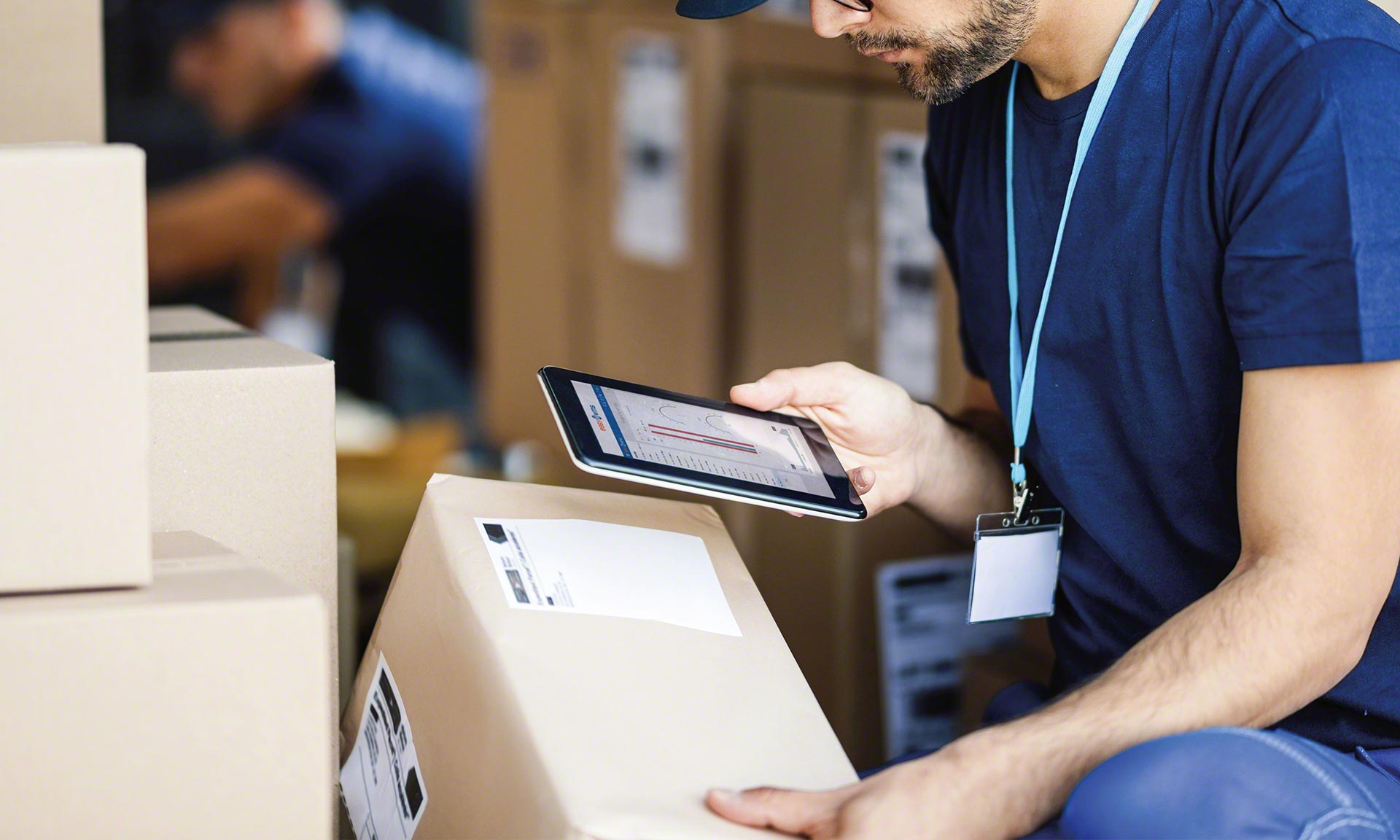
IRIS optimizes the operations of its IT equipment warehouse with Easy WMS
IRIS, a French IT solutions and services company, monitors the status of 9,000 SKUs in real time.
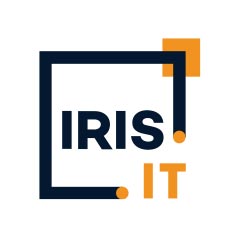
IRIS, an IT solutions and services company for all industrial sectors, has digitalized its warehouse in France with Easy WMS from Mecalux. By following instructions from RF scanners, IRIS warehouse operators are faster, more accurate, and error-free.
IRIS: Hardware installation, maintenance and repair
From its headquarters in Billy-Berclau (France), IRIS offers IT solutions and services to organizations in all industrial sectors, primarily retail and healthcare. The business provides hardware and maintenance solutions adapted to the requirements of each customer, as well as support seven days a week for companies located in France. Founded in 2009, IRIS is a company with 300-plus customers, operations in over 30 countries, and an annual turnover of more than $15 million.
CHALLENGES
|
SOLUTIONS
|
ADVANTAGES
|
---|
IRIS has a firm commitment to the quality of its IT services. With a history of almost 15 years, the company has always prioritized the satisfaction of its customers when it comes to supplying them with the solutions they have requested.
