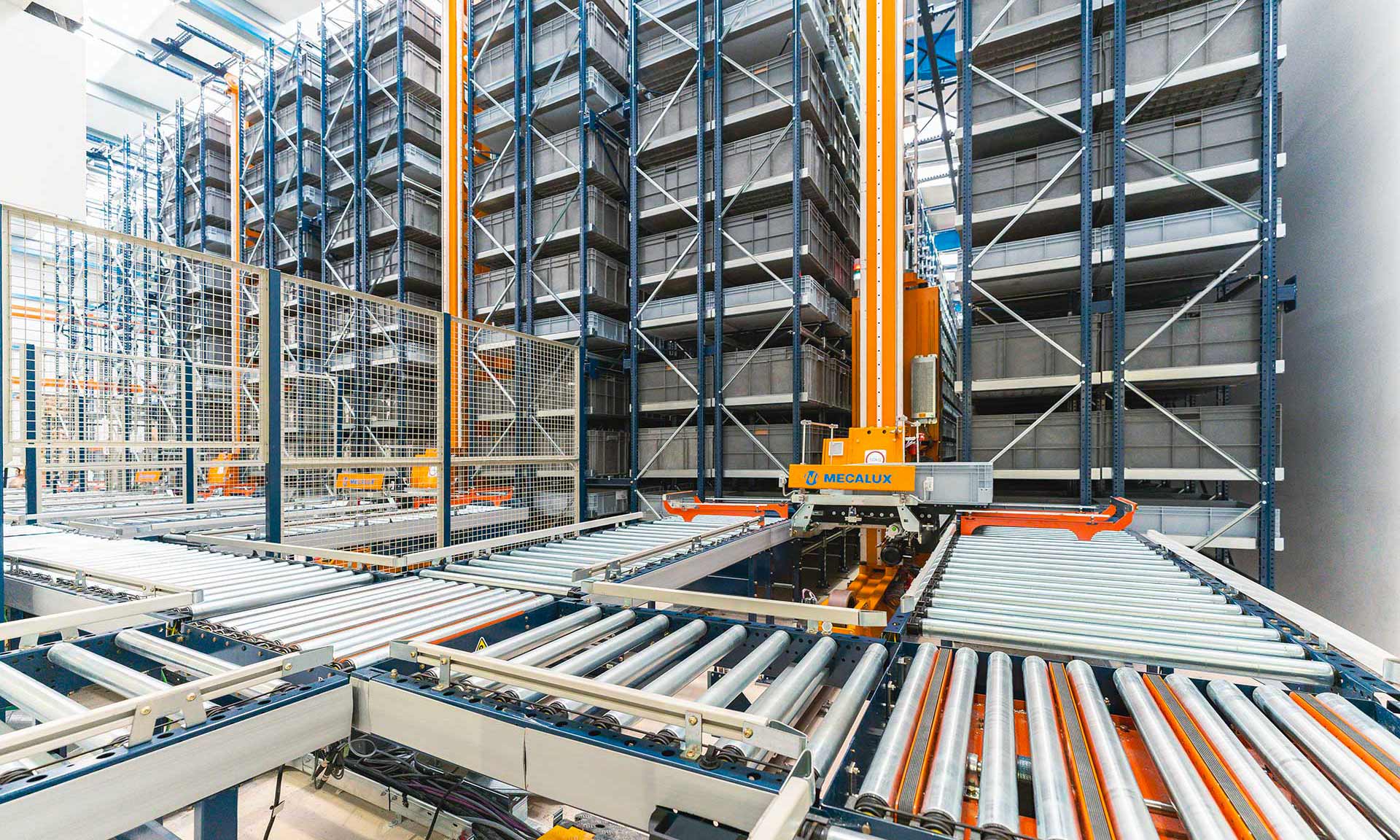
Normagrup: automation shines a light on logistics
Every day, the fully automated miniload system moves 8.75% of the boxes managed
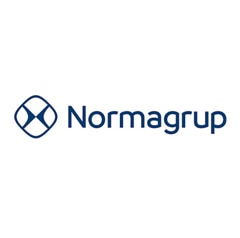
Normagrup, the leading Spanish company in the emergency lighting market, has expanded its production plant in Asturias, Spain, with the installation of an automated system for boxes with approximately 8,000 locations. Managed by Easy WMS from Mecalux, this solution houses the components used to manufacture the products. Its operation is fully automated, and it boasts various autonomous intelligent vehicles (AIVs) that automatically connect the warehouse with the production lines. The center is also equipped with pallet racking and a cantilever rack for managing bulkier goods.
