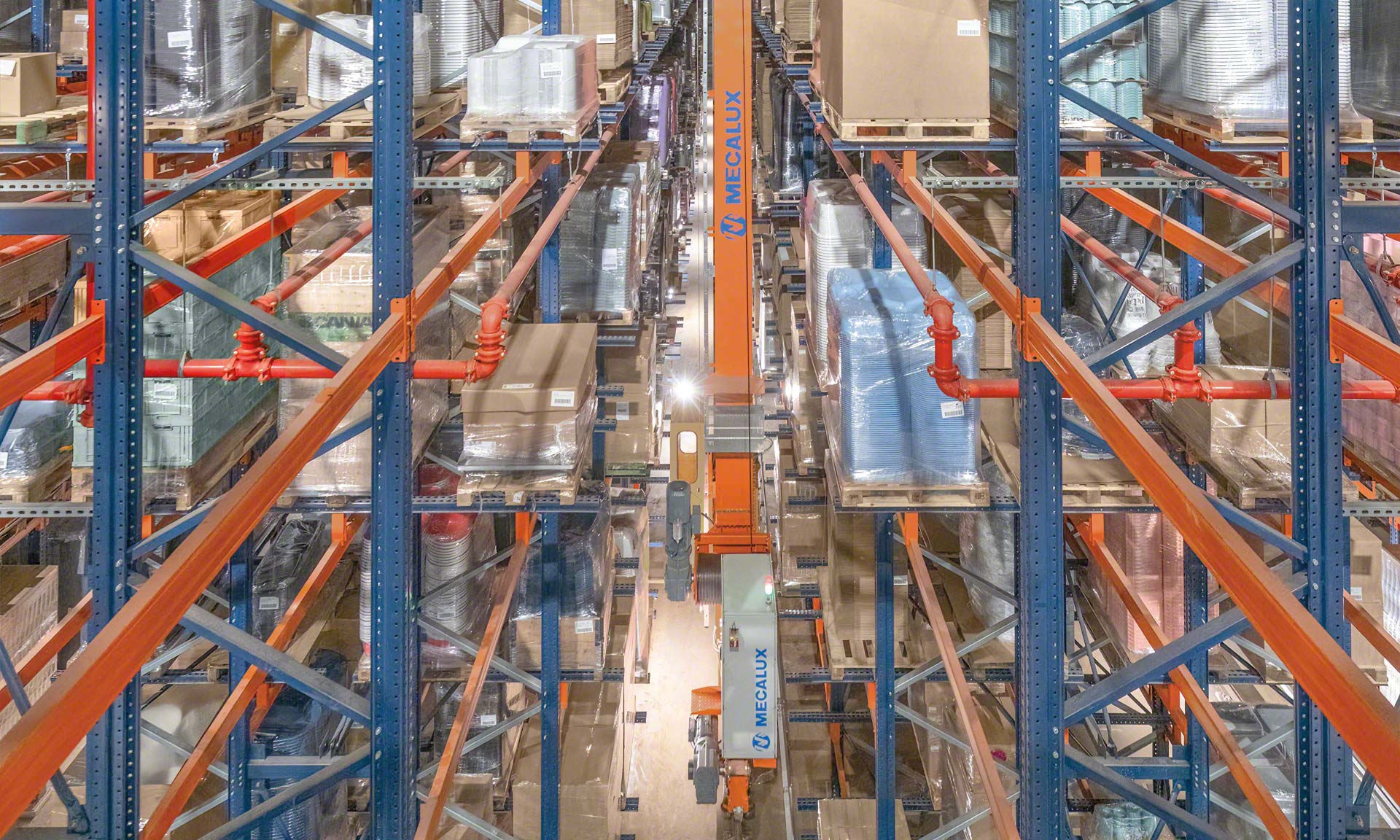
Moderna Products automates the storage of plastic pet supplies
The automated warehouse from Mecalux has increased the Belgian company’s storage capacity fourfold.
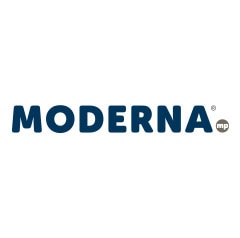
Moderna Products, a pet supply manufacturer, has built a new production center in Izegem (Belgium) and a 131' high automated rack-supported building. Managed by Easy WMS, the warehouse has quadrupled the company’s storage capacity to support the increase in production.
