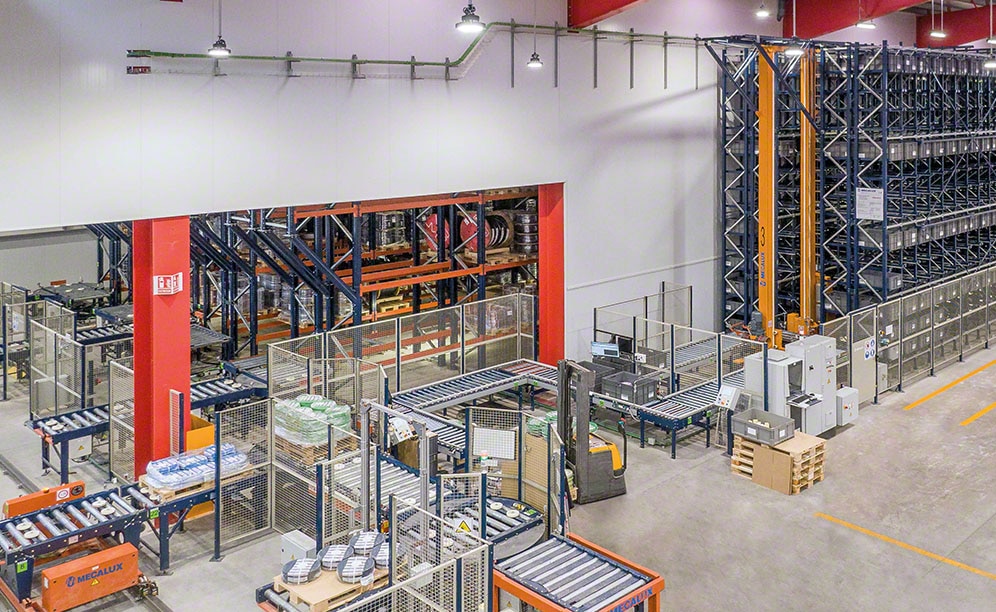
Miguélez: Latest-generation technology for the supply of electric cables
Miguélez's new logistics center stores 38,500 tons of cable manufactured every year
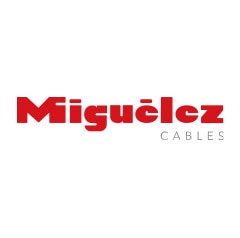
Miguélez, a worldwide leader in the manufacture of low- and medium-voltage electric cables, has equipped its new logistics center in north-western Spain with the latest technological advances. Its objective is to improve control, centralize operations and broaden its horizons. Through itspartnership with Interlake Mecalux, the company has installed two automated storage systems and pallet racking to accommodate the more than 38,500 tons of cable it produces every year. Easy WMS, the warehouse management system by Mecalux, is charged with the simultaneous and combined management of all processes carried out at Miguélez’s installation: receipt, cutting, storage, order prep, packaging, and distribution to its international markets.
Miguélez: just-in-time
Miguélez is a Spanish company that has become a global benchmark in the manufacture of low-voltage electrical cables. Since its inception, the firm has continuously invested in improving its processes, incorporating the most advanced equipment on the market when manufacturing its products. Miguélez’s cables are used in numerous types of structures and settings: airports, shipyards, underground lines, sports stadiums, tunnels, hospitals, shopping centers, etc.
The company currently has a 16 acre modern factory in the north-west of Spain, as well as 14 logistics centers throughout the world equipped with cutting-edge technology. The various distribution centers make it possible for Miguélez to supply cable immediately to any point on the planet in less than two hours. This is possible even for exceptional cases, as occurred in Spain during the installation of field hospitals in the fight against Covid-19.
The internationalization process undertaken by the company in recent years posed the following challenge: how can we provide efficient service to our customers located in such remote and disparate markets?
Construction of a new warehouse
To respond to this question, Miguélez decided to contact a specialist that could help it update both its logistics and warehouse operations, adapting the new needs to the requirements and functionalities.
Previously, Miguélez used various sites to store the more than 38,500 tons of cable it manufactures every year. With the aim of freeing up space to increase the production lines, the company decided to build a 7.91 acre modern logistics center 9 miles from the production plant. It has moved its cutting lines and its storage, packaging and distribution operations — all formerly housed in the factory — to this new facility. In addition to gaining storage space, Miguélez has centralized the management of the more than 1,500 SKUs that make up its catalog under the same roof.
To drive this project forward, the firm has relied on Interlake Mecalux’s automated storage solutions and Easy WMS, its warehouse management system. Interlake Mecalux has installed pallet racking and two automated warehouses, (one for boxes and another for pallets), which store the various types of products: drums, spools and reels. Easy WMS supervises the entire gamut of operations, including automated and manual goods storage, cutting tasks, and product receipt and dispatch.
