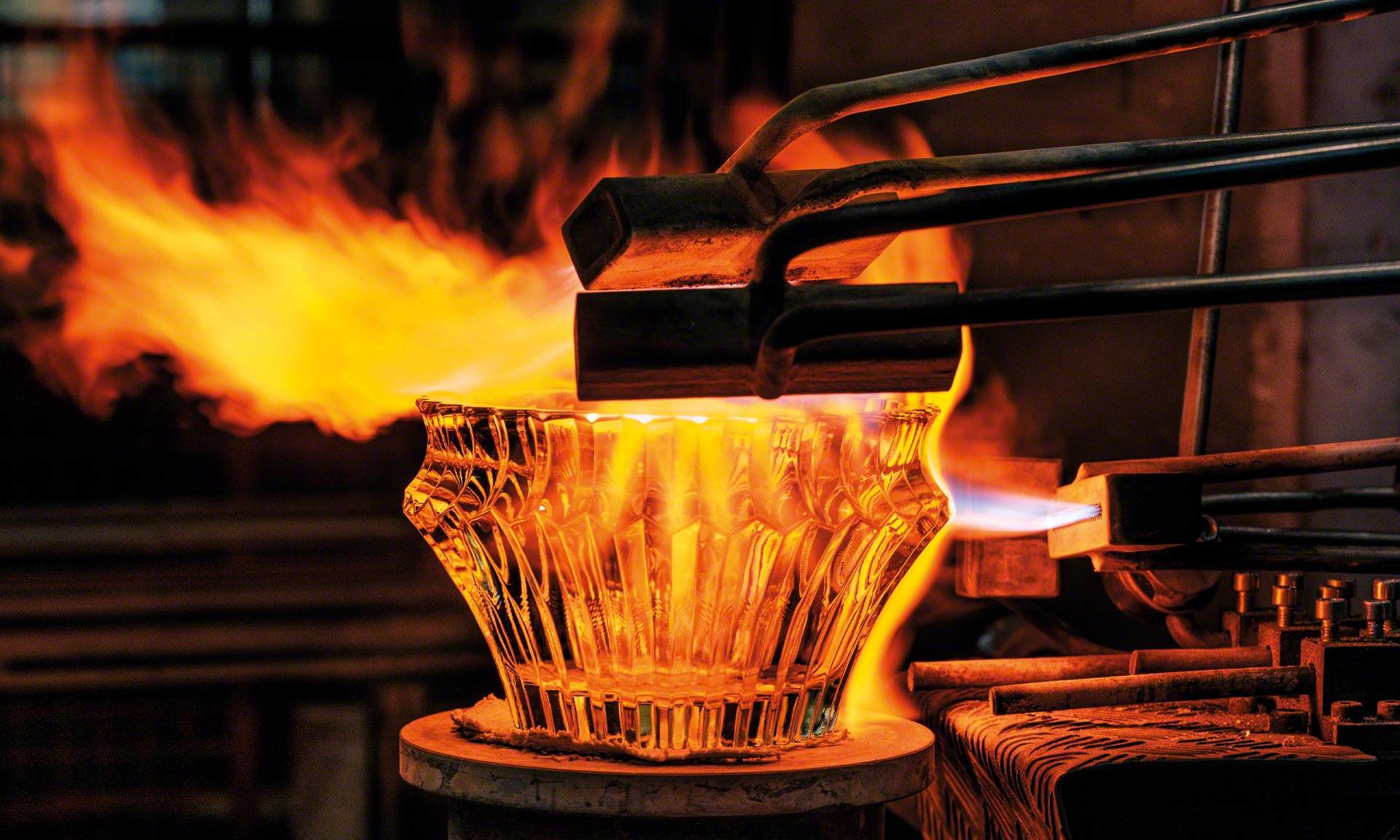
Steklarna Rogaška transforms its 4 high-end crystalware facilities
Steklarna Rogaška, a manufacturer of premium home decor crystalware, implements Easy WMS in its 4 warehouses to optimize the production of glass parts.