Moderna Products: innovative and practical pet solutions
Founded in 1932, Moderna Products is a third-generation, family-owned company headquartered in Belgium and with a second production facility in the US. Moderna proudly “creates smart plastics for happy pets” available as the Moderna brand as well as private labels. With a major focus on sustainability, illustrated by the Moderna Green Pact, Moderna’s products are available today in more than 79 countries.
CHALLENGES
|
SOLUTIONS
|
BENEFITS
|
---|
Moderna Products is ready to take on the future with the commissioning of its state-of-the-art facilities in Izegem (Belgium). The business, which manufactures all sorts of pet products, aims to double its sales over the next five years through process automation.
“We make plastic injection molded pet products at two large production centers in Belgium and South Carolina. We export to 79 countries from the Izegem site, while the South Carolina plant supplies the US, Canadian, and Mexican markets. We’re proud to say we manage the entire supply chain, spanning product development, production, storage, and distribution,” says Bart Bonte, owner and CEO of Moderna Products.
The company decided to relocate to an entirely new site in Izegem to increase its production volume and affirm its clear commitment to a more humane, sustainable, and resilient Industry 5.0. “We invest in the most advanced technologies to be more competitive. Our priority is for our storage and production systems to be highly energy efficient, ensuring that the return on investment makes sense,” says Bonte.
In the Belgian production plant, the new automated warehouse from Mecalux has quadrupled the business’s storage capacity. The rack-supported building measures 328' long by 131' high, accommodating 12,560 pallets. Robotic storage and internal transport systems automate the movement of around 1,500 pallets per day containing pet products. “Automation was the logical step. Our logistics processes had to align with the robotic advancements already underway in our production process. We opted for automation to expand our space, enhance safety, and make our processes more environmentally friendly. Consequently, we've achieved a level of efficiency where traditional lighting is no longer necessary.”
Mecalux’s Easy WMS warehouse management system oversees all logistics operations and monitors stock. The automated storage and internal transport systems, coordinated by Easy WMS, shorten Moderna Products’ response times. “Digitalization is fundamental in our daily activities. We’re currently undergoing a complete transformation. Our goal is to monitor every step taken, from the receipt of orders to their shipment. Product traceability is an essential factor, for both us and our customers,” says Bonte.
Technology to supply production for Moderna Products
The automated warehouse has marked a before and after in Moderna Products’ logistics operations. “We’ve seen a major transition in our way of working. Now, we simply put the pallets on the conveyor, and it automatically transports them to the warehouse,” says Amber Bauwens, Supply Chain Manager at Moderna Products. “Robotics has made our operations much more efficient while minimizing human errors. Process automation has also provided us with greater flexibility.”
The automated facility fulfills two functions. On the one hand, it supplies the production lines with accessories and semi-finished products. On the other, it stores all finished manufactured goods coming directly out of the manufacturing plant. “When a pallet leaves production, its information and barcode are recorded in our SAP ERP system and Easy WMS. Thus, the automated warehouse knows in advance all the goods it will receive, and the software can manage the best putaway strategy,” says Bauwens.
Automation, the backbone of the facility, ensures continuous flows of goods. Five twin-mast stacker cranes handle pallet movements inside the storage aisles. Meanwhile, a conveyor system transports pet products to the production and picking areas.
Moderna Products achieves on-time shipments
At one end of the automated warehouse, there is an adjoining building divided into two floors. Order picking is performed on the upper level, while the lower floor is allocated to shipments. The picking area is designed to fulfill orders following the goods-to-person method. The automatic handling equipment brings the operators the items they need to put together shipments.
“Picking is completely digitalized. The operators receive instructions from Easy WMS on their RF scanners and place the correct quantity of products in each order. To avoid errors, they scan the barcodes on the pallets as well as the locations,” says Bauwens. “We also use this area to prepare mixed orders incorporating various SKUs to meet our customers’ diverse needs.”