According to Jorge Miguélez, CEO of Miguélez, “we decided to go with Interlake Mecalux’s storage and management solutions because the company understood the particular characteristics of a product with such diverse packaging and varieties, ranging from 150 grams to 5.5 tons.”
Clear commitment to automation
The automated warehouse for pallets stands 74.1 feet tall. It comprises two 222.4-foot long storage aisles with double-deep racking on both sides. With a capacity of 6,504 pallets, this installation manages full pallets with goods manufactured at the production plant.
For its part, the 27.2-foot tall automated warehouse for boxes stores up to 3,876 boxes containing small cable reels. The installation has a 161-foot long aisle in which a miniload stacker crane circulates.
In each warehouse, conveyors have been set up on each end of the racking. They handle goods entries and exits, streamlining and dividing the workflows. The rear parts of the installations are used for goods entries, while the front sections are designed for order prep and shipping. In the dispatch area, three flow channels with a capacity of eight pallets each have been set up. The pallets remain there, waiting to be sent to the consolidation zone or directly to the loading docks.
Automation has given Miguélez a host of advantages, primarily, increased productivity and availability, as it can operate at maximum throughput 24 hours a day. With a project of such magnitude it is essential to carry out a strict control of the goods, as well as of the various drums around which the cable is wound. Easy WMS by Interlake Mecalux plays a crucial role in the goods receipt, cutting, storage, picking and dispatch tasks.
Miguel Ángel Tascón, Head of Sales at Miguélez, affirms, “We are extremely satisfied with the automation Interlake Mecalux has given us. It has allowed us to stay true to our DNA: customer proximity, providing support as an auxiliary warehouse and guaranteeing express service.”
Error-free, from production to receipt
The goods are transported from Miguélez’s factory in north-west Spain to its warehouse by truck. When a truck leaves the production center, the SAP ERP at Miguélez — which is in constant communication with Easy WMS — notifies the WMS (via the Advanced Shipment Notice (ASN) process) of the arrival of a truck containing products ready to be stored.
Once the truck parks in the docking area, Easy WMS springs into action to manage the receipt of the goods. First, the workers identify each pallet using radiofrequency (RF) terminals. This ensures that the goods previously designated by the ERP match those actually brought by the truck.
After scanning each item, the system decides where to place each pallet based on the type of product it contains. There are three possible destinations: racks for drums, pallet racks or the automated warehouse for pallets.
Both the racks for drums and for pallets are used to store goods that, for the most part, will be processed in the cutting area. These items are stored manually with the help of pallet trucks.
Meanwhile, in the automated installation, pallets have to go through a checkpoint, where their sizes are verified. If the measurements fall within the corresponding ranges, Easy WMS directs the stacker cranes to place the pallets in their assigned locations.
Three types of picking
At Miguélez, Easy WMS supervises the simultaneous and combined management of three types of order preparation.
According to Logistics Manager Alberto Lombo, “installing Easy WMS has helped us to improve order prep because locations containing incomplete pallets can be managed efficiently and in conjunction with the automated warehouse for boxes. Plus, the system’s intelligence lets you minimize the number of movements, optimizing operations and saving time.”
Picking in the automated installations
Both the automated warehouse for pallets and the automated installation for boxes have their own pick stations. The two stations face each other and are located just in front of the automated warehouse for boxes.
Easy WMS organises the orders, which can include products in the automated installation for pallets, the automated warehouse for boxes, or both. The pick stations are equipped with screens that display all the information related to each order and help operators carry out their tasks. For example, the screen specifies the number of items to be removed from each pallet and the order in which they should be placed.
The process begins in the automated installation for pallets. The pallets leave the warehouse and are transported to the pick station by a transfer car. Once there, the operators extract the products needed to complete each order. If the original pallet is left with few goods, they are stored in boxes. This frees up space in the automated installation for a full pallet. The remaining products are stored in boxes and are used to fulfill future orders.
For every picking task carried out, Easy WMS sends a personalized message to the SAP ERP, reporting on the characteristics of each order: products included, quantity, origin, etc. Once the order is closed, Easy WMS prints a label that provides access to all these data when scanned with a barcode reader.
Cut-cable picking
Easy WMS is also charged with overseeing the process of cutting cable. It consists of carrying the drums stored on the racks to the cable-cutting stations. There are four machines capable of cutting cable from two reels at the same time.
