
Verlhac: automated operations at full tilt
3PL provider Verlhac automates its logistics operations with the Pallet Shuttle system with stacker crane
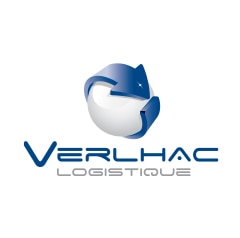
3PL provider Verlhac has automated its warehouse in Cahors, France, with the Pallet Shuttle system with stacker crane and Easy WMS warehouse software. In a surface area of 11,022 ft², Verlhac manages the products of one of its main customers: ANL Packaging, a manufacturer of thermoformed containers.
Verlhac Logistique: made-to-measure logistics
Verlhac Logistique is a 3PL operator that provides storage and transportation services for businesses from all industrial sectors. The company owns 363,820 ft2 of warehousing space in France where it manages its customers’ products.
- Founded in 1957
- No. of warehouses: 5
- Total storage space: 363,820 ft²
- No. of employees: 70
THE CHALLENGE
|
THE SOLUTIONS
|
THE BENEFITS
|
---|
How can you leverage the height of a warehouse with specific size constraints? 3PL operator Verlhac Logistique solved this logistics conundrum with the help of Mecalux. The company has opened a new, 11,022 ft2 facility in Cahors, southern France, where it manages the products of one of its main customers: ANL Packaging, a manufacturer of thermoformed containers.
During the assembly phase, while Verlhac Logistique sought a storage solution that would best meet its logistics needs, it came up against an obstacle: the warehouse is very close to an airfield, so the building could not be taller than 32.8’.
Mecalux came up with a response that was both resourceful and efficient: “It set up the automated storage and retrieval system (AS/RS) in a 6.5-foot-deep pit to obtain the capacity we needed, in compliance with the building’s height regulation,” says Michel Verlhac, President of Verlhac Logistique.
In recent years, ANL Packaging has ramped up its production pace. Verlhac explains that the new AS/RS had to support that growth: “We had to accommodate a larger number of products in the smallest space possible.”
Besides optimizing space, Verlhac Logistique also needed a solution that would guarantee a minimum number of movements per hour. This is because it had to be prepared to “cope with the arrival of more products and the dispatch of a growing number of orders,” says Verlhac.
Automated Pallet Shuttle: agility in an optimized space
“In starting up a new AS/RS, our priority was to absorb ANL Packaging’s increased production, as well as speed up the entry and exit of goods at the right time,” says Verlhac. The two companies literally work side by side. ANL Packaging has also just opened a new warehouse right next to the Verlhac Logistique building so that the two facilities can coordinate and streamline distribution of the goods. For both projects, the companies chose the same Mecalux storage system: the automated Pallet Shuttle.
“Mecalux suggested the automated Pallet Shuttle system with stacker crane because this solution takes advantage of the available surface area without losing speed in the flow of goods,” says Verlhac. This system is completely automated.
The motorized shuttle is responsible for moving the pallets inside the storage channels with full autonomy. In the storage aisle, a twin-mast stacker crane executes movements from the AS/RS entry and exit points to any storage channel, following instructions from the Mecalux software at every turn.
The AS/RS, equipped with two 32.8-foot-high blocks of racking provides capacity for 2,240 pallets in approximately 9,688 ft². Likewise, the locations have been customized to store two different pallet sizes, each weighing up to 1.1 t.
“We’re pleased with the automated Pallet Shuttle system. Thanks to this fully automated solution, we’ve gained in speed, accuracy, and safety when storing our customers’ products,” says Verlhac.
More efficient management
Verlhac Logistique has also installed the Easy WMS warehouse management system (WMS) from Mecalux to control inventory in the AS/RS in real time. “We wanted a program that would monitor product movements as well as orchestrate operations performed in our AS/RS,” says Verlhac.
