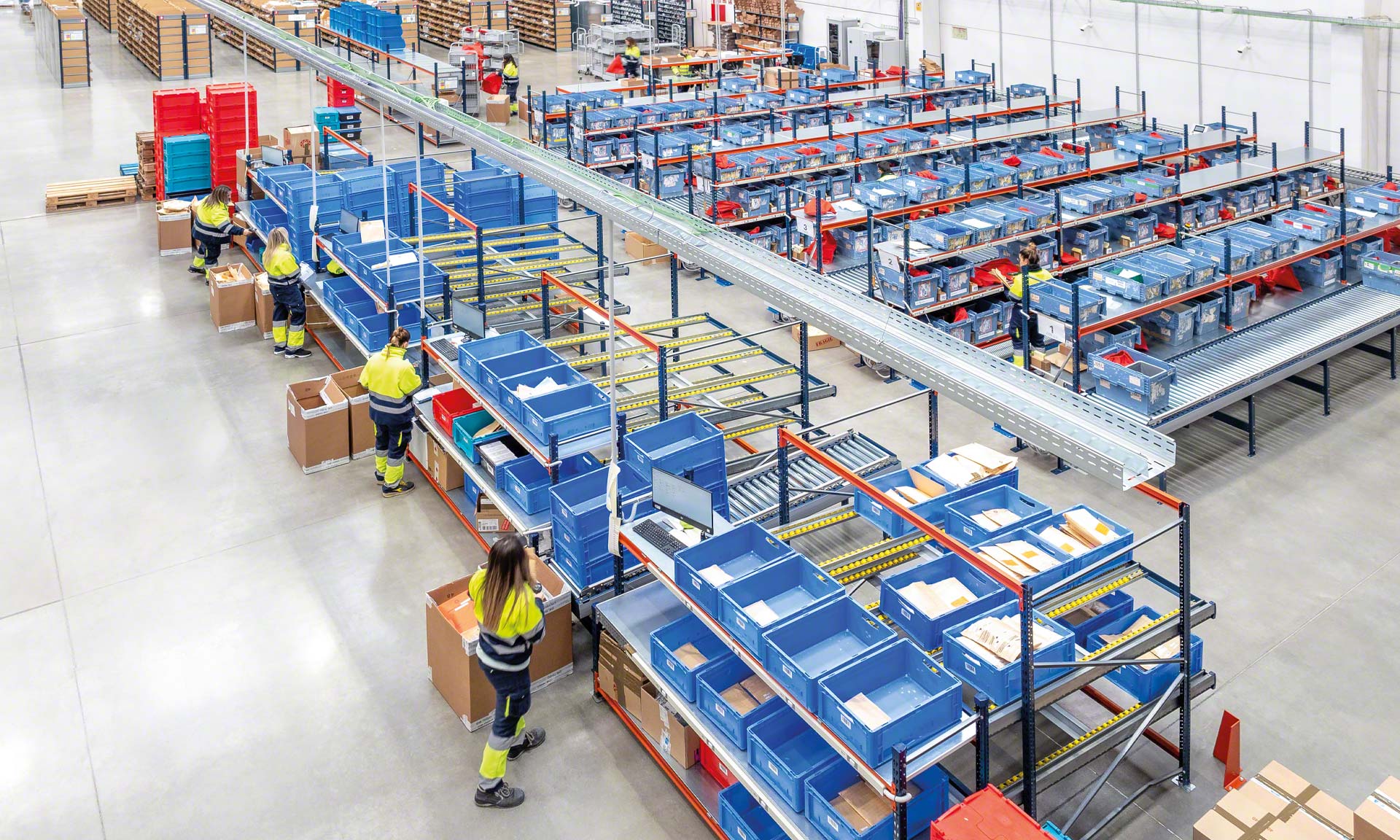
General Óptica installs an omnichannel warehouse with 4,000 daily orders
General Óptica installs logistics solutions that streamline the storage and picking of 100,000 eyeglass frames.
