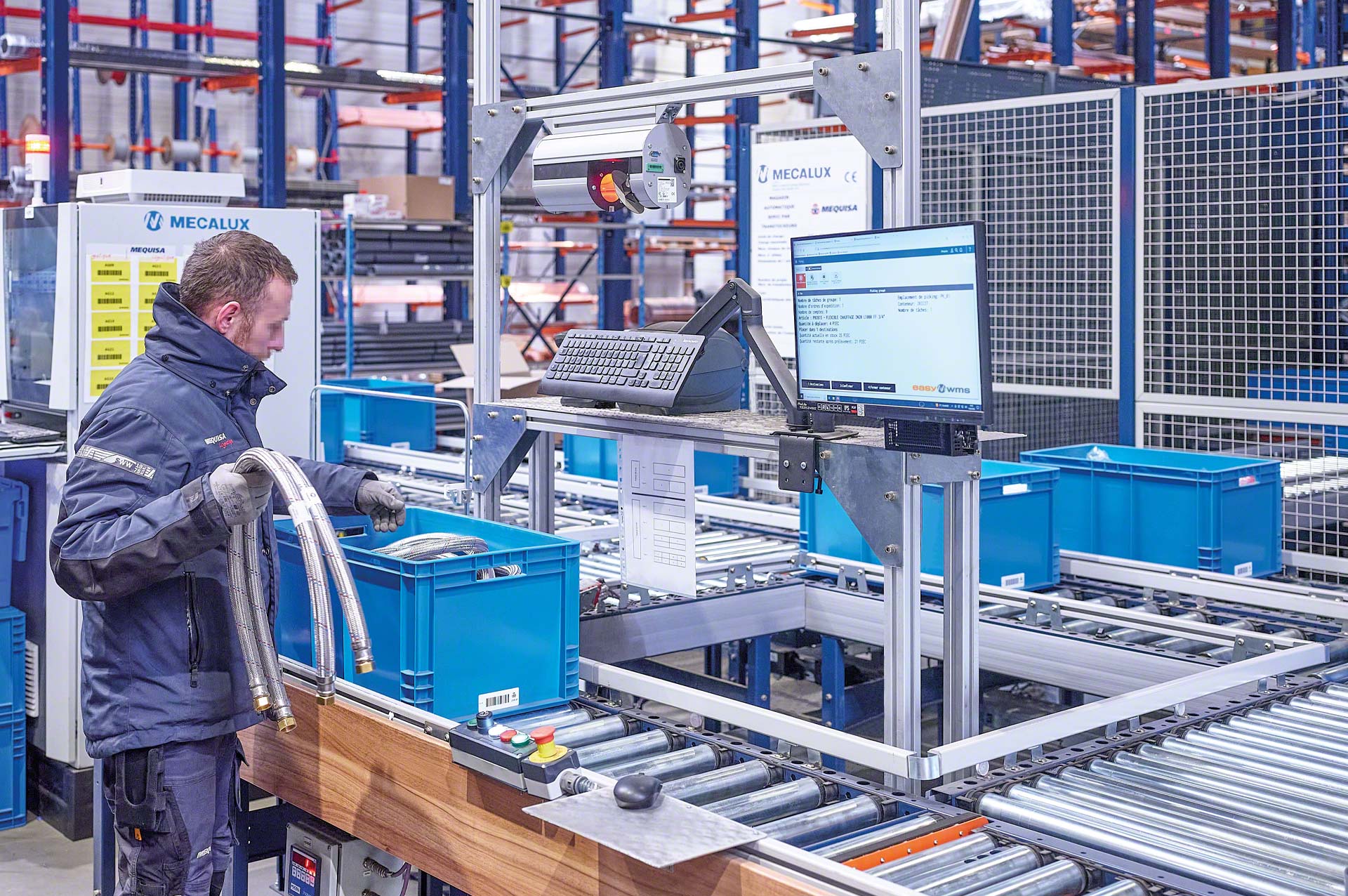
MEQUISA automates the storage of small items
MEQUISA, a wholesaler of bathrooms, flooring, HVAC, and electrical solutions, modernizes its logistics operations.
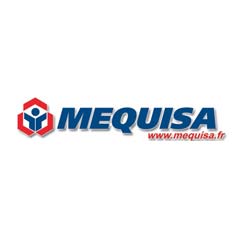
MEQUISA, a wholesaler specializing in bathrooms, flooring, HVAC, and electrical solutions, has installed a mini-load system in France. The facility is also equipped with pallet, carton-flow, and cantilever racks to store MEQUISA’s wide range of products.
MEQUISA: bathrooms, flooring, HVAC, and electrical
MEQUISA is a wholesaler specializing in four divisions: bathrooms, flooring, HVAC, and electrical. The company markets a wide variety of SKUs, such as lamps, faucets, showers, bathtubs, radiators, boilers, photovoltaic panels, light bulbs, and tools, among others.
- Founded in: 1934
- No. of employees: 210
- Points of sale: 11
- Showrooms: 10
CHALLENGES
|
SOLUTIONS
|
BENEFITS
|
---|
MEQUISA is a wholesaler specializing in bathroom solutions, including flooring; electrical; and heating, ventilation, and air conditioning (HVAC). It set out to optimize logistics operations in its facility in Metz (France), with a special emphasis on fine-tuning inventory management and order picking.