Eager to innovate
Founded in 1971, Normagrup is a Spanish firm that markets technology for businesses in any industrial sector: emergency lighting systems, smoke detectors, hospital equipment, and so on.
At its facility in Asturias, Spain, it manufactures the products of its four divisions: NormaLux (emergency lighting), NormaDet (fire detection), NormaLit (technical and architectural lighting) and NorClinic (hospital bed lighting).
Currently, Normagrup has 170 employees as well as subsidiaries in the UK, France, the Netherlands and Mexico. Present in over 50 countries, the brands of this top market leader in emergency lighting are recognized nationally in Spain, where it enjoys a 42% market share.
Innovation, applied not only to products but also to processes, has been fundamental in fostering Normagrup’s growth. The business incorporates the latest technologies in its operations with the aim of developing products that respond with the utmost efficiency, quality, safety and reliability.
An ever-expanding plant
In 1996, Normagrup built its production plant in the Asturias Technology Park in the town of Llanera. There, it produces and distributes all its merchandise. The center has been expanded numerous times over the years in order to ramp up the production pace and begin manufacturing new product ranges.
This growth has accelerated with the construction of two more warehouses and their subsequent expansion. The result is a large, modern plant measuring just under 7.4 acres. It consists of four buildings outfitted with state of-the-art technology in the fields of electronics, robotics and automated control, thus enhancing production reliability.
One of Normagrup’s most ambitious projects was the commissioning of a 23-foot-tall automated storage and retrieval system (AS/RS) with a capacity for 8,000 boxes. This AS/RS is vital for the development of the other operations in the production plant: storage, dispatch and distribution of the raw materials to the manufacturing area. For this purpose, four autonomous intelligent vehicles (AIVs) have been installed to connect the three production lines.
In the past, the company would place all these boxes containing raw materials on pallets later stored on the pallet racks. However, as this solution consumed a lot of time and resources, it was unable to achieve the production rate that Normagrup required. Aided by forklifts, the operators had to find the pallets they needed, remove them from their locations, pick the boxes and bring them to the corresponding production lines. One Normagrup representative explains, “Faced with an increasingly frenetic production pace, we needed to effectively optimize and organize the management of these goods.”
The firm came to the conclusion that its best bet was to automate its logistics systems. The reasons are obvious: an AS/RS would not only leverage the storage space to house a larger number of products, but would also boost productivity. The company representative says, “The raw materials represent the origin of the other processes that take place on the production lines. To manage them efficiently, it was clear to us that we needed an automated solution, even more so considering that our center’s operations are becoming more and more automated.”
Determined to renovate its production plant, Normagrup contacted Interlake Mecalux to drive this project forward. "Mecalux designed a solution completely adapted to the particular features of our facility and that met our needs. Plus, the excellent quality-price ratio and after-sales technical support clinched the deal.”
Technical features of the solution
Interlake Mecalux has built an AS/RS for boxes (also known as a miniload system) consisting of four 108-foot-long aisles with 23-foot-high double-deep racking on both sides. “With this solution, we can better organize the raw materials and streamline the rest of the operations in the production plant. We’ve also set aside a space for a new phase of this project, where we’ll build an additional aisle,” indicates Normagrup.
