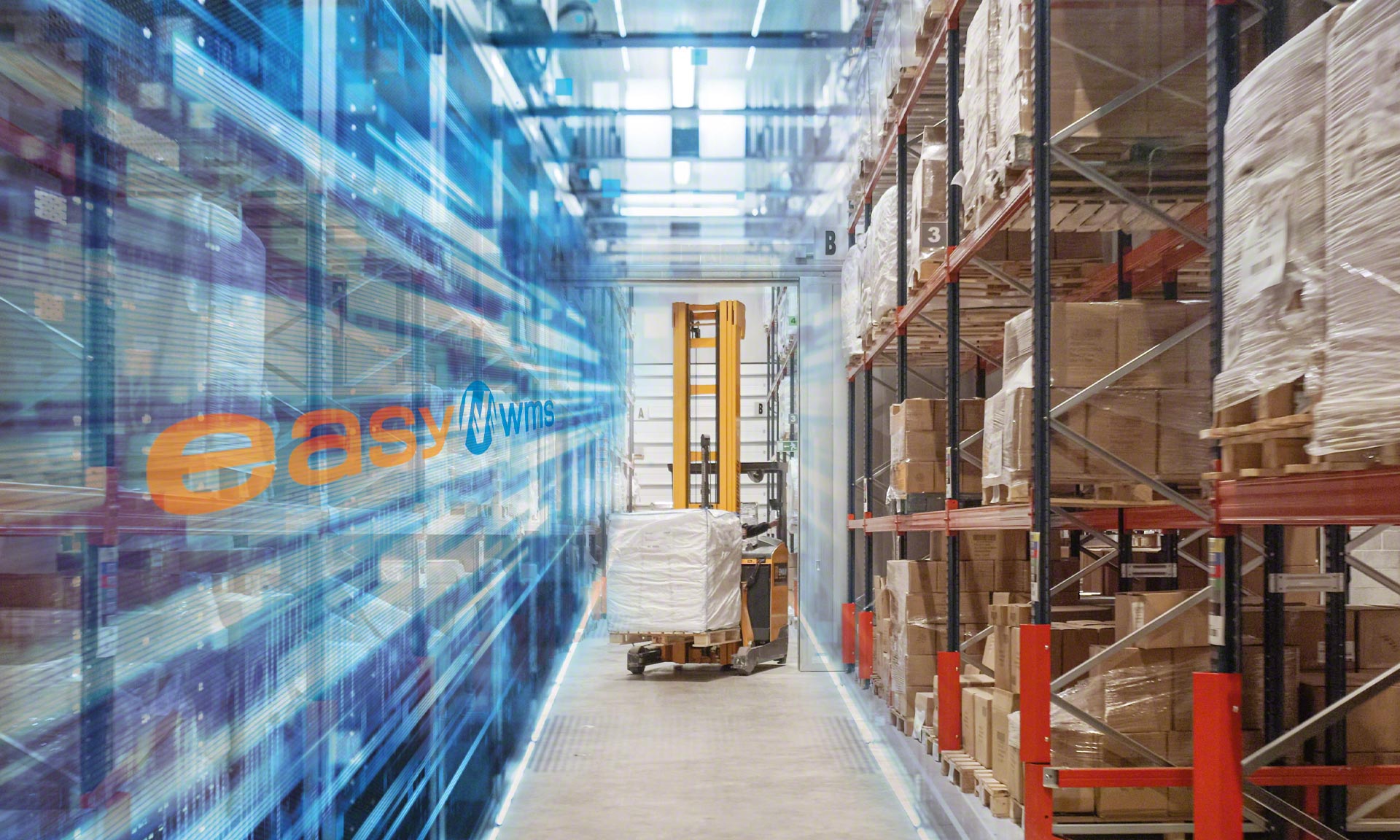
Packaging company Intermark eliminates errors in its digitized warehouse
Packaging and labeling company Intermark has centralized all its logistics processes in a new, 26,910 ft² warehouse managed by Easy WMS software from Mecalux.
