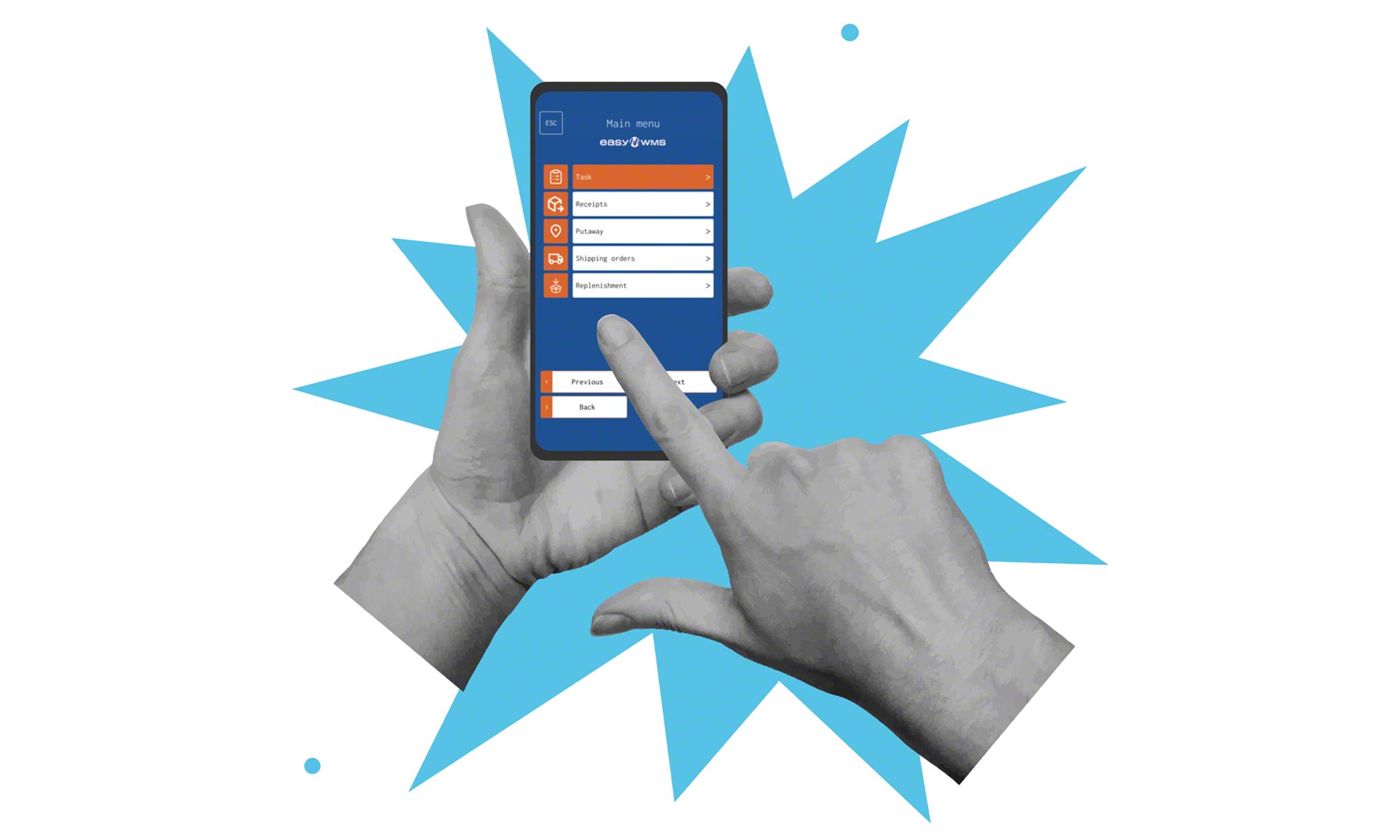
Easy WMS warehouse management software empowers Manufast workers
The Belgian logistics service and data management company has digitalized the management of 7,200 client SKUs.
The Manufast Special Employment Center, located in Brussels, provides logistics and document management solutions. With 270 workers, the company embraces digitalization as al asset in the world of e-commerce.
