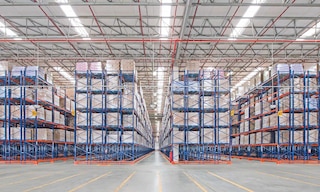
Double-deep pallet racking optimizes storage space
Double-deep racking is a configuration of selective pallet racking. It’s ideal for warehouses that manage products with several pallets per SKU.
What is double-deep pallet racking?
Double-deep racking is a storage system that accommodates two pallets or boxes in each location, one behind the other. It consists of two frames that make it easier to store more items compared to single-depth racks.
This type of racking offers direct access to products on the same side of the aisle. To reach the second storage unit, it’s necessary to remove the first one beforehand.
These racks can house products with various characteristics and measurements. They’re also very useful for picking, whether from boxes, directly from pallets, or from loose units placed on shelves.
How does double-deep pallet racking work?
Double-deep racking can be installed in manual and automated warehouses. In both cases, they require handling equipment with telescopic forks or a scissor or pantograph system that can reach the items in the second depth.
Single- and double-deep pallet racking often coexist in the same facility. The former are used for products with a higher turnover (type A) and the latter for those with lower consumption (types B and C).
What are the components of double-deep racking?
Double-deep pallet racking is made up of components that ensure the proper storage of goods. They have accessories to adapt them to a wide variety of uses and products. The basic fastening elements are:
- Frames. These serve as the racks’ vertical support. They comprise two vertical posts joined together by diagonals and crossbars.
- Frame connectors. These components join two racks together, giving greater transverse stability to the assembly.
- Shims and anchors. These secure the racks to the floor and serve to correct slightly uneven surfaces.
- Beams. These horizontal members are joined to the frames using connectors or clips fixed at their ends. They can either hold goods directly or support shelves for product storage.
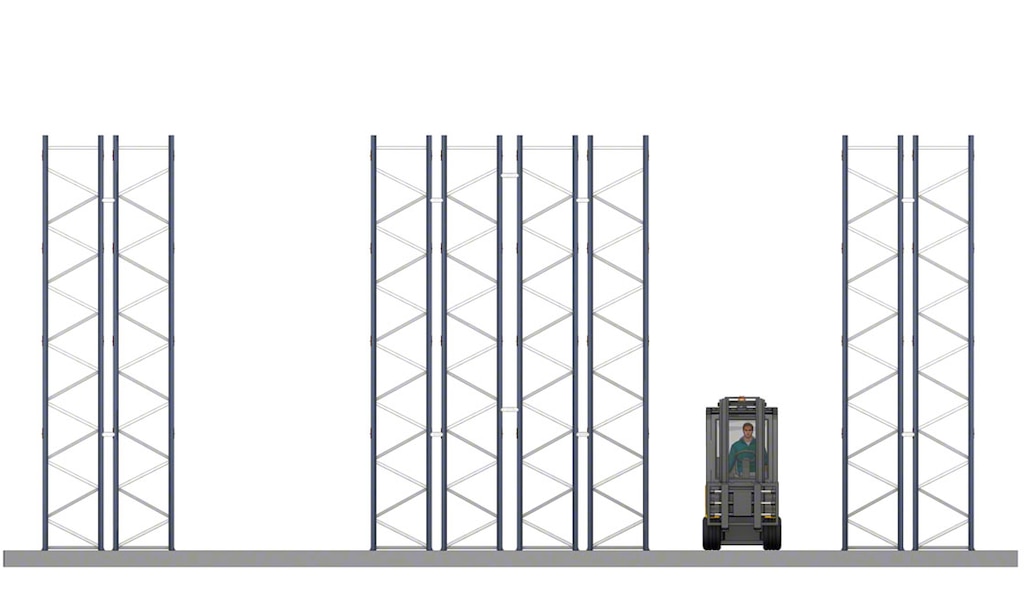
What are the pros and cons of using double-deep racks in warehouses?
Pallet racking is one of the most widely used storage solutions due to its simplicity, versatility, and ease of assembly. Double-deep racking has the following advantages:
- Greater storage capacity. It’s an ideal system for products with several pallets or boxes per SKU.
- Space optimization. It allows for storing more items in the same surface area compared to single-depth pallet racking.
- Quick access to goods. The system provides direct access to the SKUs located in the aisle, facilitating better stock turnover.
- Suitable for picking. This racking enables picking on the lower levels. It can also be done at higher locations using order pickers.
