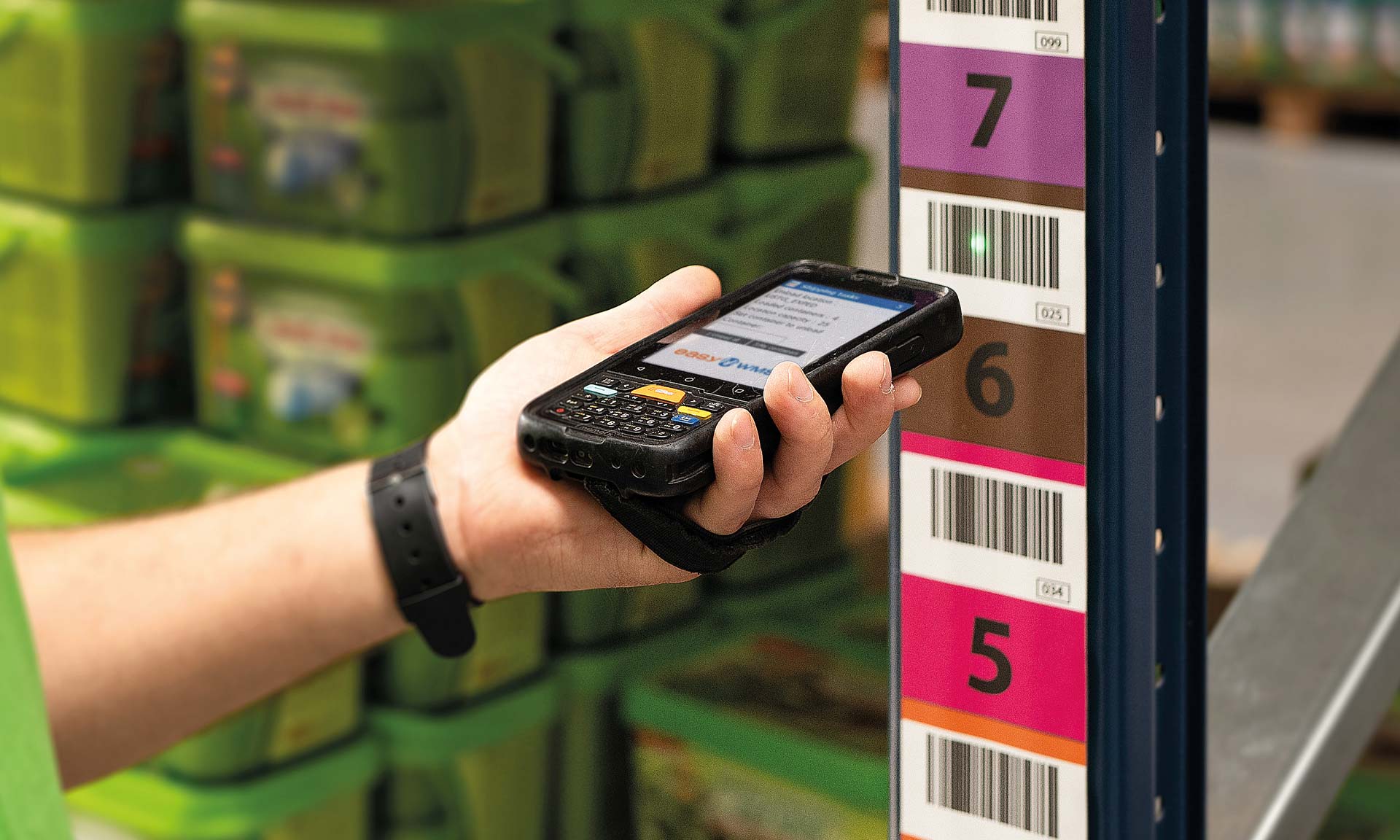
Planta optimizes operations in its warehouse in Poland
Gardening products distributor Planta improves its working culture with Easy WMS.
Planta, a distributor of gardening products for wholesalers and specialized stores, has installed Mecalux’s Easy WMS in its facility in Poland. The greatest advancement the company has seen with Easy WMS is in warehouse location management: the program tracks the status of 2,300 SKUs in real time.
Planta: everything under the sun for gardeners
Planta is one of Poland’s largest businesses in the agricultural and gardening sector. Based in the city of Tarnów, the company supplies wholesalers and specialized stores. Planta produces fertilizers, manufactures technical textiles for agriculture, distributes flower bulbs and seeds, and sells accessories, tools, furniture, and other items for gardening. Planta’s priority is to provide its customers with efficient service and top-quality products. Founded in 2002, Planta is present in Germany, Bulgaria, Czechia, Slovakia, Latvia, Lithuania, Montenegro, Poland, Portugal, and Romania.
CHALLENGES
|
SOLUTIONS
|
BENEFITS
|
---|
Improving operations is the goal of any company that digitalizes its logistics processes. With this aim, gardening products distributor Planta has implemented Mecalux’s warehouse management system in its facility in Wojnicz (Poland).
“We opted to digitalize our logistics operations with Easy WMS due to the expansion of our business. Currently, our annual turnover stands at more than 80 million złoty, which is a significant achievement for us. Plus, we manage a growing number of SKUs — over 2,300 now — and sales are progressing well,” says Piotor Sygnarowicz, Chairman of the Board at Planta. “Due to seasonal sales fluctuations and new hires, the previous solution fell short of our needs, particularly during peak demand periods. It required a lot of staff, complicated inventory management, and lacked certain capabilities that were becoming indispensable.”
