
The importance of packing in the warehouse
Packing in the warehouse is usually the operation that follows order processing: once picking has been completed, the operators carry out the tasks of packing, wrapping, and packaging to then ship the products to the end customer.
The packing operation is key for companies because the package is the first physical interaction of the customer with the goods they have purchased. In a logistics environment with increasing numbers of smaller orders, the packing process in the warehouse has become more crucial in recent years.
Packing in a warehouse: what does it involve?
Packing is the process of wrapping and packaging the items that make up an order. The main function of this operation is to foster the correct distribution of the products and to guarantee the safety of the goods during transportation. Poor packaging, wrapping, or packing of orders can lead to errors, delays, or losses in deliveries and affect your company’s logistics service.
The packing phase usually involves three operations:
- Packaging: products are individually placed in containers or receptacles such as cans, bottles, jars, or aseptic cartons.
- Packing: items are packed in a larger unit (e.g., cartons, containers, etc.).
- Wrapping/load securing: the products are protected within an even larger unit load — e.g., strapped to pallets — to facilitate transportation.
Efficient packing operations increase productivity in the supply chain. Proper packing, packaging, and wrapping make storage and transportation of the goods in and out of the warehouse quicker and more agile.
How is packing done in a warehouse?
The packing operation is normally performed as follows:
- Step 1: once picking has been carried out, the products are transferred to the packing area, where the items that make up each order are placed into the appropriate units.
- Step 2: the operators secure these unit loads, using different materials depending on the type of product. For example, very fragile goods such as glass cups require bubble wrap and fill chips to protect them during transportation.
- Step 3: once all the packaging is complete, operators enter the required data into the system to generate a delivery note with key information such as the list of items, weight, volume, and final recipient.
- Step 4: operators print out the necessary documentation for each order, which is attached to the package for subsequent shipment.
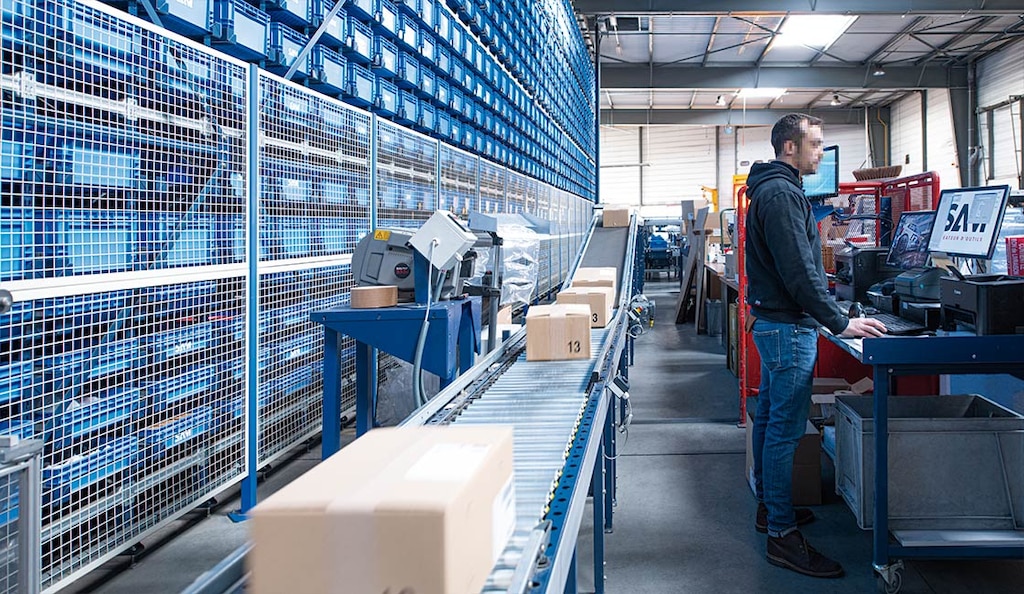
Warehouses usually have an area dedicated to product packing and wrapping. A packing station helps operators place items in the assigned bin for subsequent dispatch. The design of this workstation depends on the volume of orders to be packed, the number of operators involved in the operation, and the nature of the items stored in the facility.
In addition to implementing an ergonomic packing station, companies often digitize the organization of packing, packaging, and wrapping operations to boost performance and eliminate the risk of errors.
Software for packing in the warehouse
A warehouse management system (WMS) organizes all the operations to ensure smooth, efficient, and trouble-free packaging, packing, and load-securing. The WMS optimizes routes and guides operators in packing operations through precise instructions via RF scanners, voice-picking devices, or workstations equipped with the software. During the packing process, the warehouse management software also automates the printing of essential documentation such as the shipping label or delivery note for each order.