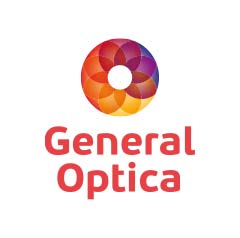
General Óptica, a leading Spanish retailer of prescription glasses, sunglasses, contact lenses, and hearing aids, has opened a logistics center in Madrid. The warehouse, equipped with box conveyors, pallet racks, and picking shelves, fulfills 4,000 orders a day and manages 100,000 SKUs.
General Óptica: maximum quality in vision and hearing solutions
General Óptica is a Spanish company specializing in the sale of prescription glasses, sunglasses, contact lenses, and other products related to eye care and hearing needs. Founded in 1955, it remains one of Spain’s leading chains, offering a wide range of items from multiple brands (proprietary and third-party) and personalized services. With 321 stores in Spain and Portugal, since 2000, General Óptica has been part of the De Rigo Group, a global leader in the manufacture, design, and distribution of high-end eyewear.
CHALLENGES
|
SOLUTIONS
|
BENEFITS
|
---|
General Óptica is a leading retailer of eyewear solutions in Spain and a benchmark in Portugal under the brand Mais Optica. The company has opened a new logistics center designed to accommodate the growth expected over the next 10 years. From its complex near Madrid, General Óptica supplies 321 eyeglass stores across the Iberian Peninsula.
The business wanted to stop outsourcing its logistics operations. “Before, all our merchandise was stored and distributed among third-party logistics providers specializing in the eyewear industry and lens manufacturing and assembly suppliers. One of our main objectives in moving to a new facility was to manage our logistics operations in-house,” says Juan González, Logistics and Transportation Manager at General Óptica. “We wanted to achieve this without increasing lead times between placements of orders for prescription glasses and their manufacture, assembly, and delivery to end customers.”
The warehouse consists of 21,528 ft² dedicated to storage and 3,230 ft² to offices. It plays a crucial role in the company’s supply chain. González says: “We distribute products to suppliers, physical stores, and online customers from this facility, in addition to replenishing frames and managing returns.” The distribution center (DC) also handles logistics-related administrative tasks and supplies stores with all the materials they need.
“To adapt to omnichannel, our warehouse required a level of automation that would boost efficiency in processes and reduce possible errors in picking and shipping products to stores and suppliers,” says González.
The DC employs a tight flow logistics strategy, whereby goods are received the minute they are scheduled to be shipped. This ensures a constant supply to points of sale. “Our stores generate orders continuously throughout the day. To prepare shipments at the end of the work shift, we need a system that streamlines product movements and helps us fill orders more quickly,” says González. With all these requirements, General Óptica decided to install an automated internal transport system along with pallet racks and picking shelves. This combination of Mecalux solutions facilitates the management of 100,000 eyeglass frames, 5,300 SKUs, and thousands of daily orders.
“Since the DC has been operating at peak performance, we’ve been shipping 4,000 orders a day on average. In addition to that volume of activity, you have to consider the level of demand in the receiving area. To comply with all quality and safety protocols, we have to verify the items arriving at the warehouse one by one, recording their batch number. Plus, we validate shipments between the various physical stores. In total, we’re talking about 12,000 transactions per day. And luckily, that number is increasing,” says González.
Optimized picking
General Óptica’s warehouse layout has been designed to expedite the company’s main operation: picking. To fulfill 4,000 daily orders, the business has implemented several logistics solutions and systems, all centered around an automatic box conveyor.
Picking operations are performed in two areas. One comprises four workstations where products are presorted. The other is equipped with a box conveyor system allocated to the final phase of order processing.
At the workstations, operators presort merchandise into boxes with the help of a put-to-light system. These boxes are housed temporarily on carton flow racks. Operators place the unit loads on the higher end of the storage system, and they slide by gravity to the other side, which opens into the exit aisle.
The order fulfillment area consists of an automatic conveyor line and shelving with a put-to-light system. Workers complete orders and gently push them onto the conveyor, which transports them to the consolidation area.
