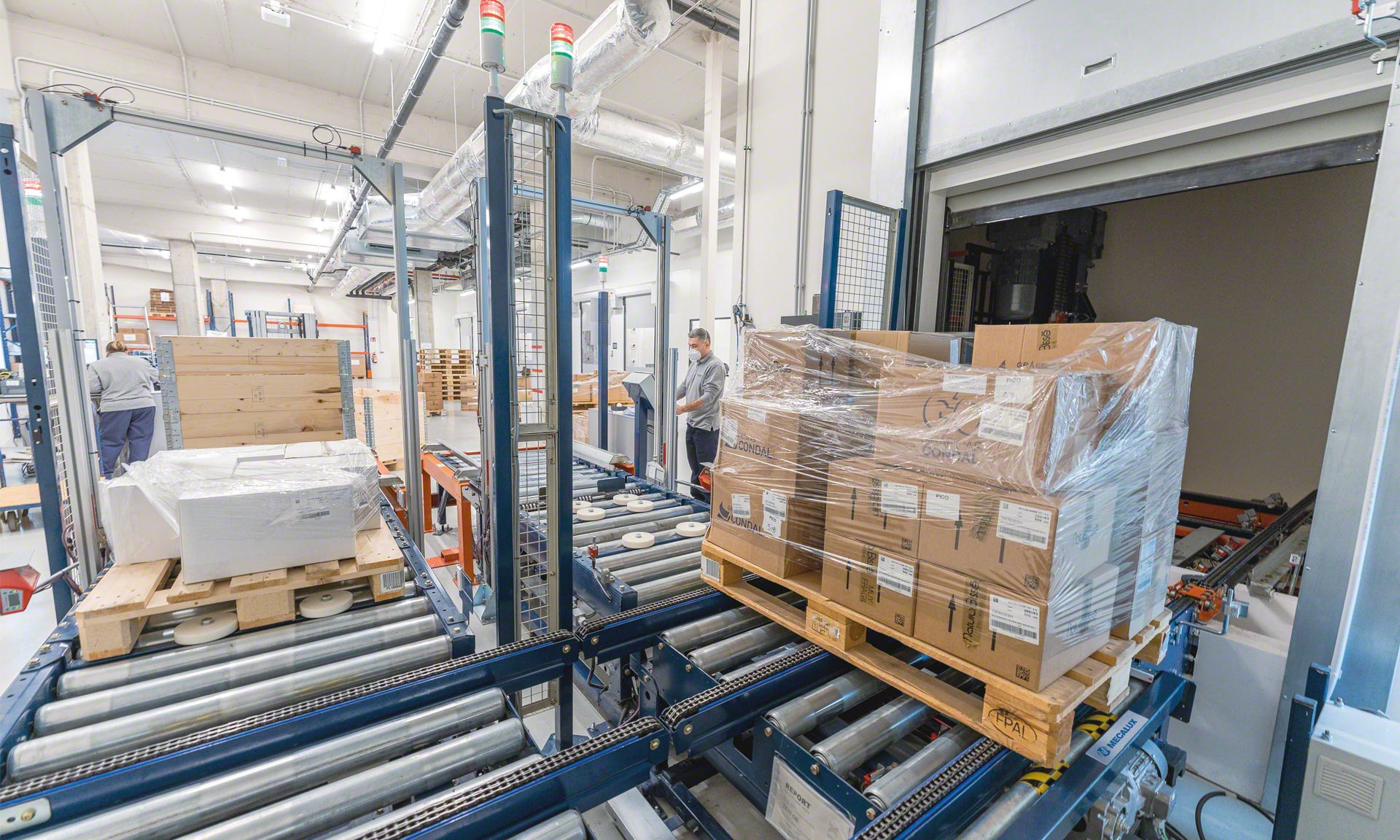
Natura Bissé: an automated warehouse for beautifying logistics
The automated warehouse was built in a 26-foot-deep pit adjusted to Natura Bissé's building
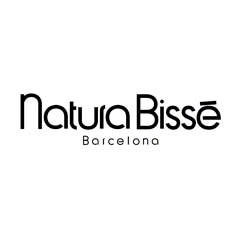
Cosmetics firm Natura Bissé has opened a new, completely personalized automated warehouse in Barcelona, Spain, where it has centralized all its goods previously outsourced to a logistics provider. Formed by merely two aisles storing 2,200 SKUs, this facility connected with production has been built in an 86-foot-deep pit. Mecalux has also implemented its Easy WMS warehouse management system to control product traceability in real time.