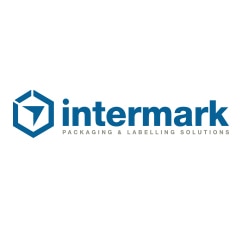
Packaging and labeling products company Intermark has centralized its logistics operations in a new warehouse equipped with Easy WMS. The software monitors movements of goods and, by sending operators instructions, avoids mistakes in order picking.
Intermark: packaging and labelling products
Intermark is a distributor of packaging and labeling materials for big companies. When it first started out, it manufactured plastic bags, adding packaging and labeling products to its catalog over time. Intermark’s product portfolio has expanded over the years, and currently, it partners with renowned manufacturers in the sector worldwide to offer tailor-made solutions at a competitive price.
- Founded in: 1972
- Products: bags, envelopes, items for identification and labelling of goods, and industrial packaging
- Customers: 1,500+
- Presence: Spain and Portugal
- SKUs in stock: 1,490
CHALLENGES
|
SOLUTIONS
|
BENEFITS
|
---|
Packaging and labeling products company Intermark has set in motion a business expansion plan that consists of transforming and modernizing its entire logistics infrastructure.
The company’s former facility had become too small to accommodate all its stock, from padded envelopes to security seals. “Warehouse operations were manual and rudimentary,” says Sergi Jané from Intermark’s Engineering Department. As the number of items and orders grew, manual management of the facility became inefficient for Intermark, which also wanted to expand its business.
Order picking was one operation the company needed to improve. “We used to use a business management software program to know which orders we had to prepare. The operators would walk around the warehouse with printed lists to locate the SKUs,” says Jané.
The organization had also outsourced management of some of its products to a 3PL provider. Determined to provide better customer service and more rigorous control of its goods, Intermark decided to consolidate its logistics processes in a single facility spanning almost 26,910 ft² in Terrassa (Barcelona, Spain). This warehouse stores 1,490 SKUs of varying characteristics, sizes, and turnover.
When opening the new center, Intermark took the opportunity to update its supply chain: “The system had to be able to manage and optimize processes in the facility,” says Jané. The company has digitized all its logistics operations with Mecalux’s Easy WMS warehouse management software, a technology solution designed to keep accurate control over SKUs. The primary goal? To consolidate the company’s growth.
Easy WMS has been integrated with Intermark’s SAP ERP system to ensure cost-effective logistics processes. The Mecalux software controls stock management in real time and closely tracks all movements made and operations performed in the facility. “Easy WMS has two interfaces: on the desktop, so that warehouse managers can monitor how tasks are being carried out, and on the RF scanners used by operators to follow instructions on how to do any job,” says Jané.
Optimized operations
“With Easy WMS, we’ve noticed a marked improvement in our way of working. By receiving instructions on their RF scanners, operators are much faster, and the risk of error is minimal,” says Jané.
Easy WMS intervenes in all warehouse operations and monitors process development. “What we most like about the software is the control it maintains over all operations,” says Jané. “Before installing Easy WMS, when there were stock discrepancies, we had a hard time accounting for them and detecting the source of the problem. Now, with the Mecalux software, we have an exact record of the movements made by the goods and a history of their entries and exits. Product traceability has helped to improve management and avoid mistakes,” says Jané.
The logistics software begins managing operations the minute the facility receives goods, sent by suppliers from Germany, China, Korea, India, and Turkey. Using RF scanners, operators read the pallet barcodes, and Easy WMS assigns each item a location taking into account its SKU and demand level. The optimal distribution of stock in the warehouse has resulted in more streamlined and efficient operations. Items are arranged strategically to facilitate inflows and outflows. For example, products in higher demand are placed near the loading docks for easy distribution when required. The operation that has been most optimized with Easy WMS is order picking. “The software organizes the work of the operators and guides them throughout the warehouse, showing them which items to locate and exactly how many to remove from each location,” says Jané.
Cross-docking is also carried out in the Intermark facility. With this logistics practice, goods are distributed directly without having to be stored. “We receive many products that have to be dispatched right away, at the customer’s request. Cross-docking is a crucial process for us,” says Jané. “When identifying items with their RF scanners, Easy WMS informs the operators of whether the pallets should be stored or moved to the cross-docking area, near the loading docks. The software enables us to manage the goods immediately.”
