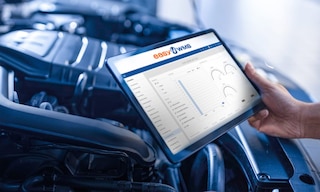
BOM explosion: What it means plus an example
Using a BOM explosion to break down all the materials needed for a manufacturing process helps with detailed planning and maintaining appropriate inventory levels. It ensures efficiency, allowing companies to anticipate potential bottlenecks or stockouts.
What is a BOM explosion?
In the context of the supply chain, a BOM explosion (or bill of materials explosion) refers to the process of breaking down a product’s components into a detailed list of all the parts, materials, and specifications required at each level of production. It’s an enhanced version of the traditional bill of materials (BOM) commonly used in the manufacturing and supply chain industries.
The BOM explosion is a crucial step in production planning, as it helps achieve efficient and cost-effective manufacturing. To perform this analysis, companies need to study the product design thoroughly, essentially “exploding” the extensive bill of materials that goes into creating the item. This procedure is also useful when designing and repairing goods or services.
A BOM explosion can be applied to any methodology. In lean manufacturing, specifically, it provides the following benefits.
- Resource planning. In a lean production system, identifying all necessary materials in advance helps streamline procurement and inventory management.
- Cost estimation. Having a clear view of what each manufacturing stage will require allows for more accurate budgeting.
- Task scheduling. Knowing how each step of the production process will unfold facilitates the creation of schedules.
- Change management. When the production process design is modified, the BOM explosion makes updating the procedure simpler.
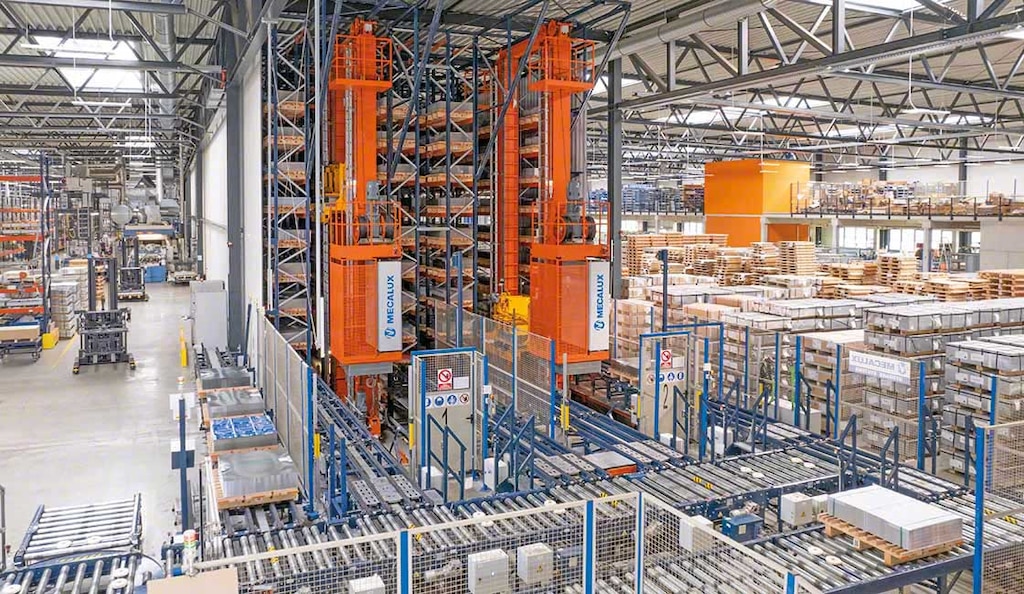
What is an overloaded BOM?
Some ERP-compatible systems can create bills of materials that cover multiple product variants and include several series of additional components. These are known as overloaded BOMs or 150% BOMs. These lists are then filtered using configuration codes or rules to create a product structure tailored to each order.
BOM flattening
The opposite of BOM explosion is BOM flattening. Instead of breaking down manufacturing materials into a detailed inventory, it consolidates them into a simpler, more compact list that includes only the essentials. The goal of BOM flattening is to optimize material management. However, excessive simplification can compromise the visibility and traceability of certain components.
What’s the purpose of a BOM explosion?
These are common scenarios for a BOM explosion and the reasons behind them:
- Complex designs. As products become more sophisticated and have more variants and versions, BOMs become more complicated.
