HAVI’s strength is its operational excellence in service, safety, and quality. It is a leader when it comes to ensuring restaurants have what they need when they need it. To deliver this promise, HAVI’s logistics centers must have fast, efficient operations as well as comprehensive control over all goods, with a focus on shelf life and quality standards.
A modern, efficient, sustainable warehouse
Mecalux's technical department and HAVI joined forces to design, build, and commission a modern logistics center in Vila Nova da Rainha, Portugal. This will be the distribution point for supplying HAVI’s customers in the restaurant industry throughout the country. The two multinationals have already worked together on other projects, forming a solid team. For example, Mecalux installed an AS/RS for HAVI in Moscow, Russia. Movirack mobile pallet racks were also set up in the company’s center in Lodi, Italy.
The new logistics center in Portugal, with a combined surface area of 2.47 acres, has been split into three zones to store and manage goods according to their characteristics: frozen, refrigerated, and ambient temperature. Each storage zone has a specific layout based on logistics needs. For this reason, Mecalux has installed both automated and standard storage and picking solutions. The common denominator between all these solutions is their operability and reliability when it comes to managing stock. The speed they provide in storage and order preparation tasks stands out. Overall, the center is a technological benchmark and a pioneer in automated -4 °F logistics processes.
Pallet racks are the only storage system installed in all three areas. The system was chosen because of its adaptability to any load, weight, or volume. In addition, the direct access it provides streamlines merchandise management.
Pallets are picked directly from the lower storage levels with the help of radio frequency (RF) devices. Palletized reserve stock, on the other hand, is placed on the upper levels of the racks.
Mecalux prioritized the safety of the goods and operators when designing each storage solution. It is essential to respect and not break the cold chain so that food reaches customers at a controlled temperature. Accordingly, the access points to the frozen- and cold-storage chambers are insulated, preventing sudden changes in temperature, cold loss, and condensation. Automation also increases warehouse safety because 77% of pallets movements are performed automatically. What is more, ergonomics are enhanced when handling goods, and physical effort is decreased. The system also means operators need to spend less time working in low-temperature environments, simultaneously reducing energy consumption by 10% thanks to a lower number of freezer door openings and better insulation of the chamber.
We’ve greatly reduced manual movements in the warehouse. Consequently, the risk of accidents is low. Plus, we’ve achieved outstanding results in volume fluctuation management, shelf-life control, and order reliability.
Frozen-storage installations
The frozen solution is equipped with the modern Automated Pallet Shuttle system operated by two stacker cranes and managed by Easy WMS software. Higher-turnover SKUs with goods such as hamburgers, fries, chicken products, etc. are housed here. “A big part of our total volume delivered to restaurants is prepared in the freezer,” says a HAVI representative.
The warehouse, which operates at -4 °F, has twin aisles with two blocks of racks. Overall, the six-pallet-deep storage lanes provide capacity for 2,247 pallets, with an increased occupancy of 75% compared to a normal racking system.
The Automated Pallet Shuttle system optimizes storage space and reduces the volume to be chilled. This not only maximizes storage capacity but also saves on power costs for keeping the installation below zero. “In addition, our vision was to increase the efficiency in that area and, at the same time, improve the working conditions of our employees,” says a HAVI representative.
The warehouse operation is completely automatic. The two twin-mast stacker cranes that run here transport goods between the in-warehouse entry and exit points to the storage channels. Meanwhile, the shuttle moves the goods inside the channels. All this is managed and supervised by Easy WMS, which is responsible for providing full traceability of each product and controlling warehouse stock. An interface with HAVI’s WMS also ensures full traceability from the receipt of goods up to customer delivery.
A conveyor circuit has been installed next to the warehouse. It moves products to the picking area at a constant 66 ft/min, all according to the goods-to-person principle. “We obtained better working conditions with two goods-to-person stations,” a HAVI spokesperson reported. Orders sequenced by Easy WMS are prepared jointly or separately in two manual and one automatic pick station, depending on each order’s requirements. To do so, a shuttle connects the three pick stations as well as the stretch-wrapping and labeling area.
The automatic pick station is equipped with an anthropomorphic robot that handles full layers of high-turnover products representing 40% of the total volume prepared in the freezer. The big advantage of this type of machine is its delivery speed, since it can prepare several orders simultaneously and handle many layers of goods safely. Automatic picking delivers speed, safety, and operational cost savings, even more so in the frozen-storage installations.
The two manual pick stations automatically receive the goods from the conveyors when they arrive from the warehouse, or with transfer cars from the anthropomorphic robot. In both cases, the goods-to-person principle means fewer trips and faster order preparation. In each station, which is equipped with pick-to-light (PTL) technology, the operator can prepare up to eight customer orders simultaneously in an ergonomic way.
This results in higher productivity and work quality. Easy WMS tells operators on screen which tasks they must perform to keep the orders sequenced, what products to extract, which order to place them in, and so on. Once finished, the worker notifies the WMS by pressing the PTL device.
The transfer car then picks up the finished orders and takes them to the stretch wrapper and labeling machine. Afterward, conveyors move these packages to the shipping area. This zone, which is also kept at a controlled temperature to prevent cold chain breakage, comprises eight preload flow channels. Here, pallets are classified and grouped according to the order or transportation route. Keeping track of the sequence and pre-grouping into preload channels saves time and minimizes errors when loading goods onto the trucks.
A block of compact racks with the semi-automated Pallet Shuttle system in the freezer store (with a capacity for 237 pallets) accommodates bread and foodstuffs. This solution, which also optimizes the storage area, has a motorized shuttle that moves pallets inside the channels automatically. However, unlike the AS/RS, operators must place the shuttle and the goods in the corresponding channel using reach trucks.