Global presence and acclaim
Since it was founded in 1979, cosmetics company Natura Bissé has been in a constant state of change and expansion. With its headquarters in Cerdanyola del Vallès (Barcelona) and subsidiaries in the UK, the US, Mexico and China, it has become a leading manufacturer of cosmetics for all skin types. A total of 87% of its revenue comes from international markets, where it boasts more than 2,500 sales outlets.
Its production processes are continuously updated, and its desire to discover new treatments compels it to consistently incorporate the latest technologies. Additionally, with the cooperation of specialists from other sectors such as the nutrition, aesthetic medicine and food industries, it develops formulas that can deliver better cosmetics results. As a result of its work, Natura Bissé has received the World’s Best Spa honor from the World Spa Awards for the third consecutive year.
Committed to society, Natura Bissé donated 19,500 single-dose hand creams and over 5,000 nourishing balms to healthcare workers treating people affected by the COVID-19 pandemic.
Logistics in flux
According to Pilar López, Industrial Director at Natura Bissé, “Our logistics systems have evolved as our business has grown.” In recent years, the company has strengthened its international presence, mainly in the US, China and Korea. This has forced it to readjust its operations in order to supply all its customers.
“Initially, we had outsourced our storage services, for both raw materials and several finished products, to a logistics provider. The downside was that we received goods at our logistics facility once a day, which prevented us from making changes to production planning with less than 48 hours’ notice,” explains Pilar López.
Determined to resolve this issue, in 2019, Natura Bissé relocated its corporate headquarters to a larger, modern building in Cerdanyola del Vallès (12 miles from Barcelona), increasing its surface area from 32,000 ft2 to 145,000 ft2. This space houses the production lines, laboratory, offices, training rooms and a storage area for components and products.
One of its priorities was to have in its facility all the items that used to be managed by a logistics provider. Another goal consisted of connecting the warehouse with production. Additionally, the firm wanted to have stricter control over the stages the cosmetics undergo and to monitor its 2,200 SKUs (finished products and packaging items).
A tailor-made automated warehouse
Natura Bissé contacted Mecalux to come up with the solution that would best satisfy its logistics needs. “We sought its advice after receiving good references from other companies that had also modernized their logistics facilities with Mecalux. It was a plus that they, like us, were located in Barcelona; this would make working together easier,” says the Industrial Director.
The solution for addressing all these particular stipulations was to install storage systems and handling equipment that would manage the products automatically. In the words of Pilar López, “Automation has meant reduced logistics costs and more flexible production.”
Along these lines, Mecalux has built an automated warehouse for pallets consisting of two 230-foot-long aisles with single-deep racking on each side. “It meets our requirements to a T. To begin with, work on the warehouse started once the building structure was already completed, so it had to adapt to the existing space just below the production area,” notes Natura Bissé’s Industrial Director.
To gain in capacity, Mecalux dug an 26-foot-deep pit where it set up taller 39-foot racking. These racks occupy all of the area’s useful space, with entry and exit points and conveyors placed strategically alongside them. The objective was clear: “We wanted to make the most of the limited space we had to obtain the largest number of locations possible,” emphasizes Pilar López.
In total, the warehouse stores 2,267 pallets with a 2,200 lb maximum unit weight. The racks, which have eight levels, were devised taking into account that Natura Bissé manages pallets of three different height levels: 30”, 43” and 59”. Thus, for example, the lower levels have been designed to hold smaller goods, while the upper levels accommodate taller items.
Warehouse characteristics
- Facility installed in an 26-foot-deep pit. The space limitations meant the warehouse had to be adapted down to the inch to achieve the required storage capacity.
- Production plant located above the warehouse. A pallet lift automatically and bidirectionally connects the warehouse with the production area.
- Reversible access points. All inbound and outbound goods access points in the automated warehouse are reversible. That is, they can fulfill whatever function is required at any given time: entries only, exits only, one entry and one exit, etc.