Modules for more productive operations
Intermark has implemented two additional Easy WMS modules to adapt processes to the requirements of the business. “The Mecalux software is scalable: it’s helped us to optimize warehouse operations and organize our supply chain more effectively,” says Jané.
- Multi Carrier Shipping Software. This program automates dispatch management, organizing product packing and labeling. “The operators read the products’ barcodes, and based on their characteristics, Multi Carrier Shipping Software tells them whether to pack the items as a single unit load or multiple ones,” says Jané. The module also connects the facility with the two transportation agencies that distribute the goods. This way, Easy WMS generates the necessary documentation so that the carriers can be swifter. When they arrive at the Intermark warehouse, they merely have to pick up the orders, as they already have all the information they need in their computer system. “Thanks to the software, we can keep full track of shipments and be sure that the products reach customers by the agreed deadlines,” says Jané.
- Supply Chain Analytics Software. This tool provides information on the status of logistics operations with the aim of improving decision-making. The module provides useful data on the main activities carried out in the facility, which aids logistics managers in making strategic improvements to increase productivity. At a glance, managers can view multiple supply chain KPIs, e.g., percentage of on-time dispatches or occupancy rate per location type. “The module includes a set of dashboards with all the warehouse processes. This solution lets us identify possible errors and correct them in advance. With all the information recorded, we can draw conclusions to improve operational efficiency,” says Jané.
Future-geared digital transformation
The digitization of the Intermark facility is a step forward in logistics efficiency. “At first, it was hard to imagine that we could transform our supply chain. However, working hand in hand with the Mecalux team, we’ve implemented logistics software that’s enhanced our processes and optimized the way we operate,” says Jané.
Mecalux’s Easy WMS has helped Intermark to strengthen its supply chain. The company houses all the products with which it serves its customers in a single warehouse, and the logistics software organizes all items optimally to ensure fast, efficient operations.
The Mecalux software is scalable and capable of adapting to changes at Intermark, i.e., business growth or the launch of new business lines. Now, the packaging and labeling products company controls everything occurring in its facility with a view to eliminating errors, improving processes, and maximizing efficiency.
Easy WMS software is scalable: it’s helped us to optimize warehouse operations and organize our supply chain more effectively. The system controls all processes and provides us with total product traceability to avoid mistakes.
Intermark responds:
Interview with Juan Pablo Calvo, General Manager at Intermark
- What were Intermark’s logistics operations like before you opened the new facility?
Our logistics infrastructure consisted of a small warehouse made up of 1,000 pallet locations where we organized products by family. We had also outsourced management of our industrial packaging products. We realized that if we wanted to grow, we needed to strictly monitor our goods. It was then that we decided to centralize our logistics processes. The supply chain is vital for us — it’s a huge part of our business. Optimizing and facilitating all warehouse tasks is key for Intermark, since, without good organization, it would be difficult to serve our customers and handle the multitude of goods arriving every day from Germany, China, Korea, India, and Turkey.
- What logistics needs did you have when you contacted Mecalux?
When we decided to move to a new, bigger facility, we got in touch with Mecalux to see how we should distribute the space. We’d already worked with them before, so we were familiar with their storage solutions and knew they’d be good partners. We asked the Mecalux team which system would provide us with the largest possible capacity, and they designed a layout adapted to the available space, to our workflows, and to the characteristics of the products.
When moving to a bigger warehouse, we were also aware that we had to change our way of working and that we needed logistics software. After checking out several alternatives, we chose Easy WMS from Mecalux; it was the software program with the most benefits and the best functionalities. We also took into account the expertise of Mecalux’s technical team and the possibility to integrate the WMS with our SAP ERP system.
-
We wanted to digitize product control, optimize processes, and prevent mistakes.
- Why was it so important to digitize your logistics operations with the Mecalux software?
Because we’d expanded our storage capacity and needed to monitor a larger number of items more accurately. We also employed a strategy to digitize all business processes, from billing to delivery notes and the logistics operations themselves. We wanted to digitize warehouse management to improve product control, optimize processes, and prevent mistakes.
- What benefits has Easy WMS brought to Intermark?
