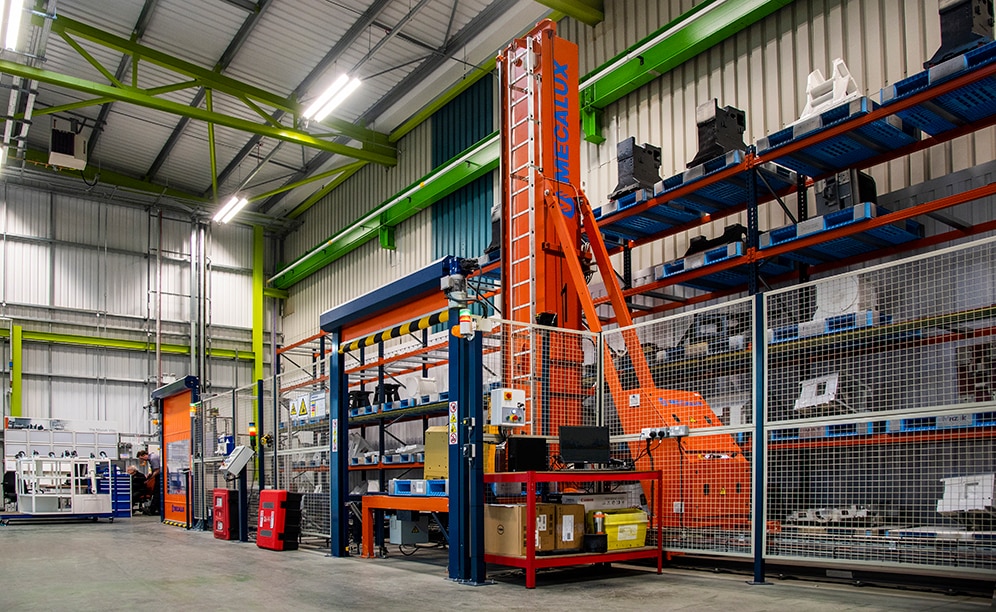
Yamazaki Mazak: an automated buffer for freshly painted parts
Managed by Easy WMS, the automated warehouse ensures safe goods movements
Yamazaki Mazak UK Ltd, one of the industrial machinery manufacturers with the largest presence in Europe, has transformed its production center in Worcester (United Kingdom) with the installation of a fully automated buffer for temporary storage. It is comprised of a small automated warehouse for pallets by Interlake Mecalux where recently painted parts are stored for as long as it takes them to dry. This process is critical for manufacturing the firm’s various components. Technology has enabled very safe goods movements and extremely precise control of each item.
From Japan to the rest of the world
Founded in 1919 in the Japanese city of Nagoya, Yamazaki Mazak UK Ltd is a multinational that manufactures machinery used to shape all types of solid parts, irrespective of their industrial sector.
Besides Japan, the company has production plants in the Unites States, the United Kingdom, Singapore and China. All these factories have a common denominator: they are equipped with cutting-edge technology to cope with the challenges of an increasingly frenetic production rate. Through its products, the firm aims not only to manufacture machines that meet high quality standards, but also to improve the industry and, ultimately, society as a whole.
In 1987, Yamazaki Mazak UK Ltd opened a production center in the town of Worcester, United Kingdom. From there, it supplies thousands of customers across Europe. In addition, the company is especially proud of having established the European Technology Center (ETC), a 31,215 ft2 showroom in which the firm’s most recent innovations are displayed and training sessions are held.
As Yamazaki Mazak UK Ltd’s entire business revolves around technology, automation imbues all its operations, including logistics. The multinational is fully aware that automatic processes are essential to guaranteeing the availability of its products and the accurate execution of storage and order preparation tasks.
To this end, Yamazaki Mazak UK Ltd has installed an automated warehouse by Interlake Mecalux in its paint shop for parts. Although not large, the installation plays a major role in company operations: it acts as a buffer where freshly painted parts are stored. The parts are left to dry before being sent on to other production departments.
Interlake Mecalux has also deployed the Easy WMS warehouse management system, which knows the exact location of each item. Via the control system, this software directs the movements of the stacker crane and conveyors, thus ensuring maximum warehouse safety.
