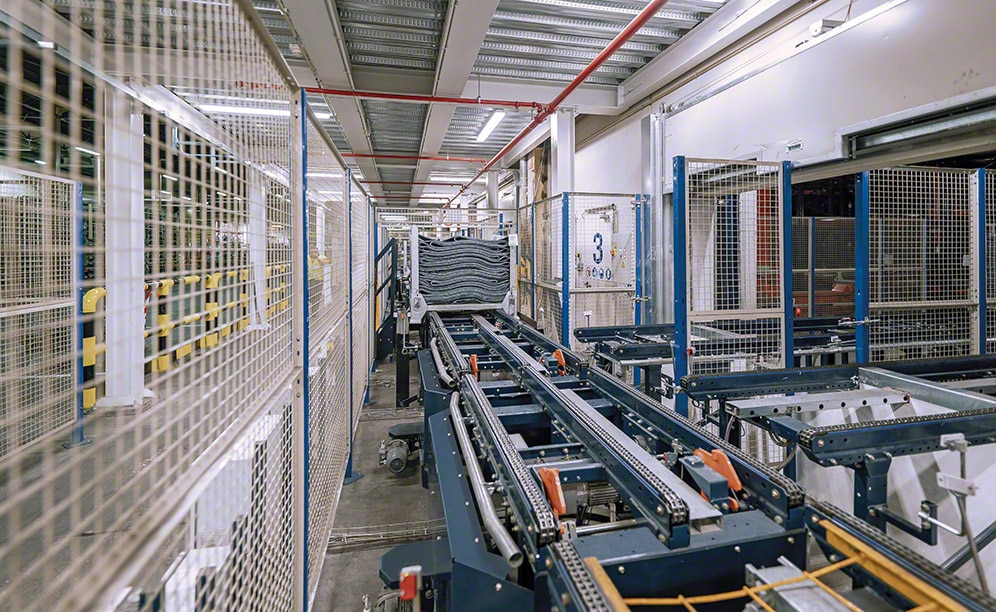
Automated rack-supported warehouse of Michelin integrated with manufacturing
Michelin has one of the largest tire making factories of Spain in Vitoria, Basque Country
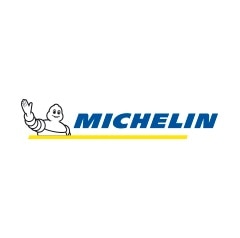
The tire maker Michelin has enlarged its manufacturing center in Vitoria (Spain) to deal with the increase in manufacturing achieved in recent years. In just eight months, Mecalux has constructed a turnkey automated rack-supported warehouse adapted to the size of Michelin’s metal containers. It is fully automated, with conveyors, stacker cranes, full pallet stackers and transfer cars that move the containers throughout the installation, as per the needs and storage goals of the company.
A manufacturing centre under expansion
In 1889, two brothers, André and Edouard Michelin, embarked on a project to develop advanced transportation solutions. Since then and up until the present, the company’s objective is to bring about better mobility of goods and people or, in other words, society’s development.
Michelin has more than 70 manufacturing plants spread throughout 20 countries. The company continually invests in its manufacturing centers and refurbishes them for new market demands. So, the business decided to build a warehouse in its Vitoria center (Spain) for the rubber used in the tire production processes.
The installation’s priority is to make full use of the surface area to provide better storage capacity. According to Antonio J. García-Montalvo, manager of this Michelin project, “Beforehand, we used a much smaller warehouse where we stacked the containers, which was extremely impractical.”
“The technical team of Mecalux worked on this project for almost all of 2017, from analyzing our needs to building the warehouse,” he explains. Moreover, the buildings located around the new warehouse were expanded at the same time, “which required a coordinated effort of more than 170 professionals and the use of 70 TM cranes simultaneously.”
The result is a warehouse integrated with the rest of the plant that, in the words of the project manager, “is set up to store all the products made on the production lines.” In this new construction, space formerly occupied by the old warehouse was allocated to another production line.
The warehouse works around the clock, 24-hours a day, seven days a week. As per García-Montalvo, “Now, we can store the goods from the production lines and, also, supply the dispatch docks faster.”
A customized warehouse
The warehouse, 89' in height, is a rack-supported installation, i.e., a standalone structure where the racks withstand their own weight, the weight of the goods, the side cladding and the roof. The advantage of this solution is it only fills the space available inside Michelin’s industrial complex and provides a 4,590-container capacity.
It comprises five aisles with single-depth racks on each side and automatic operations, which requires minimal human involvement. The conveyors, stacker cranes, transfer cars and pallet lifts send the goods to their allotted locations. The installation fulfills the requirements framed out by Michelin in terms of flows: the stacker cranes are able to move up to 240 containers an hour (120 inputs and 120 outputs).
One of the unique features of this warehouse is that no wooden or plastic pallets are used. Instead, the 43" x 49" x 48" metal containers handle the rubber used to make the tires. These unit loads have metal legs at the bottom instead of standard skids. “Both the racking and the automated handling equipment’s design has been based on our containers’ size and characteristics,” points out García-Montalvo.
