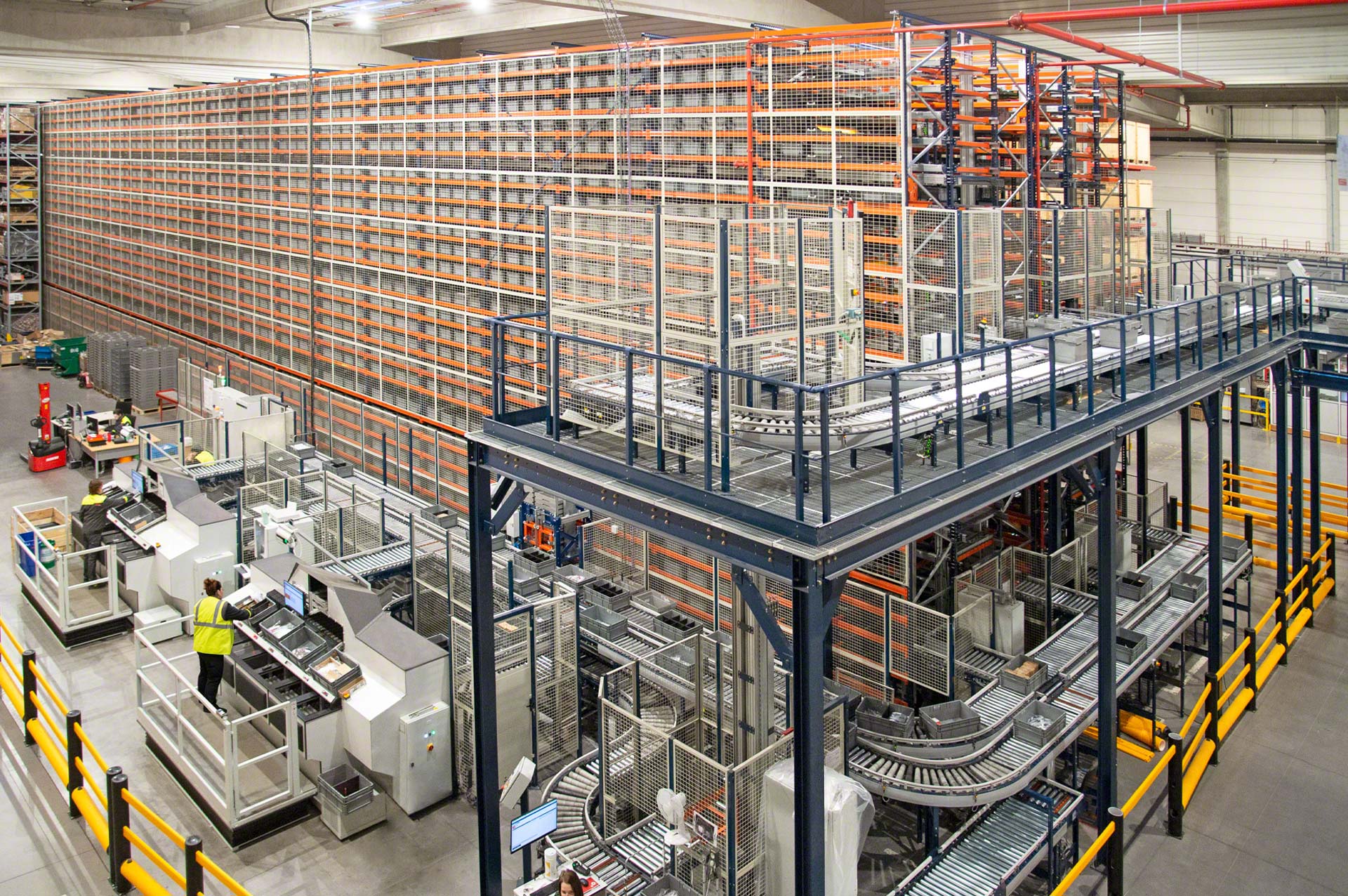
Manitou Group automates its spare parts warehouse
Manitou Group automates the storage and picking of spare parts with an end-to-end logistics solution from Mecalux.
Manitou Group, a manufacturer of materials handling, lifting, and earthmoving equipment, has automated its facility in France. The company has installed the Mecalux Shuttle System to manage small products and two high-performance pick stations.