The racks of the miniload system are designed to optimize the available space and accommodate as many products as possible. As a result, Normagrup can now store 8,000 boxes in merely 6,727 ft2 of surface area.
The locations have been personalized to handle 31” x 24” boxes, with a maximum unit weight of 110 lb and three different heights: 9”, 16” or 26”. The tallest boxes are placed on the lower levels of the racks, while the shortest are stored on the upper levels.
Normagrup’s priority with this solution was to have fully automated operations, ensuring that the handling equipment moved the goods continuously and safely. Therefore, in each aisle, a stacker crane quickly inserts and removes the boxes from their locations. It then moves the boxes to the front of the warehouse, where the conveyors are located. Once there, the AIVs pick up the goods and transport them to one of the three production lines.
Every day, between entries and exits, this AS/RS moves around 700 boxes sent to various production areas. With such a large number of movements (8.75 % of the goods stored), Normagrup needed to control all the merchandise to avoid making mistakes. Consequently, Interlake Mecalux also implemented its Easy WMS warehouse management system, charged with supervising the stock and providing total traceability.
Non-automated storage systems
The Normagrup plant also has two non-automated storage systems from Interlake Mecalux where it deposits either raw materials or finished products:
- Pallet racks. Various pallet rack units have been installed throughout the plant. Some of them are low (merely 6.5’ high and with two levels), while others stand 24.6’ tall.
- Cantilever racking. These consist of 17-foot-tall columns to which arms (that hold the goods) are attached. They are specially designed to manage Normagrup’s extra-long products (up to 10’ long).
These two solutions were chosen for two reasons: on the one hand, they are extremely versatile systems capable of housing products of varying lengths and dimensions. On the other hand, they provide direct access to the goods, facilitating their handling when required.
Connection with production
Most of the daily activity at the Normagrup center takes place at the front of the AS/RS for boxes. Three basic operations are carried out: the receipt of raw materials to be stored, kitting and, lastly, dispatch of the kits to the production lines.
“As all movements are automatic, the miniload system has been seamlessly integrated with the other automated processes at the plant,” states the Normagrup representative.
For entries of raw materials, the AIVs deposit the boxes on the conveyors, where they go through a checkpoint to verify that their size and weight correspond to the stipulated requirements for their storage in the warehouse. This process also serves for Easy WMS to identify which items have arrived. It then uses rules and algorithms to assign them a location based on their attributes.
For outbound goods, automation makes it possible to work according to the product-to-person method, whereby the goods are brought to the operators automatically. When a kit is finished, Easy WMS notifies the software that manages the AIV so that a vehicle will pick it up and take it to the production line that requires it.
Advanced management of the automated system
The AS/RS for boxes is equipped with the Easy WMS warehouse management system. According to Normagrup, We installed this program because we were already familiar with how it worked, and we felt it was the best fit.” The company’s production plant already used Easy WMS to manage part of the raw materials sent to the production lines.
Some of the production lines acted like storage buffers, temporarily storing raw materials. To prevent errors, Easy WMS carries out strict control of the goods received and employed in production processes.
The AS/RS ensures total and precise control. Easy WMS not only monitors goods inflows and outflows, but also organizes kit preparation. The WMS sends operators instructions on how to do this task accurately and more quickly: it tells them how many items to remove from each box and in which box to deposit them (each newly formed box corresponds to a kit).
To connect the miniload system with the other processes in the production plant, Easy WMS has been integrated with the Sage Murano ERP system at Normagroup and with the software that manages the movements of the AIVs. “The integration process with this software was simple; it went just as expected, and there were no major hiccups,” notes the company.
Connection and automation
Normagrup strives constantly to improve all its processes in order to fulfill its customers’ needs. Its production plant in the Asturias Technology Park is a prime example of this: year after year, it has expanded and transformed itself with a view to incorporating more processes and raising its production volume.
