
Blechwarenfabrik: Europe's most modern metal packaging plant
Blechwarenfabrik, an aluminum can manufacturer based in Limburg, Germany, integrates all its production and logistics processes in a new, fully automated, digitized center spanning 15.6 acres.
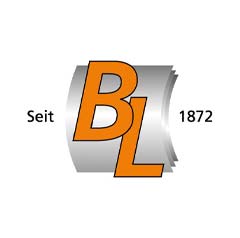
Can and metal container manufacturer Blechwarenfabrik has opened its new headquarters in Offheim, Germany, where it produces over 100 million units a year. The center's two automated warehouses are connected to production by Mecalux's Easy WMS, which organizes the movement of raw materials.
Blechwarenfabrik: tradition and innovation
Blechwarenfabrik is a leading European manufacturer of metal cans and containers used in multiple industrial sectors (mainly for storing and handling chemical products).
- Founded in: 1872
- No. of employees: 500
- Production capacity: over 100 million metal packaging units a year
- Manufacturing plants: Germany, Denmark, Russia and Poland
CHALLENGES
|
SOLUTIONS
|
BENEFITS
|
---|
Blechwarenfabrik, a European benchmark in the manufacture of metal packaging for chemical products, has automated and digitized its logistics processes to cope with increased sales.
The company has a 5.4-acre facility in the Offheim suburb of Limburg, Germany, where all goods movements are completely automatic: automated guided vehicles (AGVs) connect the two automated warehouses to the production lines.
The business used to have two production plants in Germany where it manufactured metal packaging. However, its logistics operations were outsourced due to a lack of storage space. “Raw materials were deposited in the main warehouse, and once the final product left the production lines, it was moved to a facility three miles away,” says Christoph Weber, Technical Manager at Blechwarenfabrik.
Determined to reduce costs and centralize all its logistics processes in a highly digitized and sustainable space, Blechwarenfabrik embarked on its most ambitious project to date: the construction of a new headquarters in Offheim (Limburg), where it now conducts all its business activities. This modern facility is home to the company’s offices, 25 production lines, and a storage area. The production center processes 24,250 tons of steel annually to make 100 million packaging units.
The centralization of the logistics and manufacturing processes was done in stages since some production phases had to be reconfigured and adapted to the new location. Blechwarenfabrik’s management worked closely with the Mecalux technical team to come up with a customized solution. “A project of this caliber isn’t easy to carry out because many details had to be considered. With Mecalux by our side, moving all our logistics operations to the new center was seamless,” says Weber.
Robotics for enhanced efficiency and sustainability
Blechwarenfabrik was clearly set on taking an Industry 4.0 approach, equipping itself with technology that would integrate manufacturing and logistics automatically. “Before, we managed operations and goods movements manually. Operators supplied production using forklifts. And our facilities were divided into different floors, which complicated internal logistics operations,” says Weber.
Now, manufacturing and storage are on the same floor, and up to 15 AGVs move products from one point of the center to the other with minimal operator intervention. The robots receive instructions from the warehouse management system (WMS), which tells them where to take the products. “We’ve automated goods management, from product entry to order dispatch. In partnership with Mecalux, we’ve built the most modern metal packaging plant in Europe,” says Weber.
Minimizing the environmental impact of manufacturing and logistics processes has always been one of Blechwarenfabrik’s main concerns. By bringing all its processes under one roof and thus avoiding the transfer of goods between production plants and warehouses, the company expects to cut its polluting gas emissions by 2,870 tons per year.
The Blechwarenfabrik plant also has an area where metal waste generated during the various industrial processes is collected for recycling. Likewise, 4,100 solar panels have been installed on the center’s roof to generate the energy used in manufacturing and storage processes.
Logistics and production: seamlessly connected with Easy WMS
Blechwarenfabrik’s new plant features two automated storage and retrieval systems (AS/RS). The one for raw materials is inside the facility, while the other consists of a rack-supported building to store finished products. Rack-supported buildings are formed by the racks themselves, which support their own weight in addition to that of the vertical cladding, the roof, and the goods stored in them. Mecalux has also implemented its warehouse management software, Easy WMS, which manages and optimizes all processes between the two AS/RS.
“Integrating manufacturing and logistics was one of the biggest challenges of this project. We did it by gradually moving our production processes to the new center. This way, we were able to analyze and resolve issues as they arose,” says Uwe Wonsack, Operations Manager at Blechwarenfabrik.