Manitou Group: a family-owned company with global reach
A world leader in the manufacture of material handling, lifting, and earthmoving equipment, the Manitou Group is a company that strives to improve the working conditions, safety, and performance of its customers. The business’s priority is to protect people and the environment. With innovation at the heart of its DNA, the company designs, produces, and distributes equipment through its two brands — Manitou and Gehl — for customers in the construction, agriculture, and industrial industries.
- Founded in: 1958
- International presence: 140 countries
- Network of distributors: 900
- No. of employees: 5,000
- Turnover: $2.5 billion in 2022
CHALLENGES
|
SOLUTIONS
|
ADVANTAGES
|
---|
The Manitou Group, a global leader in material handling and lifting equipment, has modernized its logistics center in Ancenis (France) with the aim of boosting order picking and, in turn, maximizing its storage capacity. This logistics facility, which employs 200 people, is responsible for delivering spare parts to Manitou dealers and other sites owned by the Group.
Maxime Deroch, President of Manitou Group’s Services & Solutions Division, outlines one of the company’s main logistics needs: “In order to provide our customers with better service, we wanted to reduce picking times for orders needing to be shipped the same day.”
It was clear to the Manitou Group that to combine productivity and capacity in the same space, it was essential to automate its logistics processes: “We were looking for a solution that would take advantage of the latest technological innovations to optimize the delivery of urgent orders. The Mecalux project team understood that our storage capacity problems could be solved with a high-density solution, which reinforced our decision,” says Deroch.
Logistics is fundamental for a company like the Manitou Group, and its post-sale service is a differentiating factor in its business. “In this warehouse, we manage spare parts that we then send to our dealers so they can manufacture or repair machines. It’s crucial to ship our products as quickly as possible because, in some cases, the customer’s machines are at a standstill, waiting to receive the spare part they need. Our commitment to dealers is that all orders that come in before 5 p.m. must be shipped by 7 p.m.,” says Benoît Stanislas, Supply Chain Project Manager for the Manitou Group.
To meet the needs of the Manitou Group, Mecalux installed the Shuttle System, an automated storage system for boxes that speeds up order picking. This solution provides a constant flow of goods from the storage area to the two high-performance pick stations.
“The Shuttle System has replaced an area with conveyors and racking where we’d been picking orders manually. It’s true that we could deploy more operators whenever we had to increase productivity, but we were very limited in terms of space and storage capacity,” says Stanislas.
Mecalux’s innovative storage system, together with the high-performance pick stations, increases productivity in the picking of orders for small parts with a high turnover: just two operators prepare 500 order lines per hour. In addition, this solution has increased storage capacity by 130%; the company can now store 20,000 totes — 20% of its total stock — in just 6,028 ft². This system has effectively mitigated the logistics center’s space constraints.
In the design of the warehouse, Mecalux also took into account the Manitou Group’s growth strategy. The automated two-aisle solution is scalable: it offers the possibility of adding on an aisle to handle higher order picking volumes in the medium to long term.
We were looking for a logistics solution that would take advantage of the latest technological innovations to optimize the delivery of urgent orders. The Mecalux project team understood that our warehouse capacity problems would be solved with a high-density storage solution. And that convinced us, because improvements in the quality of our service reinforce the satisfaction of our customers.
The Manitou Group has also implemented Mecalux’s Easy WMS management software to strictly monitor the 16,000 SKUs in stock. The program tracks incoming and outgoing goods and keeps a real-time record of inventory status. Easy WMS connects bidirectionally with the Manitou Group software to optimize operations in its facility. “We’re very happy with the performance of Easy WMS. It’s intuitive and easy to use,” says Stanislas.
“Mecalux is a world leader in storage systems. We had a very good impression when we were presented with the project in the pre-sales phase because they understood our needs. We were convinced by the proposal to install a system that would offer high-density storage and, at the same time, high-throughput order picking,” says Stanislas.
500 order lines per hour
The Shuttle System is an automated storage solution for boxes that uses all available surface area to accommodate a larger number of products in a limited amount of space. The storage system consists of two aisles spanning 240’ long with 26.2-foot-high double-deep racking. On each of the 23 levels, a shuttle removes the boxes from their locations using telescopic arms. Subsequently, four pallet lifts and conveyors move the products to the high-performance pick stations in complete autonomy. In this way, the system makes it possible to prepare orders according to the goods-to-person criterion, avoiding operator travel around the warehouse and increasing productivity.
The two high-performance pick stations, installed on one side of the automated storage system, are ergonomic workstations specially designed to foster the picking of multiple orders at the same time. Each station consists of two levels: on the upper level, the boxes with the goods arrive to make up the orders. The system works on the pick-to-tote principle; the operator takes the products from these boxes and places them in a tote located on the lower level and corresponding to a specific order.
