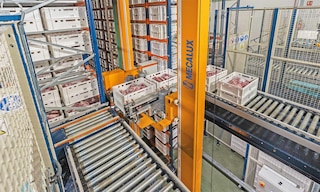
Food logistics and the pathway to optimization
Food logistics faces significant challenges, such as ensuring product traceability, storing goods under optimal conditions, and minimizing the cost of maintaining controlled temperatures. These unique demands have led many companies in the industry to invest in automation and digitalization to optimize their operations, enforce strict inventory control, and guarantee maximum food safety.
What is food logistics?
The concept refers to the efficient management of food across the supply chain, from origin to end consumer. It encompasses a series of processes and activities, such as:
-
Sourcing and procurement: purchasing and supplying raw materials and food products from producers, farmers, and manufacturers.
-
Storage: preserving products in suitable facilities (e.g., cold-storage or freezer warehouses) to maintain quality and food safety.
-
Inventory management: monitoring and controlling stock levels to prevent overstocking or stockouts and ensure proper turnover.
-
Transportation and distribution: moving goods through various links in the supply chain to distribute them in good condition and on time to retail points or end customers.
Food logistics is essential to deliver products to consumers while maintaining freshness and meeting established quality and safety standards.
How to optimize food logistics operations
Streamlining logistics processes is fundamental in all sectors. But it is particularly critical in the food industry, where any mistake could impact public health. To achieve an efficient and incident-free supply chain, food manufacturers and distributors are implementing automated storage and retrieval systems.
Below are some technological solutions food businesses are adopting to meet the sector’s logistics challenges.
Automated internal transport of food products
The automation of goods flow is one of the drivers of food logistics. It increases operational productivity and speeds up internal product movements between strategic areas such as the storage zone and production lines.
A prime example is Europe’s largest sugar processing plant, where British Sugar installed a Mecalux pallet conveyor system to connect its warehouse with production. “All product movements are automated, which really accelerates inflows and outflows,” says Samuel Chapman, Purchasing Manager at British Sugar. Internal transport automation is key for this sugar producer’s logistics strategy. It guarantees agility and safety in managing 3,000 pallets a day.
In food logistics, automatic box conveyors facilitate continuous product flow. A case in point is Elaborados Cárnicos Medina, part of Grupo Medina, a leading beef producer in Spain and a benchmark in Europe. In its plant, the Mecalux box conveyor system connects the warehouse with the cutting, aging, slicing, and packaging processes. With this solution, the business manages up to 680 boxes an hour at 35.6 °F, maintaining the cold chain to optimally preserve the meat.
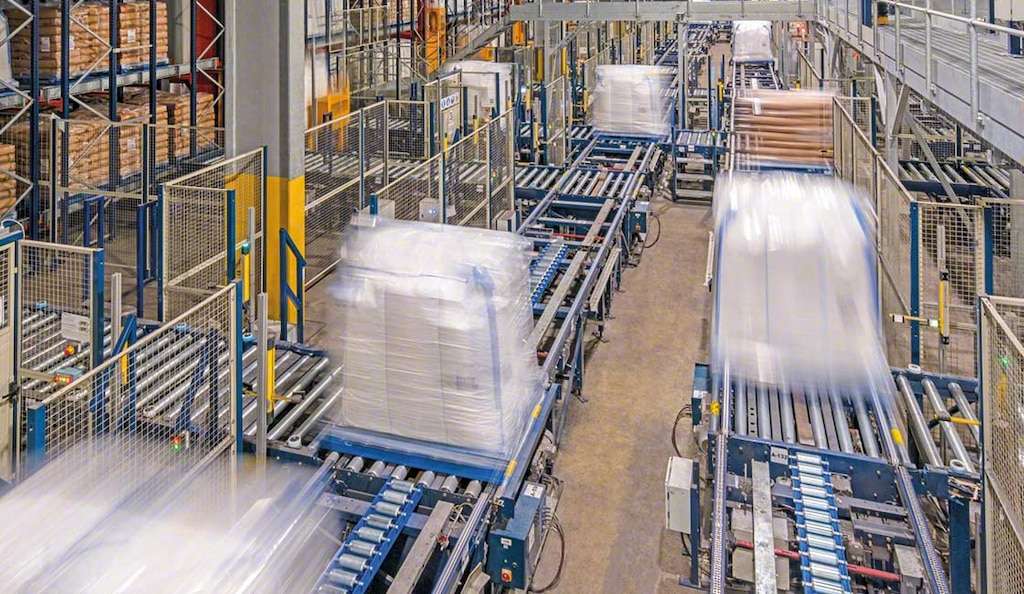
Order fulfillment in food logistics
Order picking is one of the most demanding operations for food companies. In the distribution center (DC) of agribusiness cooperative Copacol, automating the refrigerated and subzero picking area has enabled operators to fill 400 orders a day without errors. This area is outfitted with transfer cars and 306 flow channels, each with a capacity for two pallets, ensuring continuous product availability. Thanks to automation, the Brazilian co-op has increased productivity by 20% and ships around 2,200 tons of meat every day.
