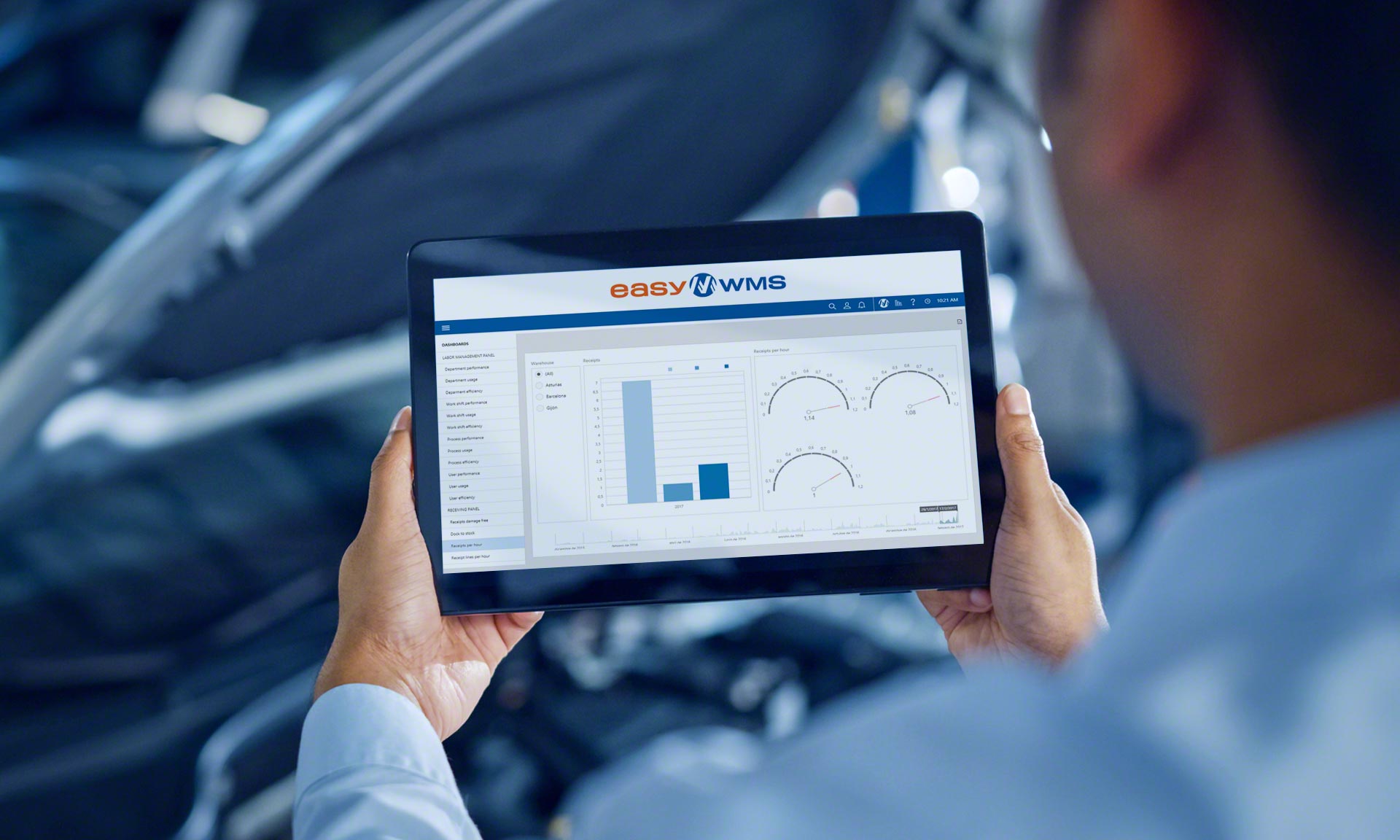
Mecalux’s Easy WMS runs the warehouse of carmaker Renault
Easy WMS manages all warehouse operations, while also ensuring the uninterrupted supply of the manufacturing plant
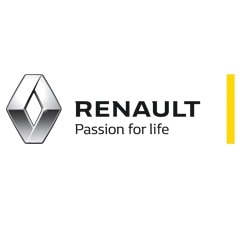
Automotive manufacturer Renault has installed the Easy WMS warehouse management system in its production warehouse in Seville, Spain. This WMS ensures that production lines are consistently supplied with the goods they require, streamlining manufacturing processes all times.
From aviation to autos
In terms of its international presence, Renault is one of the largest automobile producers. Established in France in 1898, it has become one of the most pro-zero emissions e-car companies around.