The Mecalux software identifies each product the minute it arrives at the AS/RS. To do so, the pallet checkpoint installed at the start of the conveyor line automatically reads each pallet’s barcode label. There, operators verify that the pallet corresponds to the one previously indicated by the ERP (enterprise resource planning) system, and its dimensions and conditions are checked.
Then, to assign the pallet a location on the racks, Easy WMS makes a series of calculations, taking into account the number of empty slots, the SKU, and the demand level. This is where automation comes into play: conveyors, the stacker crane, and the motorized shuttle are charged with automatically moving the pallet to the corresponding location.
“Operations in the AS/RS have to run perfectly, so it was essential for the WMS to communicate smoothly with our ERP system,” says Verlhac. The two systems have been integrated to exchange information and data on the status of the warehouse and business needs, such as items scheduled to arrive and orders placed by customers that need to be shipped as soon as possible.
Once the pallets are stored, the WMS knows the status of all the goods in real time and shares this information with Verlhac Logistique’s ERP system. When dispatching the pallets, the ERP system again notifies the Mecalux software of the pallets it needs in order for the WMS to manage the picking list for those pallets based on the transportation route of the requested order.
Personalized to a T
Verlhac Logistique has benefited from a made-to-measure warehousing solution by Mecalux. The 3PL provider now has the storage capacity it needs, a process carried out in line with local regulations for the area in which the building is located.
The company has leveraged the advantages of automation and compact storage to modernize its logistics operations and enhance its customer service. Through automation, Verlhac Logistique now has a flexible supply chain ready to take on future challenges.
The automated Pallet Shuttle system is the solution we needed to optimize space and boost our storage capacity. Plus, by fully automating operations, we now have continuous inflows and outflows.
Automated Pallet Shuttle | |
---|---|
Storage capacity: | 2,240 pallets |
Pallet sizes: | 31.5”/39.4” x 47.2” |
Max. pallet weight: | 1.1 t |
Rack height: | 32.8’ |
Rack length: | 105’ |
Gallery
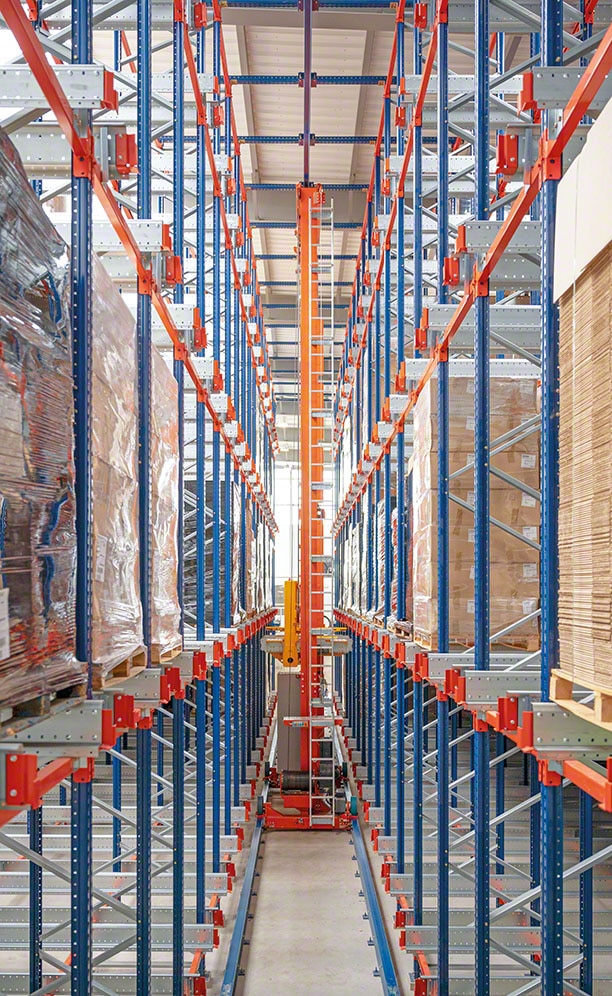
Pallet Shuttle system with transfer car in the Verlhac facility
Ask an expert