Konya Şeker, Turkey’s largest sugar producer, installed a similar solution in its logistics center in Çumra. The transfer car supplies the flow channels, where operators directly access the pallets to pick the boxes that make up each order. With this method, the company distributes 2,000 pallets containing chocolates and cookies to supermarkets and stores across Turkey.
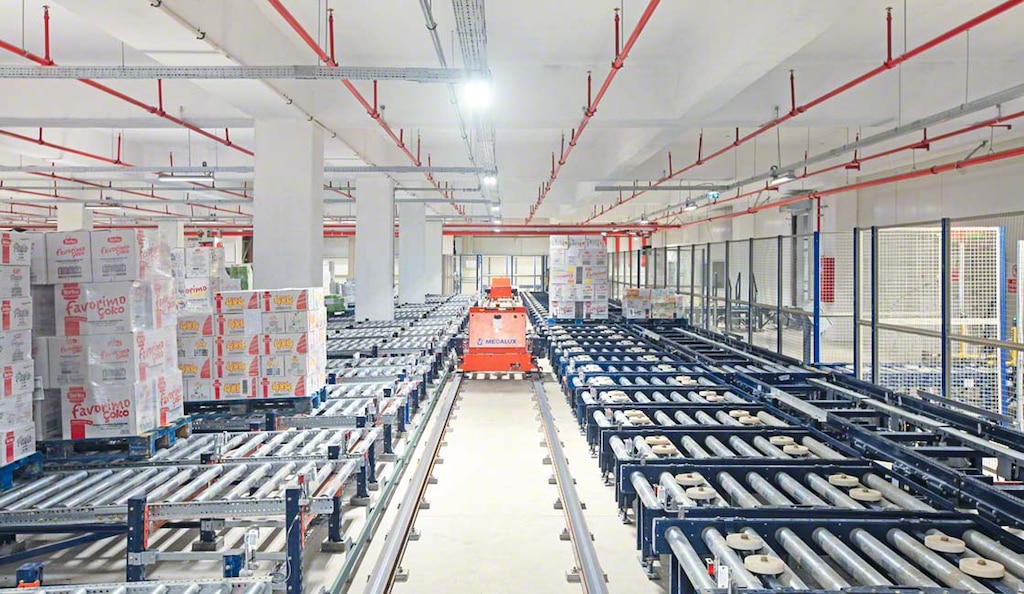
Continuous, safe food storage
Storage is one of the most vital operations in food logistics. Organizations in the sector require systems that guarantee safe food handling while delivering high performance.
In Spain, for instance, dairy company Esnelat (of the Iparlat Group) automated its warehousing operations to cope with increased production. The business installed 10 stacker cranes to efficiently store and ship 350,000 pallets of finished goods annually.
In Poland, Lantmännen Unibake, a leading European supplier of fresh and frozen dough for bakery and pastry production, implemented two automated storage and retrieval systems (AS/RSs) and six stacker cranes operating 24/7. The automatic handling equipment enables the uninterrupted intake of pallets from the production center and other warehouses as well as the distribution of 100 pallets per hour to clients throughout Europe.