- Globalization of manufacturing. Using components from different countries requires staying up-to-date with various regulations and standards.
- Outsourcing. Subcontracting parts of production can lead to a greater diversification of suppliers, triggering a BOM explosion.
- Shortened product lifecycles. Sometimes companies shorten the lifecycle of their products to implement changes and stay ahead of competitors, which alters BOMs.
- New technologies. Although vital for staying competitive, incorporating new techniques and components into products can extend the BOM.
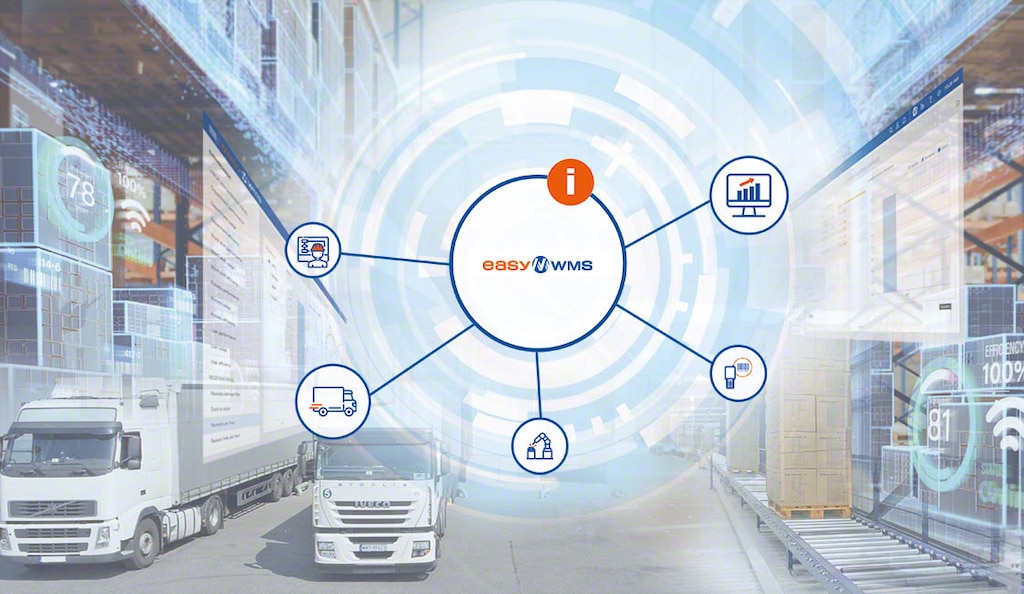
Best practices for preventing BOM explosions
A BOM explosion can provide a clearer understanding of the components and materials required to manufacture a product. But it can also lead to delays, increased costs, errors, inferior quality, and other complications. So, how can companies minimize the risk of a BOM explosion?
- Ensure that the BOM is well-organized and easy to read.
- Limit the number of items used to detect potential problems more quickly. Employing standard parts can help, and any unnecessary components that don’t add value should be identified and removed.
- Establish a review process and test parts and materials beforehand to guarantee that products meet required specifications.
- Maintain smooth communication with suppliers to facilitate coordination and notifications of schedule changes.
BOM explosion example
Exploding the BOM means creating a bill of materials that — instead of being simplified — includes a breakdown of all the subcomponents needed to manufacture a final product. In the case of a bicycle:
Table 1 (before BOM explosion)
Products | Quantity |
---|---|
Frames | 100 |
Handlebars | 100 |
Wheels | 200 |
Seats | 100 |
Table 2 (after BOM explosion)
Components | Subcomponents | Total quantity |
---|---|---|
Frames | 100 | |
Forks | 100 | |
Crankset | 100 | |
Pedals | 200 | |
Handlebars | 100 | |
Wheels | 200 | |
Rims | 200 | |
Tires | 200 | |
Seats | 100 |
Logistics traceability for efficient manufacturing
Today, logistics requires the most agile management possible. At Interlake Mecalux, we specialize in automated solutions and their control through our Easy WMS warehouse management system. Its WMS for Manufacturing module oversees the transformation of raw materials into finished products based on production orders and BOMs for each production line. If you’re looking to speed up processes and improve communication among stakeholders, contact us. We’ll share the vast intralogistics expertise we’ve built on since 1966.