
Patatas Meléndez modernizes its fresh potato warehouse in Medina del Campo
Patatas Meléndez turns to Mecalux’s automated solutions to maximize efficiency in Europe’s most innovative fresh potato factory.
Patatas Meléndez, Spain’s leading potato producer, has installed the automated Pallet Shuttle system and Easy WMS in its warehouse in Medina del Campo. The warehouse acts as a buffer, sequencing the storage and shipment of goods sent to supermarkets.
Patatas Meléndez: from field to table
Patatas Meléndez is the leading Spanish company in the fresh potato sector. The business specializes in selecting, packing, and distributing the finest potatoes supplied by farmers. It achieves this through sustainable land cultivation and by employing best practices to care for the fields and ensure the highest potato quality. Founded in 1999, the company has 250 employees, 526 farmers, a facility spanning 7.4 acres, and 9,884 acres of potato cultivation.
CHALLENGES
|
SOLUTIONS
|
BENEFITS
|
---|
Patatas Meléndez, the leader in fresh potato production in Spain, has commissioned one of the most cutting-edge Industry 4.0 factories in its sector. The new automated facility is located in Medina del Campo. This town is in Castile and Leon, the Spanish autonomous community with the largest cultivated area of potatoes. The launch of this production plant is integral to the business’s growth, expansion, and modernization plan. With a 20% market share, Patatas Meléndez recorded a turnover of $110 million in 2022, a 22% increase over the previous year.
“Our new production center features some of the most advanced Industry 4.0 innovations. The 5.3-acre plant sets a benchmark in the sector. It’s equipped with the latest technologies, enabling us to maximize efficiency,” says Francisco Pérez, Industrial Technical Director at Patatas Meléndez. The technologies driving production capacity include traceability and computer vision-powered potato selection systems in addition to internal transport via automated guided vehicles (AGVs). The figures speak for themselves: the plant processes 220,000 tons of potatoes annually, equivalent to washing 77 tons and packing 193 tons of product per hour.
To produce and sell such a large quantity of potatoes, the company has revamped all its logistics processes. “We’ve developed a distribution model that allows us to reach practically every supermarket in Spain in less than 24 hours. We have total control over our merchandise, from the selection and packaging of the potatoes to their delivery to points of sale,” says Pérez.
Commitment to logistics automation
In its Medina del Campo facility, Patatas Meléndez turned to automation to accommodate finished goods as they leave the production lines. The business implemented Mecalux’s Automated Pallet Shuttle system with transfer cars. This solution has increased storage capacity by a whopping 700%. “Automation makes us more productive, allowing us to offload all potato production quickly and without errors,” says Pérez.
Another essential logistics requirement for the company was for the potatoes’ properties to remain intact. Mecalux’s Easy WMS warehouse management system is the mastermind of the facility. It controls stock in real time and guarantees the optimal preservation of the potatoes. “The quality of our products and processes is non-negotiable. The logistics software monitors the potatoes from the time they enter our center until they’re shipped to our clients,” says Pérez.
In the food industry, the application of strict quality and safety standards makes the logistics operations of businesses like Patatas Meléndez more demanding. For instance, the warehouse is outfitted with special green LED light technology to keep the properties of the products unaltered. “The facility is designed to treat the potatoes with the same care as fruit, protecting them at all times from possible mechanical damage,” says Pérez.
Automatic buffer for finished goods
In Patatas Meléndez’s Industry 4.0 factory, logistics and production processes go hand in hand. They are linked by robotics: AGVs independently transport finished products from production to the storage area.
The entire receiving process is autonomous. The automated warehouse has three checkpoints, where the AGVs place the potatoes on pallets properly labeled using RFID technology. Easy WMS identifies each pallet and validates whether it meets the requirements established for storage. Through advanced algorithms, the software classifies products by batch, assigns them a location, and orders their automatic putaway.
In the Pallet Shuttle storage system, robotic handling equipment executes all putaway and retrieval tasks. A transfer car moves the pallets along a 131-foot-long aisle to the corresponding storage channel. Once there, a motorized shuttle takes over, positioning each pallet in the slot assigned by Easy WMS.