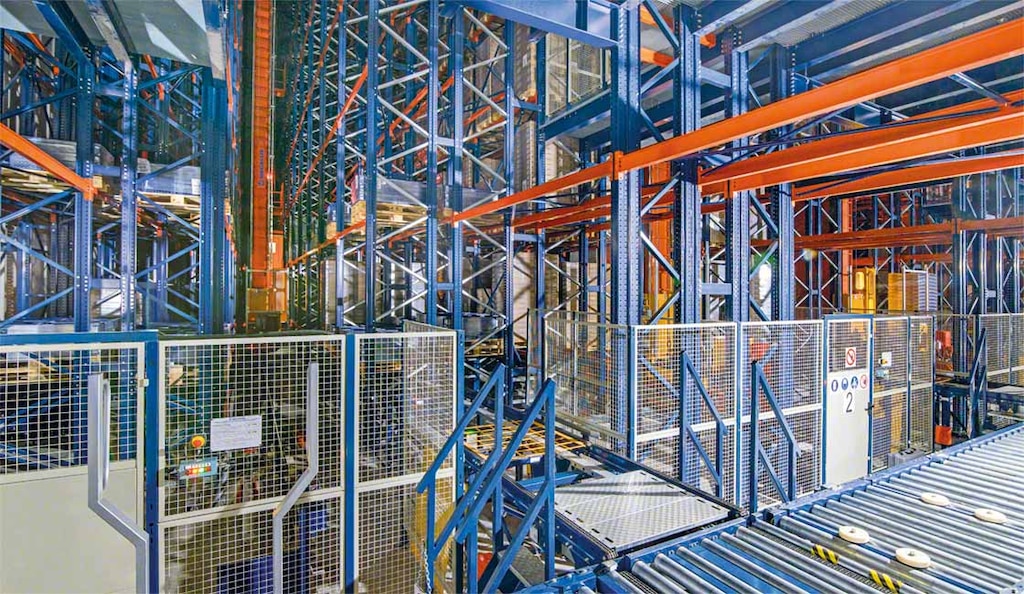
Space utilization to reduce energy consumption in cold storage
In addition to enhancing productivity and safety, food logistics companies managing refrigerated products must optimize storage space to cut down on energy use for cooling. High-density AS/RSs deliver the best results, offering agility, maximum storage capacity, high performance, and efficient goods management.
For example, Bem Brasil, a producer of frozen precooked french fries, implemented our company’s Automated Pallet Shuttle system with stacker cranes in its warehouse run at -22 °F to lower energy consumption. In Portugal, Kiwi Greensun, the Iberian Peninsula’s largest producer of kiwis, commissioned an automated rack-supported building that runs at a refrigerated temperature of 32 to 32.9 °F with 97% humidity. The goal is to preserve the flavor and properties of the 11,400-plus tons of kiwis stored annually.
Temperature control is crucial not just for food storage but also for beverages like whiskey. Rabbit Hole Distillery built a warehouse in Kentucky for 24,500 barrels, designed to adjust to temperature changes and support the whiskey aging process. The racking system maximizes airflow between the storage levels, taking into account the temperature swings in the state, which range from 10 to 120 °F throughout the year.