The Seville plant opened in 1938 as ISA (Industrias Subsidiarias de la Aviación), an aeronautics parts manufacturing business. Twenty years later, in 1958, ISA started to produce transmissions for Renault and, after the success of this venture, the French group purchased ISA.
This factory is highly regarded both inside and outside the Renault group. It fulfills 30% of the company’s requirements globally and exports 80% of its production to the group’s plants in France, the UK, Russia, Turkey, Morocco, Argentina and Mexico, among others.
How the warehouse runs
This center holds around 1,200 pallets and, currently, is expanding to house up to 1,000 more. The warehouse receives parts used to assemble transmissions, mainly axles and sprockets.
In the Seville plant, a million transmissions are made a year and then shipped to the various manufacturing centers the Renault-Nissan Alliance owns around the globe.
On a daily basis, the warehouse issues unworked parts to the manufacturing plant. This involves parts, like drive shafts, that are unsuitable for picking due to their dimensions.
That said, most of the orders need some prep —they put together between 60 and 80 orders a day. This is true for sprockets, for example. Once received, the operators slot the items for each manufacturing order into the shorter racking units. At a later stage, these items are shifted to manufacturing by Automatically Guided Vehicles (AGV).
These racks are devised to provide the goods needed for manufacturing lines and to streamline the assembly of the transmissions. Each one holds essential items to supply two manufacturing orders (the first at the front and the second at the rear).
Easy WMS by Interlake Mecalux
Easy WMS, the warehouse management system developed by Interlake Mecalux Software Solutions, spearheads all in-warehouse processes taking place at the Renault installation, including the input of goods from the machine shops, pick tasks and sending products to the manufacturing lines and/or to dispatch.
For smooth running of the various warehouse operations, Easy WMS is in ongoing communication with GPT —Renault’s ERP, as well as the automatic robot that organizes the assembly lines. Via Modbus, a serial communications protocol, the robot issues a list to the WMS with the must-have items for each manufacturing order in progress. Subsequently, the WMS transmits the orders to the workers. These personnel carry a handheld RF device to pick the list. The system pinpoints what goods each container requires and how much must be collected, which curtails any sort of potential error.
Advantages for Renault
- Perfectly controlled stock: the warehouse management system is always on the ball with the real-time status of inventory.
- Swift pickings: the WMS tells the operators how to prepare orders being sent to the manufacturing lines, stamping out any potential mistake making.
- Maximum productivity: using Easy WMS means all in-house processes and operations run without a hitch.
Gallery
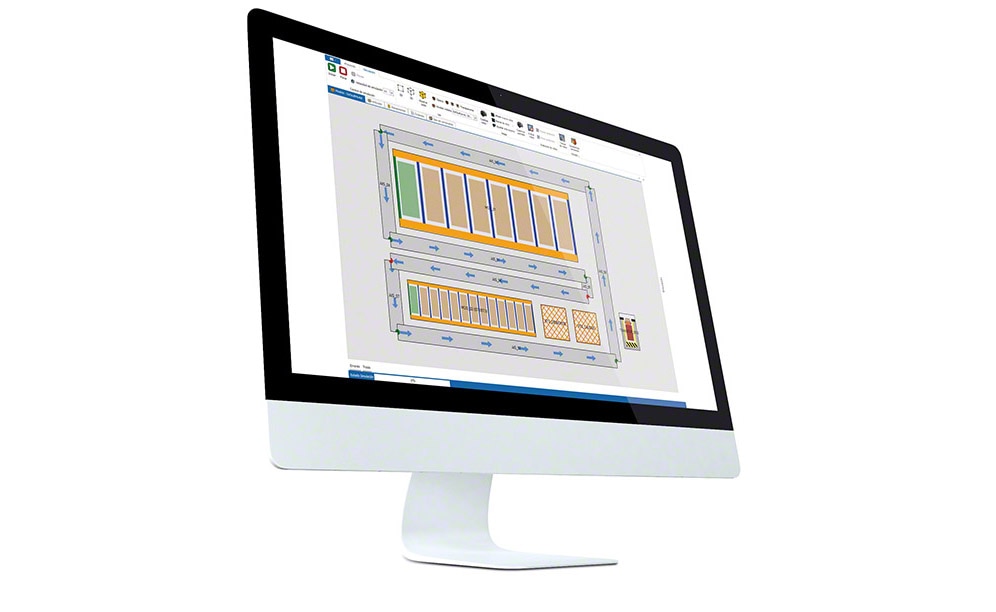
Workflows of the Renault warehouse
Ask an expert