A lift automatically lowers the products from the picking area to the ground floor. A conveyor line moves each pallet to one of the outlets assigned by Easy WMS. The Mecalux system organizes and classifies the pet products sequentially, taking into account the type of order and transportation route. For example, pallets to be delivered on the same route are placed on the same conveyor line.
By optimally organizing its goods dispatch zone, Moderna Products can now ship pallets to its customers more quickly.
Digital transformation of Moderna Products with Easy WMS
“Digitalization enables us to use historical data from the time we place orders with our suppliers to the delivery of our products to customers. The same occurs with our production processes. Everything is logged via the SAP ERP system and Easy WMS,” says Bauwens.
With the Mecalux warehouse management software, Moderna Products has boosted productivity in its facility. It has seen significant improvements in process and inventory control. “Easy WMS enhances our efficiency. The main advantage is that we have a real-time view of the tasks we’re performing. At any given time, we know exactly how much stock we have of raw materials, semi-finished products, and finished goods. This helps us maintain the necessary inventory levels at any point along the logistics chain and, as a result, streamlines production planning,” says Bauwens.
I recommend that all companies install Easy WMS — regardless of their sector. It offers a real-time view of inventory and features multiple functionalities to optimize operations.
Moderna Products has also installed the WMS for Manufacturing module to integrate the warehouse with the production lines and gain end-to-end traceability of its raw materials. “Easy WMS improves the degree of inventory accuracy, so we can organize production more efficiently. The system also ensures traceability: it knows the location of all SKUs and is tracking the movement of every pallet,” says Bauwens.
Moderna Products invests in a future-ready Industry 5.0
Moderna Products has experienced unabated growth in recent years. The Belgian company has transitioned from exporting its merchandise to neighboring countries to doing so to more than 79 countries. Additionally, in 2016, it opened a production plant in the US.
Thanks to automation and digitalization, Moderna Products benefits from an advanced supply chain. The innovative facilities in Izegem are equipped with a personalized solution tailored to the business’s requirements. The result? More efficient logistics operations that align with the principles of Industry 5.0.
Mecalux provided us with a turnkey solution. It was important for us to have a reliable go-to partner who could supply everything we needed, both on the hardware and software side.
Gallery
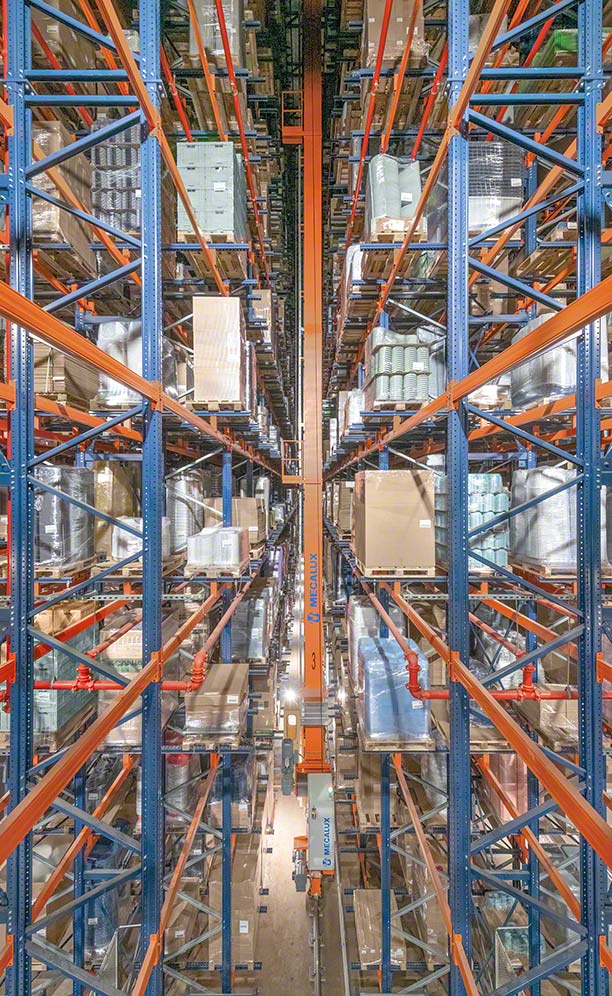
The automated warehouse has capacity for 12,560 pallets managed by Easy WMS
Ask an expert