However, double-deep pallet racking has one disadvantage: Since the products are stored one behind the other, the one in front must be removed to access the second one. Businesses need to organize their goods, anticipating the number of pallets or boxes for each SKU. The items in each location should be of the same SKU.
A warehouse management system such as Interlake Mecalux’s Easy WMS organizes goods strategically. The software considers SKU turnover and quantity when distributing products on the racks.
Examples of warehouses that use double-deep racking systems
Companies from all sectors install double-deep pallet racking in their logistics facilities to improve efficiency and better manage their products:
- Unilever. The consumer goods manufacturer equipped its warehouses in Brazil and Uruguay with double-deep pallet racking from Mecalux, with a total storage capacity of 100,000 pallets. The multinational chose this solution because it provides large a storage capacity while maintaining direct access to the pallets. The business uses them to store multiple SKUs of food, drinks, and household and personal care items from well-known brands such as Axe, Dove, Hellmann’s, and Knorr.
- Agata. In Poland, the logistics facility of this furniture distributor can accommodate more than 50,000 pallets in single- and double-deep racks. “Setting up double-deep pallet racking means we can really leverage every square foot of storage space. And we’ve cut costs compared to what we would have spent to build a new warehouse,” says Marek Skiba, Logistics Director at Agata.
- Special Dog. The automated warehouse of this Brazilian pet food company consists of two 282-foot-long aisles with 88.5-foot-high double-deep pallet racking on both sides. Stacker cranes (AS/RS for pallets) are equipped with telescopic forks that facilitate access to the second position on the levels. With a total surface area of 13,993 ft², the Special Dog warehouse offers a capacity of more than 6,000 pallets.
- Continental. In Mexico, the automated storage and retrieval system (AS/RS) for boxes run by the multinational tire company is made up of double-deep pallet racking that houses spare parts and electronic car accessories. Continental’s mini-load system makes the most of the available surface area to achieve a storage capacity of 3,460 boxes. In addition, through automation, the business guarantees a high flow of entries and exits, boosting order processing.
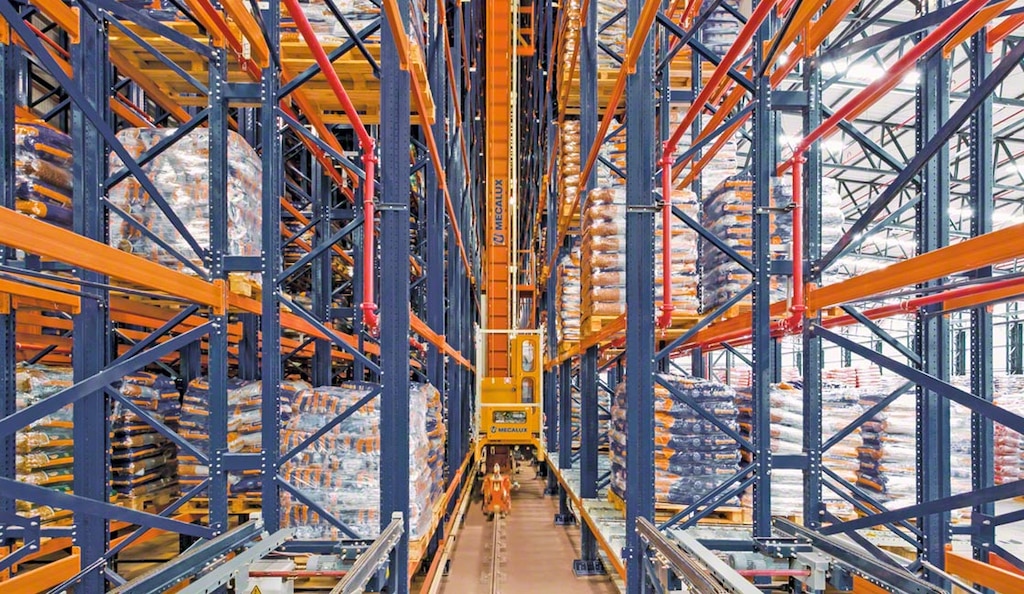
Double-deep pallet racking: Maximum capacity
Double-deep pallet racking is an efficient solution for optimizing storage capacity. It combines advantages such as direct access with maximized use of available space. This system is especially suitable for companies that handle large volumes of products, allowing more items to be stored in a reduced area and facilitating operations such as picking.
At Interlake Mecalux, we have experience designing and installing double-deep pallet racking for organizations around the world. Are you looking to expand your facility’s storage capacity while streamlining operations? Contact us and we’ll find the best solution for you.