To effectively combine logistics and manufacturing, the company employs Easy WMS software. The Mecalux program connects with Blechwarenfabrik’s enterprise resource planning (ERP) system, Infor, and its manufacturing execution system (MES) to know which items are needed in production and organize their distribution. “The programs support each other. If we’re looking for information on products, Easy WMS gives us all the details, including the available quantities and exact locations,” says Wonsack. The ERP system, meanwhile, connects with the other software involved in manufacturing processes, such as the program that manages the palletizing robots used in production, the one that collects data on the performance of plant operations, and the one that organizes, controls, and monitors these operations.
Easy WMS also communicates with the AGV control software to organize goods movements between the AS/RS and manufacturing. “The AGVs supply the production lines automatically. When Easy WMS receives an order from production, the software organizes picking in the AS/RS. The AGVs collect the materials and move them to the line that requested them. The process is transparent, fast, and efficient,” says Wonsack.
The Mecalux software also manages waste in the Blechwarenfabrik facility. As waste is generated in the manufacturing processes, Easy WMS orders it to be sent to the recycling zone.
Warehouse management software: rigorous traceability
Easy WMS from the Mecalux Group is a tool that provides total traceability of products stored. The program monitors goods comprehensively, from the receipt of raw materials to dispatches of finished products. Connecting Blechwarenfabrik’s manufacturing and logistics processes with Easy WMS has brought the company multiple benefits:
- Real-time stock visibility and management. Easy WMS knows the status and exact locations of the goods, including raw materials and finished products.
- Just-in-time production support. The software makes sure that raw materials are sent to manufacturing processes in the right quantities and at the right time.
- Item master and bill of materials management. Each production order lists the raw materials needed to make the goods.
- Enhanced manufacturing processes. Well-organized operations and accurate product control result in greater effectiveness and agility.
- Paperless processes. Operators request the raw materials they need via RF scanners or tablets.
“The biggest change we’ve seen with Easy WMS is in stock control; now, we know where every single item is at all times,” says Wonsack. Inventory control has allowed Blechwarenfabrik to better organize its goods, hence streamlining operations. Order is essential for this company to supply its production lines just in time.
Fully automated supply chain
Blechwarenfabrik knew automation would bring down costs and improve the performance of its supply chain. The company has optimized and streamlined its storage, picking and dispatch processes.
Stacker cranes, pallet conveyors, and AGV robots ensure continuous, controlled goods movements. Every day, 600 pallets containing raw materials are sent to the production lines. Another 1,200 pallets with approximately 500,000 metal cans and containers are collected from the production lines, stored and made available for shipment to hundreds of Blechwarenfabrik customers throughout Europe.
➤ AS/RS for raw materials
Standing 36’ tall by 328’ long, the AS/RS is made up of two aisles with single-deep racking on both sides. The racks can hold up to 2,500 pallets with the metal sheets used to manufacture cans.
The AS/RS receives an average of 125,000 metal sheets a day sent by Blechwarenfabrik’s suppliers. In permanent contact with the MES software, the first thing Easy WMS does when organizing inflows is to order the sheets to be deposited on the correct pallet and in the right position. Depending on the item to be manufactured on the production lines, each sheet should be placed in a certain position on the pallet.
“Goods are organized following the FIFO (first in, first out) method. This prevents products from becoming obsolete and guarantees that we have continuous material flows,” says Wonsack.
To ensure that the production lines are supplied with the necessary goods, Easy WMS checks the number of sheets needed for each order and the required position. If those quantities are not available, other sheets are picked in the warehouse and moved to the pallet inverter, where operators are instructed on how to correctly position the sheets. As directed by Easy WMS, the AGVs pick up the sheets at one of the two AS/RS exit points and automatically take them to pallet racks near the production lines. These racks act as a buffer, storing raw materials temporarily until they are used on the production lines. Once the location has been emptied, it can once again be used to hold another item for a subsequent manufacturing order.
➤ Production lines
At the start of the manufacturing process, Easy WMS directs the AGV robots to send the raw materials and semi-finished goods to the corresponding lines.
Can bodies are one of the semi-finished products included in production orders. Instead of being stored in an AS/RS, these parts are directly deposited on pallet racks next to the production lines. Easy WMS also monitors these materials and orders them to be sent to manufacturing just in time.
In production, operators communicate with Easy WMS to request empty pallets, report defective stock or return surplus raw materials to the warehouse, for instance.
“For us, production line operators should be able to focus on their main job as opposed to doing secondary tasks. Using an RF scanner, these operators can easily order the items they need from Easy WMS,” says Wonsack.