For us, the main advantage of Easy WMS is its capacity to integrate with other programs, such as our SAP ERP system and the software used by the transportation agencies. Integration with the ERP system is fundamental for the two systems to share information and be coordinated. For example, when we launch new items, SKUs, and product families, the ERP system automatically notifies Easy WMS of all these changes to organize warehouse processes. The integration of Easy WMS with the carriers’ software also enables us to manage dispatches easily.
-
Easy WMS has minimized errors in our warehouse.
- How has Easy WMS helped to reduce errors in your facility?
The software shows the operators which items to locate and where to find them. Then, they just have to scan the item, and if it’s not the right one, Easy WMS tells them. Before using the Mecalux system, the risk of operators making mistakes was very high because we have SKUs of very similar sizes and colors. Easy WMS has minimized errors in our warehouse.
- Could you describe the Easy WMS software implementation process?
The Mecalux technical team visited our facility to analyze our operations. It then tailored the software to our business to improve the efficiency of our processes. Easy WMS has been adapted to our working methods, and it meets our needs.
For us, installing the management software was a major challenge. Even though we’ve only been working with Easy WMS for a short time, our warehouse operators have already gotten the hang of it: they understand its instructions perfectly and are more productive. We’re more than satisfied with Easy WMS because we can really use it to our advantage.
- You’ve implemented Supply Chain Analytics Software, a module that analyzes all data produced daily in the facility. Why is it so important for Intermark to monitor operational performance?
The Supply Chain Analytics Software module shows how processes are being carried out and helps us to make strategic improvements based on how daily operations are being carried out. Our market is very dynamic, and our customers’ requirements change quickly. As a result, we have to transform our business to be able to meet these new needs. With this module, we now have data-driven information to introduce changes that help us fine-tune our logistics operations.
- What are Intermark’s future prospects?
Intermark has grown by almost 50% in the last five years, and in 2022, we expect to grow by 12%. To achieve this, we’re adding new lines of business, including green and recycled materials, to meet market demands. We hope to increase not only our business volume, but also the number of goods we need to move. And this expansion is only possible because of the investment we’ve made in the new warehouse and the Mecalux software, which allows us to manage all products quickly.
Gallery
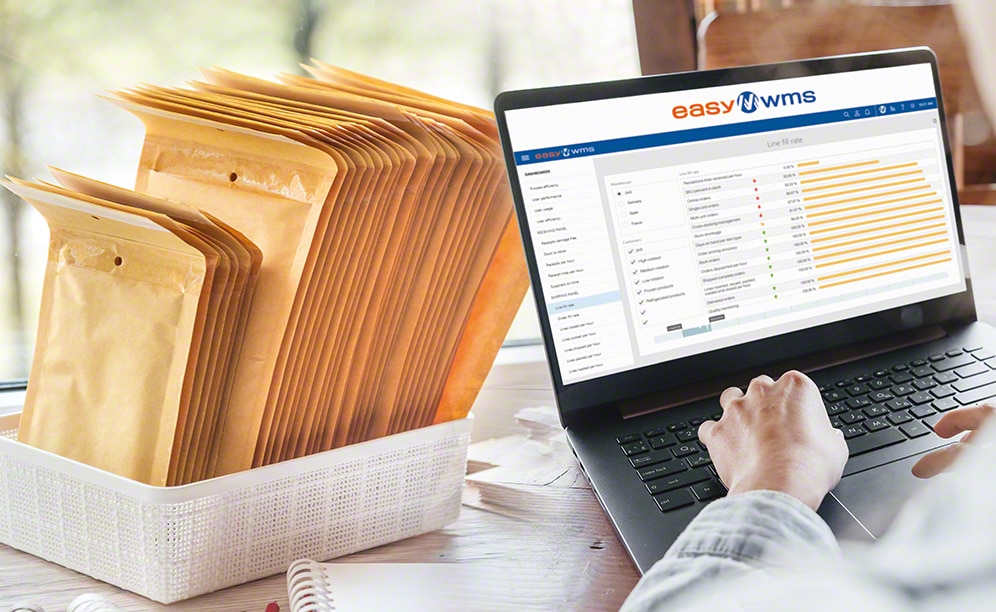
Intermark warehouse for packaging and labeling products in Terrassa, Spain
Ask an expert