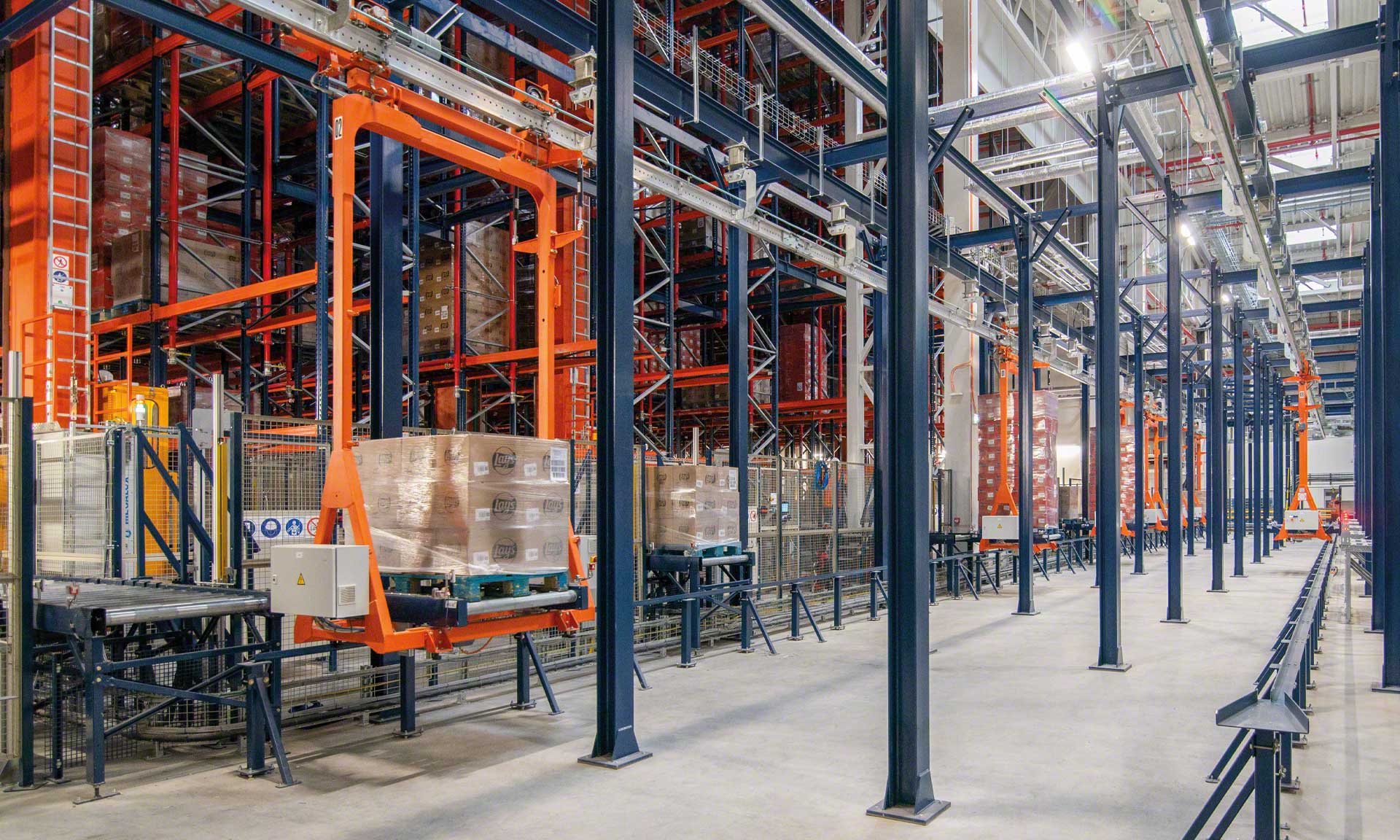
PepsiCo installs its first automated warehouse in Poland with Mecalux
The multinational beverage and snack company has automated its facility to distribute thousands of pallets containing potato chips.
PepsiCo, a global leader in food and beverages, has installed its first automated warehouse in Poland, its most sustainable in Europe. Automation facilitates production with the push system, which involves manufacturing in advance to meet anticipated demand.
PepsiCo: global leader in its industry
PepsiCo is one of the world’s largest food and beverage companies. Its wide range of products includes iconic brands such as Pepsi, Frito-Lay’s, Gatorade, Tropicana, Quaker, and Doritos. Present in more than 200 countries, the multinational is known for innovating its production and logistics processes and implementing advanced technologies in its plants and warehouses. Moreover, PepsiCo has shown a growing commitment to sustainability, investing in practices that reduce the environmental impact of its operations and promote a responsible supply chain.
CHALLENGES
|
SOLUTIONS
|
BENEFITS
|
---|
PepsiCo, a worldwide leader in the food and beverage industry, continues to expand into new markets while strengthening its presence in existing ones. This is evident in Poland, where it has operated five production centers since 1991. Thirty years later, it has implemented its first automated storage and retrieval system (AS/RS) at its new plant in Środa Śląska, PepsiCo’s most sustainable in Europe. “The water used in our processes is given a second or even a third life thanks to a system that allows for the repeated use of tap water and the treatment of rainwater. We also plan to launch our own photovoltaic farm with a capacity of 3.5 MW,” says Maciej Pietrusa, Warehouse Manager at PepsiCo Poland in Środa Śląska.