Following commands from Easy WMS, the AGVs also pick up waste and automatically move it to the recycling area.
➤ Finished products warehouse
With capacity for 18,000 pallets, the rack-supported building stands 102’ tall and consists of four aisles with double-deep racking on both sides.
Every hour, around 80 pallets arrive from the production lines. Before entering the warehouse, these products go through a pallet checkpoint to verify that they meet the requirements established for storage on the racks.
Next, Easy WMS allocates each product a location. The software incorporates rules and algorithms to decide on the best slot for each pallet taking into account its SKU and turnover.
In terms of dispatches, the ERP system notifies Easy WMS of the pallets to be distributed. The WMS then assigns each outgoing order a loading dock. Every hour, 100 pallets are sent from this facility to the picking area or directly to the docks. “Our dispatch processes work perfectly,” says Wonsack.
A pick station has been set up in the front of the building. There, operators fill orders following the goods-to-person method. In other words, they remain at their workstation as the products they need are brought to them. Operators remove boxes from the pallets arriving from the warehouse. They then deposit the boxes on another pallet where all the items in the order are grouped.
These workers are equipped with a screen and RF scanners to follow Easy WMS’s instructions step by step. With these devices, operators always know which products to pick from the pallets and which orders to place them in. Consequently, Blechwarenfabrik has minimized the possibility of making mistakes.
Pallets sent directly to dispatch are labeled and transported to the corresponding dock. Additionally, a preload area has been set up on the floor. Here, pallets are grouped and classified by order and transportation route for faster loading on the distribution truck.
Industry 4.0 for efficiency and sustainability
Through technology, Blechwarenfabrik has boosted its performance, ensuring its continued growth. The business has embraced Industry 4.0 to control its processes more rigorously and improve its customer service.
Automation has enabled Blechwarenfabrik to increase its throughput, manufacturing more than 100 million packaging units a year. Moreover, it has made the company’s supply chain more sustainable. With the automated solutions and Easy WMS from Mecalux, Blechwarenfabrik’s supply chain is now interconnected.
The software coordinates all processes with the aim of serving the production lines just in time. Digitization and automation are a winning combination for Blechwarenfabrik and will surely support the company in its future success.
When we opened the new plant in Offheim (Limburg), it was clear that our facility had to be automation-driven. With the technology of our partner Mecalux, our supply chain has taken a huge leap forward.
Gallery
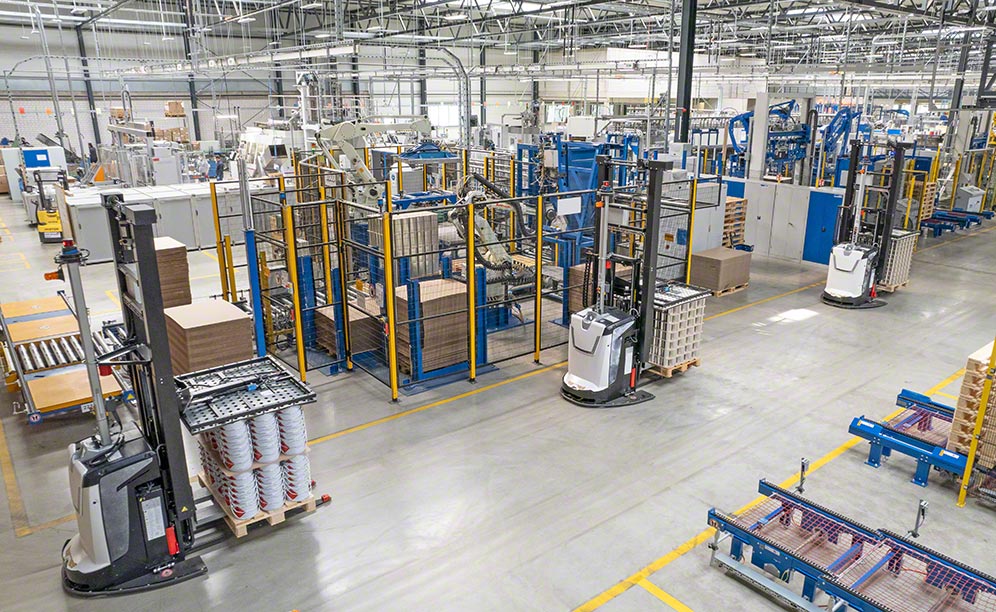
Blechwarenfabrik's AS/RS for raw materials in Limburg, Germany
Ask an expert