Conveyors with chains on them shift the goods at a controlled speed of 66 ft/min. On the other hand, the racks have built-in supports to place the containers in them safely.
The center complies with rigorous safety measures that keep the products in top condition. The warehouse is temperature controlled and kept between 50 °F and 80 °F. Moreover, it has a fire-fighting system, with sprinklers distributed inside the racks, as well as vertical fire doors that, in the event they are activated, keep the warehouse hermetically sealed to prevent the spread of the flames.
Integration: warehouse to manufacturing
The warehouse is divided into two floors: inputs flow through the bottom and outputs through the top. “This layout completely cuts out any interference between the two operations,” notes the project manager.
Incoming goods
The containers arrive from manufacturing stacked, one on top of the other. Operators use forklifts to place them on one of two reception stations that have been installed. Next, a full pallet stacker unstacks the containers and sets them on the chain conveyors without any type of pallet, so that they flow into the warehouse.
The conveyors are in charge of distributing the goods in the corresponding aisle, according to the instructions of the Easy WMS warehouse management system of Mecalux.
Outgoing goods
A double-width transfer car picks up the containers that must leave the warehouse and moves them up to four exit points. Here, full pallet stackers were also enabled, in this case, to stack the containers in vertical pairs, which the workers can then insert into the trucks. García-Montalvo highlights that, in doing so, “we streamline outgoing goods and increase dispatch productivity.”
Controlling goods
Easy WMS of Mecalux is molded to the features of the new Michelin warehouse and set up to provide personalized product management. To this end, “the WMS of Mecalux communicates with BSM, Michelin’s IT system, through an interface. This interface has been developed during trials run in Mecalux’s offices, at our headquarters in Clermont-Ferrand and the Vitoria plant. Overall, the objective is to guarantee that the synchronization of both systems runs smoothly,” mentions García-Montalvo.
For Michelin, it is crucial to control the exact location of all products. This traceability is always possible, thanks to Easy WMS which can fully control product tracking via virtual instructions, and always knows where to find each and every container, and if that container has exited or not.
Antonio J. García-Montalvo - Manager of the automated warehouse project of Michelin in Vitoria
“We chose Mecalux as the provider for our rubber warehouse in Vitoria after considering proposals from five different companies. The choice was due to its experience in building rack-supported warehouses and its high-quality products able to adapt to our metal containers.”
Advantages for Michelin
- Maximum productivity: the automated rack-supported warehouse, integrated with the Michelin production center, works 24 hours a day, 7 days a week.
- Adaptive solution: all the installations have been designed to facilitate storage and the handling of Michelin’s 43'' x 49" x 48" metal containers.
- Turnkey warehouse: besides the racking system, Mecalux has provided all safety measures, as well as the refrigeration and fire-fighting systems.
Automated warehouse of Michelin | |
---|---|
Storage capacity: | 4,590 containers |
Container dimensions: | 43'' x 49" x 48" |
Max. container weight: | 1,874 lb |
Warehouse height: | 89' |
Racking length: | 125' |
Gallery
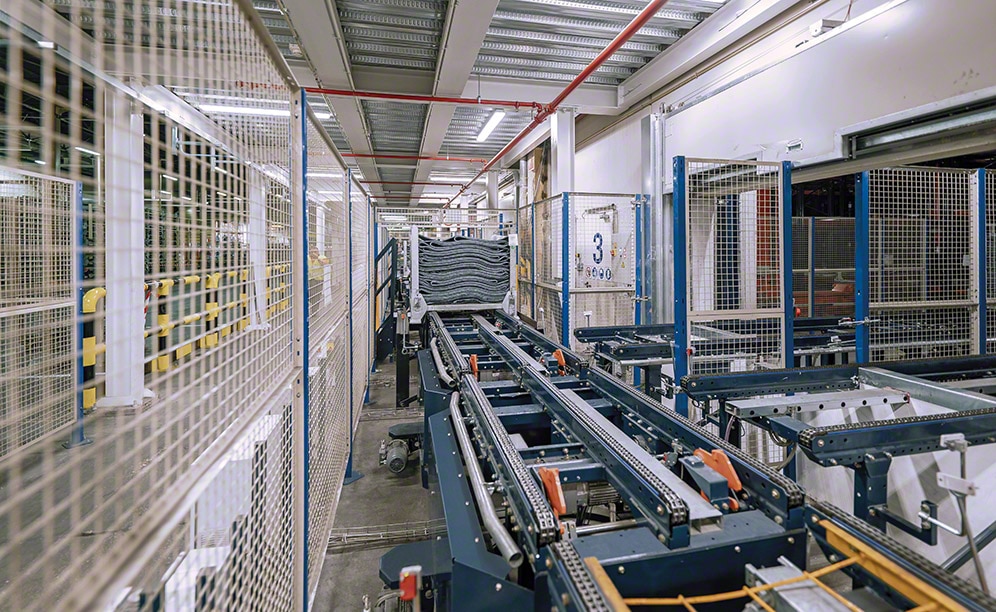
Chain conveyors adapted to the metal containers' measurements
Ask an expert