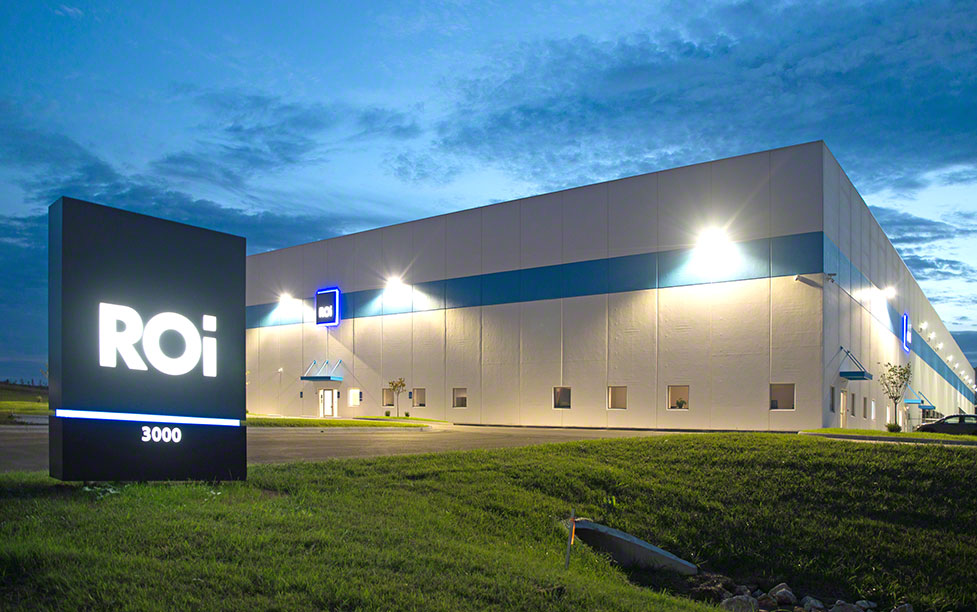
ROi was able to maximize the efficiency of its facility
Multiple storage systems improve efficiency and accuracy of ROi's new facility in Missouri
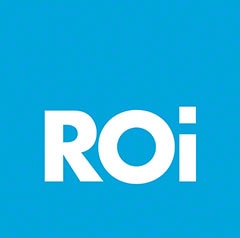
ROi was able to maximize the efficiency of its facility in Republic, Missouri, with the installation of a pick module, selective pallet racks, pallet flow and push-back racking by Interlake Mecalux.
About ROi
Resource Optimization and Innovation (ROi) is a cost management supply gain solutions organization started by Mercy Healthcare in 2002. In 2009, the company began assembling surgical custom procedure trays that hold all the supplies needed by doctors to perform a range of medical procedures. ROi has experienced exponential growth every year since its inception. Today, the program manages more than 760 different medical toolkits and averages more than 630,000 kits produced each year.
ROi’s needs
ROi’s Custom Pack Solutions (CPS) division began in ROi’s Consolidated Services Center in Springfield, Missouri, but recently outgrew its current 30,000 ft² of space. The organization recently moved into a new 107,000 ft² building in Republic, Missouri, that is responsible for the receipt, assembly and distribution of medical and pharmaceutical materials and supplies. ROi worked with Interlake Mecalux and material handling solutions provider LD Systems to equip the new facility with the material handling systems needed to reinvent ROi’s custom procedure tray (CPT) manufacturing process. This is the company’s first facility dedicated to the manufacture of CPTs.
A variety of storage systems
One of the systems the team installed is a 9,000 ft² mixed-use three story pick module that is 28’ high. Distribution centers choose to optimize storage and picking by installing a pick module system. The engineered systems may integrate several material handling products into a storage and picking operation. ROi’s module is for picking from pallets. It has capacity for 152 pallets of 40” x 48” with a maximum weight of 2,000 lb each. There are two aisles, one is 4’ wide and the other is 13’ wide. Picking takes place in the pick module with items extracted from bulk storage that have passed a quality inspection. Operators pick items by line within manufacturing work order. Once all the materials for a work order are ready, they go to a clean room. When the work order is ready for manufacture, operators take the items for that work order to the appropriate manufacturing line.
The new facility also features 52,000 ft² of 24’ high selective pallet racks that can hold 2,800 pallets of 40” x 48”, also with a maximum weight of 2,000 lb. The selective racks have four storage levels and six 11’ wide aisles with single-depth racks on both sides. The pallet racks also provide direct access to each pallet for simple stock management and high speeds when managing the pallets and picking orders. The racks are adaptable to any product volume, weight or size and provide versatility for facilities like ROi’s, which has wide varieties of product types and 2,200 SKUs. Selective rack also has a variety of accessories and options available that adjust to all SKU types.
