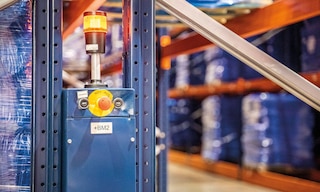
Jidoka: The method that improves manufacturing processes
Jidoka is a tool for maintaining workflow and eradicating problems in the lean supply chain.
What is the jidoka approach?
Jidoka is a lean manufacturing tool that prioritizes quality control in every step of the production process. It centers on immediately stopping production lines when an error is detected. This avoids the creation of large volumes of sub-standard or defective products, reduces the potential negative impact on sales or customer experience, and drives operational excellence.
Purpose of jidoka in lean manufacturing
The aim of implementing the jidoka method is to make products that not only meet user expectations but exceed them. Halting the production lines at the first sign of a problem allows companies to address it directly at the source, prevent its recurrence, and foster a culture of continuous improvement.
Origin of jidoka
Sakichi Toyoda, who later founded the Toyota Group, developed a system that automatically stopped looms whenever a thread broke. Although this issue caused defects in the products, the device created by Toyoda alerted operators through a visual signal, minimizing production downtime and enabling the system to self-monitor.
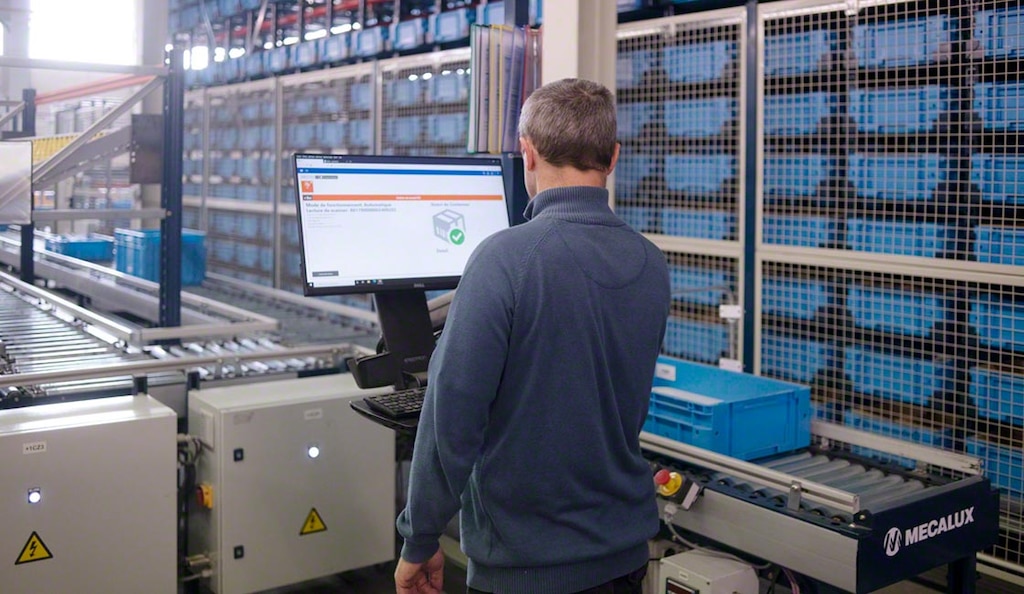
What are the 4 elements of jidoka?
The jidoka method is based on four basic principles that are still relevant today. Modern manufacturers can implement them to ensure the continuity of their workflows and maintain their takt time:
- Detect abnormalities. The goal is for the machines themselves to be able to react to their failures and trigger alerts to notify employees, preventing faulty processes from continuing. This philosophy covers all types of issues, including defective products and poor-quality raw materials.
- Stop production. Once the error is pinpointed, the machinery must shut down automatically without human intervention. Of course, workers should also be able to stop the production lines in case of emergency.
- Take corrective actions. After efforts to solve the problem quickly, a decision must be made on whether production can resume.
- Prevent recurrence. Once the issue is resolved, the responsible person or team should investigate what happened, determine how to prevent it long-term, and implement the necessary improvements to prevent its reoccurrence.
Difference between jidoka and poka-yoke
Jidoka and poka-yoke are two techniques developed by Toyota. Despite some similarities, they offer different solutions.
- The core of jidoka lies in machines or systems that automatically shut down in the event of an error by using monitoring elements such as sensors and detectors. Therefore, the method is also known as autonomation, a neologism combining the concepts of autonomy and automation.