Via RF terminals, the WMS communicates with the operators, telling them which drums they need for this process: the source reel (with the cable) and the destination reel (to be delivered to the customer with the specified cable diameter and length). Easy WMS also shows operators the amount of cable to cut so that they can configure this in the machine.
At this point, the machine begins to rotate, feeding the cable from the source drum to the destination reel. The machine is fitted with a rotary encoder that counts the feet of cable wound onto the destination reel, thereby cutting the precise amount required.
Pallet-rack picking
Operators, also aided by RF terminals, pick items directly off the pallets located on the lower levels of the racking.
Some orders include complete pallets that do not need to be broken down. Before being moved to the consolidation area, Easy WMS checks whether the reel containing the cable matches the one requested by the customer. If it does, it is brought directly to the consolidation zone. If it does not, the reel is changed at one of the cutting stations.
Goods dispatch
All picked orders (full pallets as well as pallets with goods picked from the automated warehouses, pallet racks and cutting machines) are moved to the consolidation area. There, they are grouped on the floor, waiting to be moved to the loading docks.
Using RF terminals, the operators verify that no mistakes have been made during order prep. Once this process has finished, the parcels are sent to the corresponding dock following the sequence defined by Easy WMS.
Finally, Easy WMS creates an order for the trucks to be loaded by license plate. This way, operators can make sure they are loading the goods onto the right truck.
A modern, innovative logistics center
Miguélez boasts a high-tech logistics facility that enables it to grow by leaps and bounds and achieve maximum efficiency in its supply chain. In just one year, the company has significantly increased its turnover compared to the previous year.
The two automated warehouses have made the flow of drums, reels and spools both smooth and safe. The most significant progress made by the firm can be seen in storage capacity and, especially, order preparation. Following instructions from Easy WMS, order delivery is much speedier in addition to error-free.
Jorge Miguélez - CEO of Miguélez
“We chose Mecalux’s storage solutions and WMS because the company understood the particular features of our product. We work with extremely diverse packaging and product forms, with weights ranging from 150 grams to 5.5 tons.”
Advantages for Miguélez
- Three picking methods: Easy WMS simultaneously manages orders containing goods from the automated warehouses, pallet racks and cable-cutting stations.
- Inventory control: the WMS makes it possible to know, at all times, what is in stock, where it came from, where it is located and where it is headed.
- High productivity and efficiency: the automation of operations enables quick service with on-time, error-free deliveries.
Automated warehouse for pallets | |
---|---|
Storage capacity: | 6,504 pallets |
Pallet size: | 32" x 47" |
Max. pallet weight: | 1.32 t |
Racking height: | 74.1' |
Racking length: | 222.4' |
Gallery
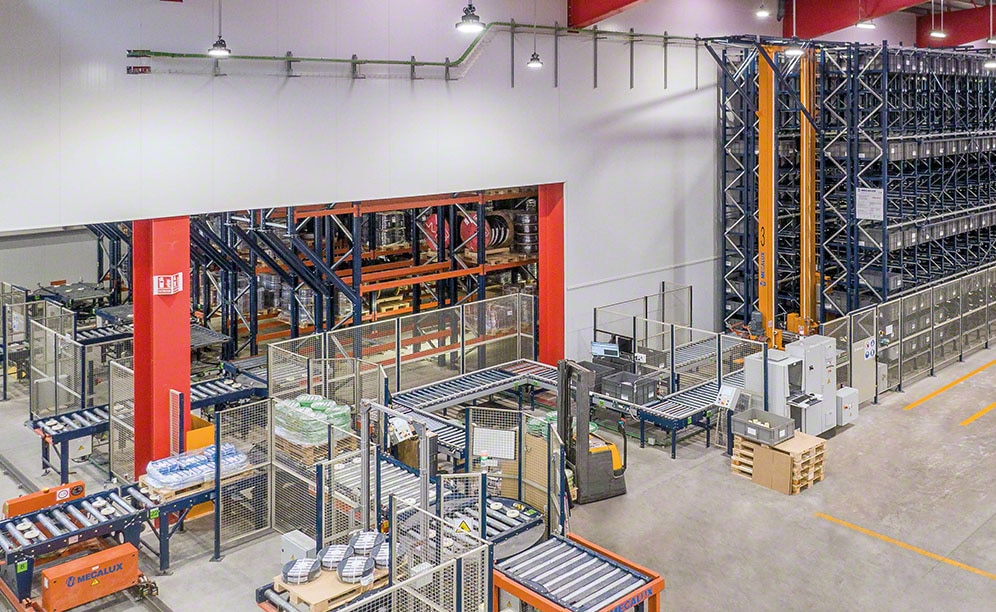
Automated warehouses to manage Miguélez's electric cables
Ask an expert