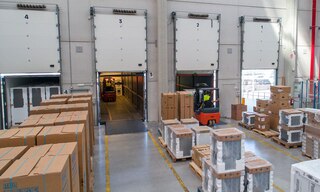
Tight flow logistics: stock just when you need it
Tight flow is a logistics strategy in which goods are received at the time they are scheduled to be dispatched or are required for production. Closely related to just-in-time and Lean logistics, the tight flow planning method calls for total synchronization between all the links in the supply chain to ensure that the product arrives as per the conditions agreed upon with the final customer.
In this post, we analyze the concept of tight flow in logistics, its main characteristics, and, most importantly, the tools you can use to implement it in your warehouse.
What’s tight flow?
In logistics, tight flow refers to the receipt of goods in the warehouse or at the production line the moment they’re needed. These products normally have an imminent expiration or shipping date, so the distribution and sales phases occur in a short period of time (hours or days).
Once the goods are received at the loading docks, they’re temporarily stored in a buffer or staging area. There, they’re either consolidated and shipped in a short time frame or sent to a production line. In the case of the latter, operators receive only the stock they need to fulfill the production order. This eliminates the cost overruns of storing stock that’s not required at that particular time.
In the field of production, the tight flow logistics strategy is commonly found in companies that adopt the just-in-time (JIT) philosophy. First seen in Japan in the 1940s, and originally conceived as a production method for the automotive industry, just-in-time aims to reduce the volume of stock stored. With JIT, manufacturing is based on actual demand. Therefore, parts and raw material suppliers must be able to deliver their goods as soon as they’re needed to avoid interruptions to production.
The concept of JIT has evolved into what is known as tight flow, now implemented in large-scale distribution, especially in the food and supermarket industries. The buffer warehouses of a supermarket chain, for example, receive goods from their suppliers in a coordinated way so that, in a cycle of a few hours, they can consolidate and dispatch the products to supermarkets for immediate sale. All the suppliers and carriers must be perfectly in sync to make sure that, during consolidation and shipping, no product is missing and no delays occur.

Keys to tight flow logistics
Tight flow logistics calls for maximum coordination throughout the supply chain to guarantee that products are supplied at the right time. These are the fundamental principles for implementing this strategy successfully:
- Exact demand forecasting: the company must know the sales forecast to be able to supply demand without generating overstock.
- Shared information: tight flow is only viable when information is synced across the entire product supply chain, especially with the suppliers and logistics providers involved in the production and distribution of the item in question.
- Defined lead times: purchase and shipping orders should be precise, indicating when and where the goods are being sent so that the different supply chain stakeholders can prepare to receive the products and streamline stock movements in the warehouse.
- Internal coordination: all company departments ― including administration, purchasing, logistics, and management ― must be carefully synced to prevent inefficiencies in operations taking place in the facility.
Differences between tight flow and cross-docking
The logistics concepts of tight flow and cross-docking are often considered synonymous, but this isn’t entirely true. The cross-docking dispatch model is a solution used in facilities that employ the tight flow strategy to receive and ship products without having to store them.
Specifically, methods such as cross-docking ensure that the tight flow of goods is carried out efficiently and without incurring storage costs: the products received are temporarily deposited in a storage buffer and then dispatched to another warehouse, to a distribution or returns center, or to the end customer.
This can be seen, for instance, in the facility of Ypê, a leading Brazilian producer and distributor of household cleaning products. The company’s new, automated warehouse has a zone next to the docks that’s dedicated to cross-docking. This area, equipped with pallet flow racks, stores consumer products that don’t enter the facility, as they’re shipped directly to customers. The Easy WMS warehouse management system is charged with coordinating all operations in the facility, controlling stock, and supervising goods inflows and outflows.
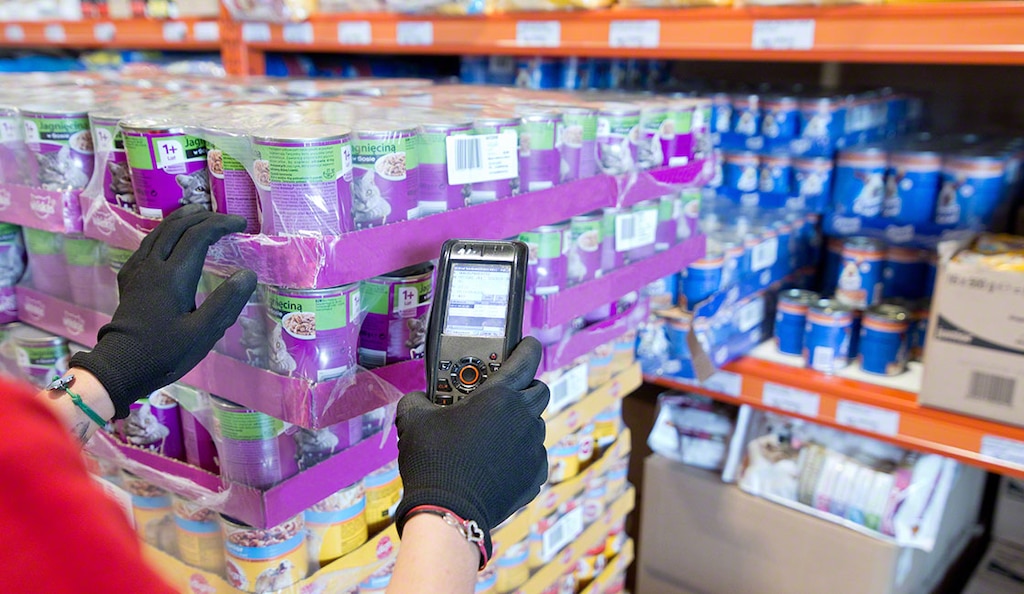
How to implement tight flow logistics
There are multiple ways to apply tight flow in a warehouse or production center. As shown in the section above, cross-docking is an excellent solution: the receipt of goods is scheduled right when they are slated to be dispatched. This does away with having to store the products, reducing investments in storage systems, square footage, and handling times.