- Poka-yoke, meanwhile, looks to eliminate mistakes by implementing preventive measures. It focuses on repetitive actions where mistakes are relatively easy to make, preventing them through devices designed to anticipate human errors. One example is the safety mechanism that only permits appliances like dishwashers, microwaves, and dryers to start when their doors are securely closed.
How do you implement jidoka?
Adopting the jidoka method in a company involves a shift in mindset. Embracing this philosophy means paying attention to seemingly minor issues and not overlooking them while managing other priorities and deadlines. Although jidoka focuses on machines, ultimately, people have the power to improve processes. These are the first three steps to achieving jidoka:
- Seek the collaboration of management. To implement jidoka effectively, management must understand its benefits, seeing strategic halts in production as opportunities for growth. With this alignment, the entire business will recognize the value of jidoka and prioritize it alongside other systems, such as just-in-time.
- Carry out assessments. Before moving forward, take time to evaluate the viability of processes and identify the implications and requirements for implementing jidoka.
- Start with small projects. Begin with pilot tests on select machines before rolling out this working method across the organization.
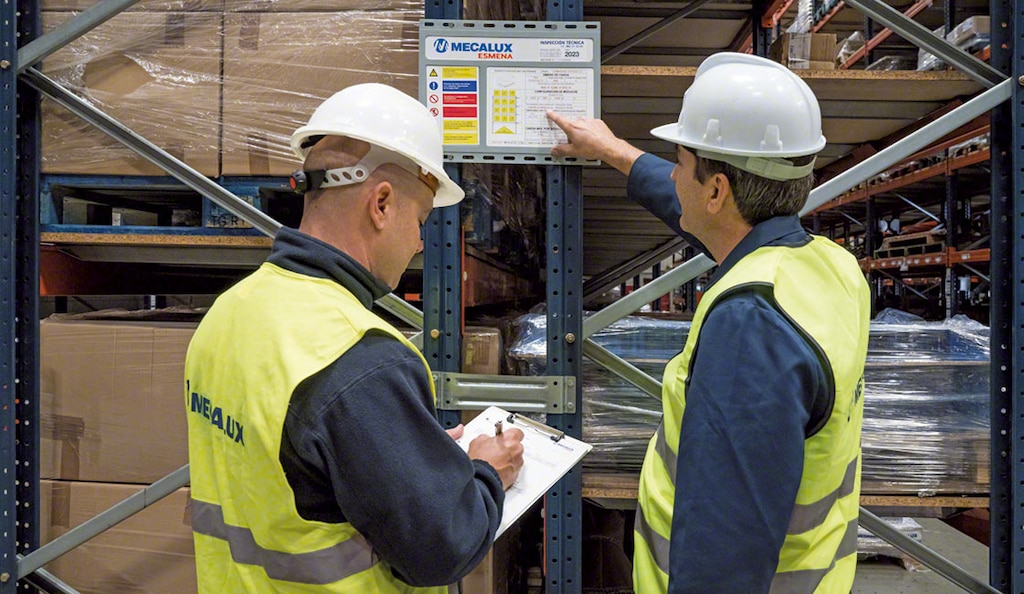
What are the benefits of using jidoka?
Incorporating jidoka into operations offers companies multiple advantages:
- Boosted productivity. Timely detection of irregularities prevents the need to halt and restart production runs. Jidoka also allows operators to work on more than one machine simultaneously.
- Cost reduction. Manufacturing defect-free goods lowers expenses related to repairs, labor, and raw materials.
- Customer satisfaction. Product quality and on-time delivery enhance the overall purchasing experience.
Examples of jidoka in everyday situations
Beyond Sakichi Toyoda’s looms, jidoka is present in various everyday objects and processes:
- Electronic devices. An example of jidoka can be seen in home or office printers, which automatically stop when a paper jam is detected. They issue a visual or audible alert so that the user can clear the jam before wasting more ink or exacerbating the problem.
- Transportation. Vehicles are equipped with visual indicators that inform drivers about potential issues that could affect their safety or the vehicle’s performance.
- Healthcare. Healthcare providers monitor patients’ vital signs using specialized devices. When these devices detect an anomaly, they alert medical staff to take immediate action.
From manufacturing to logistics
Competitive companies analyze their operations closely. They look for ways to fine-tune their processes and incorporate the latest technological advances to optimize their teams’ performance. Warehouse automation plays a key role in this, especially when combined with the control provided by a warehouse management system. Interlake Mecalux’s Easy WMS, for instance, provides complete visibility and traceability of all products and their status. This software is essential for detecting abnormalities as they happen, in line with the first principle of jidoka. Contact us, and we’ll find the best solution for your company.