- Connection between aisles. The facility is equipped with a pallet transfer zone between both aisles as opposed to an inflow/outflow area in the front of the warehouse providing direct access to the two aisles. With this layout, the company has increased its storage capacity at the cost of reduced agility in the flow of goods.
Operations in the automated warehouse
One of the aisles is reserved for finished products, while the other stores packaging components. In each aisle, a stacker crane automatically inserts and removes goods into/from their locations as per instructions from Mecalux’s Easy WMS warehouse management system. Both aisles are interconnected by means of two lines of conveyors that transfer the goods.
The loading docks are located just next to the aisle for finished products to streamline the distribution of the goods. These docks also receive pallets sent by suppliers containing the components used in the production processes. All of them must go through a checkpoint where their sizes are checked. They are then sent to the components aisle via the transfer area.
At one end of the components aisle is a lift that links the warehouse with the production lines. It is tasked with sending the parts to production (on the upper floor) and the finished cosmetics to the warehouse. As finished products are not stored in this aisle, they must change aisles via the transfer conveyors.
A facility under control
Considering the wide variety of SKUs and number of goods movements, Mecalux has implemented the Easy WMS warehouse management system. “It’s made our storage processes more efficient, which has helped to enhance our operations,” explains Pilar López.
The software incorporates rules and algorithms to organize the goods based on their particular characteristics (whether they are finished products or components) and demand level. The aisles are divided into three sections according to product turnover: type A, B or C. Thus, for example, type A items (higher demand level) are placed at the ends of the aisles to streamline entries and exits. This enables Natura Bissé to control the traceability of all its products in real time.
To improve goods management, the WMS communicates with the Ekon ERP at Natura Bissé. “The process to integrate the two systems was very well documented, and we were given proper support,” notes the Industrial Director. The ERP notifies Easy WMS in advance of the items scheduled to arrive at the facility. The WMS then organizes the locations and, once the products are received, checks that no mistakes have been made.
Now, all our stock is in our new automated warehouse connected with production. Thus, the planning of all our operations is more flexible, and we can manufacture our cosmetics without interruption. Plus, by doing away with the subcontracted warehouse, we’ve reduced our logistics costs.
Non-automated storage systems
Mecalux has also installed three non-automated storage systems with different functions:
- Push-back racks. In the docking area, two 11.5-foot-tall push-back racking units have been set up. They have three load levels that provide capacity for 106 pallets ready to be shipped. As these racks are slightly sloped, the pallets can be pushed in. The front part is lower so that, when a pallet is removed, the rear pallets move forward by gravity to the front position.
- Pallet racks. Standing 10 feet tall and with three levels, these racks accommodate 700 pallets. This storage system was chosen for its direct access to the products, which brings great agility to goods management and order preparation. In addition, it facilitates stock control, since each location is assigned to a single SKU. Pilar López affirms, “In these racks, we store high-turnover products near the processes in which they’re going to be used.”
- M7 longspan shelving. These shelves stand 10 feet tall and have six load levels with galvanized panels. This system is reserved for the storage of boxes and small individual products.
Innovation in cosmetics and logistics
Natura Bissé is a forward-thinking company that, from the start, has demonstrated a commitment to change and continuous improvement. The opening of its new corporate headquarters in Barcelona is a testament to the promising future that lies ahead for this firm. “If the coronavirus pandemic has taught us anything, it’s that companies that invest in innovation have been able to navigate this situation better, and we’re not going to be left behind,” asserts Pilar López.
Automation and digitization guide Natura Bissé in achieving all the goals it sets for itself. Technology enables it to closely monitor its products and optimize all its operations. All of this is done with a single purpose in mind: to provide optimal service.
“After the pandemic, solidarity and collaboration will continue to be vital. We believe we need to be agile and flexible while being able to react quickly to continue adding value to society,” states Natura Bissé’s Industrial Director.
Advantages for Natura Bissé
- Space optimization: the warehouse was built in a 26-foot-deep pit adjusted to the sizes of Natura Bissé’s facility. The racks leverage all the available surface area to provide the greatest possible storage capacity, totaling 2,267 pallets.
- Automatic connection with production: a pallet lift ensures the uninterrupted supply of the production lines. Following the manufacturing process, the finished products are sent down to be stored on the shelves.
- Efficient organization: in just two aisles, pallets are distributed according to whether they are finished items or parts.