This center has several working areas that operate independently to be able to act quickly and flexibly but, at the same time, are interconnected. This is the case of the new AS/RS for boxes from Interlake Mecalux: on the one hand, it houses and controls the raw materials, and on the other, it supplies the production lines with the goods required for day-to-day operations.
As this solution is automated, Normagrup can monitor all the items and eliminate any risk of error. Bolstered by technology and automation, nothing can hold Normagrup back. In the words of the company representative, “With the coronavirus pandemic, logically, we’ve suffered a decline in activity. But there’s nothing to worry about — we’re sure we’ll bounce back.”
Automation will continue to provide Normagrup with its characteristic productivity and excellence.
With the AS/RS for boxes, we’ve optimized the space dedicated to the storage of raw materials used in production processes. Our goal was to automate all processes, including management of raw materials and supply of the production lines, which we’ve achieved through the miniload stacker cranes. Finally, we should highlight that Easy WMS has provided us with total control and traceability of the goods, so we can monitor the products across the supply chain.
Advantages for Normagrup
- Organization and management of raw materials: the storage and distribution of the raw materials and components used on the production lines are fully efficient, thanks to the miniload system and the Easy WMS warehouse management system from Interlake Mecalux.
- Space optimization: the AS/RS for boxes, which measures 23’ high and 108’ long, makes the most of all the available space, storing 8,000 boxes in just 6,727 ft2.
- Elevated movement flows: the miniload system, with completely automated operations, can move 8.75% of the boxes stored every day. Additionally, it is automatically connected to the three production lines.
AS/RS for boxes | |
---|---|
Storage capacity: | 8,000 boxes |
Box sizes: | 24” x 31” x 9” / 16” / 26” |
Max. box weight: | 110 lb |
Racking height: | 23’ |
Racking length: | 108’ |
Gallery
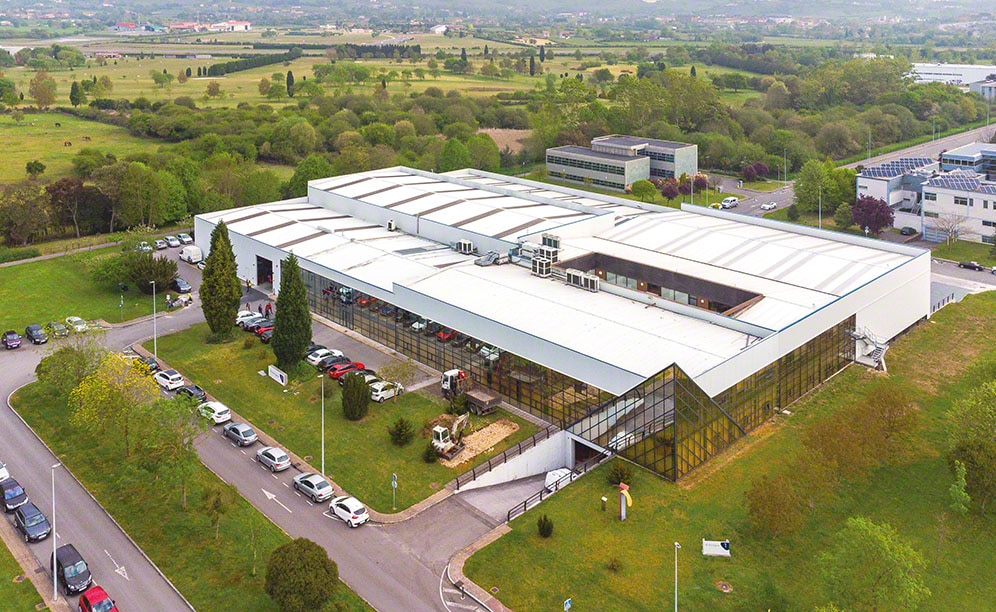
New Normagrup miniload system in Asturias with emergency lighting
Ask an expert