About Manufast
Manufast is a Special Employment Center located in Brussels (Belgium). It employs over 270 people, 170 of whom have some form of disability. The excellent work of its staff in areas such as printing, packing, logistics services, and document management has earned the trust of a diverse range of clients over Manufast’s 60-year history. With its integrated, tailored solutions increasingly valued, the company has embraced digitalization as a key asset in the demanding world of e-commerce.
CHALLENGES
|
SOLUTIONS
|
BENEFITS
|
---|
Manufast’s goal is to ensure employment opportunities for people with disabilities in the Brussels (Belgium) area. To achieve this, the business has fully embraced e-commerce, digitalizing all operations relating to document services, printing, logistics, and packaging. To facilitate this transformation, Manufast implemented specialized warehouse management software.
With 7,200 SKUs in stock and without the need to use paper packing lists or memorize locations, Manufast’s 270 employees have become unstoppable. “Easy WMS allows us to control and optimize all processes in our warehouse. Moreover, it has boosted our storage capacity and eliminated paper-based management,” says Vincent Mullender, Process Improvement Manager at Manufast. Mecalux’s Easy WMS warehouse management system has completely overhauled the way this team of individuals of various ages and social and cultural backgrounds works.
Until now, Manufast had been using a standard ERP system to oversee its inventory. Nevertheless, its limitations were evident in areas such as multi-product management, expiration-date monitoring, receiving processes, and other stock-related operations. According to representatives from the Process Department: “We used to prepare orders using paper packing lists. But this led to problems linked to reading the documents and tracking backorders.” All Manufast services — which involve packaging and distributing goods as well as scanning and processing client documents — relied on visual recognition.
As Manufast serves a growing number of e-commerce customers, it needed a tool to control its inventory, replenishment, and order fulfillment. Operators had become highly specialized in their particular areas, underscoring the need to digitalize locations, items, and quantities for every SKU using barcodes. Now, Easy WMS sends precise instructions to each warehouse worker’s RF scanner.
A process free from human errors
Easy WMS centralizes orders and information from suppliers, showing each operator where to go. As a result, workers no longer have to memorize locations in the facility. “The process leaves almost no room for human error: it involves double — practically triple — verification before handling each item. Mistakes have decreased dramatically,” says Mullender. First, the scanner directs the operator to a specific point in the warehouse. Next, it prompts the employee to scan the product code. Once the correlation is verified, it indicates the quantities to retrieve.
With the Manufast facility operating in an organized manner, its clients can monitor the status of their merchandise with Easy WMS’s 3PL Client Portal. “Manufast wanted to offer users complete and real-time visibility of the operations we carry out for them,” says Mullender. To that end, Mecalux provided the Belgian company with the necessary training to implement this system. “Gaining autonomy is crucial for our group, as our strengths are flexibility and execution speed. If a client provides us with information on its stock, we can begin managing it within a very short time.”
Manufast clients also have the opportunity to use the transportation agency of their choice via Easy WMS’s Multi-Carrier Shipping Software. The module generates a specific label for each one. “All configurations are possible, whether with FedEx, DPD, a Belgian carrier like Bpost, or other private transportation companies,” say representatives from the center.
Digitalization: an e-commerce asset
Six decades after its inception, and supported by Easy WMS, Manufast has entered the e-commerce sector. Furthermore, the software has facilitated business growth without requiring major changes to the company’s equipment or processes. Manufast can now manage the arrival of two or three shipping containers a day. It can also effectively meet the demands of business-to-business (B2B) companies worldwide, shipping 95% of orders on the same day they are received. With Easy WMS in the SaaS (software-as-a-service) model, Manufast handles an average of 300 daily shipments along with seasonal peaks such as Black Friday.
“Easy WMS only requires a good internet connection; we haven’t had to install anything at our headquarters or on our clients’ premises. Users can access information on their operations from any computer. All they have to do is log in to the app,” says Mullender.
By standardizing processes, Easy WMS has increased our storage capacity and eliminated paper-based management.
Ask an expert