To efficiently produce and ship 220,000 tons of potatoes a year, Easy WMS constantly communicates with the other programs integrated in the Patatas Meléndez facility: the SAP ERP and production control systems.
Sequenced goods dispatch
Next to the automated storage system, Mecalux set up a fully equipped staging area. It features a transfer car and 32 preload flow channels, each with capacity for 16 pallets. In this temporary storage zone, potatoes are strategically sorted to streamline shipping based on delivery routes.
The transfer car moves along a 164-foot-long circuit, placing the pallets — already organized and sequenced — in the corresponding preload channel. From there, they are loaded onto trucks.
Before shipping the goods, operators check each pallet using RF scanners. RFID technology, connected to Mecalux’s Easy WMS, maximizes throughput in this process. The software ensures that the correct products are loaded onto the trucks and placed in the optimal order for delivery to clients.
Advanced technology for a demanding production pace
Patatas Meléndez’s new production plant stands out for its commitment to state-of-the-art technology. The new automated solutions facilitate the production and shipment of 220,000 tons of potatoes annually. Process automation and digitalization help the company control its goods from start to finish. “Our corporate culture is based on the quality of the production processes, from harvesting potatoes in the field to shipping the product to our clients,” says Pérez.
Patatas Meléndez’s supply chain can successfully implement the international expansion strategy it has pursued in recent years. The business is already present in France as Meléndez France and in Portugal as Batatas Meléndez. Currently, it exports 15% of its production and is eyeing Central and Eastern Europe. Its goal is to gain more market share and diversify its export destinations. The Industry 4.0 factory reflects Patatas Meléndez’s steadfast commitment to continuous improvement as a growth strategy.
The Mecalux storage and internal transport solutions enable us to cope with our production pace efficiently and meet the needs of our clients.
Gallery
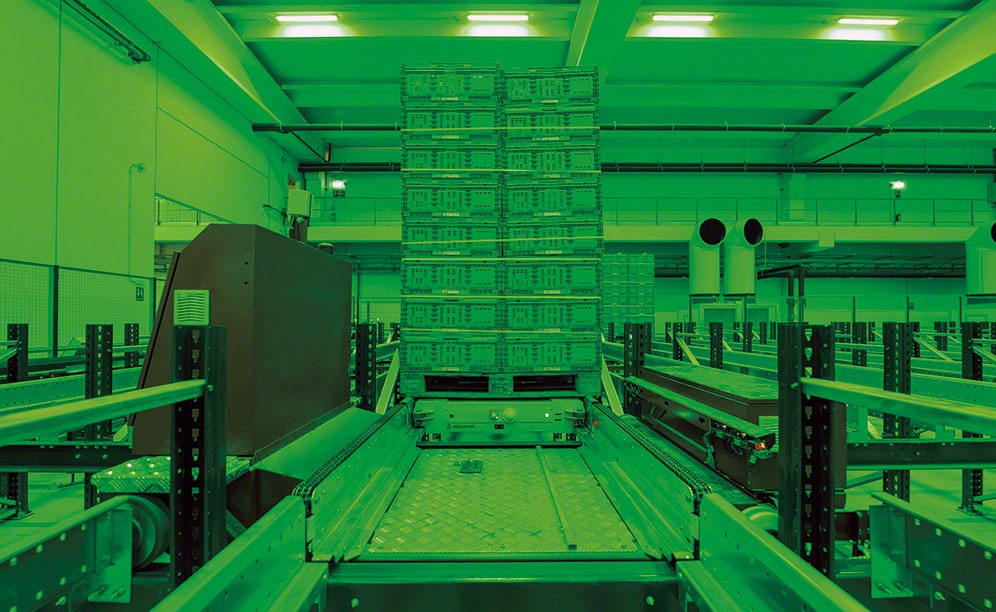
The transfer car moves pallets to their locations automatically
Ask an expert