Despite the integration of automated solutions, at General Óptica, employees continue to play a vital role in order fulfillment. Therefore, any technological implementation that enhances their work increases productivity.
“Automation has significantly accelerated our processes performed prior to shipping, optimizing our efficiency. Plus, it’s improved operator performance by eliminating possible adverse effects of manual handling and transfers,” says González.
Racks to facilitate picking
To ensure successful order processing, General Óptica relies on pallet racks and picking shelves. These two storage systems house 100,000 stock units comprising essential products and accessories for the business’s day-to-day operations. Direct access to the goods has streamlined operations.
“In addition to frames and cases, we use the pallet racks to house various consumables that help enhance daily activities in our warehouse,” says González. Thanks to the system’s strength, each level can support up to 3,968 lb. Moreover, wire mesh decking allows for the storage of both palletized merchandise and boxes.
“On the picking shelves, we house frames, protective glasses for industrial environments, and accessories such as clips, straps, and replacement cases, among other items,” says González. Mecalux equipped the company with light-duty shelving (66 lb per level), wide-span shelving (110 lb per level), and several configurations and add-ons to store multiple types of SKUs.
Future-ready omnichannel logistics
“General Óptica has experienced consistent growth over the past 15 years, which has bolstered our strong financial and commercial position. We work to address the numerous changes and challenges that arise in the vision care market,” says González.
With the Mecalux solutions, General Óptica’s DC efficiently manages 100,000 frames and fulfills an average of 4,000 orders a day. Furthermore, it supplies 321 eyewear stores in Spain and Portugal along with online customers. The company is ready to double its inventory stocked, if necessary, and to meet the projected growth for the next decade.
Mecalux — with its extensive experience and wide range of logistics solutions — has been an invaluable asset and an integral part of our project’s success.
Gallery
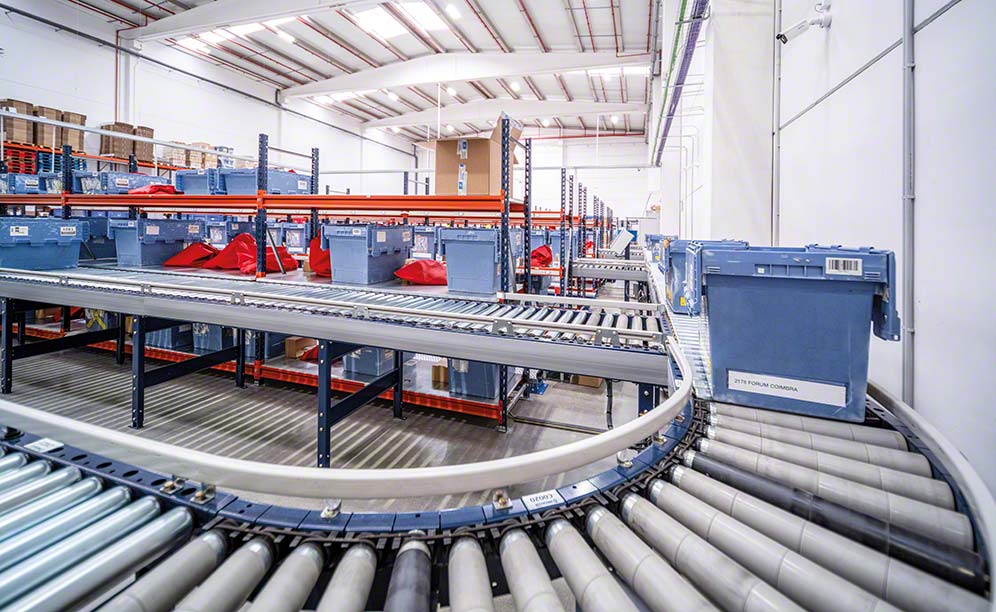
Conveyors speed up the picking of General Óptica’s glasses and frames
Ask an expert