
Vandemoortele: logistics with a taste of automation
Mecalux equips the modern logistics center of multinational company Vandemoortele in Barcelona with five storage systems
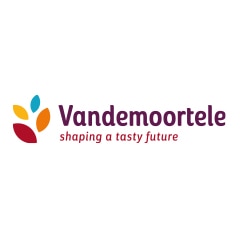
Mecalux equips the modern logistics center of multinational company Vandemoortele in Barcelona with five storage systems. An automated rack-supported warehouse; pallet, flow, and push-back racks; and picking shelves vitalize a logistics facility that manages the movement of 1,200 pallets a day.
The best taste, the best quality, the best service
Founded in 1899 in Izegem, Belgium, Vandemoortele is a leading business group in the food industry in Europe. It has two business lines: one for pastry and bakery products and another centered on the production of margarines, oils, and cooking fats. In addition to Europe, the company is present in the US.
- Products: 4,700
- European markets: 17
- Employees: 5,100
- Production centres: 31
CHALLENGES
|
SOLUTIONS
|
BENEFITS
|
---|
The role of a finished goods warehouse in the supply chain is critical, as it has a direct impact on customer satisfaction. There is no point in optimizing management of raw materials and production processes if, in the end, the finished goods warehouse lacks efficiency.
A few years ago, multinational company Vandemoortele opened a modern production plant in Santa Perpètua de Mogoda (Barcelona, Spain) to manufacture margarines and fats. The facility also has an area allocated “solely to the storage of finished goods coming off the seven production lines,” says Oriol de Haro, the business’s Logistics Manager.
The warehouse stores pallets with a high turnover, acting as a buffer in which products are deposited temporarily until they are distributed to end customers. To manage the goods efficiently, Mecalux has installed five distinct storage systems. In addition to housing around 360 SKUs of varying characteristics, sizes, and turnover, these five solutions have optimized the storage space.
An automated rack-supported warehouse; pallet, flow, and push-back racks; and picking shelves vitalize a logistics facility that manages the movement of 1,200 pallets a day: 400 from the production lines, 400 that are distributed to end customers or other warehouses where picking is carried out, and 400 that are sent to suppliers. “We used to work with pallet racks. The area with the automated warehouse and pallet flow racks didn’t exist; it was built when we began to ramp up the volume and pace of production,” says Haro.
Automated clad-rack warehouse
“The rack-supported building has radically changed our logistics infrastructure,” says Haro. “It’s helped us to boost productivity in moving, storing, and dispatching our goods. Moreover, this solution has optimized the available space, improving organization of the finished goods that leave the production lines.”
With a height of 51.4’ and capacity for 4,721 pallets, the automated clad-rack warehouse operates at a controlled temperature of 41-59 °F. The clad-rack structure fosters energy savings, as the cold air is distributed among a larger number of stored pallets.
The facility is made up of three 213.3-foot-long aisles. During the first phase, Mecalux installed a single twin-mast stacker crane, which operated in the three aisles. It did so by means of a system of curved rails set up at the back of the warehouse, enabling the stacker crane to change aisles as required. This solution is implemented when the storage volume is high and the flow of movements is moderate.
During the second phase, and due to the spike in production, Vandemoortele decided to install a second (single-mast) stacker crane. Its position was fixed in the first aisle, with the twin-mast stacker crane operating in the other two. “The second stacker crane has enabled us to increase the flow of movements and ensure that the warehouse is always operational,” says Haro.
The pallets from the production lines enter the warehouse via a conveyor system. They then go through a checkpoint and are stored in the racks with the help of a transfer car and a stacker crane. The various automated elements are also charged with moving the pallets to the dispatch area, where the five loading docks are located.
Four complementary storage systems
Mecalux has also installed four non-automated storage systems with different functions:
- Pallet flow racks. With capacity for 640 pallets, this compact system houses many pallets per each SKU of finished product, making the most of the space. Each channel, capable of storing up to 16 pallets, is reserved for a single SKU. The pallets are moved by gravity from the highest part of the channel, which has a 3.7% slope, to the last free position.
- Push-back racks. This high-density solution stores drums and intermediate bulk containers (IBCs) on larger pallets. Standing 21.3’ tall, this system makes it possible to push pallets back into the lanes on each level.
- Pallet racks. This storage solution, which stands out for its versatility and strength, stores finished product, empty containers, and the packaging used on the production lines. The racks have five levels and can accommodate up to 800 pallets. This type of racking was chosen because of its direct access to the products, which greatly expedites management of the goods.
- Picking shelves. Located on the lower level of the pallet racks, the picking shelves house the samples from the production lines.
Scalable, efficient logistics
Vandemoortele is an innovative company that, from the start, has demonstrated a commitment to continuous change and improvement in order to guarantee the excellence of its products. At its plant in Barcelona, the company has a finished goods warehouse that has been expanded to allow it to cope successfully with the high rate of production. The various storage systems and optimized layout of the facility enable the movement of around 1,200 pallets a day. Likewise, the rack-supported warehouse ensures the safe, continuous flow of goods at a controlled temperature to maintain their flavor and quality. Vandemoortele’s logistics operations are befitting for a leading European food company.
We’re pleased with the automated warehouse and the investment we’ve made because they’ve helped us to raise our productivity and throughput. Thanks to the different storage systems installed, we store our goods in the best possible conditions.
Gallery
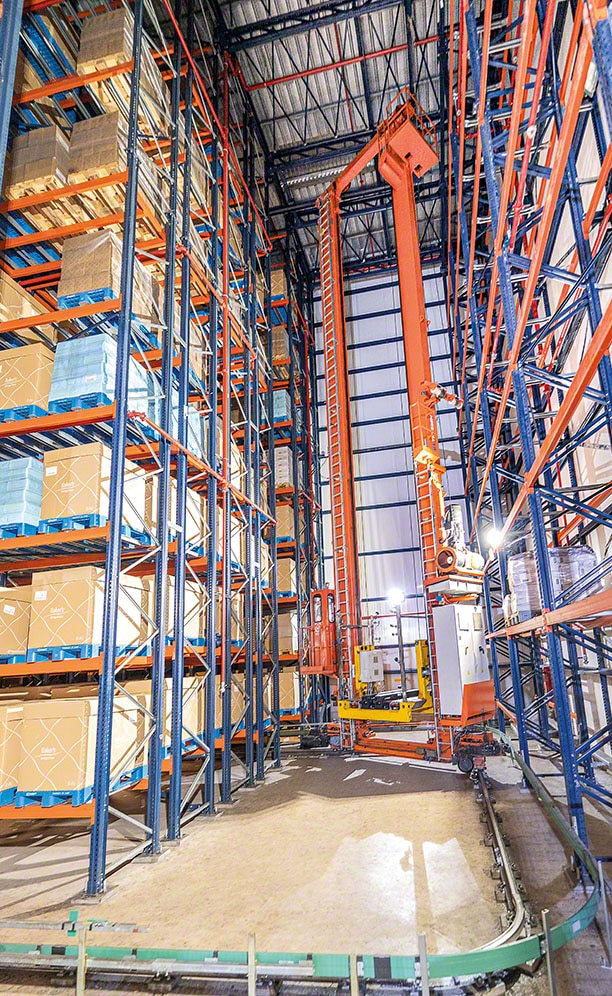
Vandemoortele stores SKUs of varying sizes and turnover
Ask an expert