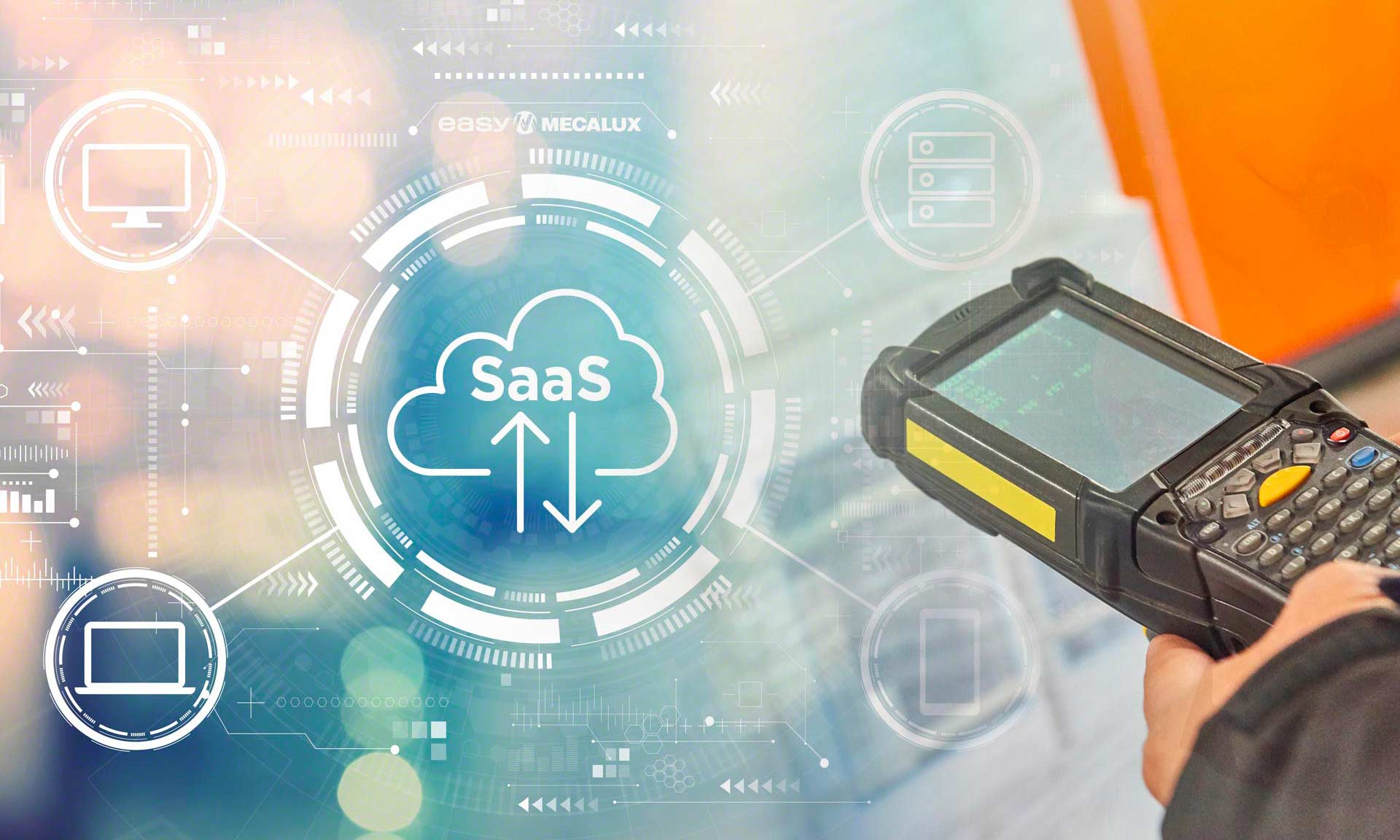
Yamazen: traceability optimizes the supply chain
Traceability of over 5,000 SKUs and total control of Yamazen's supply chain
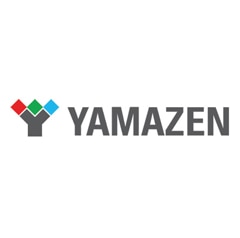
Machine tool importer and distributor Yamazen has opened a new North American headquarters and logistics center in Elk Grove Village, Illinois, with the aim of expanding its storage capacity and improving its customer service. To do so, it has implemented the Easy WMS warehouse management system from Interlake Mecalux in addition to the Slotting module to optimize the placement of goods in the warehouse and the Supply Chain Analytics Software module to control everything that happens in the supply chain.
