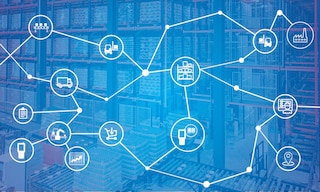
Operational processes in business and warehousing
Operational processes are a part of the day-to-day of companies in any sector. However, it can sometimes be challenging to identify and find ways to improve them. Fortunately, management techniques and specific software programs for warehousing and logistics can help.
What are operational processes?
A company’s operational processes are the activities that directly generate revenue and profit. They connect the organization with its target audience to provide customers with the best products and services, and they are central to its operation. Operational processes are tasks that are crucial for ensuring your business remains competitive.
All companies perform operational processes, whether logistics activities or product manufacturing. When procedures are well-designed and correctly executed, they not only save time and money but also optimize quality and customer service.
Operational processes can vary depending on the particular activity and its position within the supply chain. That said, they generally include these aspects:
- Planning
- Resource acquisition
- Storage
- Manufacturing
- Distribution
- Quality management
Also known as primary processes, these tasks are essential. They are centered around your organization’s ultimate goal and are related to the production or sale of your product or service.

Operational process vs. business process
Operational processes are a subset of business processes, which cover all the actions required to manage a successful enterprise (e.g., marketing, sales, accounting, and human resources). There are three types of business processes: support, management, and operational.
Thus, operational processes are the tasks that directly add value to your product or service, meaning they are vital for producing it. They represent the core of your company’s activity.
How to identify and improve operational processes
There are several ways you can identify your operational processes and pinpoint which ones require improvement to enhance performance:
- Assess revenue and production. After obtaining the raw materials or inputs you need to manufacture your product or offer a service, it’s important to identify what is ultimately delivered to customers.
- Request feedback. Asking employees for their input is another way to define operational processes, as they are the ones who perform them daily. They can contribute valuable information on what works well and which areas need shoring up. Likewise, user feedback will provide insights into what is effective and what is not.
- Analyze. Tools and techniques are helpful for knowing how activities are being carried out within your organization. Examples include process mapping, flowcharts, and process modeling.
- Gather data. Once you’ve identified your business’s operational processes, study them to determine where to make changes and take steps to address possible bottlenecks.
Operational process example
Every company has its operational processes and organizes them as it sees fit. Nonetheless, they all share some common aspects. The following example could apply to an ecommerce retailer:
- Purchase of merchandise
- Storage
- Inventory management
- Order fulfillment
- Shipping and transportation
- Website maintenance
Simultaneously, it will perform other activities such as marketing, customer service, and business accounting.
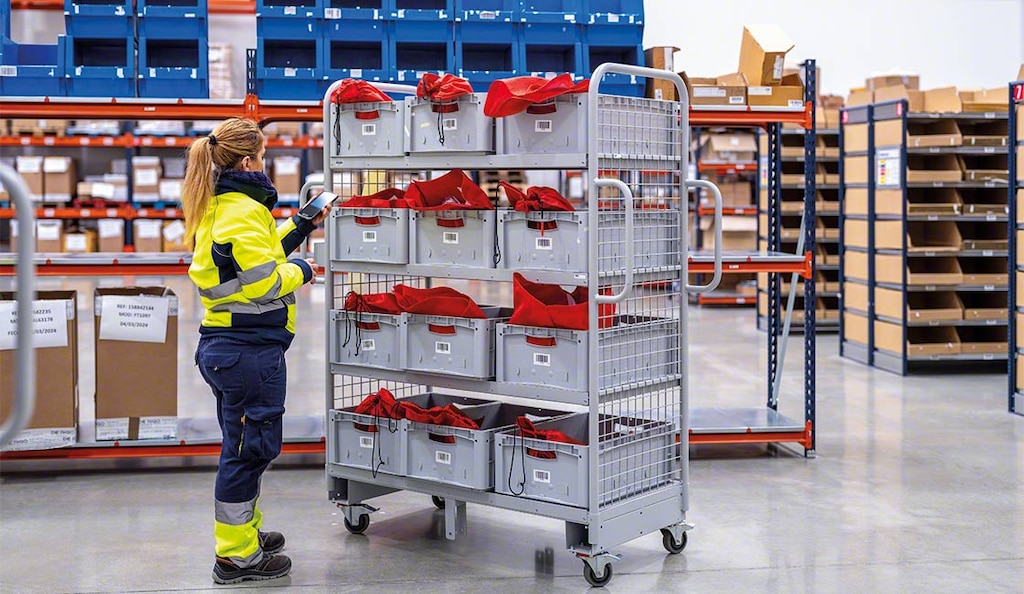
Classifying operational processes in a warehouse
Once you’ve identified the operational processes taking place in your facility, it’s advisable to create a diagram depicting them. (It will come in handy for future operational process improvement). Let’s take a look at some of the most common ones:
- Receiving. This refers to the intake of goods in the warehouse. It might be carried out by external suppliers, which involves conducting verifications, checking quality, and ensuring that the materials ordered have arrived.
- Storage. Next, the products are moved to the racks (for putaway), packing stations, or loading docks. They can also be palletized or housed in cold stores.
- Picking. When an order is received, it is picked and placed in a container. There are multiple ways to perform picking. Some options are autonomous mobile robots (AMRs), high-performance pick stations, and picking robots.
- Returns. An order can be sent back to the warehouse for several reasons. For instance, it might contain defective merchandise or the wrong items. In these situations, some operational processes have to be repeated: product receipt, inspection, classification, and processing.
Having a record of all these actions in a warehouse management system (WMS) like Easy WMS is highly beneficial for analyzing your facility. Moreover, this software automates information and process flows.
Advantages of implementing operational processes
Analyzing the activities that are profitable for your business and how to carry them out has numerous benefits:
- Optimal use of resources
- Sound decision-making
- Detection of non-value-adding activities
- Shorter lead times
- Customer satisfaction
Manage your warehouse’s operational processes with Easy WMS
The most competitive companies closely examine how they operate. They look for ways to fine-tune their operational processes, incorporating the latest technological advancements to enhance their teams’ performance.
Automating and overseeing your facility with Interlake Mecalux’s Easy WMS warehouse management system will put your business on the path to operational excellence. This software provides complete visibility and traceability of all products and their status. Contact us, and we’ll find the best solution for your company.