LD Systems also installed 12,000 ft² of Interlake Mecalux push-back racking that is 24’ high and can accommodate 1,200 pallets weighing a maximum of 2,000 lb each. This section of racking has four levels and three aisles that are 11’ wide. Available in two-, three-, four-, and five-deep pallet designs, push-back racks allow efficient use of space with limited sacrifice in product accessibility. They also provide the optimal combination of selectivity and storage density. Loading and unloading takes place using the same aisle according to the LIFO system (last in, first out). Operators place pallets on a free-rolling cart that pushes back into the system by loading additional pallets. When unloading, gravity moves the pallets forward to the aisle on the telescoping carts, eliminating the need for reaching or driving into the rack.
There also is pallet flow rack on the first, second and third floors of the installation. All of the pallet flow lanes are two pallets deep. On the ground floor, there are two beam levels in every other bay and the remaining bays have one beam level. The bays on the second and third floors have one beam level. There are 19 bays on each level with two pallet facings per bay. One bay on each level is for the return of empty pallets. The remaining bays provide 117 pallet pick facings and store up to 234 pallets. Pallet flow systems fully utilize the available storage space while ensuring the faces along the picking aisle remain regularly stocked. In this first-in, first-out (FIFO) system, operators load pallets at the top end of the slightly inclined rack and the pallets glide safely at a controlled pace to the other side.
Overall, it took only four months to install all of the systems and another five months to complete the testing and documentation necessary for the facility to comply with U.S. Food and Drug Administration regulations. With its new arrangement of storage systems, ROi wants to be able to handle at least the 300% growth it is expecting over the next five years. “The new system allows us to pick more material with less staff and be much more scalable as we grow more CPT volume,” said Rick Parrish, director of manufacturing at ROi. Thanks to its new setup, the organization also expects to reduce labor costs per material pick by 30% and picking accuracy improvement by 20%. “To our knowledge the new system is more accurate and efficient than any other for manufacturing CPTs,” Parrish said.
Advantages for ROi
- Increased productivity: the warehouse’s various storage systems will enable ROi to triple its production of custom procedure trays (CPTs).
- Reduced labor costs: the new system will allow ROi to pick more material with less staff and be much more scalable.
- Improved accuracy: with its new setup, ROi expects to improve picking accuracy by 20%.
Interlake Mecalux Product: Mixed-use 3 story pick module | |
---|---|
Number of bays: | 19 |
Frame specs: | 48” X 28’, 4” X 3” column, 8” X 8” X 3/8” foot plate |
Beam specs: | 144” and 96” beams, various capacities |
Number of beam levels: | 4-8 |
Height of rack: | 28’ |
Number of aisles: | 2 |
Aisle width: | 4’ and 13’ |
Pallet positions: | 152 |
Pallet type: | GMA |
Pallets per level: | 1-2 |
Capacity: | 2,000 lb |
Area racked (square feet): | 9,000 square feet per level, 3 stories |
Gallery
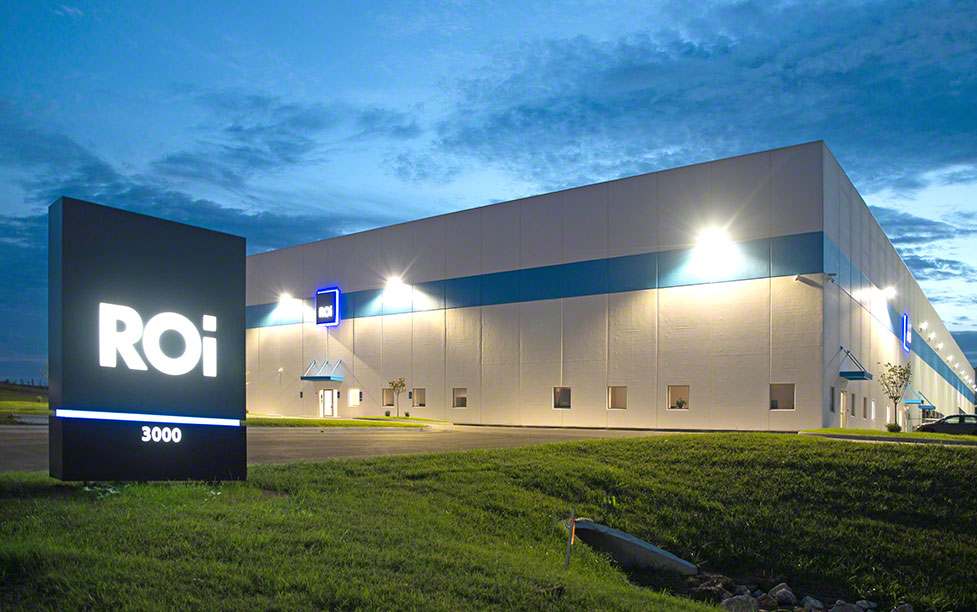
ROi's facility in Republic, Missouri
Ask an expert