Cold-storage installation
Apart from selective pallet racks, Mecalux has installed a block of 29-foot-high drive-in racks that provide storage capacity for 1,996 pallets. The racks are mainly used to hold products such as tomatoes, ready-made salads, etc. It is an optimal solution for storing homogeneous products and a large number of pallets per SKU.
The racks comprise a set of four high-level lanes. Meanwhile, each level has support rails on both sides where the pallets are placed. When managing the loads, operators use reach trucks to enter the storage lanes with the goods raised above the level where they are going to be deposited.
Ambient-temperature installation
In this area — dedicated to products such as bottled water and other beverages, ketchup, mayonnaise, toys, packaging, etc. — there is an automated warehouse with a capacity for 530 pallets. It consists of a single aisle with 33.5-foot-high double-deep racking on both sides. A twin-mast stacker crane is responsible for moving products down the aisle, from input conveyors to the locations assigned by the WMS.
On the lower racking level, 36 flow picking channels that coincide with the working aisle have been installed. Each channel can hold four pallets of the same SKU: one for picking and the other three for reserve stock. The operators, using RF scanners, locate the SKUs that comprise each order and pick items from the pallet closest to them.
When a flow channel runs out of palletized goods, the WMS orders the stacker crane to replenish that channel with the corresponding merchandise. The advantage of this system is that the products for picking are always on hand, preventing delays and stoppages in order processing.
Easy WMS: sequencing and merchandise control
HAVI’s two AS/RS (the freezer store and the ambient installation) are run by Mecalux's Easy WMS warehouse management system. In the automated warehouse with the Pallet Shuttle, Easy WMS identifies items when they arrive at the warehouse. It then assigns them a location based on their stackability and typology. The system offers total traceability, knowing the exact location of all goods in real time.
The WMS also organizes order preparation. On the one hand, it instructs which SKUs to send to the pick stations. On the other hand, it tells the operators which products comprise each order. Easy WMS carries out all these tasks considering a key HAVI prerequisite: order sequencing. Grouping and sequencing the goods for dispatch avoids errors, speeds up operations, and allows the company to offer a more efficient service.
Easy WMS executes the stacker crane movements in the ambient-temperature installation. Its job is to supply the flow picking channels with needed goods when they become empty.
Easy WMS is interfaced with HAVI’s WMS to control stock, provide traceability from supplier to customer, and sequence all distribution center processes.
Technology to serve customers
HAVI has invested in a modern, high-tech distribution center with efficient operations. It is ready to supply restaurants promptly and on demand. Automation has not only streamlined warehouse flows but also reduced logistics costs and improved the working environment for operators. Importantly, the equipment also allows HAVI operators to learn new skills.
Advantages for HAVI
- Goods sorting: the warehouse has been designed in three zones, where different storage solutions have been enabled for efficient warehousing and management of goods.
- Order sequence: Easy WMS is responsible for sequencing the orders to be prepared and sending them to the preload area, where they are sorted by order or transportation route.
- Technology and safety: all the technological elements installed here mean the warehouse complies with the highest safety standards both in terms of the goods and the operators.
- Great place to work: HAVI has modernized its working environment, making it a more attractive place to work for operators who can learn new skills when operating the technology and the installation.
Selective pallet racks | |
---|---|
Storage capacity: | 6,341 pallets |
Pallet size: | 32" x 48" |
Max. pallet weight: | 1.1 t |
Racking height: | 28' |
Gallery
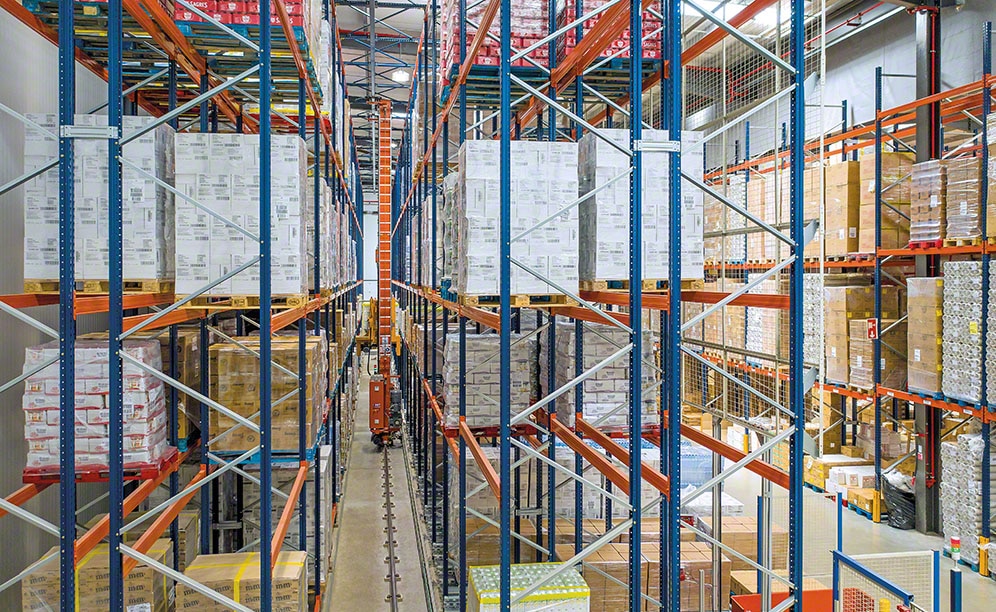
Pallet Shuttle system with a stacker crane at HAVI in Portugal
Ask an expert