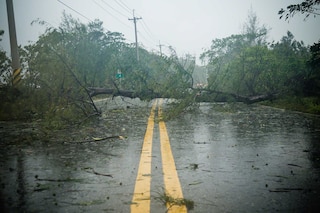
Supply chain disruption: how to mitigate risks
Supply chain disruption can stem from external factors such as a political dispute, a natural disaster, or, as experienced worldwide over the past year, a pandemic. Obviously, the supply chain isn’t isolated from the social, political, and economic circumstances surrounding it.
In this post, we examine the role of logistics in emergency situations. Additionally, we unlock the keys to designing and implementing an action plan that will help to prevent the collateral effects of these disasters and provide information on how to proceed when they occur.
Supply chain disruption
The supply chain encompasses all the stages from the moment a customer orders a product up to the time it is delivered and charged. It includes phases such as the procurement of products to be manufactured and quality control. Any variation during this process could lead to inefficiencies or, in the case of the latter, fail to meet the goal of the supply chain: that the goods reach the final customer with the required quality and at the agreed time and place.
Supply chain disruption, hence, is the alteration of any phase of the supply chain caused by agents external to the product: weather conditions, changes in legislation, and cyberattacks, among others.
Disruptions can be classified by origin:
- Natural: these include catastrophes related to nature, such as earthquakes, tsunamis, and volcanic eruptions.
- Biological: these originate from epidemics or pandemics, as in the case of the coronavirus or Ebola. Given globalization and internationalization of an increasing number of businesses, a good disaster prevention policy in the supply chain will be crucial to avoid the spread of these viruses.
- Policies: these derive from decisions made by governments or supranational institutions that have a direct influence on the proper functioning of the supply chain. This is seen in the US-China trade war and the 1973 oil crisis.
- Technology: these are due to errors or malicious use of certain technologies (global server crashes, data leaks, cyberattacks, etc.).
How to prevent supply chain risks
Although there can always be unexpected disruptions that may alter industrial activity, prevention is the key to avoiding or mitigating these effects.
To this end, organizations need to scrutinize each stage of a product’s supply chain and identify possible risks to its smooth operation: overdependence on a supplier, little room for maneuver when it comes to mistakes in last-mile delivery management, excessive seasonality of a product, and so on.
So, what’s the solution? Beyond knowing the product and determining potential threats, nowadays, there are tools for monitoring and analyzing the performance of all the parts that make up the supply chain. Moreover, these tools can show companies how to implement continuous improvement projects to increase operational productivity.
Along these lines, Easy WMS, the warehouse management system from Interlake Mecalux, incorporates an additional data management module, Supply Chain Analytics, which allows you to:
- View business information in its entirety.
- Create automatic alerts to remedy inefficiencies (excessive dependence on a single supplier, poor performance of certain automatic elements, etc.).
- Be equipped with a productivity panel to have more in-depth knowledge about the performance of the various operations.
- Identify trends and future inefficiencies from the data collected.
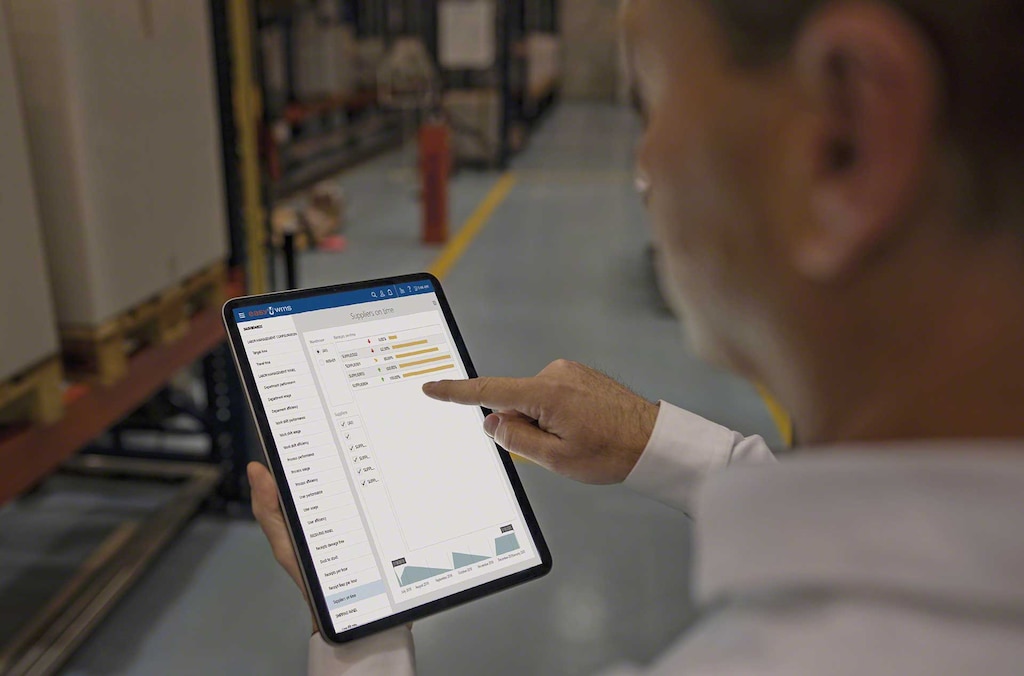
How to manage disruption: a logistics action plan
As part of the disruption prevention plan, upon examining the threats present in its supply chain, the entire company should develop an action plan to minimize or offset the effects of a catastrophe in its installations.