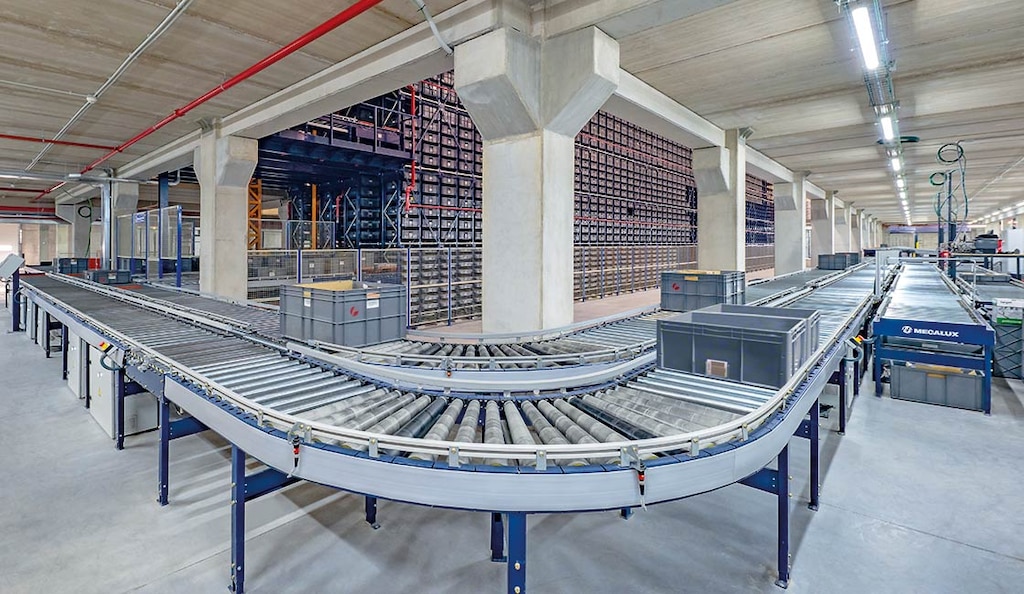
Warehouse management software such as Easy WMS by Interlake Mecalux parameterizes the different packing methods based on the requirements of the logistics manager, the customer, or the assigned carrier. The WMS software coordinates operator tasks and the movements of the automated elements to increase the flow of products to the dispatch area. For example, the software manages the movement of the conveyors for boxes to supply the packing stations and subsequently transport the goods to the loading docks.
Easy WMS has a wide range of modules to meet the specific needs of each facility. The advanced Multi Carrier Shipping Software module increases the throughput of the packing, labeling, and shipping process in the warehouse. The module guides operators, showing them which items to pack and whether to do this as a single unit load or multiple ones. While the products that make up the orders are being packed, the software communicates with the selected transportation agency in real time to transmit shipment information.
Examples of packing with Easy WMS
Easy WMS coordinates and streamlines packing in warehouses in all types of sectors. Here are just two examples:
- Aghasa Turis (Spain): at the company’s logistics center, the Mecalux WMS streamlines packing operations, indicating to operators which items to pack and in what order depending on their weight and size. The company dispatches 95% of orders within 24 hours and error-free, thus meeting the demands of its customers. Easy WMS enables Aghasa Turis to efficiently manage dropshipping dispatches. The software enables products to be packed in customer-specific boxes with packaging adapted to direct shipment.
- Stand-Privé.com (France): the French fashion e-commerce retailer has a large area for packing 2,600 online orders per day. Easy WMS sends instructions to the operators on how to pack the products and generates and prints the labels to ship the orders. The orders are grouped by delivery agency so that when the carriers arrive, they only have to pick up the packages. “Our priority is to prevent errors and guarantee customer satisfaction. With Easy WMS, operators no longer make mistakes, and we’ve minimized customer returns,” says Julien Wang, founding partner of Stand-Privé.com.
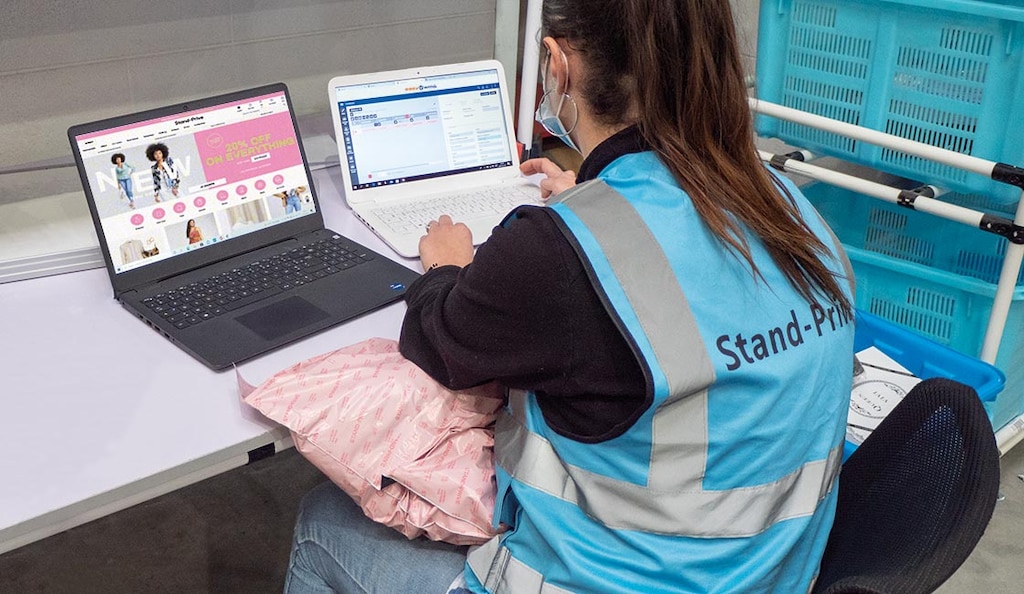
Packing for an efficient warehouse
Efficient packing fosters error-free logistics. There’s no point in having productive picking methods if procedures are not in place to increase throughput in packaging, packing, and wrapping. Warehouse management software such as Interlake Mecalux’s Easy WMS streamlines the picking, packaging, and dispatch of goods to ensure on-time deliveries.
If you’re interested in boosting your warehouse performance and avoiding errors in operations such as packing, don’t hesitate to contact us. An Interlake Mecalux expert will advise you on the best logistics solution for your facility.