In the past, the company stored its small products on multi-tier shelving and its larger items on pallet racks. Over time, MEQUISA’s supply chain became overwhelmed by the increase in activity. This motivated the company to launch a modernization and expansion project with the help of Mecalux.
MEQUISA’s new warehouse had to be automated for several reasons: to scale up throughput, optimize the storage capacity of small items, and improve working conditions for operators in order picking.
To replace the multi-tier shelving, Mecalux installed a mini-load system. This automated storage and retrieval system (AS/RS) for boxes boosts goods receipt and order picking through the nonstop flow enabled by the handling equipment and two pick stations. “Undoubtedly, investing in a mini-load is a guarantee for improving and optimizing customer service,” says José Esteves, CEO of MEQUISA.
Easy WMS, the warehouse management system from Mecalux, supervises all operations in the AS/RS for boxes. The program serves a dual function: to update inventory in real time and guide operators in order picking.
With various storage systems under one roof, the company can distribute goods based on their characteristics and turnover. Thus, for example, smaller and high-turnover products are placed in the mini-load system to streamline their entries and exits. Larger merchandise, meanwhile, is stored on pallet racks.
Automatic throughput in a minimal space
“With Mecalux’s AS/RS for boxes, we’ve considerably cut order picking times. Operators no longer have to travel from floor to floor in our center, which accounted for more than 40% of their working day. We’ve allocated the time saved to tightening quality control during the goods receipt and dispatch processes,” says Esteves.
The mini-load system consists of a single 148-foot-long aisle with double-deep racking on both sides. In just 2,153 ft² of floor space, MEQUISA can store 7,000 SKUs and up to 7,412 boxes.
A stacker crane equipped with telescopic forks handles up to four totes simultaneously to streamline their storage and retrieval in the racking. The AS/RS was designed in line with MEQUISA’s growth prospects. Therefore, when the company needs to double its productivity, another storage aisle can be set up without halting the facility’s operation.
Two pick stations have been installed in front of the mini-load system. There, workers prepare up to 30 orders at a time according to the goods-to-person method. These operators remain at their workstations as the products are brought to them. They then sort the items in the carton flow racks located behind them. This storage system stands 7.2’ tall and is made up of slightly inclined roller platforms. Hence, once an order is closed, it slides by gravity to the dispatch area on the opposite side.
Integrated into the carton flow racks, put-to-light displays guide operators to improve their performance as they sort goods and put together orders, ensuring ergonomic, accurate, and reliable picking.
MEQUISA’s put-to-light system is connected to the Easy WMS warehouse management software. Via the put-to-light displays, Easy WMS shows the operators which box to deposit the products in and the exact number of units required. The program strictly controls the goods thanks to its permanent two-way connection with MEQUISA’s AS400 ERP system.
Easy WMS organizes the stock and decides on a location for each item using rules and algorithms that take into account their characteristics and demand level. The distribution of the products is designed to optimize the movements of the stacker crane while maintaining the flow of goods that MEQUISA requires.
“The automation and put-to-light system, directed by Easy WMS, have raised the quality of order picking, minimizing errors due to manual management,” says Esteves.
Advantages of put-to-light systems
- Productivity. They cut down on operator travel and eliminate the need to read barcodes.
- Error reduction. Product verification is immediate, with an order accuracy rate of over 99.5%.
- Real-time updating. These systems update inventory information instantly by transmitting stock movements to the software, which records them in the database.
- User-friendliness. This order picking technology is very intuitive and easy to use, requiring no prior training.
Storage of bulky products
The AS/RS is complemented with a storage area reserved for palletized products with a capacity for 6,432 pallets containing ceramic tiles. MEQUISA chose selective pallet racks because of their versatility, as they can be adapted to different unit load sizes.
Pallet racks also offer direct access to products. This makes goods management extremely agile and fosters strict product control, as each location is assigned to a specific SKU.
In most of the lower racking levels, operators pick directly from pallets. Safety stock and shipping materials (e.g., cardboard boxes) are placed on the upper storage levels.
Integrated logistics solution
The AS/RS for boxes is a major step forward for MEQUISA: in addition to housing 7,000 SKUs in a limited space of 2,153 ft², it has boosted productivity in order picking. The system is prepared to drive the company’s growth in the years to come: MEQUISA will have the option to install another stacker crane to double its warehouse throughput.
The digitalization enabled by the Easy WMS software provides rigorous control of the goods and sends instructions to operators on how to fulfill orders more quickly. The combination of an AS/RS, carton flow racks, and Easy WMS has streamlined the simultaneous preparation of multiple orders, greatly reducing the likelihood of errors. MEQUISA’s end goal? To offer its customers quality service.
The mini-load AS/RS helps us cut the time needed to fill orders. The automation and put-to-light system, directed by Easy WMS, have raised the quality of order picking, minimizing errors due to manual management. Undoubtedly, investing in an AS/RS for boxes is a guarantee for improving and optimizing customer service.
Gallery

MEQUISA automates its facility in Metz, France
Ask an expert