Thus, all action plans should include the following guidelines:
- Analyze the causes and the consequences of the disruption on production, storage, and transportation of the goods to end customers.
- Prioritize measures according to importance to ensure the safety of staff and others that could be affected by the event. Once this has been checked, the goods stored, raw materials, and installation should be secured.
- Listen to all supply chain stakeholders: an action plan shouldn’t be limited to information specific to the company’s business activity, but should also integrate the other participants in the supply chain. After all, this is the only way to ensure accurate product traceability.
- Collaborate with external actors: these can include other logistics organizations, such as logistics providers (they know the most about the lay of the land), other links in the supply chain, and the relevant authorities.
Every action plan should contain these guidelines in order to be effective in the face of supply chain risks. Once they have been set out, it’s time to prepare the execution of the plan. Consulting company PwC outlines the following steps: prepare (the planning described above, consisting of assessing the main threats and indicating how to mitigate their effects), respond (execute the agreed lines of action to reduce the impact on the business's productivity), and, lastly, retrieve and collect information on the impact of the disruption. Then, you will be able to interpret how the plan worked and what aspects need to be improved in the event that the situation occurs in the future.
Examples of disaster risk management
Every company specializing in the design and construction of infrastructures should take into account not only the materials and land used for this purpose, but also the climate conditions, risk of earthquakes, presence of volcanoes in the area, and so on.
Thus, when Interlake Mecalux carries out projects in self-supporting buildings, in which the racks constitute the actual structure of the warehouse, company engineers also assess the impact of all the external variables: wind speed, snow overload, type of terrain, etc.
These are some of our projects in which risk management played a vital role:
Iron Mountain
Five months before the devastating 8.8-magnitude earthquake struck Chile in 2010, information management firm Iron Mountain had hired us to build one of its many warehouses in the South American country. Following the earthquake, the firm lost seven of its installations. However, our facility was still standing.
As a result, Iron Mountain commissioned our company to build two more warehouses and repair the facilities that had been destroyed by the earthquake.
Hayat
The Hayat Kimya group, a benchmark in the Eurasian hygiene and cleaning products market, needed an automated warehouse in western Turkey, one of the highest earthquake hazard areas in Europe.
Our company built it a rack-supported warehouse measuring over 150 feet tall. For this project, it used over 11,000 tons of steel in order to ensure the safety of the facility and comply with the requirements of the country's regulations on storage installations.
Analytics and prevention in the event of disruption
Although there are always unforeseen disasters capable of breaking any link in the supply chain, the various threats in the logistics sector tend to be predictable: due to geographical area, industrial sector, or seasonality.
The use of software such as a warehouse management system (WMS) allows you to know your logistics systems inside out: WMSs collect a multitude of data that enable you to accurately identify weak points and prepare a made-to-measure plan to protect your company against any risk to its supply chain. Therefore, the best way to avoid breaking the supply chain is to embrace digital transformation.
At Interlake Mecalux, our team of experts will offer you the ideal storage solution for preventing future disruptions at your company, cutting out extra costs and ramping up warehouse productivity.