Premium crystalware brand Steklarna Rogaška has installed Easy WMS in its 4 warehouses in Slovenia. Digitalization has enabled the company to connect its logistics processes with its production lines and control its SKUs.
Steklarna Rogaška: 350+ years of tradition
Based in Rogaška Slatina (a Slovenian region with a rich glassmaking tradition), Steklarna Rogaška specializes in crystalware for the home. Drawing on nearly 350 years of artisanal glassmaking, the business markets unique, stylish items. Its commitment to honoring tradition adds to the distinctiveness of its products, contributing to its global success. Additionally, the company sponsors sports competitions, social events, and beauty pageants and has even “conquered” Hollywood. Founded in 1927, the company’s total storage space measures 353,147 ft³.
CHALLENGES
|
SOLUTION
|
BENEFITS
|
---|
Steklarna Rogaška’s supply chain stands out for its ability to adapt to the demands of its customers around the globe (primarily in the US and UK). In line with its just-in-time (JIT) manufacturing strategy, the business produces and ships glass objects and crystalware upon the receipt of customer orders. Despite dealing with a high volume of monthly orders, the company always maintains minimum stock levels of the essential raw materials required for production.
“Our number one priority is to provide our clients with the best possible service. To do this, we decided to make significant improvements to our supply chain, for instance, embracing digital technologies to guarantee more rigorous stock control. We’re convinced that digitalizing our logistics processes is a crucial step towards success. It not only benefits our company but also ensures that our customers receive the service they expect: fast and error-free deliveries,” says Gregor Vaukan, Logistics Coordinator at Steklarna Rogaška and leader of the organization’s warehouse management system (WMS) implementation project.
When it came to modernizing its logistics operations, this manufacturer sought the collaboration of Špica, a technology company with expertise in digital solutions for supply chain management. “Špica has an excellent reputation in Slovenia and a highly professional team that helped us find the best WMS software for our business,” says Vaukan.
Process integration across four facilities
Steklarna Rogaška opted to install Mecalux’s Easy WMS software in four of its warehouses. Two are located in the town of Rogaška Slatina (with one adjacent to the manufacturing plant), while the other two are in the towns of Kozje and Rogatec, respectively. “We visited the logistics centers of a Slovenian organization that was using Easy WMS. After observing the system in action, we were sure it could be tailored to our specific logistics needs,” says Vaukan. Easy WMS tracks the status of the more than 5,000 SKUs in stock in any of the four facilities. These products span raw materials, packaging items, semi-finished goods, and finished products.
Before installing Easy WMS, Steklarna Rogaška relied on an ERP system to handle the fundamental operations of its warehouses. For example, the ERP software monitored inbound and outbound shipments and coordinated the preparation of a limited number of orders.
Operators manually entered all stock-related information into the SAP ERP system. Upon receiving a product, they had to complete two steps: inform the software of the item’s arrival at the logistics center and then specify its storage location. Manual handling of goods posed the risk of errors: “Discrepancies between the physical stock in the facilities and the inventory we had on record were a common occurrence,” says Vaukan.
Digital makeover for just-in-time manufacturing
As sales continued to grow, the company’s logistics processes became increasingly complex and demanding. Steklarna Rogaška wanted to go paperless to eliminate redundant tasks and streamline operations. How did it plan to do this? By digitalizing its logistics processes.
“We believed that WMS software would give us precise control over the status of products in addition to distributing tasks among our staff and improving operations overall. Before deploying Easy WMS, we had various logistics challenges we need to respond to: boosting picking productivity, reducing errors in inventory handling, and cutting down on warehouse operational costs,” says Vaukan.
One of Steklarna Rogaška’s top priorities was for Easy WMS to seamlessly integrate with the SAP ERP software to efficiently organize all supply chain processes. These two systems now communicate continuously and bidirectionally to exchange data and information. The result? Raised productivity across all operations.
Effective coordination between logistics and production processes is crucial for the JIT manufacture of glassware and its timely shipment. By integrating Easy WMS with the SAP ERP system, the production lines always have the materials they need. “The connection between these two software programs has enhanced process efficiency as well as employee performance,” says Vaukan.