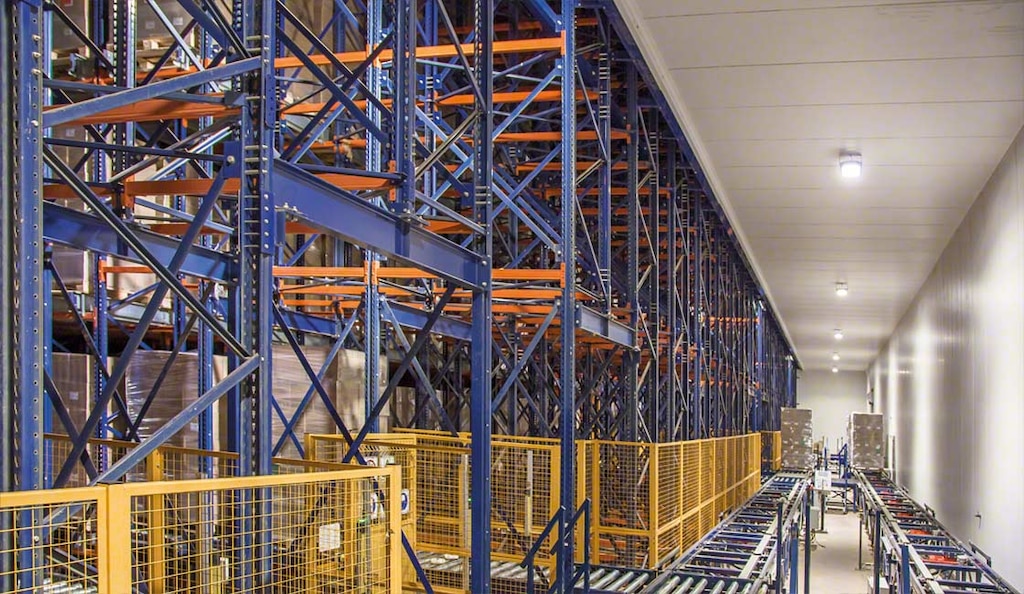
Software for complete traceability in food logistics
Real-time inventory management is paramount in food logistics. Full traceability of food products is becoming imperative for both suppliers and customers. To meet this demand, process digitalization allows for rigorous and efficient stock management while maximizing operator productivity.
Congelados de Navarra is a leading European producer and marketer of deep-frozen vegetables. With our company’s Easy WMS, the business simultaneously supervises four automated warehouses as a single unit. Among many other functions, the software tracks palletized goods arriving from production, assigns a storage location to each item, controls inventory, and streamlines pallet transfers to mixing areas. All of this is carried out in line with a key objective for any food industry company: ensuring traceability.
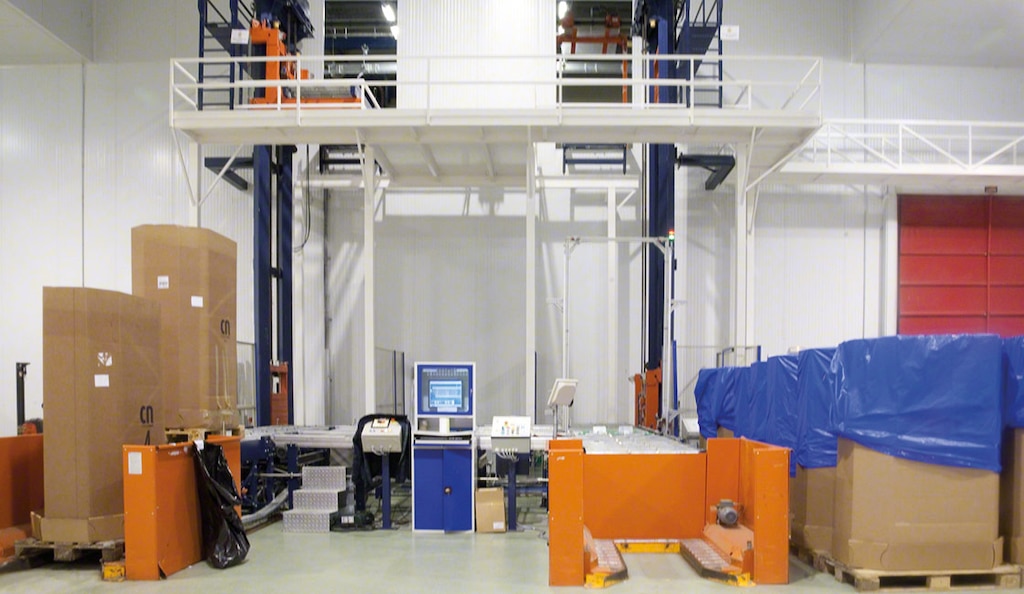
Food logistics: traceability, efficiency, and safety
Food and beverage logistics operations require efficient, secure operations for food to reach end customers in perfect conditions. To handle inventory effectively and error-free, more food industry businesses are automating and digitalizing their supply chains.
Are you looking to leverage the latest technologies to boost your business? You’ve come to the right place. At Interlake Mecalux, we specialize in automating and managing facilities for food producers and distributors with our Easy WMS warehouse management system. Be sure to contact us. Together, we’ll take your logistics processes to the next level.