The facilities — covering an area the size of seven soccer fields — “produce bags of potato chips and snacks for the European market, primarily Germany,” says Pietrusa. Every year, the PepsiCo plant receives 66,000-plus tons of potatoes to manufacture Lay’s and over 16,500 tons of corn to make Doritos chips.
The facility was designed in line with the push system, which involves manufacturing in advance to meet anticipated demand. While this method reduces unit costs, it requires sufficient space to manage large production runs. With 9,000 locations, PepsiCo’s new finished goods warehouse receives a large number of pallets daily, loaded with ready-to-ship bags of potato chips for clients. “The production process is fully integrated with the automated warehouse. Each potato chip bag is transported from the manufacturing area to final packaging, ready to be picked and loaded onto the truck,” says Pietrusa.
The Easy WMS warehouse management system is connected with PepsiCo’s SAP ERP software to ensure facility operations are carried out automatically. Direct, bidirectional communication between the WMS and ERP systems is key to synchronizing the machines installed in PepsiCo’s plant and organizing inbound and outbound orders.
3,500 pallets moved per day
“We’ve built our most modern plant in Europe. Automation has brought us major benefits, including standardized production and logistics processes, 24/7 operation, peak efficiency, and complete product traceability,” says Pietrusa.
PepsiCo’s first automated warehouse in Poland balances storage capacity with agility. “The four stacker cranes from Mecalux ensure 3,500 continuous movements a day. Plus, automation has eliminated human errors in logistics processes, optimizing costs.”
Transporting goods internally between storage and production is now faster thanks to electric monorail and conveyor systems for pallets. These solutions also connect the warehouse with the docking area, facilitating the shipment of thousands of pallets a day. The electric monorail deposits pallets ordered by clients into five double-channel gravity flow conveyor lines. Each channel has a 34-pallet capacity. SKUs are grouped according to delivery route, vehicle type, client, and shipping priority, among other factors.
PepsiCo–Mecalux partnership
Mecalux’s storage systems are helping to optimize PepsiCo’s supply chain in Europe. “The positive experience we had with Mecalux when building and commissioning our warehouse in Środa Śląska convinced us to work with them again for our factory in Veurne, Belgium,” says Pietrusa.
The Warehouse Manager at PepsiCo Poland in Środa Śląska explains the company’s decision: “Mecalux is an end-to-end AS/RS provider, offering both hardware and software. It meets our requirements in terms of technology, safety, and project execution timeliness.”
We’ve built our most modern plant in Europe. Automation has brought us major benefits, including standardized production and logistics processes, 24/7 operation, peak efficiency, and complete product traceability.
Gallery
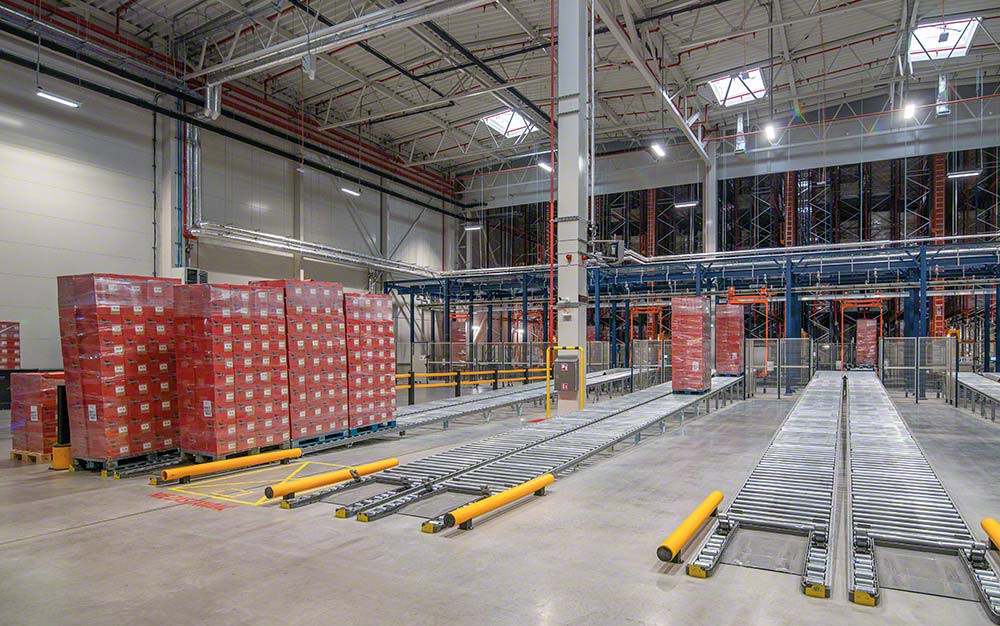
Easy WMS controls the movements of PepsiCo’s pallet stacker cranes
Ask an expert