Planta began using its enterprise resource management system (ERP) to coordinate warehouse operations. “The ERP was limited to creating lists of pending orders, organizing priorities, and coordinating the distribution of completed orders. It lacked features for managing product locations within the facility,” says Sygnarowicz. Therefore, Planta decided to implement a specific software program to meet its needs. “We installed a more sophisticated, advanced digital solution to upgrade the capabilities of our distribution center, which has now reached a capacity of over 4,500 pallets.”
Storage processes under control
Easy WMS has improved the working culture in Planta’s facility. The software tracks the status of the gardening products in real time and organizes the various tasks, issuing operators instructions via RF scanners.
“Implementing Easy WMS has enhanced order in our warehouse. One of the aspects we most like about this solution is that it resolves incidents instantly. Before, these issues were often put off until they were eventually resolved,” says Sygnarowicz.
Easy WMS has expedited operator tasks and facilitated the onboarding of new employees. “Our business is highly seasonal. We experience demand peaks in the spring, requiring us to hire more staff temporarily. We wanted a user-friendly software program for our team. Now, we can train new workers in just a day, including those without prior experience. That’s a huge advantage for our company,” says Sygnarowicz.
Delay-free international shipments
Every day, Planta’s warehouse receives over 100 pallets. They contain gardening products sent by European and Asian countries as well as Australia, New Zealand, and the US. Operators read the barcode of each pallet, and the software shows them where to slot it. Then, workers fulfill more than 140 orders a day — each containing multiple items — which are delivered to customers in Poland and other countries.
“For us, the greatest advancement we’ve seen with Easy WMS is in location management. Thanks to this software, we know exactly where to find each item, which is critical for our business. Operators don’t have to remember where every SKU is stored. All they need to do is follow the path indicated by the program,” says Sygnarowicz.
The Mecalux software adapts to Planta’s changing requirements, such as processing larger numbers of orders during peak season. “Operations have become much more organized, efficient, speedier, and transparent. This is reflected in the warehouse staff’s working hours,” says Sygnarowicz.
Drive for continuous improvement
Planta is a company firmly committed to continuously improving its logistics processes. “Like many businesses, we’ve overcome a challenging period caused by the pandemic. However, optimizing our warehouse has enabled us to supply our customers without interruption. Now, we’re continuing to explore ways to boost our supply chain. We’re analyzing the situation and getting ready to apply new measures to raise our competitiveness. These involve expanding our facility, using automation equipment, and reorganizing our logistics operations,” says Sygnarowicz.
By digitalizing its warehouse with Easy WMS, Planta has optimized its operations and laid the groundwork for further supply chain developments and improvements. With a focus on innovation, the gardening products distributor is prepared to tackle new challenges and seize future opportunities.
With Easy WMS, we can train new workers in just a day, including those without prior experience. That’s a huge advantage for our company.
Gallery
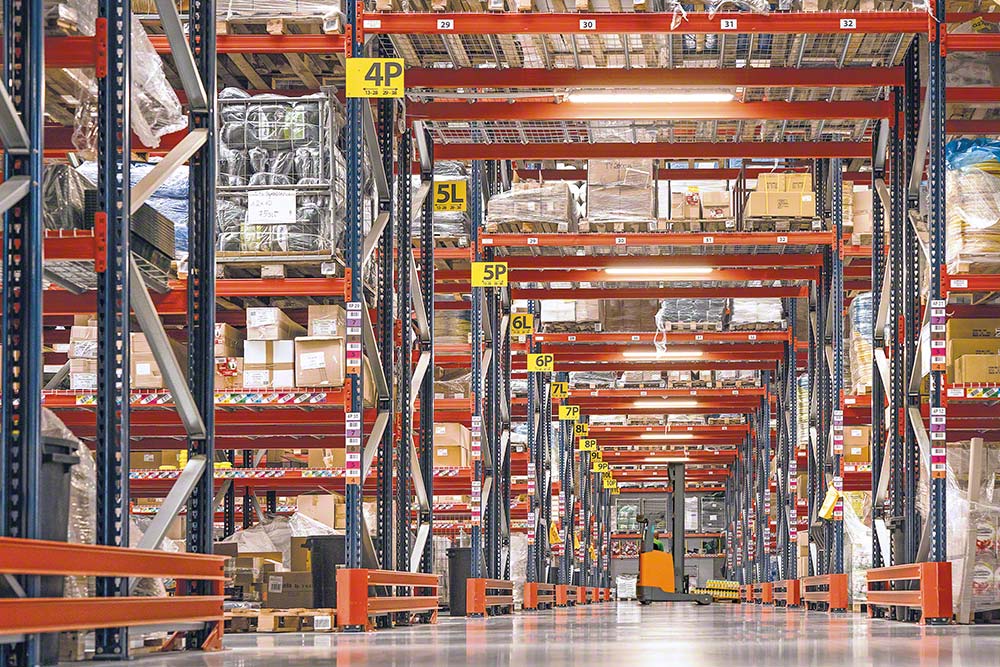
Easy WMS monitors the status of Planta’s gardening products
Ask an expert