Evolution and growth
In business in the United States since 1967, Yamazen is a multinational devoted to the sale of machine tools, tooling, and automotive solutions used by renowned manufacturers in the industry to produce precision machined parts. The company is in a constant state of transformation, developing new, increasingly sophisticated high-tech machining solutions to adapt to market demands.
Aside from its headquarters in Japan, the firm boasts an extensive sales network comprising 60 offices and production plants in over 20 countries in Europe, Asia, and North America.
Yamazen arrived in the US in 1967 and, since then, has experienced steady growth. “Our company provides its know-how and solutions to hundreds of companies throughout North America. Our priority is to find the right solution for their needs, which helps us to drive our business forward and increase sales. As a result, we’ve had to expand our demonstration, integration, and logistics facilities,” explains James Hansen, Executive Vice President.
Previously, the company had a headquarter and distribution facility in Schaumburg (IL) that lacked space. It also had major difficulties when it came to properly organizing all the goods and efficiently supplying its 13 points of sale in the US.
Therefore, it decided to move to a new larger center in Elk Grove Village (also in IL). Its demonstration and integration areas, as well as its offices and warehouse, are now housed in a surface area of 138,000 ft2. When commissioning this new facility, James Hansen knew exactly how to improve Yamazen’s logistics systems: “We wanted to optimize all operations and carry out much stricter control of the goods.”
From manual to digital logistics
“In the past, operators would make a note of the products received in the warehouse on a piece of paper; they would then enter that information in an Excel spreadsheet,” says James Hansen. Nevertheless, there was a major drawback to that working method: the probability of error when jotting down or entering the information in the program was very high.
Likewise, product traceability was practically nonexistent. For a long time, the company had wanted to track its goods movements, from the time the products arrived at the warehouse until their dispatch. “As our workload increased, monitoring stock with Excel became less and less viable,” adds James Hansen.
To foster its supply chain performance, Yamazen was convinced that it had to implement a warehouse management system (WMS). After weighing different options, it chose Easy WMS, the WMS from Interlake Mecalux, due to its features and scalability.
“We really liked what we saw in the Easy WMS presentation; it fit the particular characteristics of our business like a glove. With this system, we know the availability of the SKUs and can take inventory in real time. It also seemed like the most user-friendly tool for our operators,” indicates James Hansen.
The Executive Vice President of Yamazen was not wrong. The WMS is designed to optimize operations, especially picking. With the help of a radiofrequency scanner, workers follow instructions from the warehouse management system Easy WMS, making them faster and more efficient. Moreover, the WMS designs routes throughout the warehouse (for storing products or preparing orders, for example) that minimize operator travel.
Interlake Mecalux has also deployed two additional modules that enhance the functionalities of Easy WMS: Slotting, dedicated to organizing goods, and Supply Chain Analytics Software, capable of analyzing the throughput of warehouse operations.
Easy WMS in the cloud
Yamazen has implemented Easy WMS in its cloud-based SaaS (software as a service) mode so that Yamazen operators are able to access Easy WMS from any browser with an internet connection. The data are securely stored on external servers, and the company always has the latest updated version of Easy WMS.
With this modality, Yamazen has improved its logistics processes with minimal investment in terms of software infrastructure. “Eliminating server maintenance tasks is a huge advantage for our IT team,” enthuses James Hansen.
Slotting: merchandise control
Accurate stock management was a crucial step for Yamazen’s supply chain. Proper distribution of the goods prevents operators from wasting time trying to locate each item. Consequently, all warehouse operations are streamlined.