To employ these strategies effectively, it’s crucial to digitize your logistics operations with a warehouse management system (WMS) that automates operations as complex as the distribution of locations in the different storage areas, replenishment paths, and order picking. Easy WMS software from Interlake Mecalux ensures that the logistics manager has complete and up-to-date visibility of purchase orders, of supplies of raw materials to the production lines, and of reverse logistics management, in the case of ecommerce.
Easy WMS has advanced functionalities to adapt tight flow to the goods of any business or sector:
- WMS for Manufacturing: this module syncs the production buffer with the supply buffer (temporary storage area in which the necessary raw materials are deposited). It tells operators, using RF scanners, when to supply the raw materials and to which production line. This module ensures the tight flow of goods from the warehouse to the production area, eliminating errors in manual operations and coordinating operator routes.
- Store Fulfillment: geared specially towards retail, this advanced functionality makes it possible to redistribute stock between the distribution center, the main warehouse, and the various physical stores according to customer demand.
- Supply Chain Analytics Software: this app collects information on the various processes taking place inside and outside the warehouse. It gives the logistics manager a complete picture of the throughput of any operation.
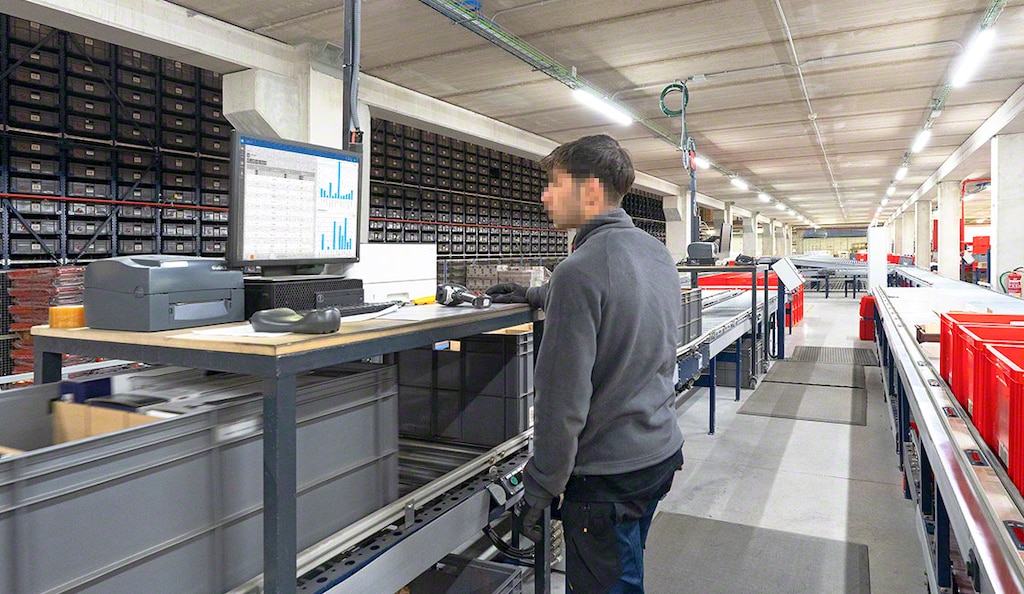
Tight flow: continuous receipts and dispatches
The tight flow logistics strategy guarantees the constant supply of goods to points of sale and production lines, with minimal storage requirements. This method brings down operating costs by optimizing space and reducing the risk of stock expiring in the warehouse.
However, a tight flow strategy calls for perfect coordination throughout the supply chain. To this end, it’s critical to digitize processes to eliminate any possibility of error. Interested in implementing a tight flow strategy? Don’t hesitate to contact us. Easy WMS is the ideal solution for maximizing warehouse resources and employing tight flow efficiently.