To ensure error-free picking, each pick station is equipped with six tote locations with put-to-light devices. By following the Easy WMS instructions, operators can identify the location from which they are to extract the goods and in what quantity.
Exact traceability of 16,000 SKUs
“The Easy WMS management software handles customer orders and tells the Shuttle System which products it needs to complete them. The software instructs the automatic handling equipment to pull the boxes from the racks and send them to the high-performance pick stations for the orders to be prepared,” says Stanislas.
Easy WMS keeps a tight control of the products due to the permanent two-way connection with the Manitou Group software. Mecalux’s Easy WMS receives an ASN (Advance Shipping Notice) message from the software for each spare part that arrives at the warehouse from suppliers. Based on this message and using a set of rules and algorithms, Easy WMS assigns a location to the goods according to their characteristics and turnover.
Each aisle is divided into three sections according to product turnover: type A, B, or C. Thus, for example, type A items (higher demand level) are placed at the front of the racks to streamline entries and exits, while B and C items are slotted further away. At night, Easy WMS is able to optimize the locations of the automated storage system by moving the boxes towards the exit stations.
The traceability of the 16,000 SKUs stored in the Shuttle System is total. With Mecalux’s software, Manitou Group knows the real-time location of all its products and can track any movement so as to avoid errors that could disrupt its supply chain.
Integrated logistics solution
With the integrated logistics solution installed by Mecalux, the Manitou Group can offer excellent service to its dealers. “Thanks to the quality of our service, we’re constantly improving customer satisfaction,” says Deroch.
Stanislas, stresses the importance of having a reliable supplier: “The Shuttle System meets our expectations. Now that the project has been completed, we continue to work with Mecalux on optimizing and improving our productivity. It’s very reassuring to know that we can count on their assistance at all times.”
The Manitou Group is an innovative company that, from the outset, has been committed to technology with the aim of fostering change and the constant improvement of its processes. The opening of this new spare parts warehouse is a testament to the promising future that lies ahead for this business.
We’re satisfied with the performance of the Mecalux Shuttle System because we’ve been able to increase productivity in the storage, dispatch, and picking of spare parts. In addition, Easy WMS more than meets our expectations. It’s a very intuitive and user-friendly tool.
Gallery
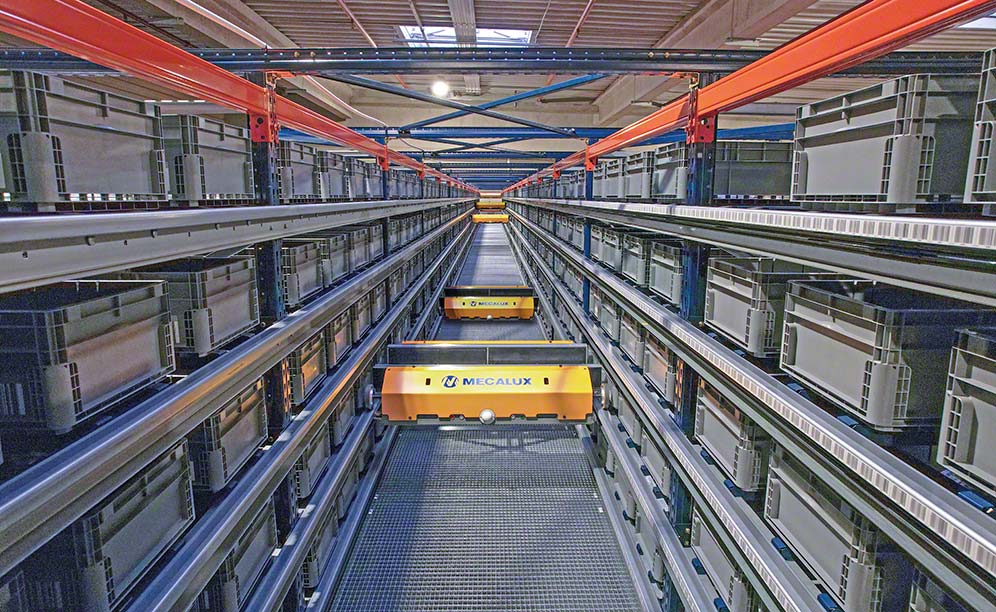
Shuttle System in the Manitou Group warehouse in France
Ask an expert