Automation is a must
The warehouse consists of a single, 20-foot-high pallet racking unit with five storage levels. A trilateral stacker crane automatically inserts and extracts the goods from their locations according to instructions from Easy WMS. In total, 60 pallets measuring 43” x 43” with a 1c,100 lb maximum unit weight can be stored.
Yamazaki Mazak UK Ltd opted for this solution because, in the words of Wayne Price, Yamazaki Mazak UK Ltd’s Sheet Metal Department Manager, “Our objective was to guarantee the controlled inflow and outflow of the painted parts.”
The trilateral stacker crane works exactly the same as the forklifts used by operators, the difference being that its operation is fully automated. As a result, all products can be handled with minimum human involvement.
Communication and integration
Yamazaki Mazak UK Ltd has a fully integrated manufacturing plant, the operations of which are coordinated with each other. This working method ensures that all departments have at their disposal the necessary resources for turning out the greatest amount of work possible.
Work in these installations is carried out over two eight-hour shifts, five days a week (Monday to Friday). The racking served by the trilateral stacker crane has been specifically designed to house products the multinational needs and to guarantee that their entries and exits are carried out at the right time and without delay.
Automation has helped us satisfy the two priorities we had for this project: speeding up the entry and exit of painted parts at the right time and being able to continuously monitor the stored goods.
Advantages for Yamazaki Mazak UK Ltd
- Connected production and logistics: the warehouse acts as a buffer. Freshly painted parts are placed on the racks, where they are left to dry before being dispatched to other production areas.
- Uninterrupted operations: the trilateral stacker crane inserts and extracts recently painted items from their slots.
- Technology and automation: one of this firm’s priorities is for all its processes to be at the forefront; therefore, the buffer for recently painted parts is fully automated, improving operator and goods safety.
Yamazaki Mazak's warehouse | |
---|---|
Storage capacity: | 60 pallets |
Pallet size: | 43” x 43” |
Max. pallet weight: | 1,100 lb |
Rack height: | 20' |
Gallery
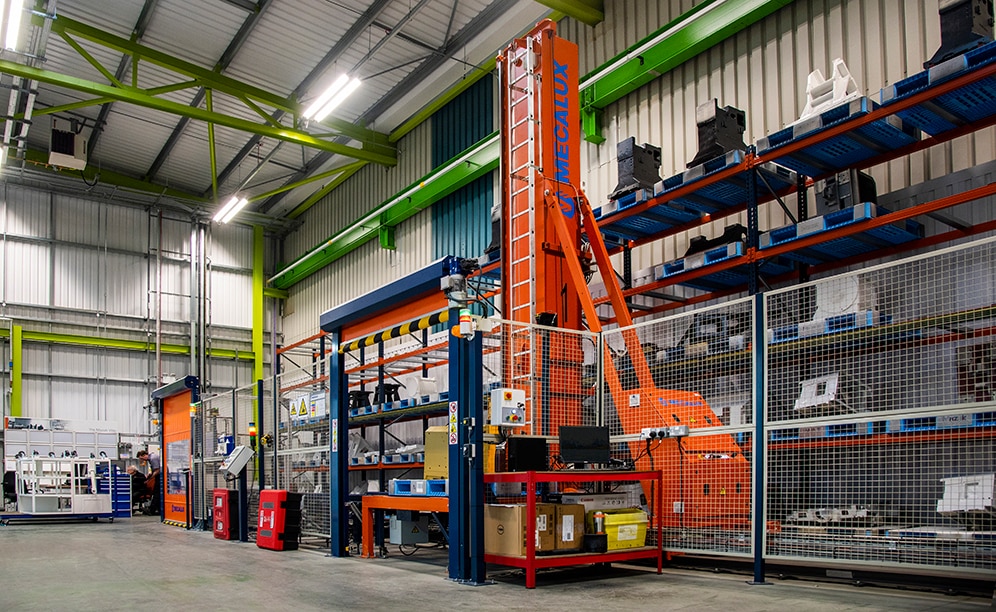
Automated warehouse with Yamazaki Mazak's industrial machinery
Ask an expert