Simultaneous management of four facilities
Easy WMS keeps track of 5,000 SKUs in the business’s day-to-day warehouse operations while it managing its 110,000 total SKUs in stock. The system also provides real-time location information for 12,000 pallets spread across the four logistics centers, whether they contain raw materials or finished products.
At the same time, Easy WMS oversees all operations in Steklarna Rogaška’s four logistics facilities: the receipt of raw materials, their dispatch to production, the storage of finished merchandise, and its shipment to customers.
Operators use RF scanners to follow instructions from the WMS software, which guides them at every turn. It shows them where to locate each raw material needed for production and the crystalware to be shipped to customers. Thanks to these detailed instructions, all goods movements are recorded in real time in the Easy WMS database. “All the information is online, and we can access it whenever we need to. We can monitor stock in real time,” says Vaukan.
Raw materials and packaging products sent by suppliers in Slovenia, other European countries (especially Germany and the UK), and China are stocked based on demand levels. Easy WMS assigns these supplies a location near the production lines to streamline their transfer at the right time.
Once finished products leave production, they are moved to the corresponding warehouse and strategically distributed in the racks following several criteria. These include, among others, their size, characteristics, or whether they will be used to fill a pending order.
Raw materials are stored according to the FIFO method, where the first pallet in is the first out. “The FIFO stock management strategy is crucial to maintain the proper turnover of our glass items. We have a high volume of incoming and outgoing goods. Therefore, we have to make sure that raw materials are sent to production in the order they arrived at our facility,” says Vaukan.
Optimizing order fulfillment
Order processing has seen considerable improvements following the installation of Easy WMS. “Picking is now much faster and more accurate. We’ve automated administrative tasks so that our warehouse operators can focus solely on locating the required merchandise and shipping it as quickly as possible,” says Vaukan.
Steklarna Rogaška fulfills 2,900 orders a month, which translates into 7,300 pallets sent to the production plant or customers around the world. This high order volume calls for meticulous process control and optimized movements to avoid errors and ensure swift delivery.
Before, Steklarna Rogaška would print a list of orders for operators to fill. However, this list quickly became irrelevant as new orders came in. Managing goods on paper presented major challenges in terms of verifying order completeness and identifying missing items.
“With a digital tool like Easy WMS, we no longer need to print documents that would soon become obsolete. Operators simply follow the system’s instructions via their RF scanners, allowing for faster picking,” says Vaukan.
Digitalization makes it possible to locate the SKUs needed to fill each order in a quick, error-free way. “Pickers no longer need to hunt for items around the facility; the entire operation is much faster. Easy WMS designs efficient paths for these workers to cover the shortest distances,” says Vaukan.
Once Steklarna Rogaška’s operators have prepared the orders and they are ready for shipment, the Logistics Department assigns them to the appropriate carrier for final customer delivery. Previously, operators created packing lists manually. They had to input all the data into the SAP ERP system, which was time-consuming and labor-intensive. “Now, the WMS software automatically generates the delivery note, resulting in substantial time and cost savings,” says Vaukan.
Advanced management and real-time control
Steklarna Rogaška is an internationally renowned high-quality crystalware manufacturer. Transparency is at the core of the company, both in its creations and its production and logistics processes. Digitalization has given the business complete, real-time visibility into its entire supply chain.
Thanks to Mecalux’s WMS software, Steklarna Rogaška’s four warehouses operate in an integrated way to streamline processes. Production and logistics work hand in hand with the primary goal of serving customers as rapidly as possible. Easy WMS has also provided the company with precise control over the status of its goods and the performance of its operations.
“We’re committed to continuous improvement to be able to adapt to changing market needs. Our mission is to keep growing and to become a reliable partner for our customers in supplying the highest quality glass pieces,” says Vaukan.
Easy WMS has given our supply chain a massive overhaul. Now, we can track the status of the 5,000 SKUs we keep stocked across four facilities. We’ve also dramatically improved order picking. This has boosted our productivity as well as customer satisfaction.
Photo: Iztok Nikolić
Ask an expert