- Full traceability: Easy WMS monitors the goods, from the time they arrive at the warehouse until the finished products are dispatched to be delivered to customers.
Automated warehouse for pallets | |
---|---|
Storage capacity: | 2,267 pallets |
Pallet sizes: | 32” x 47” |
Racking height: | 39’ |
Racking length: | 230’ |
Gallery
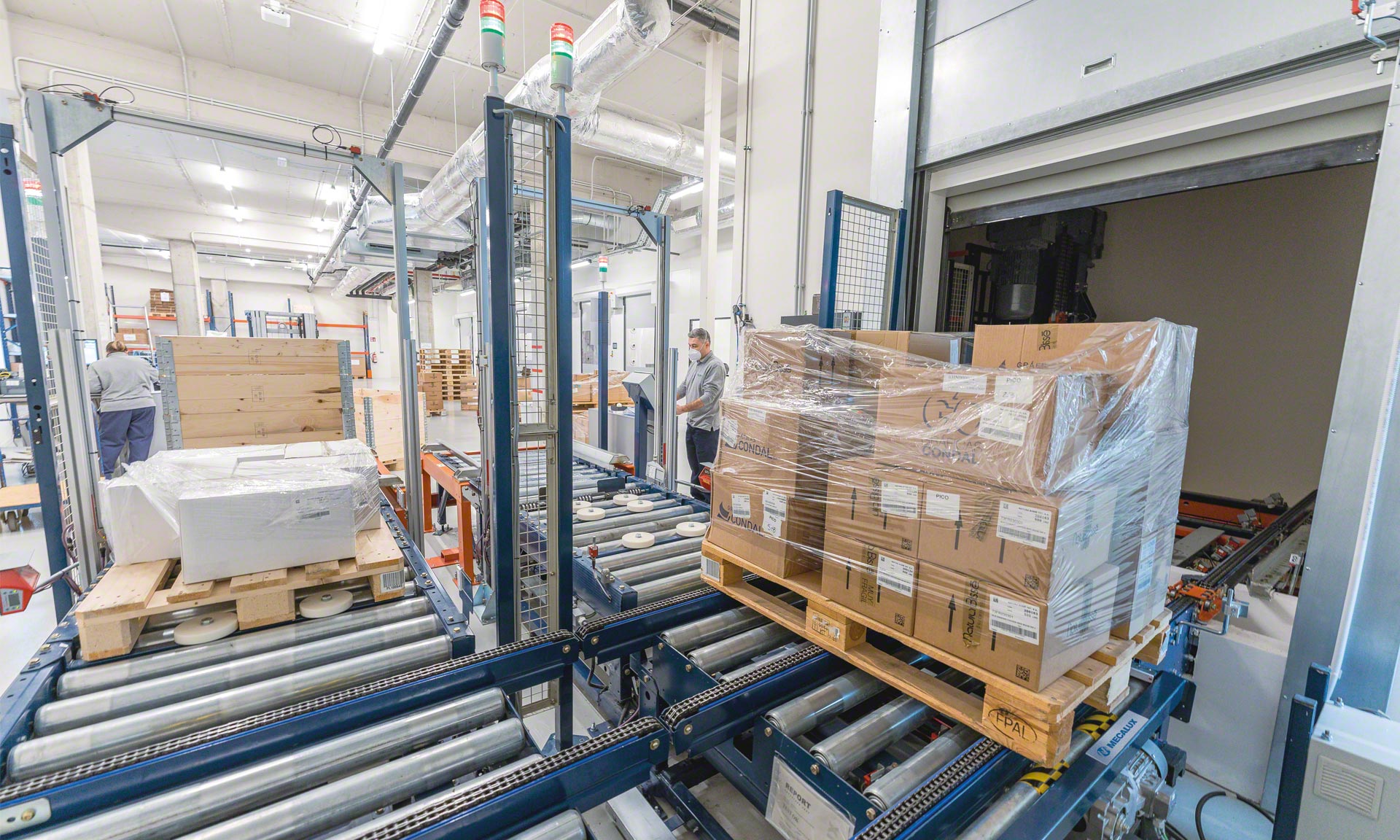
The automated facility manages Natura Bissé's cosmetics products
Ask an expert