In order to serve its customers as efficiently as possible, logistics is one of IRIS’s key processes. Providing hardware solutions on time can only be achieved with rigorous control of goods. “IT equipment is not just any product; it requires ideal storage conditions and rapid distribution to achieve immediate availability anywhere in Europe whenever it needs to be operational,” says Yves Courtois, the company’s Logistics Manager.
IRIS’s 64,584 ft² logistics facility is located in Billy-Berclau, in the north of France. There, the company accommodates more than 9,000 SKUs that are distributed to its 300+ customers throughout Europe. The business recently implemented Mecalux’s Easy WMS warehouse management system to optimize processes and maintain much stricter control of goods.
Before digitalizing the facility, all operations were carried out manually. “We used our ERP software to organize tasks and track the goods. Operators would enter the items received and orders shipped into the system every day, which posed a high risk of making mistakes,” says Courtois.
As IRIS began to expand its customer base and the pace of work in the warehouse increased, the company realized it had to overhaul its logistics operations to continue providing good service. “We knew that the organization of the stock could be improved. The ERP was incapable of optimizing warehouse locations, a process that to us seemed essential to facilitate operations as demanding as order picking. We needed to ensure the traceability of the goods from the moment they arrive at the warehouse until they’re shipped. To achieve this, we had to install more sophisticated software focused on logistics management,” says Courtois.
After analyzing different options, IRIS decided to install the Easy WMS warehouse management system to improve stock control and raise productivity in the facility. “We opted for the Mecalux solution because we saw that it could be adapted to the specific features of our warehouse. The system is scalable: it adjusts to changes in the business, such as increases in sales or the incorporation of new technologies in the future,” says Courtois.
One of the issues that most concerned IRIS was the commissioning of the software. “What convinced us was the simplicity and speed when implementing the system. In our case, within a short space of time, the operators were already preparing orders following instructions from Easy WMS,” says Courtois. The Mecalux technical team worked closely with IRIS to find the best solution for the company and resolve any questions.
Digitalized logistics processes
Easy WMS intervenes in all operations carried out in the IRIS warehouse, ranging from receiving goods from suppliers to preparing and distributing more than 150 daily orders to customers around Europe.
“Installing Easy WMS has been a major step forward in our logistics management,” says Courtois. IRIS operators only needed a short training course to learn how to use the software’s different functionalities. They became familiar with them very quickly. Using RF scanners, they follow the system’s instructions, which indicate step by step how to locate the hardware equipment. “Our team is delighted with the software because it’s simplified their work. Now, order picking is much faster,” says Courtois.
In the receiving area, for example, operators have noticed a great improvement. They no longer have to manually enter the products that have arrived at the warehouse into the ERP. They only have to read the barcode of each pallet or each package with the RF scanner, and the system enters them into the database and assigns them a location automatically.
To decide the position of each item, Easy WMS takes into account variables such as the SKU, the level of demand, or whether the product is part of an order that a customer has already requested. The Mecalux software has been integrated with IRIS’s ERP so that both systems can share information to boost the facility’s throughput. For example, the ERP notifies Easy WMS of the products that the warehouse is going to receive so that it can verify that the corresponding goods have arrived.
Order picking is another operation that has seen a significant rise in productivity thanks to Easy WMS. “Operators no longer waste time looking for IT products in the warehouse,” says Courtois. The system helps workers prepare each order: it tells them which items to locate and their exact location. It also generates efficient routes through the building to ensure that operators travel the shortest distances possible.
“By organizing all movements of goods and operators, we have total control of our stock. The software knows the precise location of each product at all times and prevents errors from occurring,” says Courtois. Advanced stock management results in much more fluid operations.
Personalized service
One of the services that the company offers is the customization of IT equipment. For example, when a customer requests computer equipment for their business, IRIS makes sure to deliver it with the applications installed, taking into account that each department may need specific computer programs.
To customize IT equipment, IRIS has implemented Mecalux’s VAS (value-added services) software. This Easy WMS extension incorporates the necessary functionalities to guarantee that each requested order is delivered respecting certain customer requirements.
When preparing orders, VAS indicates to the operators whether the products they have removed from the racks need to undergo any additional processing. If this is the case, the software shows them where to move the equipment to configure it before distributing it to customers.
VAS is also involved in the IRIS recycling process. Another service provided by the company, as part of its commitment to caring for the environment, is the collection and treatment of computer equipment at the end of its useful life. After destroying the data and ensuring the confidentiality of the information, IRIS recovers and recycles the computing devices to give them a second life. To do this, the software sends instructions to the operators on what to do with each product, whether this involves moving it to the waste area or to be repaired. Digitalization helps the company efficiently manage second-hand IT equipment and comply with regulations.
Speedy, controlled shipments
“We’ve saved time on shipments and are now much faster. It’s no longer necessary to generate and print the documents and labels for carriers manually. The software does it with total autonomy and speed,” says Courtois.
IRIS has implemented Multi Carrier Shipping Software, an Easy WMS extension prepared to optimize order distribution. This program organizes the packaging, labeling, and shipping processes accurately, swiftly, and without errors.