Along these lines, the Slotting module is an extension of Easy WMS designed to determine the ideal location for each product. This app was just what Yamazen needed, as its facility manages 5,000 SKUs of diverse sizes and characteristics: 300 comprise machines stored in large boxes on pallet racks, while 4,700 consist of spare parts in small boxes on picking shelves.
By means of a stock distribution strategy based on rules and algorithms, the Slotting module boosts productivity in the goods receipt, replenishment, and picking processes. The operators merely have to read the barcode of each product with their radiofrequency scanners, and the Slotting module assigns it a location.
In addition to distributing warehouse locations according to the physical characteristics of the goods, this module also takes into account this facility’s main operation: picking. Thus, for example, products with a higher demand level are more accessible to facilitate their entries and exits.
Optimized picking
“Before, employees from different departments in the company would go directly into the warehouse to get the products they needed. They know better than anyone the items they use on a daily basis,” explains the Executive Vice President. This caused stockouts and delays in order prep due to the lack of monitoring.
Now, with the help of Easy WMS, the entire operation is much faster and safer. As Yamazen uses the zone picking method, it is not necessary for the warehouse operators to be thoroughly familiar with all the products stored.
The Yamazen facility prepares three types of orders:
- Machine tools. These orders are dispatched in containers. The operators locate the machine tools indicated by the WMS and bring them directly to the dispatch area.
- Individual spare parts. When a customer requires a specific spare part, Easy WMS shows an operator exactly which location to go to, exactly how many items to remove, and where to deliver the merchandise.
- Tooling and accessories. Generally, customers ordering tooling items request a higher number of products (nearly 100 orders a day, each made up of an average of 20 items). For these cases, batch picking is carried out. Following orders from Easy WMS, operators travel around the warehouse with a cart in which they place all the products.
Once the items for all the orders have been picked, they are sent to the consolidation area to be packaged, labeled. Then, they are moved to the dispatch area, where the packages are grouped by order or transportation route.
Supply Chain Analytics Software: control of operations
“When we installed Easy WMS, we specifically told the Interlake Mecalux team that we wanted it to be capable of controlling our goods and our warehouse operations,” underlines James Hansen.
Therefore, the team deployed the Supply Chain Analytics Software module, a system used to consult and analyze all data relating to warehouse activity by means of indicators: inflows, outflows, order prep, storage capacity, etc. With this information, the company has reliable data and objectives that will help it to make strategic improvements that enhance its supply chain efficiency.
Optimized, controlled logistics
The digitization provided by Easy WMS has made Yamazen’s supply chain more efficient and competitive; the company now has full traceability of all the products stored in its facility.
The Slotting module has enabled Yamazen to leverage its space and, at the same time, speed up picking tasks. Meanwhile, with Supply Chain Analytics Software, the business has the exact information it needs to make the most of its operations.
The result is overwhelmingly positive: a warehouse with maximized productivity and excellent service whose aim is to serve a growing number of customers in the US.
What we like most about Easy WMS from Interlake Mecalux is that it’s so easy to use. Operators merely have to follow the instructions from the WMS step by step to complete their tasks quickly and safely. Another thing we value is the dedication of the Interlake Mecalux technical team, which advised us throughout the entire commissioning process and was able to answer all our questions. The result is a system that meets our needs. Plus, it’s increased our productivity.
Advantages for Yamazen
- Full traceability: Easy WMS monitors Yamazen’s 5,000 SKUs in real time, identifying each item from the moment it arrives at the warehouse.
- Strategic goods distribution: the Slotting module strategically organizes the goods in the facility, fostering increased productivity in picking and better leveraging of space.
- More efficient picking: the WMS sends the operators instructions on how to prepare the orders quickly and without error.
- Easier decision-making: the Supply Chain Analytics Software module incorporates indicators for controlling the way in which the various warehouse operations are carried out. Based on these objective data, logistics managers can make decisions for improvement.
Ask an expert