The system has been integrated with the software used by TNT and UPS, IRIS’s delivery agencies, to automate order management. The program has simplified shipments: when an order is completed, Multi Carrier Shipping Software selects the appropriate transportation agency. It then communicates with that carrier to obtain the necessary data to generate and print the labels and the tracking number.
Transportation agencies are synchronized with the facility to streamline the work of warehouse operators. At the same time, carriers can be much more agile and ensure that deliveries are made more quickly. When they arrive at the IRIS facility, they only need to load the goods onto the truck and distribute them.
Logistics in a constant state of flux
For IRIS, solving customer needs efficiently involves controlling goods and achieving optimized operations. The company has embraced digitalization to boost its logistics processes and adapt to market changes with ease. In recent years, the business has undergone tremendous expansion, which has compelled it to transform and overhaul its operations.
“Now that we have digital logistics processes, our future prospects are much more promising. This year, we plan to open a new, larger warehouse that will enable us to keep supplying our customers effectively. We’re also looking forward to leveraging the Mecalux software’s new functionalities to continue providing customers with impeccable service,” says Courtois.
Thanks to Easy WMS, we’ve transformed our logistics processes and are now much faster and more efficient in distributing goods to our customers. We recommend Mecalux software to companies that have a high level of activity in their warehouses.
Gallery
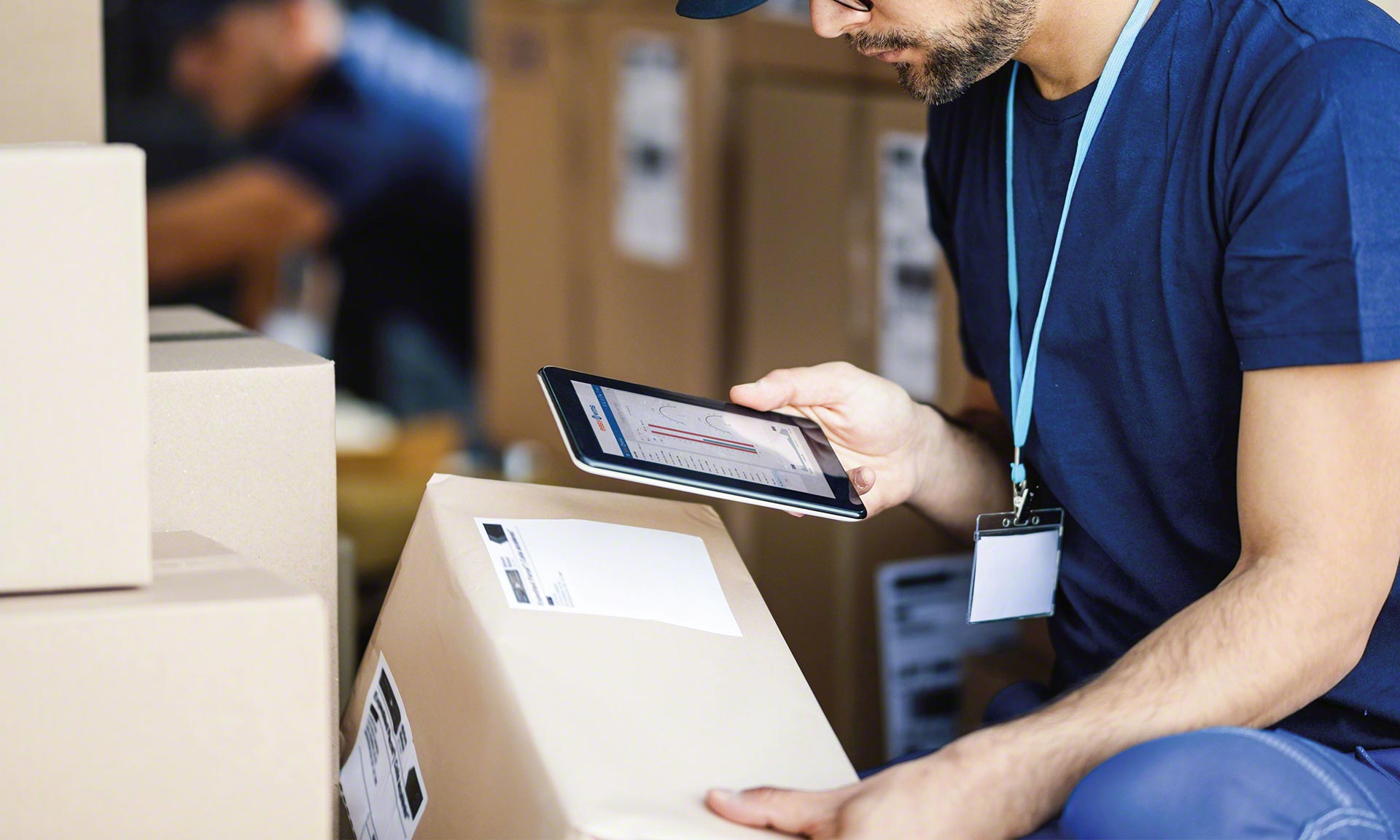
IRIS operators prepare orders with RF scanners
Ask an expert